Time to read: 7 min
Prototyping is a critical stage of the product development lifecycle, allowing designers to validate their ideas physically before moving on to production. The prototype manufacturing method you choose is a make-or-break decision, as processes allowing quick and accurate manufacturing will enable you to iterate through designs efficiently, ultimately leading to a better end product.
CNC machining and 3D printing each offer unique advantages for prototyping. CNC excels in producing high-precision parts from solid materials, making it ideal for functional testing. Meanwhile, 3D printing often offers faster turnaround and greater flexibility, especially for complex geometries. The best choice depends on your product’s material, detail, and turnaround time requirements.
In this article, we will further compare these two processes to help you select the right process for your project.
An Overview of CNC Machining vs. 3D Printing
3D printing and CNC machining are two different processes, both in terms of operation and suitable application. CNC (Computer Numerical Control) machining is a subtractive manufacturing process that uses precision cutting tools, such as lathes, mills, and grinders, to carve parts from solid blocks of material. Conversely, 3D printing, or additive manufacturing, is the process of building objects layer by layer from the ground up.
Table 1 below gives a summary comparison of CNC vs 3D printing for prototypes based on different performance factors.
Factor | CNC Machining | 3D Printing |
Process Type | Subtractive (material is cut away) | Additive (material is built layer by layer) |
Best For | High-precision, functional prototypes, and metal parts | Complex geometries, lightweight structures, and fast iteration |
Material Options | Metals, plastics, composites | Plastics, resins, some metals, and composites |
Surface Finish | Smooth, but machining marks may be present (Finish improves with post-processing) | Varies: Smooth or layer lines and stairstepping may be present |
