Time to read: 10 min
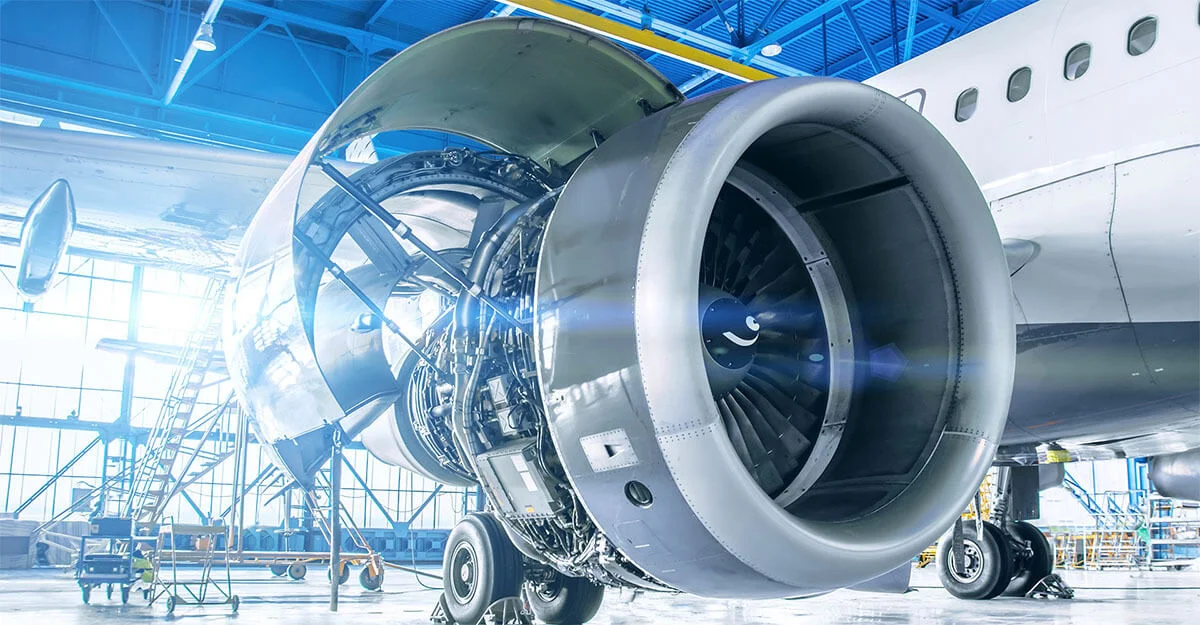
Aerospace CNC machining involves producing high-precision components like engine parts, structural supports, and landing gear with complex geometries and tight tolerances. CNC Machining aerospace parts creates lightweight, durable materials and supports rapid prototyping, low-volume, and high-volume production, meeting strict safety standards while reducing lead times and minimizing human error.
This article begins with an overview of aerospace CNC machining and describes the types of parts that are manufactured and the processes used. You’ll also find information about materials, challenges, quality control measures, cost considerations, and trends. In addition, this article describes the role of CNC machining in aerospace prototyping and production. Fictiv provides AS9100 CNC machining services and even offers an Ultimate Guide you can use during part design.
Why Precision Matters in Aerospace
In aerospace precision machining, achieving tight tolerances is critical since many aircraft components belong to life-sustaining systems such as jet engines and landing gear. The right CNC machining tolerances also ensure that aerospace parts are sized properly for optimal performance, including aerodynamics. In addition, parts that fit together precisely can minimize friction, reduce wear, and promote fuel efficiency—a key concern in both commercial and military aviation.
Importantly, aerospace CNC machining can produce precise parts repeatedly and consistently. These interchangeable components are essential for global fleets where maintenance needs to be fast and efficient to avoid costly aircraft on-ground (AOG) situations. Failure to meet part quality and safety standards can also lead to part recalls or hefty fines from regulatory agencies like the U.S. Federal Aviation Administration (FAA) and the European Union Aviation Safety Agency (EASA).
Types of Aerospace Components Produced with CNC Machining
CNC aerospace machining is used to produce the following types of aircraft parts.
