Time to read: 9 min
CNC machine safety is about reducing the risk of accidents and injuries caused by computer numerical control (CNC) equipment like mills, drills, lathes, and routers. From moving parts, hot surfaces, slippery fluids, and sharp edges to sparks, chips, and noise, CNC machinery can put unprotected workers at risk.
Properly understanding how to stay safe when interacting with CNC machines is imperative to manage and mitigate these hazards, which can occur during routine operations or because of machine failure. This guide provides tips to help you stay safe in the CNC shop.
Important: These tips are not intended to be comprehensive guidelines or replace existing safety standards. Rather, they’re a starting point for further exploring the specific frameworks or regulations that may affect your working environment.

Hazard identification and safety compliance are essential, but there’s more to CNC safety than wearing personal protective equipment (PPE) and following a CNC machine safety checklist. Remember, too, that you can outsource CNC machining to Fictiv and (safely) get complex parts at ridiculous speeds.
Understanding Safety Hazards
CNC machining safety hazards can be classified into four categories:
Mechanical Hazards | Moving parts such as spindles, cutting tools, and workpieces can injure an operator’s hands, fingers, wrists, and arms. |
Electrical Hazards | The electrical systems that power CNC machinery can expose personnel to electrical shocks or fires. |
Flying Debris | High-speed cutting and machining processes can generate flying debris, such as chips, which can cause eye injuries. |
Ergonomic Hazards | Prolonged operation, poor posture, or loading or unloading heavy materials can lead to musculoskeletal disorders. |
In the United States, the Occupational Health and Safety Administration (OSHA) publishes health and safety regulations for CNC machines in OSHA Standard 1910.212(a). As part of a comprehensive safety program, companies should also identify the specific hazards in their manufacturing operations and work to mitigate them.
Personal Protective Equipment (PPE)
Workers must wear appropriate personal protective equipment (PPE) when operating or working near CNC machinery. In both the U.S. and Canada, employers must provide eye, face, foot, and ear protection. Employees such as CNC operators and machinists are responsible for wearing this equipment.
The following types of PPE are often worn to promote CNC machine safety:
- Safety glasses/shields shield the eyes from flying debris and coolant splashes. They are impact-resistant and include face shields, safety glasses, and safety goggles.
- Cut-resistant gloves protect the hands and wrists from cuts, abrasions, and puncture wounds. They may also provide extra gripping.
- Hearing protection reduces the intensity of sound that reaches the eardrum to help prevent noise-induced hearing loss. Earplugs and earmuffs are commonly used noise-reduction measures.
- Protective clothing includes aprons and footwear. Examples include flame-retardant fabrics, steel-toe boots, and S3 safety shoes.
The National Institute for Occupational Health and Safety (NIOSH), a U.S. federal agency that makes recommendations to prevent workplace injuries, puts PPE at the bottom of a hierarchy of controls that are designed to protect workers from injury.
This means that while PPE is required, it’s the last line of defense in CNC machine safety. The higher level controls are more effective in reducing injuries during CNC machining.
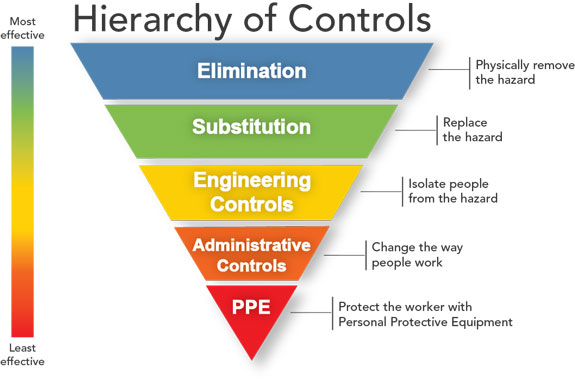
Machine Guarding for Accident Prevention
Machine guards are safety barriers or devices that enclose hazardous parts of equipment. These protective measures are classified as engineering controls, and machine guards are designed to prevent employees from intentionally or accidentally contacting these parts while the machine is running.
OSHA publishes specific machine guarding standards, including 1910.212(a)(3)(iv) for milling machines. Machine guards may be factory installed, or added to the machine after it arrives at a CNC machine shop.
Three main types of machine guards are fixed, interlocking, and adjustable.
- Fixed guards attach to machinery and are not adjustable by employees while the CNC machine runs. Examples include fences, gates, and protective covers for cutting tools.
- Interlocking guards, otherwise known as safety interlocks, are moveable and combine a physical barrier with a safety mechanism such as a switch. When the guard is open, they stop the machine.