Tolerances | ± 0.001″–0.005″ (high precision) | ± 0.004″–0.02″ (depends on printing technology) |
Strength & Durability | Excellent for structural applications | Depends on the printing material and the process |
Cost Considerations | Cost-effective for high-strength and more expensive for complex geometries | Cheaper for rapid iterations, higher cost for end-use parts |
Production Speed | Slower setup, but faster for batch production | Faster setup, but slower for large solid parts |
Design Complexity | Limited by tool access; not ideal internal features, undercuts, and organic shapes | Good for complex geometries that cannot be done with traditional subtractive methods. It offers virtually unlimited design freedom |
Cost | Lower cost for high volumes | Lower cost for low volumes |
Table 1. Comparison of CNC machining and 3D printing
When to Use CNC Machining for Prototype Manufacturing
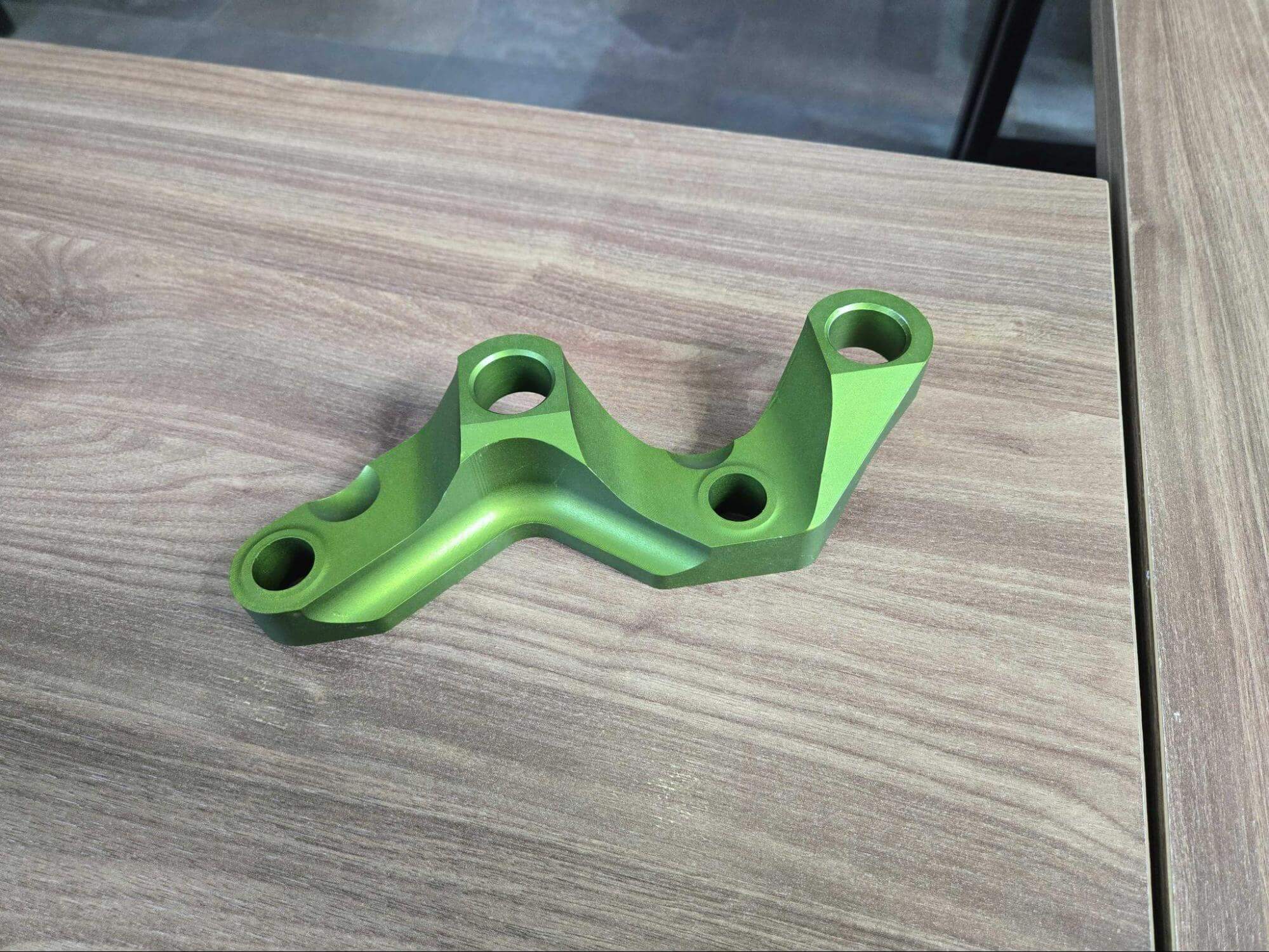
CNC machining is a very mature manufacturing method and is used in a wide range of industries. It offers excellent precision, part strength, and a smooth surface finish. You typically want to opt for CNC machining over 3D printing for the following:
- High precision and tight tolerances (e.g., aerospace or automotive components)
- Functional prototypes that must withstand stress or harsh environments
- Metal parts that need to be strong and durable
- Smooth surface finishes that require minimal post-processing
However, while CNC machining delivers unmatched quality, it can be more expensive and time-consuming than 3D printing, especially for single prototypes or small batches. The subtractive nature of the process can also lead to large amounts of material waste, although it can often be recycled. However, for projects where precision, strength, and reliability are non-negotiable, CNC machining is often the best choice.
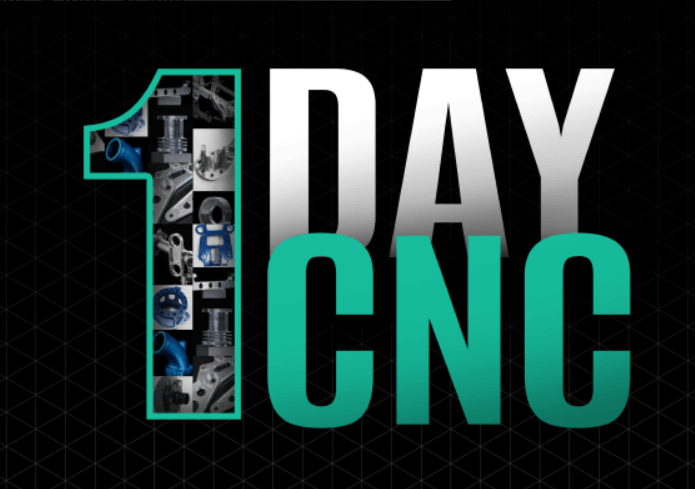
Fictiv can machine and deliver CNC parts in as little as one day. Get your expedited CNC quote here.