- Structural
- Tail section
- Engine and powertrain
- Interior
- Doors and hatches
CNC machining is often also used for satellites, spacecraft, and rockets.
Structural Components
CNC-machined structural components are used throughout the airframe. Examples include ribs, spars, flaps, and ailerons. Ribs and spars provide mechanical strength and help the wing to maintain rigidity under significant forces. Flaps and ailerons are movable surfaces that help direct airflow. Landing gear struts and beams are also machined to exact specifications because they must withstand extreme stresses.
Tail Section Components
Aircraft CNC machining is used to create the internal structures for an airplane’s vertical and horizontal stabilizers, as well as aerodynamic surfaces that provide longitudinal (pitch) and/or directional stability and control. Elevators and rudders, control surfaces on the tail of the aircraft that must move smoothly, are also precision machined.
Engine and Powertrain Components
Aerospace CNC machining can produce turbine blades and housings, engine mounts, and engine pylons. Turbine blades have complex geometries. Engine mounts must reliably secure the engine to the airframe to handle the stresses of flight. Engine pylons connect an aircraft’s engines to the wings or fuselage and are precisely machined to withstand loads and engine vibrations. Thermal management components, like heat exchangers, are also often CNC machined, along with casting and brazing.
Interior Components
The cockpit and cabin of an aircraft also contain numerous CNC machined components. Examples include seat tracks, support brackets, clamps, and mounts. Often, these smaller parts help hold larger assemblies together. They may also be critical to an airplane’s structural integrity and safe performance.
Doors and Hatches
Landing gear doors and access panels require precision machining. Whether it’s for passengers, cargo, or maintenance access, aircraft manufacturers need doors and hatches that fit precisely and have smooth surfaces that support proper sealing. When aircraft doors are closed during flight, they must withstand tens of thousands of pounds of pressure. Leaks are unacceptable because of safety concerns.
CNC Machining Processes Used in Aerospace Manufacturing
CNC machining for aerospace manufacturing can be divided into the following categories.
- 3 Multi-axis CNC machining (milling)
- 5-axis CNC machining (milling)
- Precision CNC turning (lathe)
- CNC grinding and finishing
CNC machining is good for both prototypes and high or production volumes. In addition, aerospace CNC machining can be integrated with additive manufacturing (3D printing).
3-Axis CNC Machining
3i-axis CNC machining is often utilized for CNC parts with simpler geometries and lower complexities. The equipment may cost less, reducing capital expenditures and allowing small businesses to tap into CNC milling. This CNC aerospace machining process can be used for larger parts such as fuel pumps, motor housings, and landing gears. Think of a 3-axis CNC mill as a powerhouse that is really capable of removing large volumes of material.
5-Axis CNC Machining
Aerospace parts that have intricate geometries that can be difficult or impossible to produce with 3-axis machining are better suited for 5-axis CNC machining. Parts best-suited for 5-axis machining may have machined features on multiple faces or complex contours. With their ability to allow for simultaneous movement along more axes, 5-axis CNC machines can approach parts like turbine blades and impellers from almost any angle. The advantages of 5-axis CNC machining include reduced setup time, better surface finishes, more efficient material removal, and support for complex holes and undercuts.
Precision CNC Turning
CNC turning is a key part of machining in the aerospace industry and is used with round and cylindrical aerospace parts that require a high degree of precision.CNC turning is accomplished using a CNC lathe machine, where the stock is rotating and material is removed when the stock makes contact with a stationary tool. Example applications include the shafts and threaded components used in mechanical systems. Precision CNC turning is also used for aerospace fasteners, pins, and bushings. When CNC equipment is automated, manufacturers can readily produce high volumes of identical parts.
CNC Grinding and Finishing
Shafts, bearings, and other aerospace components that are subject to friction need high-quality surface finishes to ensure smooth operation. CNC grinding refines the finish on these machined components without affecting critical part tolerances. When CNC grinding machines are highly automated, there’s also greater part-to-part consistency.
