Time to read: 5 min
Humans do not like change. Believe it or not, after calculators were invented, some people refused to give up their slide rules. Similarly, CNC machining was invented decades ago, yet there are still those who prefer manual machining techniques. This preference persists despite CNC technology’s ability to manufacture and replicate precision parts that are fully interchangeable with one another, while manual methods must make mating components as matched sets or produce custom replacements.
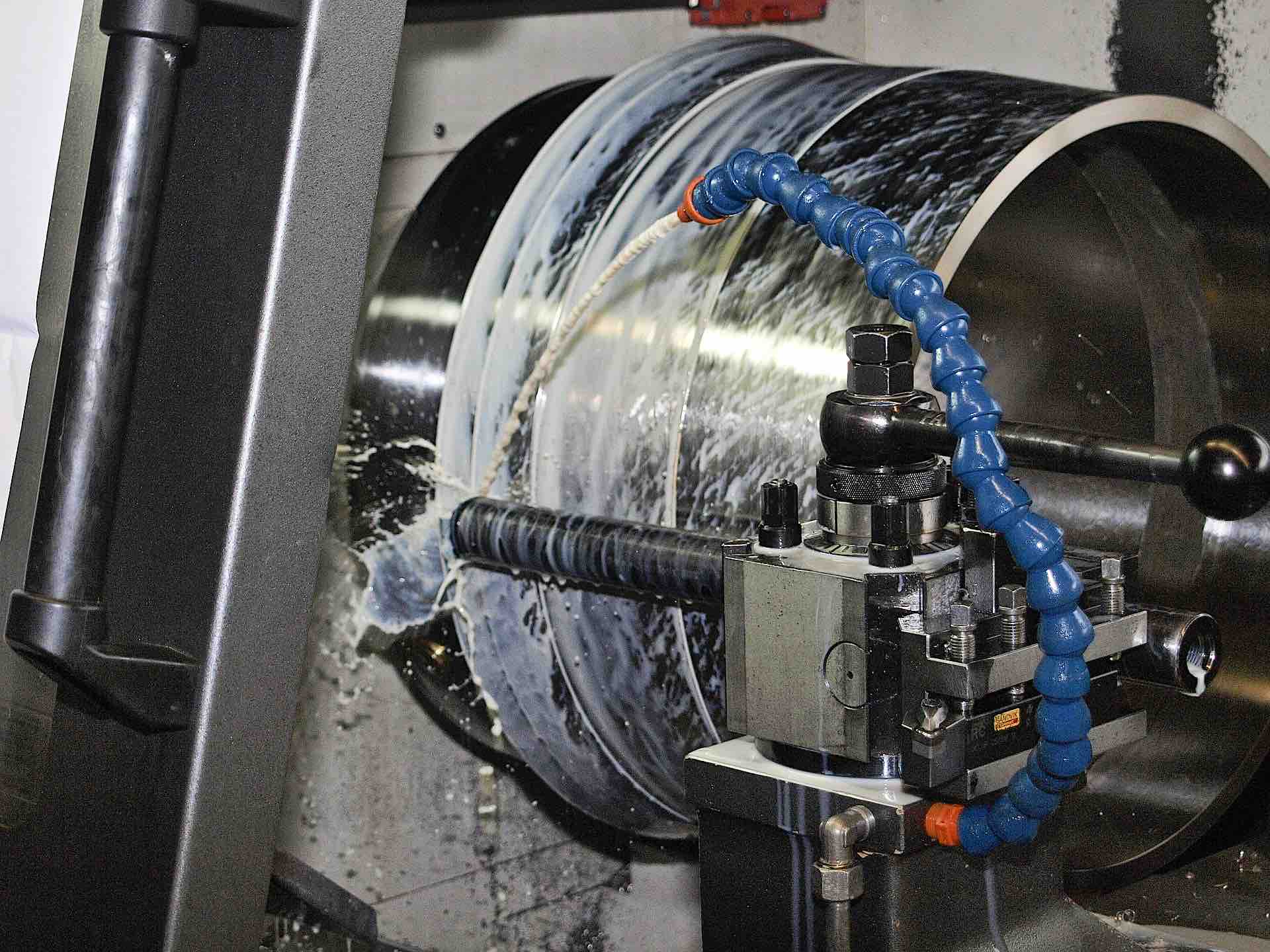
The Different Types of CNC Machines
CNC machining can produce a wide array of parts from the simplest component to the most complex assembly. Need to machine a gear shaft for a vehicle? Or an inlet for a heat exchanger shell on a military transport vehicle? What about a precision electrical contact for a fighter jet or a lifesaving pacemaker?
CNC is the process of “feeding” a set of sequenced instructions into a specially designed, programmable controller and then using it to direct the movements of a machine tool. In all methods of CNC operation, data input and computer-controlled and monitored feedback are critical parts of the machining process. The path the tooling takes in removing material is also controlled by computer programming and calculations involving complex algorithms or interpolation.
