Time to read: 9 min
CNC robotics is transforming manufacturing by using automated CNC equipment with industrial robots. It blends the accuracy and consistency of computer numerical control (CNC) with the versatility and flexibility of articulated robots that have arm-like structures. Together, these two technologies can increase efficiency, reduce human error, and perform complex tasks.
This article examines the basics of CNC robotics, the technologies behind it, and the trends shaping its future. Fictiv is your online platform for quality CNC machining services and delivers parts in as little as 2 days with 95.4% of orders delivered on-time and in-full. Keep reading to learn more about CNC robotics and get an instant CNC quote.
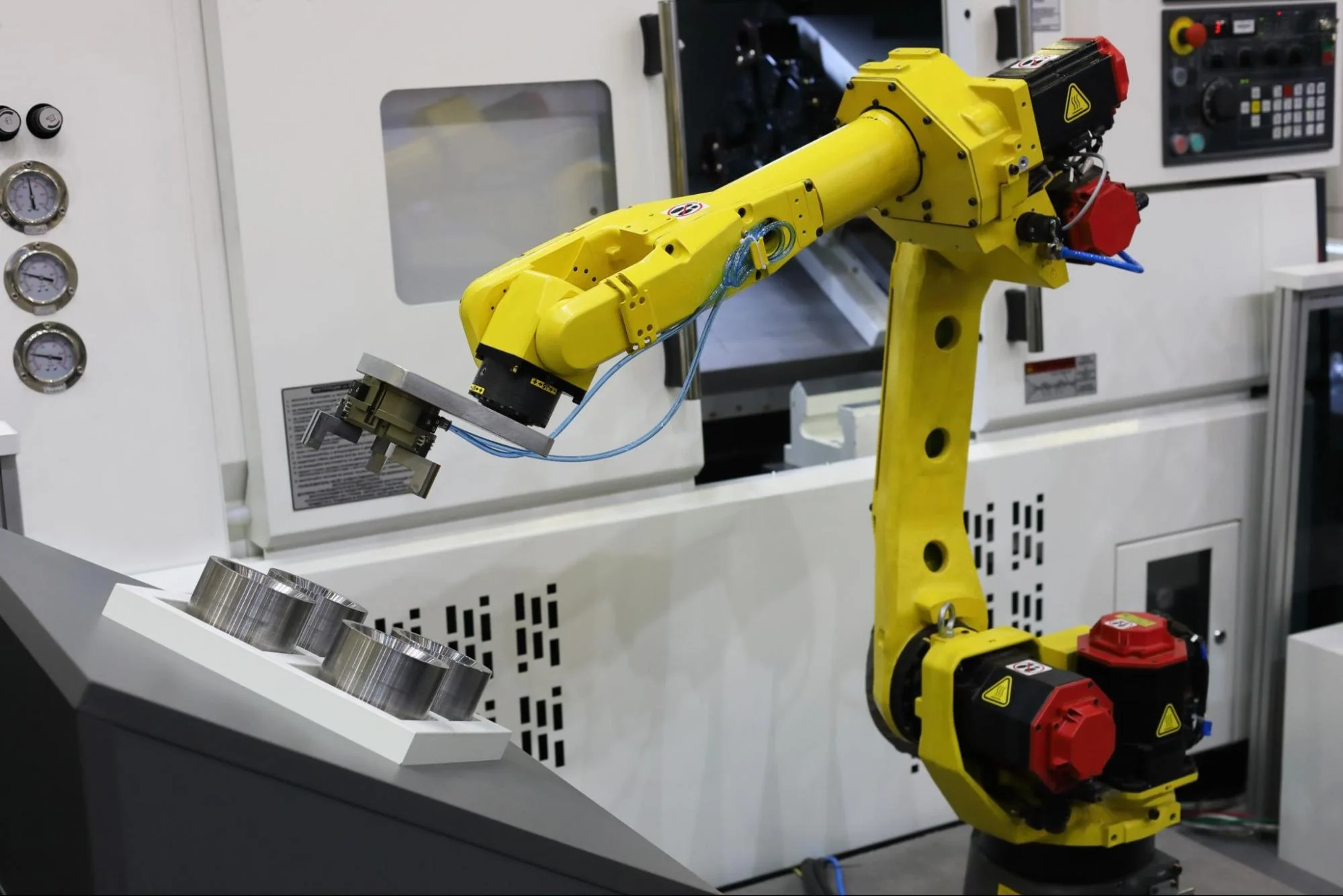
What Is CNC Robotics?