- Adjustable guards can be repositioned or resized depending on the machining operation or the size and thickness of the workpiece. They require the most operator involvement between runs.
Guards are standard CNC machine safety features, but other precautions are also used. Examples include light curtains, safety contact mats, and CNC machine safety glass:
- Light curtains use infrared light beams and self-monitoring circuitry to send an automatic stop signal to the CNC machine if the light beam is interrupted.
- Safety contact mats send a stop signal to the equipment when stepped upon. Often, these specialized floor mats include anti-slip features.
- CNC machine safety glass is impact-resistant and extremely resistant to heat and coolants

Emergency Stop Switches and Lockout/Tagout (LOTO)
CNC machines are also equipped with emergency stop switches that, when pressed, shut down the machine quickly. Known as E-stops, these switches remain in the off position until they are manually reset. Typically, an E-stop features a large red button that is easy to recognize and press during emergency stop procedures.
Operators must also recognize the locks and tags used in lockout/tagout procedures. These physical locks and warning tags are designed to de-energize equipment and prevent accidental startup, typically during maintenance or repairs. CNC operators should not attempt to remove locks and tags, which are designed to protect them from the release of hazardous energy.
CNC machine shops are responsible for training all personnel who will be using CNC machines or performing work in any area near a CNC machine on lockout/tagout procedures.
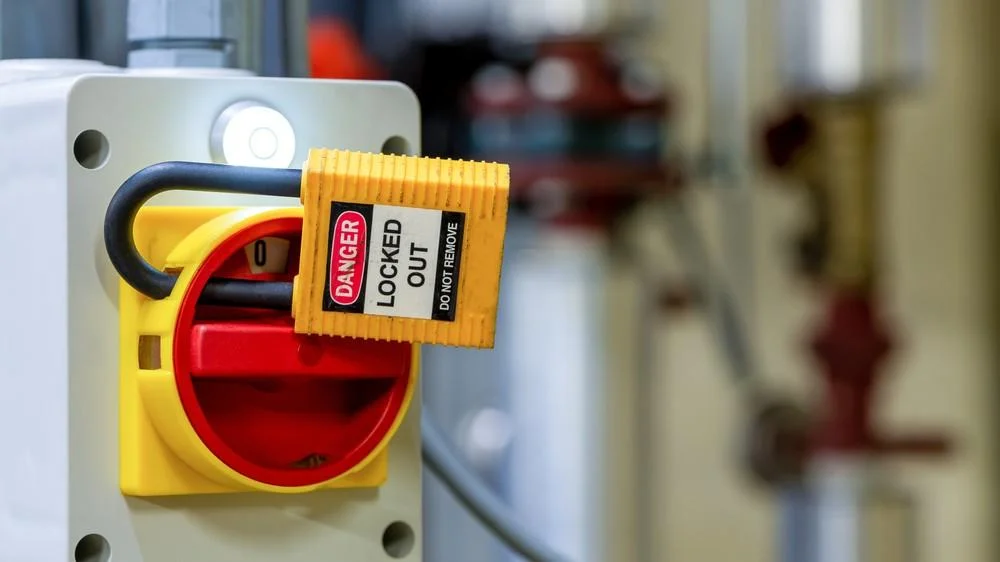
CNC Machine Safety Rules
Safe operating procedures can help minimize the risk of injury while running CNC equipment. Use the bulleted list below as a basic checklist, but consult your company’s CNC machine safety guidelines, as they may be different.
- Pre-Operation Safety Checks: Before starting a CNC machine, inspect it for damage or wear. Tooling, fixturing, fluid lines, and guards should all be inspected. Ensure all machine guards are in place and verify that all safety devices work correctly.
- Proper Workholding: Secure the workpiece properly to prevent it from shifting during machining. Unwanted movement could lead to tool breakage or workpiece ejection.
- Tool Selection and Maintenance: Use the right CNC tool for the job, and regularly inspect and maintain tools to ensure they are sharp and free from damage. If you do not perform maintenance yourself, ensure all preventive maintenance is up-to-date.Safe Machine Operation: Never bypass safety interlocks or operate the machine with guards removed. Always stay alert and focused when the machine is running.
- Check Yourself: Do you have the correct PPE on? Is there anything you wear that can be snagged in a machine or guard? Is your hair tied back if it’s long?
Handling CNC Machine Failures
CNC machines are reliable, but unexpected failures can happen. Programming errors, improper tools, excessive vibration, or a lack of routine maintenance are a few causes. When it comes to CNC machine safety in the event of a failure, keep these tips in mind.