Listed below are the most common types of CNC machines and a breakdown of their typical uses and capabilities as compared to manual machines.
1. CNC Mill
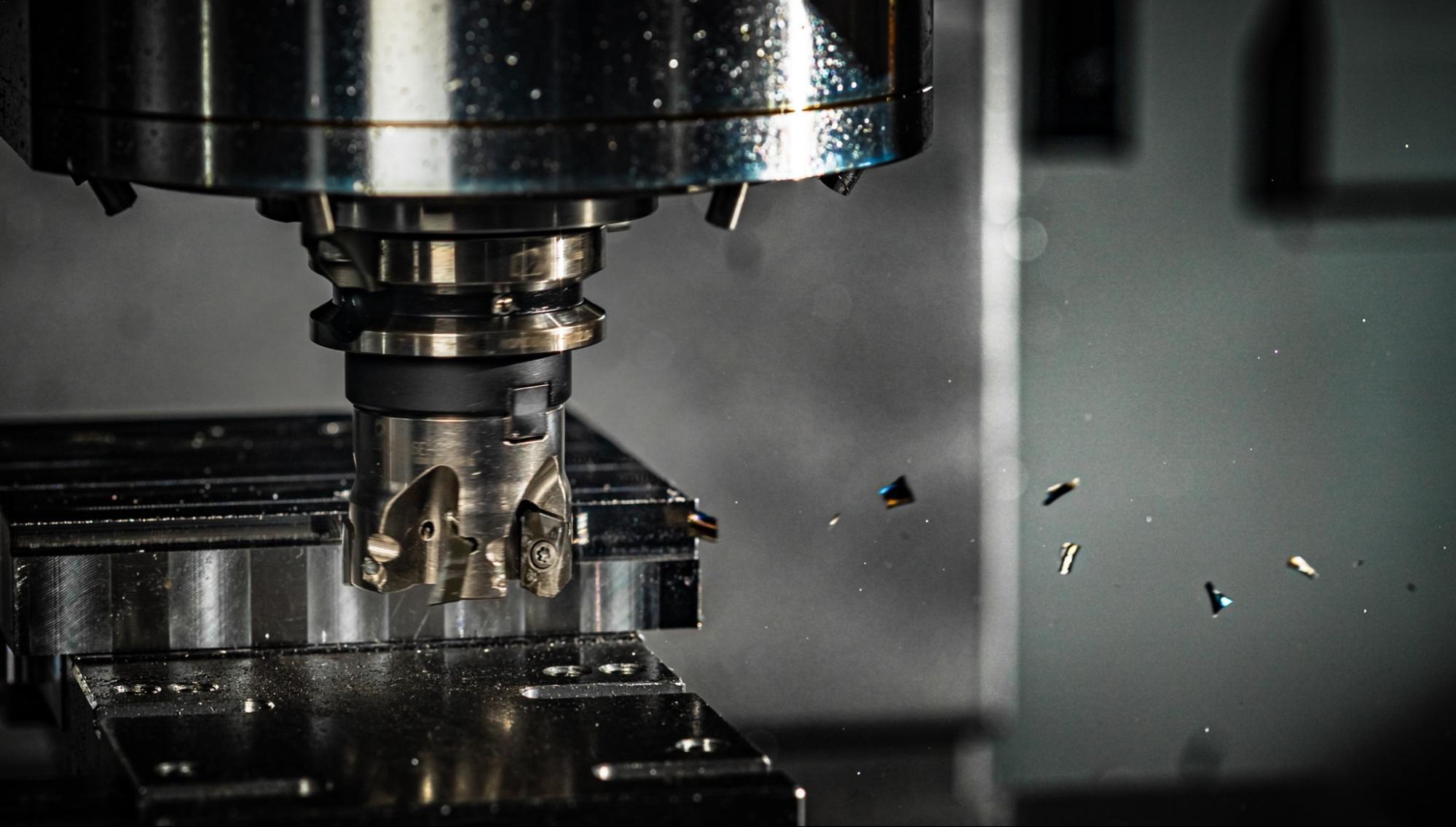
Operation Overview
CNC mills remove material from a workpiece that’s fixtured to a table via contact with a mobile, rotating tool. Typically, the mill has multiple degrees of freedom which allows for machining on multiple planes with one setup/fixture. CNC mills are best for high-precision, high-speed manufacturing, and can drill, form slots, facilitate planing, cut grooves, and engrave material.