Application Examples for CNC Machining Prototypes
Some application examples for CNC-machined prototypes include:
- Aerospace & Automotive: Metal brackets, engine components, and high-temperature parts
- Medical Devices: Surgical tools, implants, and high-precision components
- Industrial Equipment: Gears, machine parts, and durable housings
When to Use 3D Printing for Prototype Manufacturing
3D printing has recently cemented itself as one of the most popular rapid prototyping methods. It offers virtually unlimited design possibilities and rapid design iterations that are as simple as updating a CAD file and starting a print.
While CNC machining does offer better surface finishes and tighter tolerances, 3D printing outperforms CNC machining in the following scenarios:
- Rapid prototyping and iterating through design cycles quickly and cost-effectively.
- Complex geometries with intricate details, internal features, or organic shapes.
- Lightweight structures or designs optimized for material efficiency.
- Custom, one-off prototypes, or low-volume production where traditional manufacturing would be too costly.
- Low-cost material testing before moving to the final production.
While 3D printing excels in speed and design freedom, it typically offers lower precision and strength compared to CNC machining, depending on the material and printing process used. Additionally, the layered surface finish may require post-processing to achieve a smoother appearance. Despite this, 3D printing has proven itself to be an invaluable tool for projects that require speed, affordability, and creative design.
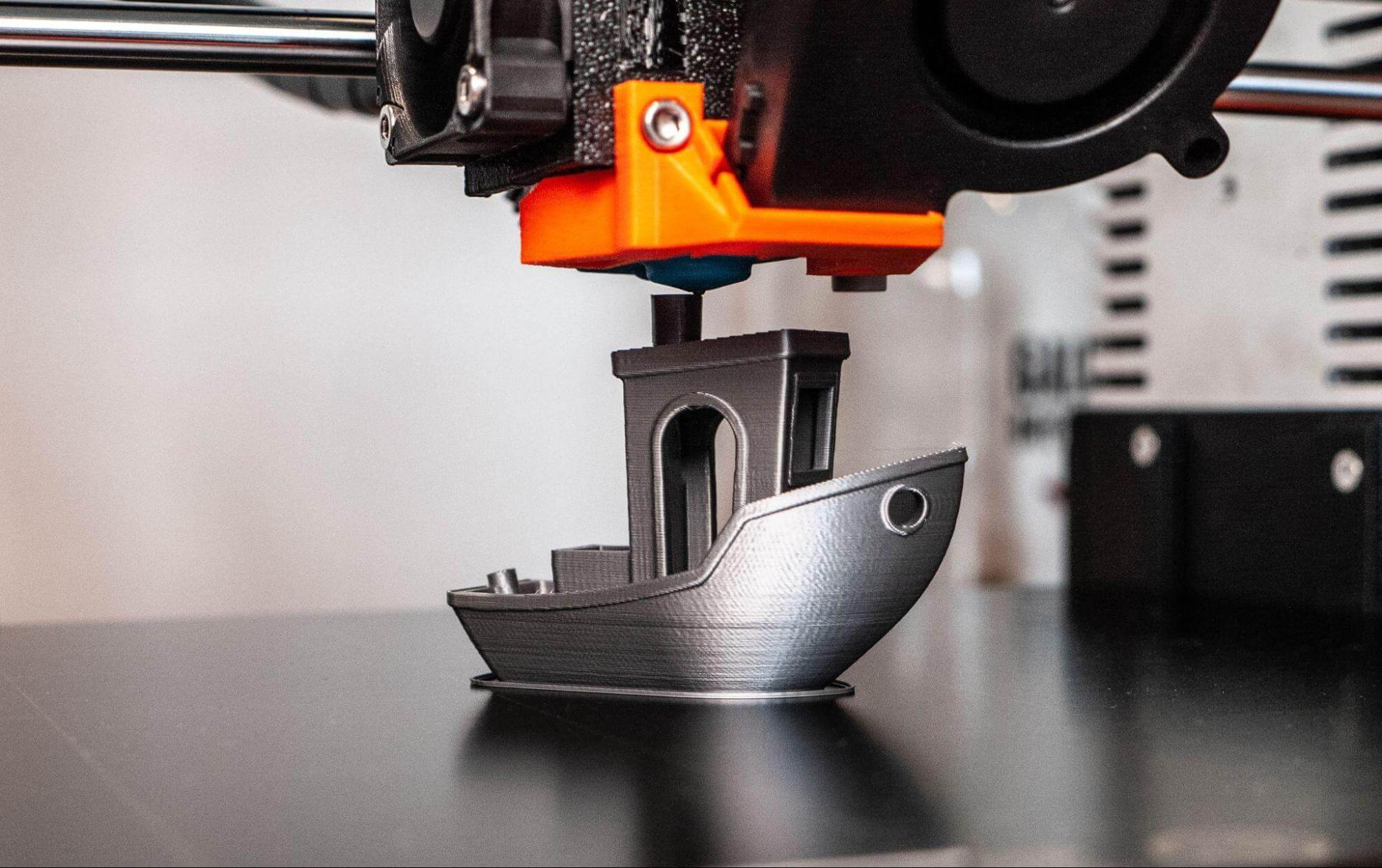
Application Examples for 3D Printing Prototypes
Here are some examples of where 3D printing excels as a prototyping method:
- Consumer Electronics: Enclosures, ergonomic test models, and concept designs
- Medical & Dental: Custom prostheses, anatomical models, and surgical guides