- Don’t Panic: Immediately stop the machine using the E-stop button.
- Assess the Situation: Determine the cause of the failure, such as an equipment jam, and whether it presents an immediate danger.
- Report and Repair: Report the failure to the appropriate personnel, who must follow lockout/tagout procedures before attempting any repairs.
Safety Training Programs and Safety Culture
Training is essential for creating and maintaining a safe working environment. Any employee running a CNC machine needs operator training for the specific equipment and information about the company’s emergency response plan. Regular safety audits can identify potential hazards and ensure compliance with CNC machine safety protocols.
Continuous improvement, the process of making incremental changes over time, can help you build a safety culture characterized by proactive efforts to identify and mitigate risks. A safety management system can also help you implement policies and procedures that everyone needs to follow.
“We find people struggling to implement their policies and procedures. What is needed is a safety management system, which is a proactive process that results in an established safety culture.” – Jim Testo of EHS Risk Management in Rust, Paint, and Why You Need a Safety Culture.
Additional CNC Machine Safety Precautions
CNC machine safety also includes safety signage, machine maintenance, electrical safety, and environmental considerations.
Safety Signage
There are several different types of safety signs used with CNC machines.
- Danger signs are used in areas with immediate hazards that could cause serious injury or death if precautions aren’t taken.
- Machine warning signs may include warnings to wear protective gear or to remain cautious while equipment is in use.
- Moving machinery signs remind workers about specific risks, such as to fingers and hands, that are posed by moving parts.
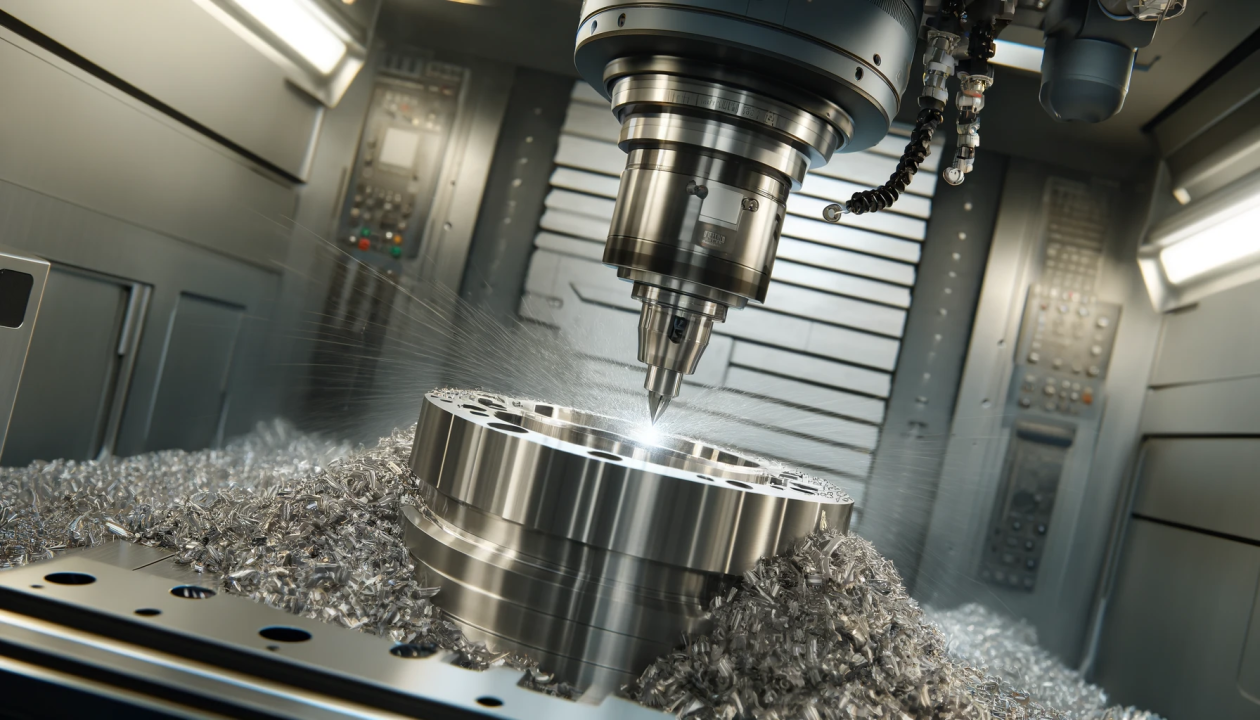
CNC Machine Maintenance
CNC machinery that is well-maintained is less likely to fail and cause injuries. Maintenance is often needed daily, periodically, and annually. This is based on machine utilization and the manufacturer’s specifications for the CNC machine you are using.