Types of Parts
CNC Mills can be utilized to make a variety of parts with intricate geometries, such as:
- Fittings
- Housings
- Brackets
- Gears
- Pacemaker shells
- Holes or material removal on cast parts
- Grooves for welds
- Engine components like cylinder heads
- Prototypes
- Gearboxes
Benefits over Manual Operation
CNC mills provide more precision and accuracy than manual mills because of their ability to utilize computer technology for positioning, depth control, and speed. A human operating a manual mill simply doesn’t have the ability to perform real-time calculations or interpret resistance into feedback to alter the settings as a computer does. Manual mills also typically can only perform material removal in a single plane at a time, which seriously compromises throughput.
2. CNC Lathe
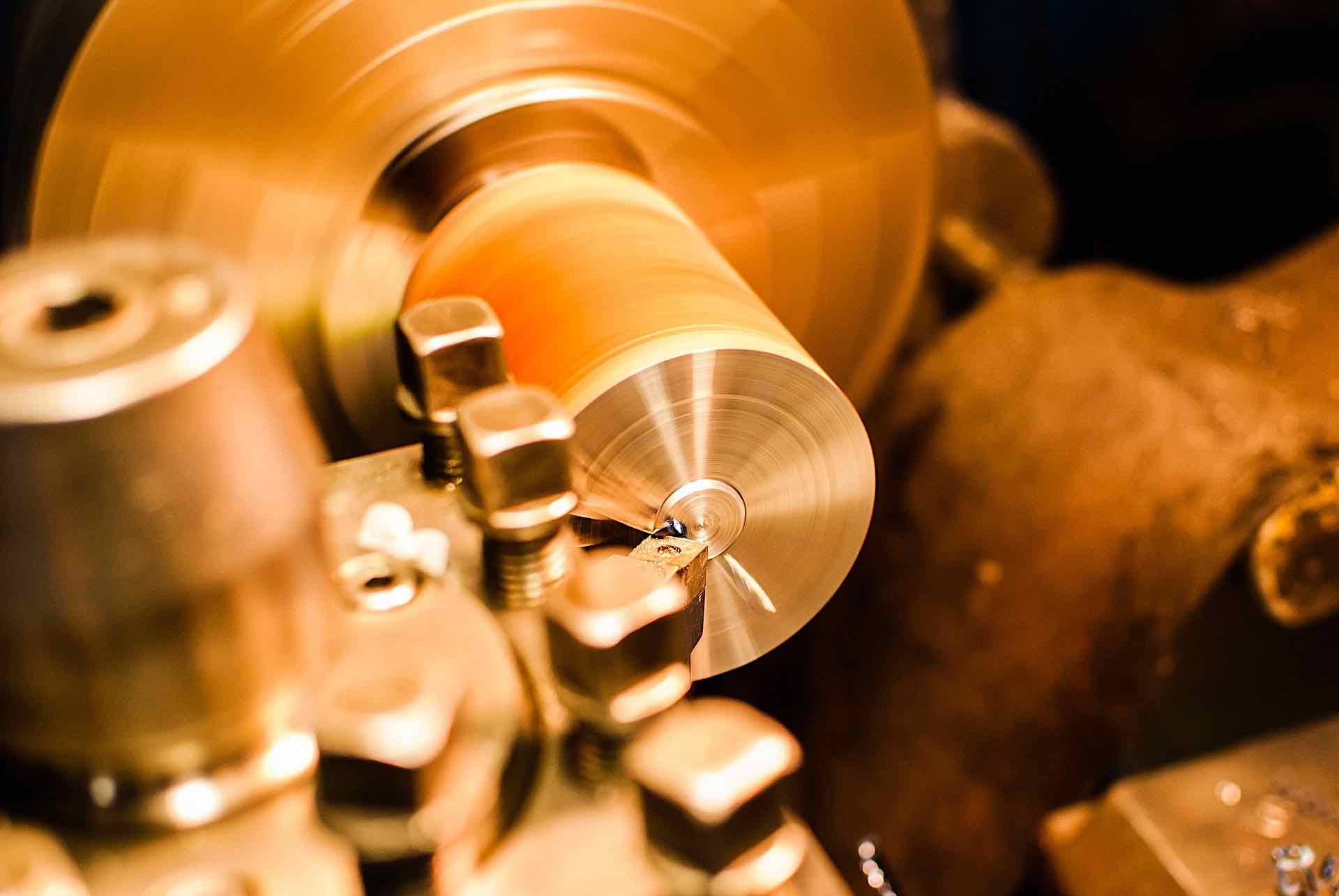
Operation Overview
CNC lathes remove material from a rotating workpiece by applying a stationary cutting tool. They’re primarily used to create conical or cylindrical geometries or flatten a surface. Lathes can also alter surface roughness and drill, bore, ream, tap, face, or chamfer features. A CNC turning machine is a more efficient, enclosed version of a CNC lathe, that has more than one tool changer and is typically equipped with a chip conveyor.
