Time to read: 5 min
If you’ve ever seen a CNC machine operate, you know it’s loud, hot, and fast — I remember the first time I saw one in action and felt the vibrations through the floor next to the machine. Achieving accurate and high-quality results without overheating or damaging the equipment requires advanced machinery and proper cooling methods. The selection, monitoring, and maintenance of CNC machining coolant are crucial for maintaining temperature control, chip evacuation, lubrication, and extending tool life.
Read on to learn more about the different types of CNC machining coolants, their specific uses, and why they’re necessary to ensure precision in the machining process.
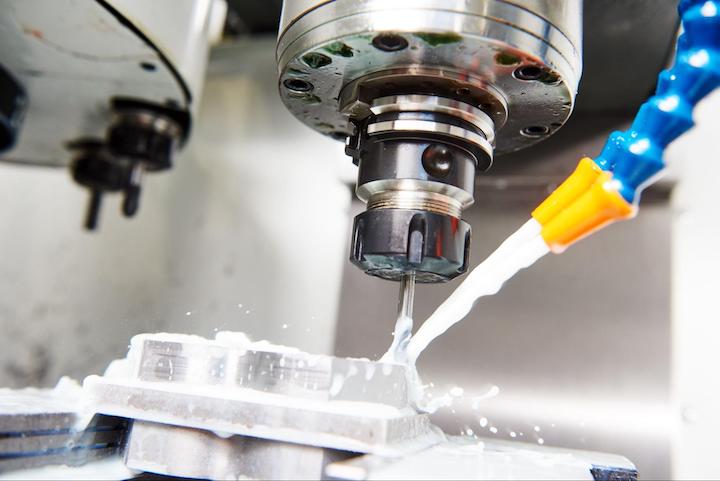
What is a Coolant?
Coolant is fluid used to dissipate heat from equipment, machinery, or systems. Coolant can be utilized to protect a system from overheating or to remove undesirable heat from a system. Coolant is typically pumped through a series of tubes, plates, and fins within a heat exchanger, where it passes next to another fluid that has absorbed heat from the system that needs to be cooled.
Coolant is used in a variety of applications, including:
- Automotive
- Industrial machinery and equipment
- HVAC systems
- Aerospace
- Metalworking
The Importance of CNC Machining Coolant
CNC machining coolant serves the same purpose as coolant in other applications: to remove heat from a system. When a cutting tool contacts a workpiece, it generates heat due to friction between the workpiece and tooling. Coolant is required to maintain proper operating temperatures and prevent overheating that leads to reduced performance, increased tool wear, and equipment failure.
Increased tooling temperature can result in one or more of the following:
- Thermal expansion of the part to be machined, which makes it difficult to maintain precision and accuracy due to the changing dimensions (especially with metallic parts)
- Accelerated tool wear, because tools wears faster at higher temperatures
- Workpiece distortion occurs if high temperatures are sustained over time, which creates quality issues for the finished part
CNC machining coolant mitigates these risks by efficiently dissipating heat to reduce tool wear, and improve overall machining precision and accuracy.
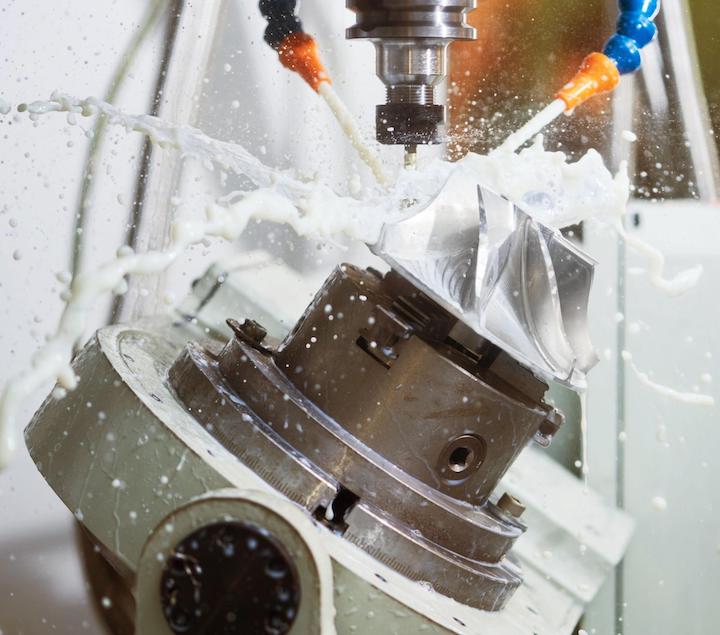
What Happens if You Don’t Use Coolant When CNC Machining?
