Time to read: 9 min
If you’ve ever seen a CNC machine operate, you know it’s loud, hot, and fast. Managing heat and friction in CNC machining is critical to maintaining precision and tool longevity. Excessive heat, primarily generated by friction between the cutting tool and the workpiece, can lead to premature tool wear, poor surface finishes, and even material deformation.
That’s where cutting fluids come in. These fluids, also known as metal cutting fluids or machining coolants, serve multiple functions: they dissipate heat, reduce friction, and help remove chips from the cutting area. Choosing the right fluid can significantly enhance machining efficiency, extend tool life, and improve the overall quality of finished parts.
Read on to learn more about the role of cutting fluids in CNC machining, their types, and how to choose the right one for optimal performance. This article also includes best practices for maintenance and proper disposal to ensure efficiency and compliance.
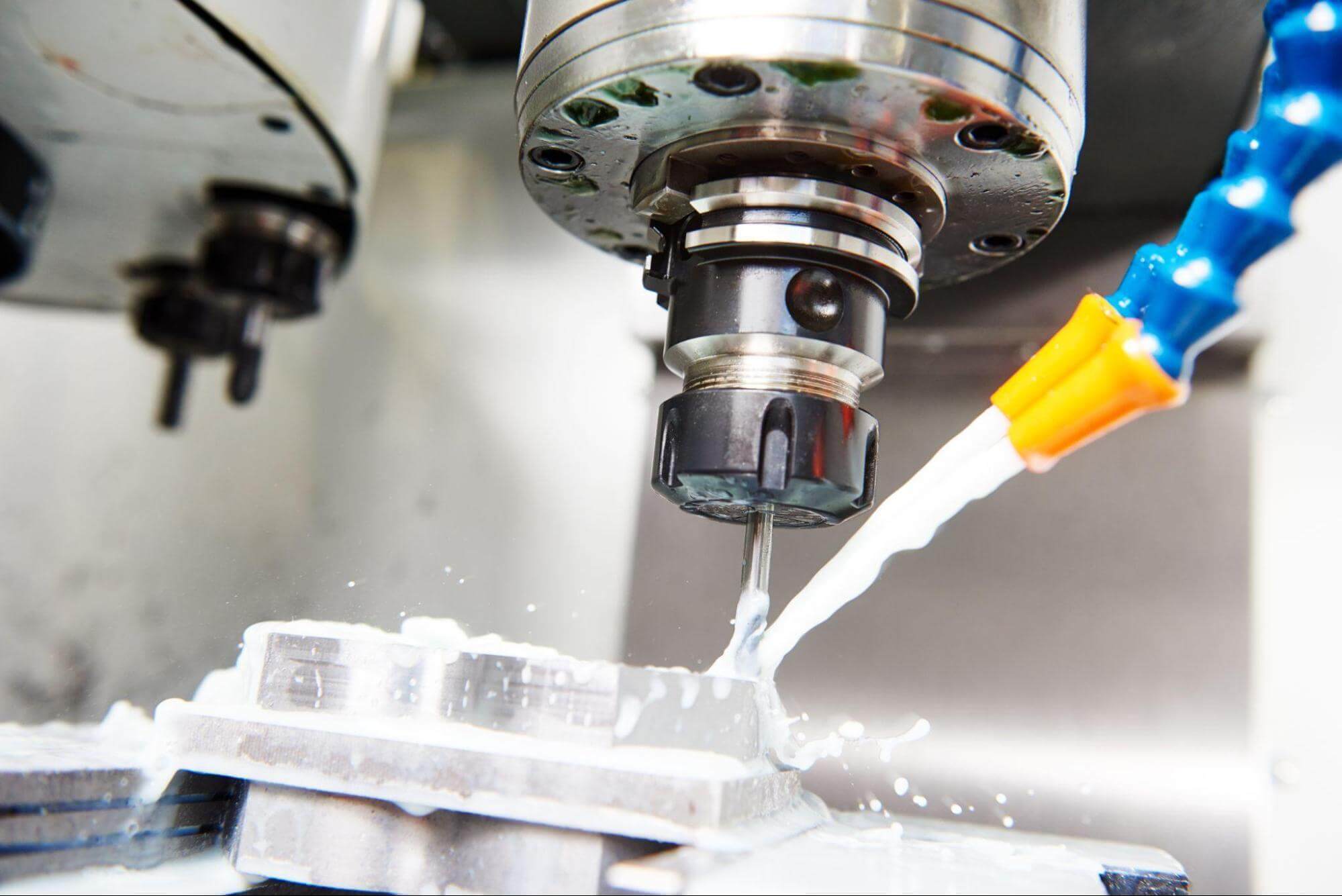
Functions of Cutting Fluids in CNC Machining
Cutting fluids play a critical role in making sure machining operations run smoothly. In CNC machining, cutting fluids are essential because they offer several key benefits:
- Cooling
- Lubrication
- Chip evacuation
- Corrosion prevention
- Productivity enhancement
Cooling
In CNC machining, high cutting speeds generate significant heat, which can lead to rapid tool wear and potential workpiece deformation. Effective cooling is essential for maintaining machining precision and extending tool life. Water-soluble cutting fluids (like emulsions, semi-synthetics, and synthetics) play a critical role in heat management by absorbing and dissipating excess heat, preventing both the cutting tool and workpiece from overheating. This ensures smoother operations, enhances tool longevity, and improves machining efficiency.