CNC robotics combines the principles of computer numerical control (CNC) machining with advanced robotics. The benefits include increased efficiency, enhanced precision, reduced labor costs, and improved safety. Applications include loading and unloading materials into CNC equipment, handling and positioning workpieces, and performing repetitive tasks.
It’s important to understand that not all CNC machines use robots, and many robots are used independently of CNC equipment. For example, a machine operator might manually load and unload metal from a CNC mill. Similarly, an industrial robot could be used to package parts in an area away from production equipment.
What Is CNC Automation?
CNC automation uses computerized systems to control machine tools and processes such as milling, drilling, grinding, and turning. By shaping materials with high precision and minimal human intervention, CNC machining can produce complex parts with greater accuracy and consistency. Applications include automotive, aerospace, and medical device manufacturing.
CNC machines offer greater flexibility, easier programming, and higher precision than numerical control (NC) equipment, which are more manual in nature. CNC equipment is more expensive and requires some knowledge of computer programming, but operators can easily switch between different programs and run equipment continuously.
During production, a computerized control system manages the speed and motion of CNC machine tools. There are different categories of control systems, but three main types: motion, loop control, and the number of axes. Each control system interprets programmed instructions and helps guide machine tools such as drill bits, hones, and gear shapers.
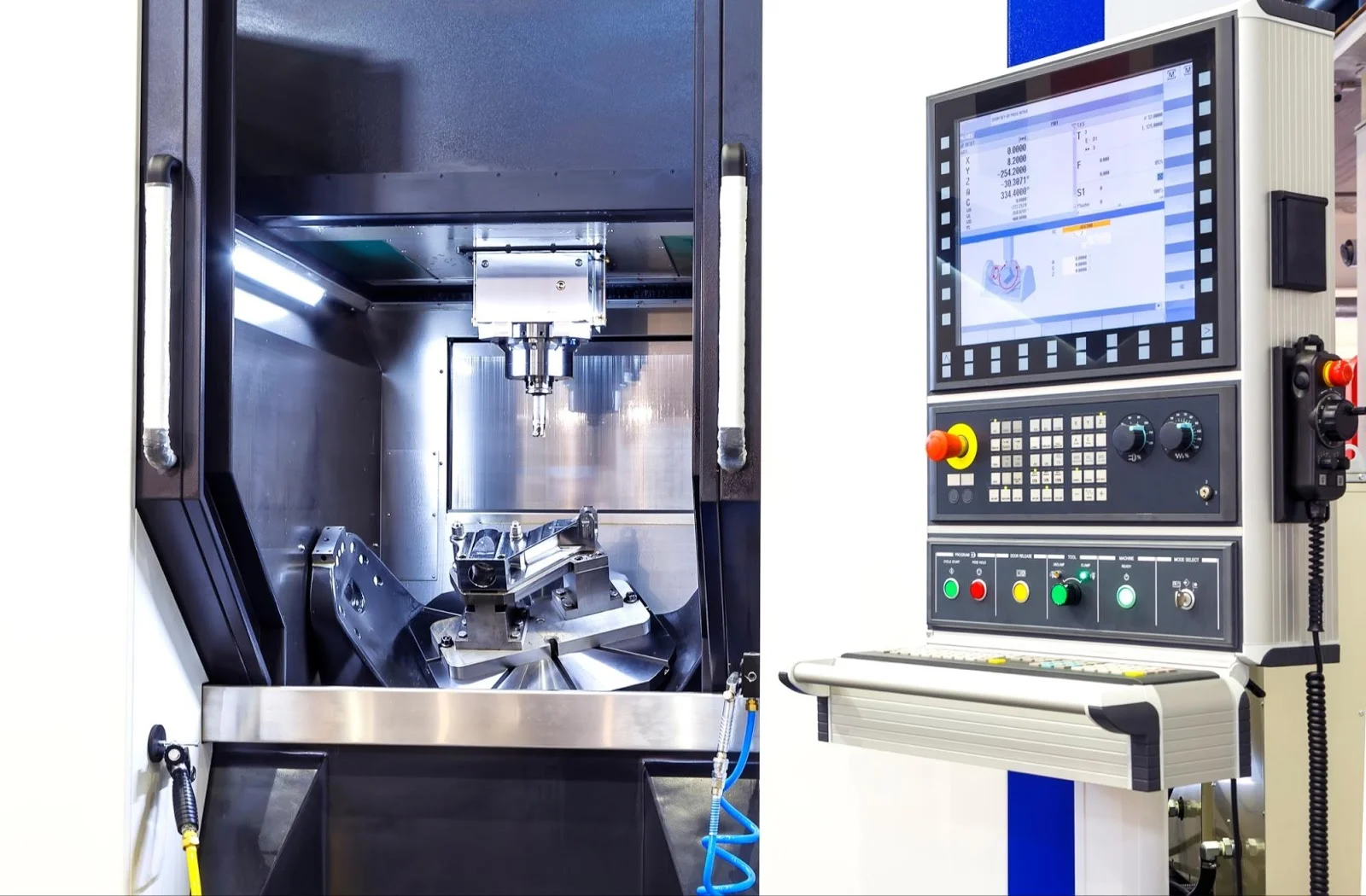
How is CNC Machining Automated?
For designers, CNC automation requires a computer-aided design (CAD) file of your part. The manufacturer then uploads this CAD model to computer-aided manufacturing (CAM) software, which is used to establish CNC machine instructions with tool paths. There are many types of CAM software, but some common types include MasterCAM and AutoDesk Fusion.
During automated CNC machining, adaptive control can adjust parameters in real-time. Feedback from onboard sensors helps monitor and control the machining process while ensuring product quality. Adaptive control systems can automatically modify speeds, feeds, and cutting depths to account for varying conditions, such as tool wear and material inconsistency.
In addition to sensors and vision systems, automated CNC equipment uses programmable logic controllers (PLCs) for managing machine functions and workflows. Conveyors may be used to move parts and materials between different stages of production. For loading and unloading materials and performing repetitive tasks, robotic arms can complement CNC automation.
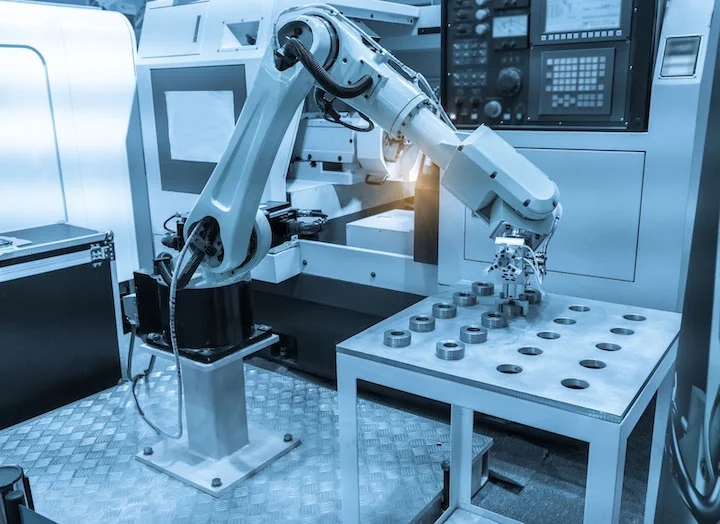
What Is Robotics?