- Automotive: Aerodynamic testing parts, low-load functional components, and custom fittings
Material Comparison: CNC Machining vs. 3D Printing For Prototypes
Another thing to consider when selecting your prototyping process is material compatibility. CNC machining and 3D printing are compatible with a wide range of materials, but not all of them overlap. Let’s take a look at which materials are suitable for these two processes.
Table 2 compares the material capabilities of CNC machining and 3D printing.
Material Type | CNC Machining | 3D Printing |
Metals | Aluminum, stainless steel, steel, titanium, brass, copper | Limited metal powders for DMLS/SLM, including steel (stainless steel and tool steels), superalloys (cobalt chrome and Inconel), aluminum, titanium, copper |
Plastics | ABS, PEEK, Nylon, Delrin, Acrylic, Polycarbonate, HDPE | PLA, ABS, PETG, TPU, Nylon, resins, PEEK, Polycarbonate |
Composites | Carbon fiber, fiberglass-reinforced plastics | Carbon-fiber-filled filaments, glass-filled nylon |
Ceramics | Alumina, zirconia, silicon carbide, boron nitride | Alumina, zirconia, silicon carbide, etc. (through processes like SLA/DLP, binder jetting, etc.) |
Elastomers | Limited (softer elastomers are harder to machine) | TPU, TPE, silicone (specialized 3D printers) |
Wood | Hardwood, softwood, plywood, MDF | Wood-filled filaments |
High-Temperature Applications | Excellent (metals, high-temp plastics like PEEK) | More limited (PEEK and PPSU) |
Table 2. CNC Machining vs. 3D Printing Material Comparison
As seen in the table, CNC machining works with a range of robust materials, including metals such as aluminum, stainless steel, and titanium, as well as engineering plastics like PEEK, nylon, and polycarbonate. It can also handle composites like carbon fiber and even wood, although it’s not always well-suited for flexible or rubber-like materials.