Lubrication
Lubrication helps reduce friction between the cutting tool and the workpiece, minimizing wear and tear on the tool and making the whole operation more efficient. Cutting fluids, like straight oils (mineral-based, synthetic, or vegetable-based oils), provide much-needed lubrication to the cutting tool, reducing friction between the tool and the workpiece. This is key for reducing wear on the tool and making the whole machining operation more efficient.
Good lubrication helps reduce tool chatter and vibration, improves the surface finish, and stops material from sticking (built-up edge formation).
Chip Evacuation
Cutting fluids help clear away metal chips from the cutting area. This prevents the tool from recutting the chips, which can damage both the tool and the workpiece. High-pressure coolant systems with synthetic fluids are good at flushing away chips, ensuring cleaner cuts and better accuracy.
Cutting fluids also improve the quality of the machined workpiece by constantly clearing away metal bits and cuttings from the tool and cutting area. This cleaning action helps prevent defects and ensures a smoother finish.
Corrosion Prevention
Some cutting fluids have anti-corrosion additives that protect tools and workpieces from rust and oxidation. This is especially important when machining materials like aluminum and steel. Adding corrosion inhibitors to cutting fluids can reduce the risk of corrosion on machine parts and tools. These chemicals create a protective layer on the metal surface, stopping moisture and other corrosive agents from causing damage.
Productivity Enhancement
Cutting fluids are crucial in increasing productivity in machine shops by enabling higher machining speeds and improved surface finishes. By reducing tool wear and enhancing workpiece quality, they minimize downtime and optimize overall efficiency in production processes.
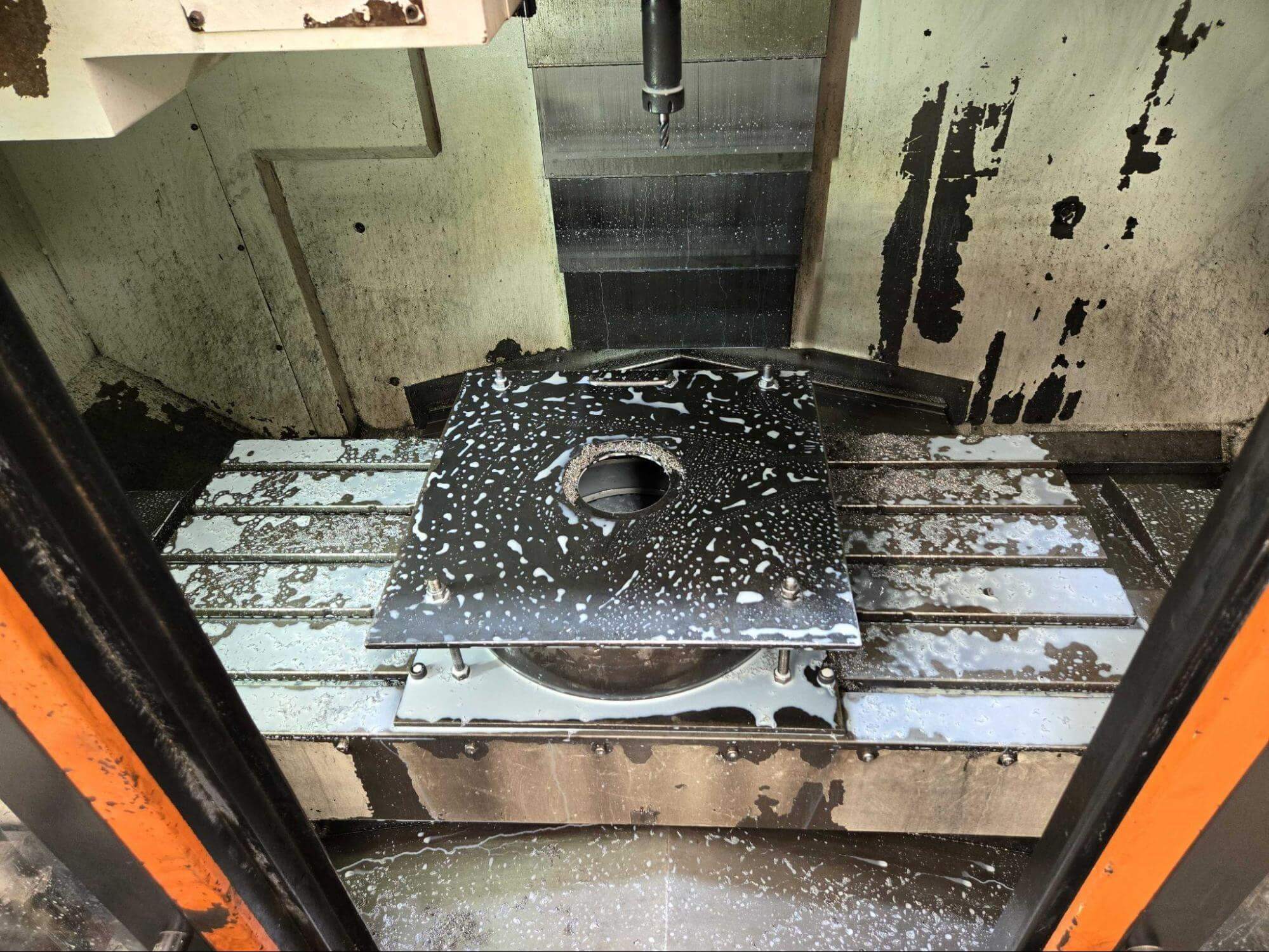
Types of CNC Cutting Fluids
