Time to read: 5 min
Injection molding is used to produce medical devices and pharmaceutical products for an increasing number of therapeutic, diagnostic, surgical, laboratory, and orthopedic applications. In part, that’s because injection molding uses plastics with excellent material properties and can produce high volumes of tight-tolerance parts in a repeatable and cost-efficient way.
Yet, medical injection molding also supports the use of silicones and thermoplastic elastomers (TPEs) – and not just for high-volume production either. If you need prototypes or smaller quantities, partnering with Fictiv also offers a complete solution. From prototyping through production at any volume, we can provide the complex parts that you need at ridiculous speeds.
This article describes some common injection molded parts for the medical and pharmaceutical industries. It also explains what’s meant by terms like “medical devices” and “pharmaceutical products”, and how different injection molding materials support different applications. And if you’re interested in more injection molding design tips, our downloadable e-book is a great place to start.
Download Fictiv’s Injection Molding Design Guide
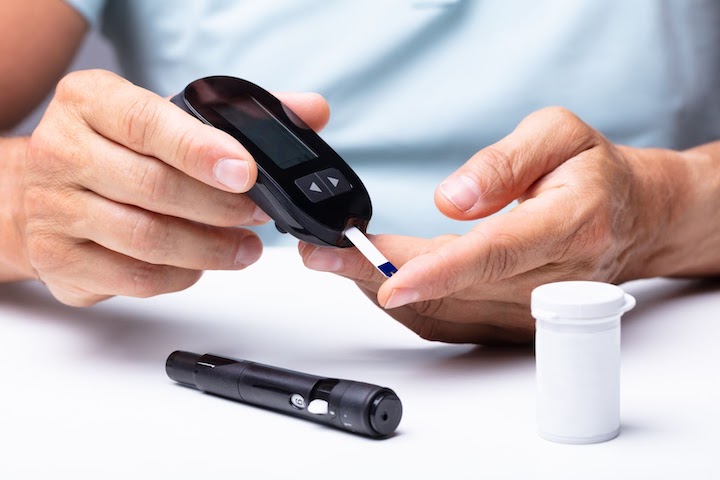
Medical Devices and Pharmaceutical Products
In the United States, the Food and Drug Administration (FDA) defines the term medical device – and does so very broadly. Under Section 201(h) of the Federal Food, Drug, and Cosmetic Act, a medical device is “any instrument, machine, contrivance, implant, or in vitro reagent that’s intended to treat, cure, prevent, mitigate, or diagnose disease” in humans. Examples range from simple products such as plastic tongue depressors to complex assemblies such as blood glucose meters that incorporate plastic dials and buttons.
The definition of a pharmaceutical product is also broad and, as Law Insider, explains, “means any product, compound, medicine, or therapeutic which is subject to regulation as a drug, medicine, or controlled substance” by the FDA. Examples include drug delivery systems as well as the drugs, medications, or hormones that these systems deliver. As with medical devices, some or all of a pharmaceutical product may be injection molded.
For example, a product may consist of a molded plastic enclosure, machined metal fasteners that are overmolded, and injection molded tubes and seals. This same device may also contain other machined components and use different types of injection molded materials for its external and internal parts. There are also medical devices, such as catheters, that are entirely injection molded, or types of durable medical equipment, such as hospital beds, where only a few parts (such as the pedals) are made of molded plastic.
Medical Injection Molding Materials
Injection molded parts for the medical and pharmaceutical industries use a wide variety of plastic materials. Depending on your specific application, the biocompatibility of a medical plastic and its ability to withstand autoclaving may be important concerns. For the injection-molded enclosure for a surgical robot, impact resistance and the ability to withstand chemical cleaning may be key considerations. With single-use medical products, cost and cleanliness typically drive design decisions.
Although there are many types of plastics, these polymers are often used for medical injection molding.
- Polyethyelene is a cost-effective thermoplastic that absorbs little water and maintains its structural integrity during multiple sterilization processes. Applications include membranes for oxygenators.
- Polypropylene is also a commodity thermoplastic, but this polymer provides excellent fatigue resistance. Applications include the living hinges on pill organizers.
- Polystyrene supports sterilization by radiation and is available in clear grades that are a good choice for blood dilution lab vials.
- PEEK, or polyetheretherketone, is an engineering thermoplastic with excellent mechanical strength that is used in load-bearing implants such as spinal cages and knee replacements.
Thermoplastic elastomers (TPEs) can also be injection molded. Because of their softness and elasticity, these materials are a good choice for medical bandages and tourniquet bands. Liquid silicone rubber (LSR) and high-consistency silicone rubber (HCR) are also used in injection molded parts for the medical and pharmaceutical industries, especially for medical wearables and drug delivery systems.

Medical Wearables and Drug Delivery Systems
Injection molding can produce parts for intravenous (IV) infusion pumps, which are medical devices that deliver fluids, medications, blood, and blood products. IV infusion pumps for ambulatory patients are considered to be medical wearables, devices that are designed to be worn on the body and used to track and monitor various vital signs. There are also IV infusion pumps with injection molded parts that — like more traditional drug delivery systems — are designed for stationary use.
Today, injection-molded medical devices can be implanted within the human body to deliver cancer-fighting drugs and other active pharmaceutical agents (APIs). These drug-eluting implantable devices expand the therapeutic window because, unlike pills and injections, they steadily release an API at a controllable, optimal rate. Injection molding’s advantages in this application include the ability to load the matrix of a device with the API before injection molding occurs. Often, silicone is used because it can be injected molded at relatively low temperatures, which helps to avoid temperature-induced drug degradation.

Laboratory Products and Labware
Injection molding also uses plastic materials to produce laboratory products and labware for the medical and pharmaceutical industries, including:
- Petri dishes and lids for culturing cells such as bacteria and fungi
- Pipettes for transporting measured volumes of liquids
- Test tubes for observing biological, biochemical, or chemical reactions
- Microplates (microtiters, microtiter plates) for molecular biology and biomedical studies
- Beakers for measuring liquid volumes during chemical procedures like heating and mixing
- Flasks for holding or volumetrically measuring chemicals, samples, and solutions
- Scintillation vials for holding radioactive substances in liquid scintillation or beta/gamma counting
- Cryovials for the cryogenic storage of biological materials using liquid nitrogen
Injection molding is also used to produce septa, silicone membranes that support the air-free transfer of liquids or gases with a needle and syringe. Although septa can be cut out or punched out instead, injection molding ensures that each individual septum has uniform dimensions. With cutting or punching processes, septa may become hourglass-shaped and lack the disk shape that’s needed for proper sealing.
Fictiv — Complex Injection Molded Parts for the Medical and Pharmaceutical Industries at Ridiculous Speeds!
Do you need medical injection molding for prototyping, low-volume, or high-volume production? A good plan and skilled production partner are critical to your success. Fictiv has the global manufacturing network and production experts that you need to get quality parts, no matter how complex your designs. And we have the skills to support you from part design through prototyping and production.
Create your free Fictiv account to request an injection molding quote today. We mold complex parts at ridiculous speeds!