In contrast, 3D printing offers a diverse but slightly different material palette, including plastics like PLA, ABS, and PETG, flexible TPU, high-performance resins, and even metal powders for processes like SLM or DMLS. While 3D printing can’t always match the strength or durability of CNC materials, it opens up possibilities for unique materials like wood-filled filaments and specialized ceramics, which may be a good option for more creative and less structurally demanding applications.
Design Constraints: CNC vs. 3D Printing for Prototypes
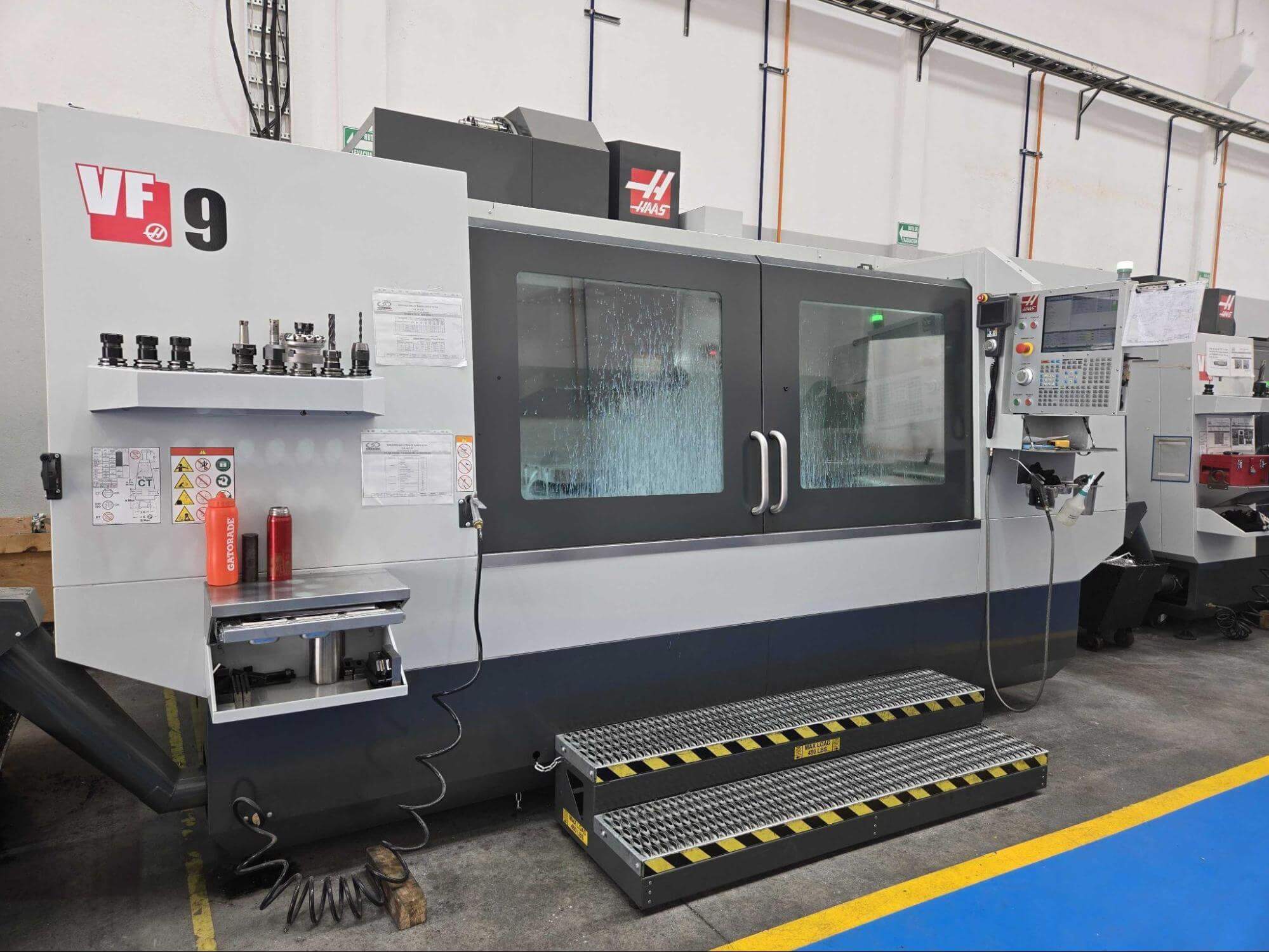
CNC Machining Constraints
While CNC machining is a mature technology, it does have its own set of limitations. Sharp internal corners can be challenging to achieve due to the physical constraints of cutting tools. Additionally, the process is limited to geometries that can be accessed by these tools, making intricate or highly complex designs challenging to produce. CNC machining is fastest for parts with solid, high-strength designs, while parts that have delicate features or organic shapes (freeform, irregular, or inspired by natural forms) can take more time to manufacture.