Robotics is a field of technology that involves the design, construction, and use of robots. Like CNC equipment, robots are programmable machines that can carry out a series of tasks either autonomously or semi-autonomously. There are many different types of robots, but these machines typically include sensors, actuators, and end effectors.
Sensors detect environmental conditions such as the presence of a part or workpiece. Actuators convert the signals from sensors into physical actions—typically movement. These actuators are powered electrically, pneumatically, or hydraulically and work in conjunction with end effectors—devices at the end of a robotic arm. Examples include grippers, end mills, and drill bits.
Robotic systems use sophisticated programs and control systems to execute tasks. Typically, these systems include software for motion planning, path optimization, and real-time monitoring. There’s also a controller that tells the robot which tools to use, when to place or remove parts, and how to perform tasks such as packing parts for shipping.
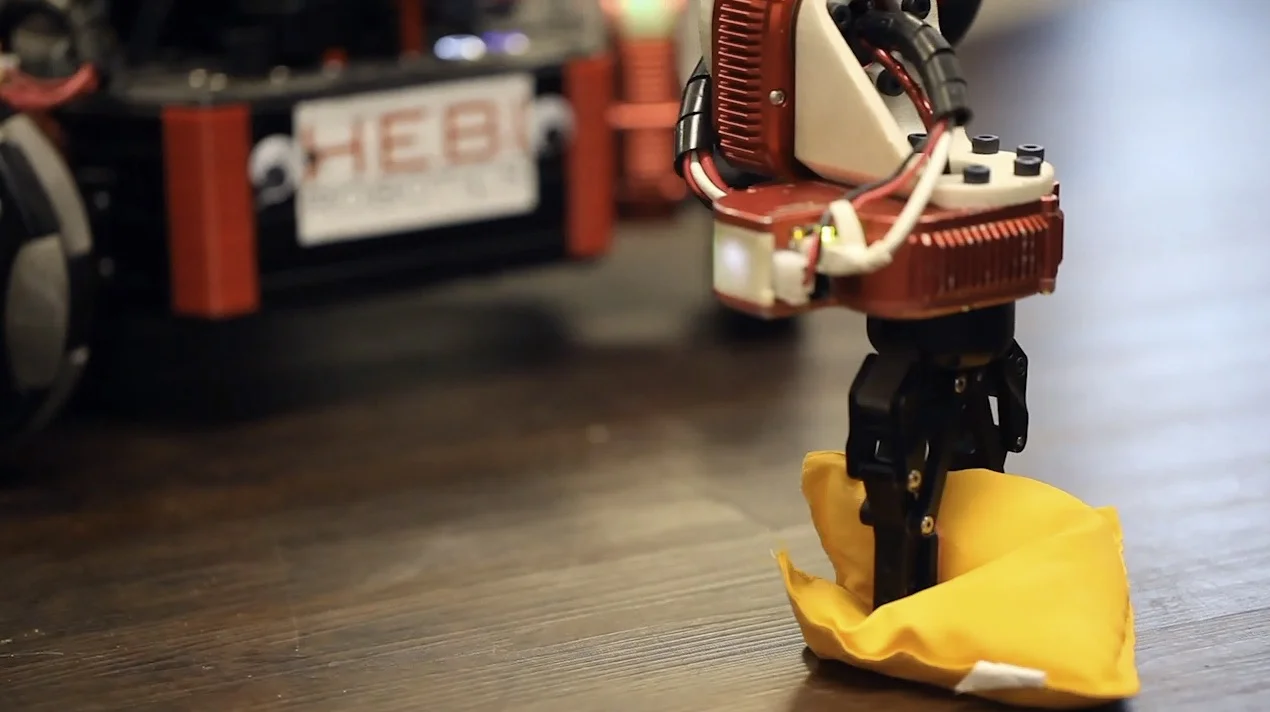
How Are CNC Machines Different From Robots?
CNC machines and robots are related technologies, but they are not the same. That’s because they differ in terms of purpose, movement, flexibility, and structure.