Additive Manufacturing Integration
Aerospace CNC manufacturing can be integrated with additive manufacturing (AM) for post-processing operations. There are also hybrid machines that can switch between adding material with 3D printing and subtracting material with CNC machining. This form of hybrid manufacturing combines the design freedom of AM with the precision of quality CNC machining.
Materials Used in Aerospace CNC Machining
The materials used in aerospace CNC machining are both strong and lightweight.
Examples include:
- Aluminum Alloys
- Titanium and Superalloys
- High-Performance Polymers
- Composite Materials
With additive manufacturing integration, 3D printed plastics and metals can also be used.
Aluminum Alloys
Aluminum alloys are strong, lightweight, corrosion resistant, and cost-effective. They also have good thermal conductivity for effective heat dissipation and are fatigue resistant. Several aluminum alloys are specifically tailored to aerospace applications.
For example:
- Aluminum 2024 provides high strength, excellent machinability, low density, and good fatigue resistance, enabling use in thermal management and structural components.
- Aluminum 6061 is moderately strong and corrosion resistant. It’s used in structural components, hydraulic systems, engine parts, fittings, and couplings.
- Aluminum 7075 is both strong and durable. It’s used in aircraft wings, fuselage bulkheads, and structural parts.
Titanium and Superalloys
Titanium alloys are valued for their high strength-to-weight ratio, excellent corrosion resistance, and ability to withstand high temperatures, higher than steel or aluminum alloys. Titanium alloys also possess some excellent fatigue resistance, along with a coefficient of thermal expansion that is similar to composites commonly used in the aerospace industry, further enabling wear resistance – thermal and mechanical. With these properties, titanium is often used for airframes, engine parts like casings, fasteners, landing gear, and structural elements.
Super alloys are metals that offer better creep, oxidation, and corrosion resistance than traditional alloys. A superalloy, also known as high-performance alloy, is a metal alloy developed for high temperature, high pressure, and highly corrosive environments. These materials typically exhibit exceptional mechanical strength, resistance to thermal creep deformation, good surface stability, and resistance to corrosion or oxidation. The base alloying element in superalloys is usually nickel, cobalt, or iron, combined with varying amounts of chromium, molybdenum, titanium, aluminum, and other elements. Superalloys are critical in applications such as jet engines, turbine blades in power plants, and in the chemical and petrochemical industries, where ordinary metals would fail under the extreme operational conditions. Both are used on aircraft and spacecraft, but superalloys such as Inconel and titanium alloys such as Ti-6AL-4V are difficult to machine.
High-Performance Polymers
Metals aren’t the only materials used in CNC aerospace machining. PEEK, a high-performance polymer, is used in critical engine parts because it supports fine tolerances and can withstand high temperatures. ULTEM, another high-performance polymer, has one of the highest dielectric strengths of any thermoplastic. It’s often used for insulating the electrical cables in aircraft cabins.
Various plastics are also widely utilized in aircraft interiors.
Composite Materials
Composite materials for lightweight, high-strength parts are also well-suited for CNC machining. Carbon fiber, fiberglass, and aramid fibers are three examples in the aircraft industry. Today, approximately 50% of the Boeing 787 Dreamliner is made of composites. The wings and fuselage of the Airbus A350 XWB also use strong, lightweight composite materials for greater fuel efficiency.
Key Challenges in Aerospace CNC Machining
Aerospace CNC machining supports a variety of part types, manufacturing processes, and materials. However, it can be challenging to achieve the tight tolerances and complex geometries that many components require. Designer engineers need to optimize part tolerances for each application, and machinists need to select the most efficient manufacturing method. Don’t forget tolerance stack analysis and try to use GD&T callouts where possible.
When working with multiple components, designers also need to prioritize tolerances for parallelism and perpendicularity. Otherwise, CNC machined parts may not align properly. Material selection is critical because different aerospace materials have different mechanical, thermal, and electrical properties. Work hardening, stress, and thermal effects can all complicate machining. If your application requires corrosion resistance, there are many different surface treatment and coating options.Common surface finishing in the aerospace industry includes anodizing, conversion coating, electroplating, painting, and passivating. ..