Pro-Tip: If you need a rapid-turn CNC-machined prototype, check out our article on CNC machining complex parts to ensure you have incorporated the best DFM practices.
3D Printing Constraints
3D printing offers incredible design freedom, but it also comes with a variety of challenges. Overhangs and complex structures often require support materials, which add time and effort to post-processing. While 3D printing can produce lightweight and intricate parts, the strength of printed materials often falls short compared to machined metals, especially for high-stress applications. Additionally, layer adhesion can impact mechanical properties, potentially affecting the overall durability of the final part.
Cost Considerations – Which Is More Budget-Friendly?
While CNC machining tends to have higher material costs due to its subtractive nature, this difference is often negligible in low-volume prototyping, where precision and material performance may take priority over material efficiency. 3D printing, in contrast, uses only the material required to build the design, resulting in minimal waste. However, support structures—often necessary for complex geometries—can add time and labor during post-processing, which may be more relevant than the material waste itself when evaluating efficiency.
For CNC machining, producing one-off, custom, or complex parts can be prohibitively expensive. However, as production volumes increase, the process becomes more cost-effective, whereas with 3D printing, the cost per part remains the same regardless of volume. 3D printing is ideal for low-cost, rapid iterations and is therefore mainly used for early-stage prototyping and design validation. This overall process becomes expensive and slower when large, solid parts are being printed.
The most cost-effective strategy is often a hybrid situation, where 3D printing is used for early-stage prototype manufacturing to quickly and affordably test some design ideas and concepts. When this stage is completed, CNC is often used to create the functional prototypes and final-stage testing. This ensures efficiency and effective use of time and resources throughout the prototyping process.