Purpose
CNC machines are used for machining tasks such as cutting, drilling, and milling. Robots are more versatile and can be programmed for either machining operations or for non-machining tasks such as machine tending, product assembly, and material handling.
Movement and Control
CNC machinery operates on fixed axes (typically 3 or 5) using predetermined paths established by machine code. Robots also use pre-established computer code and have a specific number of axes, which are defined as degrees of freedom.
With their articulated joints, however, robots can achieve a variety of positions. For example, robots can bend to perform intricate assembly operations, weld at various angles, and maneuver around obstacles. Although many articulated robots are stationary, the flexibility that their joints provide supports their use with a variety of tasks and environments.
Flexibility
CNC equipment is specialized and supports specific machining tasks. Robots are more flexible and can be reprogrammed and retooled for more operations. Through the combination of automated CNC equipment and robotics, manufacturers can do everything from loading and unloading materials to machining, inspecting, and packaging parts.
Structure
CNC machines need to withstand the forces involved in high-speed machining operations. That’s why they feature a rigid construction built to minimize vibrations and deflections that could affect toolpaths and compromise part precision and quality. Many industrial robots have a plastic shell that’s strong and rigid but more flexible than metal.
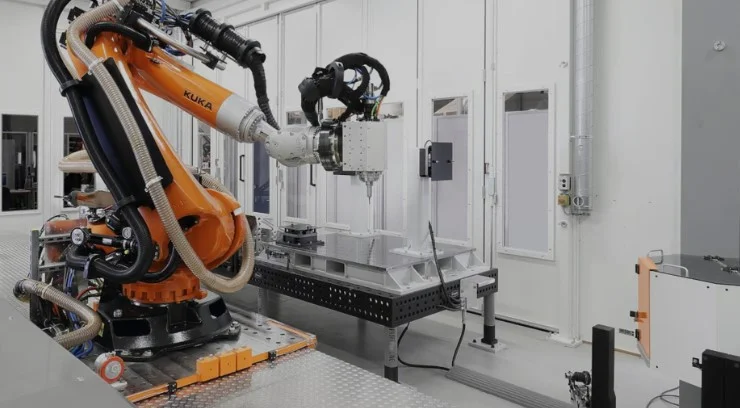
What Are the Tasks of CNC Robotics?
CNC robotics are used for tasks ranging from machining and milling to large-scale production. They’re also used for operations such as routing and welding.
Robotic Machining and Milling
Robotic machining provides a level of flexibility and versatility that traditional CNC equipment can’t match, especially for operations involving large or irregularly shaped workpieces, like those used by the automotive and aerospace industries. The articulated joints in robotic arms enable robots to navigate around large, complex geometries and access hard-to-reach areas.
This is especially valuable in industries where large components with intricate designs require precision machining. Robotic milling, a type of machining, uses robotic arms that hold milling tools to perform precise cutting and shaping operations. Traditional CNC machines can’t follow the same complex paths or make the same detailed cuts.
Large-Scale Production
In addition to handling intricate designs, robot milling is ideal for large-scale production. Because they can operate continuously and with consistent levels of precision, CNC robotics is well-suited for high-volume manufacturing. The ability to automate repetitive tasks reduces the risk of human error, not just for machining but also for tasks such as part inspection.
Robot CNC Router
A robot CNC router can complete intricate cutting and shaping operations with materials that include metal, wood, and plastic. Moreover, manufacturers can quickly switch between different materials and processes for applications such as furniture making. Robotic CNC routing is also used to create decorative wood carvings and intricate plastic components.
CNC Robot Welding Machine
CNC robot welding machines add flexibility to automated welding processes. They follow programmed paths with precision and eliminate part-to-part variations. This combination of consistency and quality supports safety and performance in the automotive industry, and the integrity and durability of aerospace components.