It’s always a good idea to check your machine’s operating manual, but here are a few tips for starting a preventive maintenance program for your CNC machines:
- Daily tasks include checking lubrication levels, emptying chip hoppers, checking all safety mechanisms, ensuring equipment is not broken, and wiping down surfaces to prevent the build-up of metal shavings.
- Periodic tasks range from cleaning the coolant tank of debris to removing chucks and jaws for cleaning. Coolant or lubricant fluid may need to be cleaned or replaced. Typically, these tasks are performed every six months or 1,000 hours.
- Annual tasks include running software simulations to check tool alignment and indentation. Software updates may also be included.
Electrical Safety
Improper grounding, faulty wiring, and power surges can cause electrical shocks, burns, fires, or fatal electrocutions. To mitigate these risks, manufacturers and machine shops need to perform periodic inspections and retain the services of a trained electrician. Always follow lockout/tagout procedures before inspecting and repairing equipment.
Environmental Considerations
CNC machine safety can raise environmental considerations that go beyond the use of the equipment. For example:
- Proper ventilation can reduce employee exposure to fumes, dust, and coolant mist.
- Adequate lighting promotes safe machine operation and can reduce the risk of mistakes.
- Housekeeping is essential because debris or obstructions around a CNC machine can pose a tripping or slip-and-fall hazard.
In addition, safety data sheets (SDS) or technical data (TDS) sheets should always be checked for proper procedures when disposing of or cleaning up chemicals such as machine coolants and lubricants.
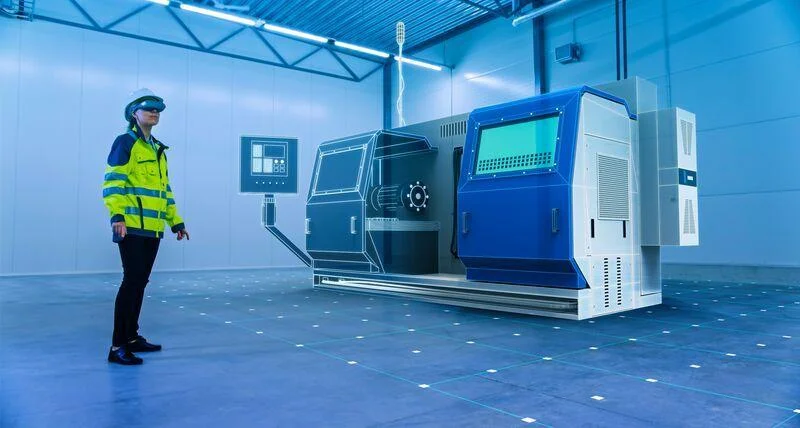
Trends in CNC Machine Safety
Advancements in technology, safety standards, and industry best practices are improving the safety of CNC operators and machinists.
- Enhanced guarding systems, such as automated doors and interlocked barriers, can prevent access to dangerous areas while a CNC machine is operating.
- Programmable logic controllers (PLCs) can be integrated into CNC machines to monitor and control safety functions. They can also quickly shut down the equipment.
- Safety sensors and laser scanners can detect the presence of a CNC operator near a hazardous area and either slow down or stop the machine.
- Artificial intelligence (AI) and the Internet of Things (IoT) can monitor CNC machine conditions in real time and recommend predictive maintenance to help prevent safety issues.
- Virtual reality (VR) and augmented reality (AR) simulations let workers go hands-on with safety procedures.
- ISO 12100 outlines requirements for the design of safety systems in machinery. Although it does not contain CNC safety standards per se, ISO 12100 contains general principles for risk reduction.
Choose Fictiv for CNC Machining Services
CNC machining can speed up production, improve accuracy, and reduce manufacturing costs. CNC machines can also reduce operator fatigue and the risk of injury and error thanks to automation. There are risks, however, and using PPE alone is not enough. Machine guards, E-stops, and LOTO procedures are all part of the solution.
Fictiv provides CNC machining services and works with a carefully vetted network of CNC machine shops to ensure we can provide you with the parts you need, made to your specifications, and at speeds as fast as one day.
Whether it’s for prototyping or production, Fictiv is your source for CNC machining services. To get started, create a free Fictiv account and upload your CAD file.