There are several negative consequences that can occur when machining without coolant, which impact both the machining process and the quality of the finished parts.
- Overheating: Overheating leads to thermal expansion in the workpiece and the cutting tool, which can cause dimensional inaccuracies, part warpage, and even damage to the workpiece.
- Tool Wear: High temperatures and friction from the cutting action can accelerate tool wear, so proper cooling and lubrication extends the cutting tool’s lifespan. Also, increased tool wear leads to frequent tool changes, additional downtime, increased costs, and decreased productivity.
- Chip Clogging: Machining chips can accumulate around the work area and create a messy and unsafe working environment. Coolant lubricates the cutting zone and facilitates efficient chip removal. Without coolant, chips remain in the work area, which causes chip recutting and chip clogging — and results in reduced productivity, excess material removal, undesirable surface finish, or issues with features like internal threads.
- Smearing: Friction between the tool and the workpiece in the absence of coolant can cause smearing, which causes built-up edge formation, and results in rough surfaces, burrs, and other irregularities.
- Poor Surface Finish: CNC machining without coolant can cause thermal damage to the workpiece, leaving undesirable marks and discoloration.
CNC machining without coolant compromises the precision, quality, and efficiency of the process. It increases the likelihood of dimensional inaccuracies and workpiece and tool damage, while reducing tool life, and creating a poor surface finish. Coolant is vital for maintaining the temperature control, lubrication, speed, efficiency, and chip evacuation necessary for optimal cutting conditions — and getting consistent and high-quality results.
Types of CNC Machining Coolants
There are many types of CNC machining coolants, each with advantages tailored for specific applications. CNC machining coolants are often referred to as cutting fluids that serve as both coolants and lubricants during the machining process. There are two types of cutting fluids: water-based (aka water-dilutable) and non-water-based (aka neat) coolants.
There are several types of water-dilutable cutting fluids: soluble, synthetic, and semi-synthetic. Here’s a list of the most commonly used types and the benefits of each:
Coolant Type | Composition1 | Most Common Applications | Common Industries |
Soluble (Water-Based) | Oil-in-water emulsions are a combination of a water-based fluid that is either oil or water-based (mineral bases), surface-active additives such as rust inhibitors, antifoaming agents, pH stabilizers, and emulsifiers, lubricating agents, corrosion inhabitants, and detergents or dispersants. | Multi-functional and stable with excellent cooling and lubricity. Good for light to heavy-duty cutting and grinding of metals; provide a good surface finish. | Multi-purpose, used for less precise applications like hardware parts and tighter tolerance applications like bikes, automotive, construction, aerospace, etc. |
Synthetic (Water-Based) | Do not contain petroleum-based oils (which are organic); instead, they are a combination of rust inhibitors and synthetic lubricants, which are water-soluble. They typically come as concentrates you mix with water to create a usable coolant. | Since they are tailored specifically for the application, they offer superior cooling and lubricating properties compared to water-based coolants. Synthetic coolants are preferred for high-speed cutting, hard material CNC machining, or when trying to hit tight tolerances. | The demand for synthetic coolants is higher in applications like aerospace machining, where precision and surface finish are critical. |
Semi-Synthetic (Water-Based) | A combination of an engineered, synthetic base fluid (polyglycol, polyalphaolefin), mineral oil, surface-active additives such as rust inhibitors, antifoaming agents, pH stabilizers and emulsifiers, lubricating agents, and detergents or dispersants. | Provide a good balance between cost-effectiveness and performance; good for CNC milling, turning, and drilling; | Metal fabrication, automotive, aerospace, and medical device manufacturing. |
Straight (Straight Oils) or Neat Coolant | Provide the best lubricity, but the lowest cooling capacity; some sort of organic lubricants like vegetable oil, fat, and ester; biodegradable; can be added to petroleum or mineral oils to increase lubricity; sometimes contain chlorine, phosphorus, and sulfur. | Heavy-duty machining, high-speed machining, hard metal machining, thread cutting, thread tapping, screw machining, and gear cutting. | Automotive, heavy machinery, metal fabrication, tool and die manufacturing, and precision engineering. |
1Always consult your product’s manufacturing technical data sheet or manufacturer for specific formulation as it may vary by product
Fictiv – Your CNC Machining Partner
If you’re looking for a CNC machining service that can provide the support, quality and speed you need, then CNC machining with Fictiv is the right choice. We have some of the most skilled CNC machinists in the world who are well versed in the right coolant to use for any application. They can deliver the precision parts you need in as little as 2 days!
Create an account and upload your design today!