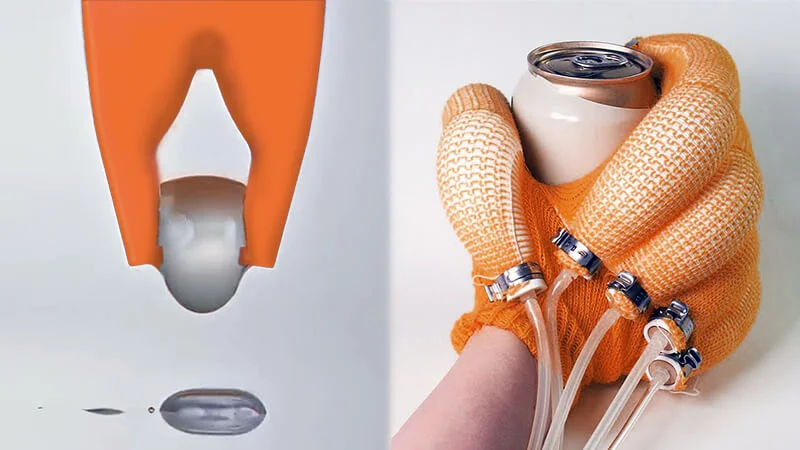
Key Trends in CNC Robotics
Technological advances and evolving industry needs are shaping the future of CNC robotics. Some key trends are described in the sections that follow.
Artificial Intelligence and Machine Learning
Artificial intelligence (AI) and machine learning (ML) are being integrated into CNC robotics to enhance decision-making, predictive maintenance, and process optimization. AI focuses on tasks, such as problem-solving, that normally require human intelligence. ML is a subset of AI that develops algorithms and statistical models that computers can use to make decisions.
Collaborative Robots (Cobots)
Collaborative robots, or cobots, are designed to work alongside humans within a shared space. For example, CNC machining with robotics can use cobots for tasks such as loading and unloading materials. This helps reduce human fatigue and the risk of injury while avoiding manufacturing defects caused by human error.
Soft Robotics
Soft robotics is a subfield of robotics that designs, builds, and uses robots that are made of flexible, compliant materials instead of rigid links. For example, soft fluidic actuators can consist of elastomeric matrices with embedded cloth, paper, fiber, or particles. Soft robots are adept at gentle movements and can handle delicate or irregularly shaped objects.
Swarm Robotics
Swarm robotics involves the coordination of multiple robots to perform tasks collaboratively. This approach can increase efficiency and flexibility in manufacturing processes, particularly in large-scale operations in which multiple processes must be completed to fully fabricate parts such as large structures.
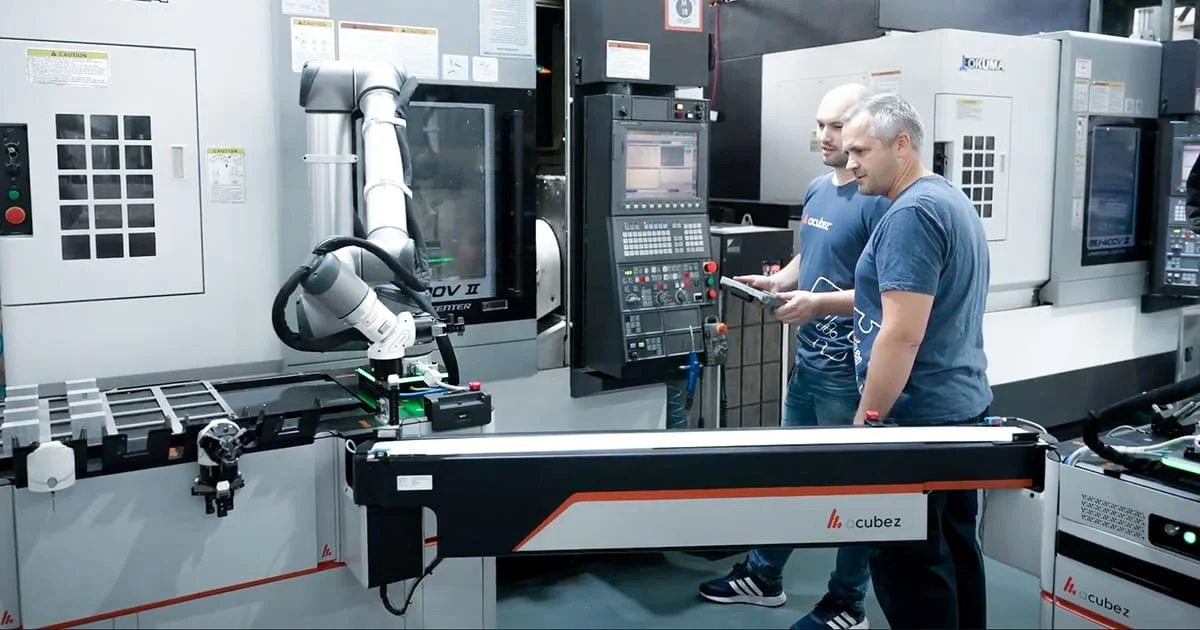
Future Outlook and Market Impact
The industrial robotics market was valued at USD $17B in 2023 and is expected to reach $32.5B by 2028. During this five-year period, the market for cobots is expected to record the highest compound annual growth rate (CAGR). The advantages of collaborative robots are many and include flexibility, ease of programming, and a faster return on investment (ROI).
Cobots aren’t always used in CNC robotics, of course, but they can help manufacturers address workforce challenges. According to a report from Deloitte and the Manufacturing Institute, “many skilled workers in the manufacturing sector are nearing retirement age, and there are not enough younger workers to replace them.”
CNC Robotics Case Studies
These real-world examples demonstrate how CNC robotics can help manufacturers realize business and technical benefits.
Cobot Speeds CNC Machining