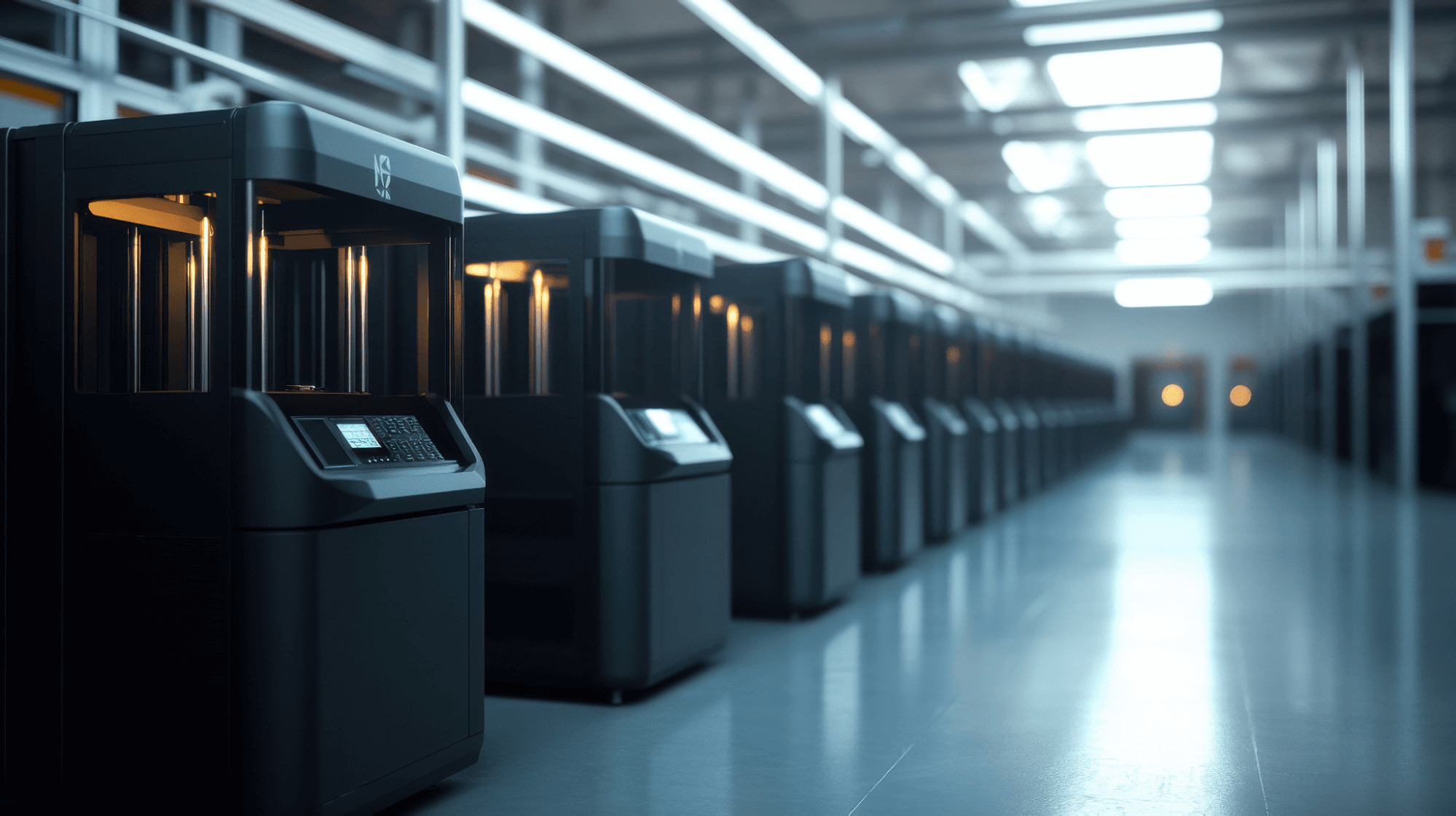
The Future of Prototyping–Hybrid Manufacturing
The future of prototyping is all about hybrid manufacturing—combining the pros of different methods to get the best result overall. For CNC machining and 3D printing, this typically involves starting with 3D printing to iterate through early-stage design cycles before switching to CNC machining for the final product to ensure precision, strength, and a flawless finish. CNC machining can be used for metal parts to post-process 3D-printed components, enhancing their surface quality and accuracy.
Hybrid manufacturing could also be a combination of other processes, such as 3D-printed molds for the injection molding industry. Combining these two processes can bridge the gap between prototyping and full-scale manufacturing.
CNC or 3D Printing for Prototypes – Which Should You Choose?
When it comes to choosing between CNC and 3D printing for your project, it boils down to the following: CNC machining is best for high-precision, functional parts, whereas 3D printing is better for rapid, low-cost iteration. Hybrid strategies, on the other hand, allow you to utilize the strengths of both processes and combine them for the best results.
How Can Fictiv Help with Your CNC or 3DP Prototype?
Fictiv simplifies the transition from prototyping to production by offering CNC machining and 3D printing in one easy platform. Our team provides expert design-for-manufacturability (DFM) feedback to optimize your parts for cost and speed, ensuring you get the most value. We provide an agile, meticulously vetted, and expertly managed global supply chain for custom mechanicals, fueled by world-class experts alongside technology that adapts seamlessly to your evolving needs.
Want to get started on a prototyping project? Get an instant quote today to see which prototyping method is right for your needs!