Time to read: 5 min
This is Part III in our series on CNC machining secondary operations, where we’ll be discussing hardware installations — we covered heat treatments and post-processing finishes in Parts I and II.
Hardware installation is an essential step for joining multiple parts to create the final product and is always performed after heat treating and post-processing to avoid altering the hardware.
Among the most common types of hardware installations are fasteners, like screws and bolts. These fasteners go through a clearance hole (which is sized to be larger than the fastener) in one part and screw into the threads of another part to connect them. These threads can be tapped into the part material or installed via a threaded insert.
Other types of fastener include dowel pins, which are for alignment purposes or for press fits, with the pins varying in size and design depending upon the application and fit required.
Threaded Inserts vs. Tapped Holes
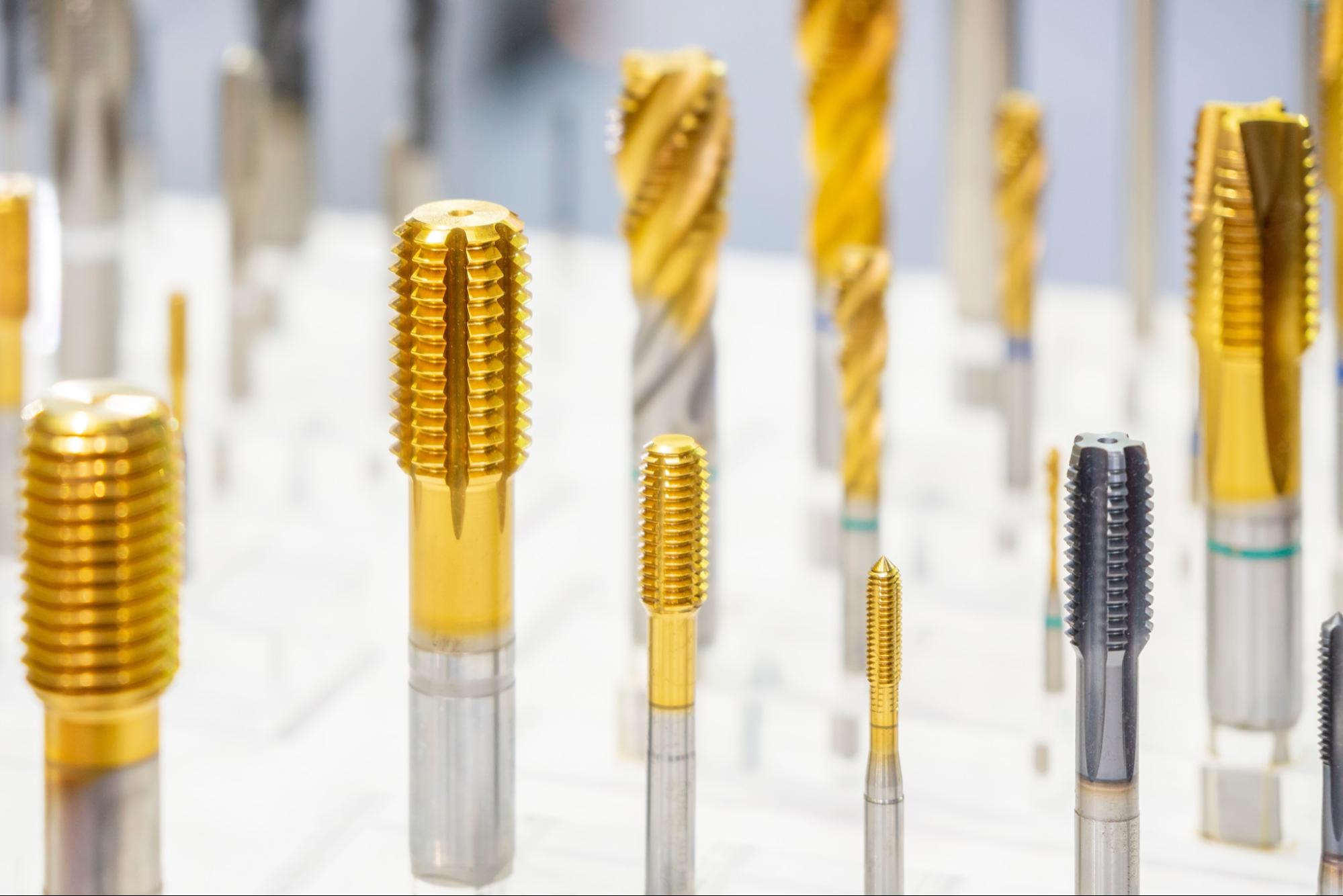
The primary advantage of using a threaded insert instead of tapping a hole is that the insert can be made of harder, sturdier material (like using steel threaded inserts in an aluminum part). Threaded inserts are generally more durable and easy to replace if damaged, while damaged threads in a tapped hole mean the part is usually ruined. Still, inserts require special tooling and may add cost and lead time, especially when post-processing has to happen before they can be fitted.
On the other hand, tapping holes is more cost-effective since it’s done during the CNC machining process, so there are no extra production steps. Tapping also offers more sizes than inserts and doesn’t have a depth constraint, whereas threaded inserts are limited to certain lengths.