Go Fast Campers of Belgrade, Montana makes lightweight campers. Production begins when a billet of aerospace-grade metal is cut into rectangular lengths. These cut pieces are then put onto a tray and delivered to a CNC machining cell, where a Universal Robots (UR) cobot grabs each piece, finds the center, and loads individual parts into a Haas CNC machine.
After the CNC machine performs the first operation, the UR cobot flips the part so that a second machining operation can be performed. The part is ejected from a vise, and the cobot removes the part from the machine. At Go Fast Campers, a single cobot program can control the machining of 174 different parts, and a single operator can run four machine cells.
Industrial Robot Triples Production
A manufacturer of specialized optical equipment tripled production thanks to a Kuka robot and a Mazak Integrex machine. CNC robotics also enabled the manufacturer to deploy its labor resources more effectively. Instead of constantly loading and unloading the Integrex, operators are spending more time on process control, which helps to improve manufacturing efficiency.
Challenges and Limitations
CNC robotics can save manufacturers time and money, but there are some challenges and limitations.
- High Initial Costs: Manufacturers need to make significant upfront investments not just for CNC machines and robots, but also for software and physical infrastructure.
- Complexity and Integration Issues: Industrial robots can be difficult to program, and CNC machines and robots from different manufacturers can be challenging to integrate.
- Accuracy and Precision Limitations: CNC machines are generally precise, but robotic arms may not be as accurate because of joint play, thermal expansion, and wear.
- Reliability and Downtime: Over-reliance on automation can make a manufacturing process vulnerable to technical issues, with limited options for manual intervention.
- Environmental Sensitivity: CNC robots are sensitive to dust, temperature and humidity. That can interfere with robotic sensors and moving parts.
- Space Requirements: CNC robotics systems, especially those involving multiple robot arms or large machines, require significant floor space.
Choose CNC Machining Services From Fictiv
Fictiv’s online CNC machining services use advanced technology and deliver complex parts at ridiculous speeds. From CNC milling and CNC turning to electrical discharge machining (EDM) and gear hobbing, we support a wide variety of metal and plastic materials. In addition, we offer design for manufacturing assistance (DFM) along with your request for a quote.
Are you ready to get started? Create a free Fictiv account and upload your design today!