CNC Machining Quality Control in Aerospace
For the best results, it’s essential to design CNC-machined aerospace parts with the final inspection process in mind. That’s because the more difficult a part or feature is to machine, the harder it is to measure tolerances. Coordinate measuring machines (CMMs), laser scanning, and other inspection methods and non-destructive testing (NDT) techniques are commonly used.
CNC machining quality control also requires process repeatability. The global aerospace industry demands consistency and reliability across production runs, and your project may require a manufacturing partner that is AS9100 certified. Unlike ISO 9001, which is used by a variety of industries, AS9100 is specific to aerospace but also more comprehensive as it contains all of the quality management system requirements of ISO 9001 plus additional clauses that pertain to aerospace part manufacturing quality, specifically.
Cost Considerations in Aerospace CNC Machining
Material selection, part complexity, and production volumes are the three main drivers of aerospace CNC machining costs. By balancing cost efficiency with the need for precision and quality, designers can avoid cost overruns. Part cost isn’t the only consideration, however. Lightweight composites can be more expensive than metals but can help reduce aircraft fuel costs.
Designers also need to compare the pros and cons of outsourcing aerospace machining vs. keeping the work in-house. Titanium alloys and superalloys are among the most difficult metals to machine, so you may need a CNC machining service that specializes in these materials. Similarly, if your in-house shop only has 3-axis CNC equipment, you may need access to a 5-axis CNC machine instead.
The Role of CNC Machining in Aerospace Prototyping and Production
Among its advantages, CNC machining supports the quick iteration of aerospace prototypes. Depending on the complexity of your part, turnaround times can range from a few hours to a few days. That’s especially important during the design phase when iterations are common. Then, once CNC machines are programmed, they can support low-volume to high-volume production.
During aerospace prototyping, designers need to test parts for form, fit, and function. Aerospace CNC machining can produce parts with extreme accuracy, ensuring that a prototype represents the final product as closely as possible. This level of precision is critical for aerospace designers, but CNC machining’s ability to work with a wide range of materials is also essential.
For example, if an aerospace part is made from aluminum 6061, a designer can use the same material during both prototyping and production. That may not be possible with 3D printing since the materials used with additive manufacturing don’t have the same properties as the materials used with subtractive manufacturing processes like CNC machining.
When it’s time for production, aerospace CNC machining ensures that each part is produced with consistent quality. Plus, 5-axis machining can achieve complex geometries and tight tolerances that may not be possible with other manufacturing methods. The custom tooling that’s used in aerospace machining includes specialized clamps, jig pins, and bushings.
Future Trends in Aerospace CNC Machining
Artificial intelligence (AI), machine learning (ML), and advanced automation are shaping the future of aerospace manufacturing and driving innovation throughout the industry.. Hybrid manufacturing and Industry 4.0, the integration of traditional CNC machining with digital and additive manufacturing technologies, are also helping aerospace manufacturers achieve greater production efficiency.
At the same time, the entire aerospace sector is becoming greener. Designers are developing aircraft that consume less fuel or use more sustainable energy sources, such as algae biofuel. Electric vertical takeoff and landing (EVTOL) aircraft are also transforming aviation while replacing liquid fuels with battery power. Yet EVTOL still needs CNC machined aircraft parts.
Choose Fictiv for CNC Aerospace Machining
Fictiv provides aerospace CNC machining services for aerospace companies and others and works with a carefully vetted network of AS9100 certified manufacturers. Importantly, we also provide complex parts at ridiculous speeds. That’s why when Heliospace needed faster turnaround on aerospace parts, they asked Fictiv to help them accelerate product development. We cut their lead times from 18 weeks to 2 weeks.
Fictiv also reduced lead times for Honeywell Aerospace from 22 weeks to just 3 weeks. When this well-known company needed to speed up product innovations to meet customer expectations, Fictiv delivered. Our engineering experts provided fast design for manufacturing (DFM) feedback for the high precision CNC machining an auxiliary power unit (APU).Do you need aerospace CNC machining services? Create a free Fictiv account and upload your part design.