Types of Threaded Inserts
When it comes to threaded inserts, you have options, though one of the most commonly used is a helicoil, or helical insert. With helical inserts, you can choose between tanged or tangless and between free run or locking inserts.
Tanged vs. Tangless Helical Inserts
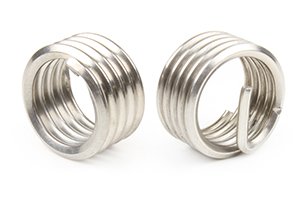
In the image above, you can see the difference between tanged and tangless, or tang-free helical inserts. The tang piece that sticks out across the insert is there so that a tool can drive the insert into a threaded hole. Once the insert is fitted, you hit the tang to break it off and lock the helicoil in place. Tanged inserts are less expensive, but are difficult to adjust and require more inspection to ensure the removed tangs don’t stay in the part or fall into a machine.
Tangless inserts, on the other hand, have a notch that’s used for installation and adjustment — an advantage over tanged inserts that allows them to easily be removed without destroying or damaging the part.
Free run vs. locking inserts
Free run inserts are the standard helicoil and can be tanged or tangless. Locking inserts, also available with or without the tang, have a few segments of the coil that are polygonal, instead of round. These flex outward when a bolt or screw is installed, which exerts extra pressure to keep the bolt in place. Locking inserts are good for assemblies that experience a lot of vibration or impacts, as the helicoil locks the bolt in place.
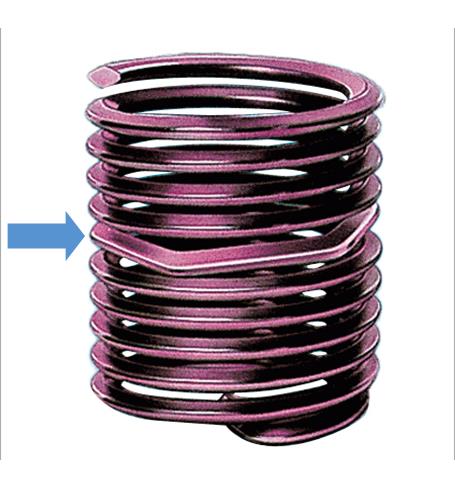
Thread Locking Fluid
Some applications call for fasteners to be extra secure or protected from corrosion, which calls for an adhesive, called thread locking fluid, to do the job. (Loctite is a common example). Thread locking fluid is critical for assemblies that experience vibration.
There are many types of thread locking fluid for different applications. Some are permanent, but some can be loosened with heat or chemical solvents, so it’s a good idea to double-check what kind you have before applying any thread locking fluid!
Dowel Pins
Beyond threaded fasteners, dowel pins are another common hardware installation. Dowels, or dowel pins, can be used to join two parts using a press fit, and are also used to locate features and align parts.
Types of dowel pins
Different types of dowel pins are available for different applications. They’re all the same basic shape: a cylindrical metal pin. Some have features, like threaded holes or grooves, that make them suitable for more advanced use cases.
Standard
Dowel pins have chamfers on both ends for easy insertion. Standard pins are used to align parts and absorb shear forces under load while other fasteners, like socket screws, bear the tensile loads. Standard dowel pins are made to be 0.0002” larger than standard hole diameters to fit snugly (although not tight enough for a press fit).
Precision
Precision dowel pins are a good choice for press fits because they are designed to specific, precise diameters to provide the interference necessary for sturdy press fit assemblies. It’s important to calculate the size and tolerance you need for your precision dowel pin when designing for a press fit (use our tool to help!) The tolerance and amount of interference will depend on the material and size of the hole.
Grooved
Grooved dowel pins have grooves along the side, either axially along the length of a dowel, or in a helical pattern around a dowel. The axial grooves on a pin close when it is pressed into a hole, effectively increasing the diameter of the pin. This locks the pin in more tightly and helps it fit in a wider range of holes, including holes that aren’t perfectly circular.
Reamed holes, which require an extra reaming step, are much more precisely sized and circular and are usually required for dowel pins. However, grooved pins can be used in standard drilled holes, and the pin’s helical grooves also hold adhesives to provide better bonding between the pin and the enclosing hole.
Oversized
Oversized dowel pins are useful for holes that have been damaged. They’re made to be 0.001” larger than standard hole sizes so that the damaged hole can be bored out to fit an oversized pin. They’re also used for holes that aren’t perfectly round and in parts made of softer materials because the softer material is deformed more easily.
Pull-out
Pull-out, or pull dowel pins have a threaded hole in the center. This allows a screw to be inserted to help remove the pin from the hole. Pull-out pins are useful for blind holes, which don’t go all the way through the material.
Final Thoughts
Whether you want to tap your hole, use a threaded insert, or just press in a pin, you’ve got options for fastening parts together! Just remember that hardware installation is always the final secondary operation, after heat treating and other post-processing have occurred, and each operation plays a critical part in transforming CNC machined components into final products.
Fictiv’s network of manufacturing partners is ready to provide CNC machining services, milling, finishing, and delivering the quality, precision parts you need. Create an account, upload your design, and find out what Fictiv can do for you, today!