Types of Parts
Conical or circular geometries are the most optimal fit for a CNC Lathe, and so are used to manufacture:
- Fasteners
- Shafts
- Probes
- Pins
- Electrical contacts
- Pipe fittings
- Spindles
- Altered geometric features on previously machined or formed parts
Benefits over Manual Operation
CNC lathes replace manual/conventional lathes that require highly skilled operators with years of training. Manual lathes also must be manually set up, don’t have near the precision of their CNC counterparts, and produce much lower throughput as well.
3. CNC Electric Discharge Machine
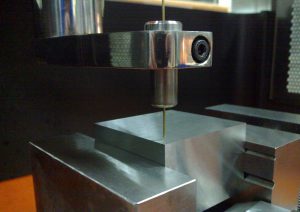
Operation Overview
An Electric Discharge Machine or EDM is the most complex CNC machine on this list. The machining process uses electrical discharges/sparks to remove material from a workpiece submerged in dielectric fluid and placed between two electrodes.
The computer calculates how much voltage to discharge through a dielectric fluid to create the desired shapes or features. The part is partially or fully immersed in dielectric fluid and does not make direct contact with tooling; instead, the spark is used as the cutting tool.
Types of Parts
Due to its nature, an EDM can easily machine intricate parts that traditionally are difficult to manufacture, such as:
- Hardened/heat treated parts
- Thin walled parts
- Molds
- CNC tooling
- Metal matrix composites
- Fashion items like watches and jewelry
Benefit over Manual Operation
EDM services can replace nearly every single manual machining operation, including those performed on mills and lathes, provided the machined materials are conductive. The cost of wire EDM is higher, but the precision and setup provide a great cost-to-benefit ratio.
CNC Machining Delivers Higher Accuracy, Precision, and Interchangeability of Parts
Not only is CNC extremely versatile, as explained above, it’s also widely available. CNC machines are utilized in many industries, and their use is increasing every year. The global CNC machine market is projected to grow from 83.99 billion USD in 2021 to 128.41 billion USD in 2028 – that’s over a 50% increase — and it’s primarily due to an increased demand for greater manufacturing efficiency and precision.
The bottom line is that a CNC machine can perform more calculations and slight modifications to cutting rate, depth, and location than a human working on a manual mill or lathe. CNC machining can deliver tolerances to a thousandth of an inch in minutes, while manual machining requires hours of set-up, calculations, and measuring (not to mention years of training) to accomplish the same thing.
Because of their computational prowess, CNC machines manufacture parts with higher accuracy and precision, which makes them interchangeable with one another in assemblies.
The True Cost Difference Between CNC and Manual Machining
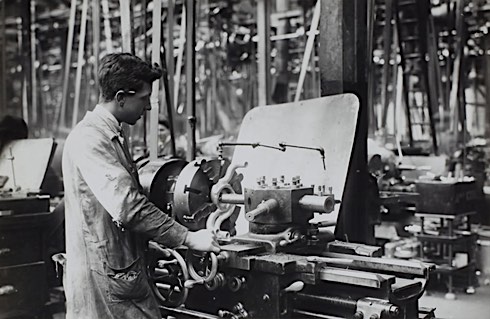
CNC machines are faster and produce less waste than their manual counterparts. Manual machines which have undergone a CNC retrofit have been shown to produce parts 75-300% faster. Increasing throughput reduces part costs by decreasing the number of man-hours required to produce each part. Also, switching tools on a CNC machine can be over four times faster than on a similar manual machine. This results in faster turnaround times to get finished parts to customers.
The higher accuracy and precision of CNC machines also produce a lower scrap rate and therefore a lower part cost. One such comparison calculated the following rejection rates for a 50,000-unit production volume run:
Machining Method | Total Units Manufactured | Units Scrapped | Total Cost to get 50,000 QC Passed Units |
Manual Machine | 56,155 | 6,155 | $202,158 |
CNC Machine | 50,000 | 0 | $172,500 |
Lower scrap rates not only mean more money in your pocket upfront, but higher precision machining tends to decrease customer rejection rate as well. When you have a more precise, repeatable process, the risk for missing defects during inspection is low. This prevents the customer from receiving faulty parts which, in turn, increases customer satisfaction.
Conclusion
Hopefully, this article has helped you understand the benefits of CNC machining and its advantages over manual methods. While there will always be hobby, woodworking, and prototyping applications for manual machining, CNC machining is a vast upgrade when it comes to industrial production.
Not only do CNC machines create parts faster, but those parts are more precise and making them creates less scrap and uses less labor. Plus, they increase production speed which leads to greater customer satisfaction. So, while human devotees of manual machining may not like change, they do like making money and making their customers happy — and CNC machining makes it easier to do both.
Fictiv has a network of experienced and knowledgeable CNC machining partners who can deliver you the precision parts you need. Learn all about our CNC machining service. All you need to do is create an account and upload your part, and you can get an instant quote with free DFM feedback today!