Cutting fluids in CNC machining can be classified into three main types based on their composition and primary function:
- Straight oils: Pure oil-based fluids that provide excellent lubrication but minimal cooling.
- Water-miscible fluids: Fluids that mix with water to enhance cooling efficiency.
- Chemical cutting fluids: Engineered fluids with chemical additives to improve performance, often including synthetic and semi-synthetic formulations.
Within these types, cutting fluids are further divided into four main categories based on their formulation and application:
- Water-soluble cutting fluids
- Synthetic cutting fluids
- Semi-synthetic fluids
- Straight oils
Water-Soluble Cutting Fluids
Water-soluble cutting fluids, including emulsions (soluble oils), semi-synthetics, and synthetics, are widely used in CNC machining due to their ability to balance cooling and lubrication. These fluids, which account for approximately 80–90% of machining applications, are mixed with water to enhance heat dissipation and machining efficiency.
Emulsions combine oil and water, offering a good balance of cooling and lubrication. While they do not lubricate as effectively as straight oils, water-soluble fluids are well-suited for high-speed machining and materials such as aluminum and ferrous metals. However, regular monitoring is required to prevent bacterial growth in the fluid and maintain performance.
Synthetic Cutting Fluids
Synthetic fluids are completely chemical-based and contain no mineral oil, making them highly resistant to bacterial growth and degradation. They offer excellent cooling with minimal residue, making them ideal for high-speed CNC machining, grinding, and aerospace applications. However, they provide less lubrication than straight oils, which may be a consideration for specific machining processes.
Semi-Synthetic Fluids
Semi-synthetic fluids, a hybrid of synthetic and soluble oils, offer a balanced combination of lubrication, cooling, and cleanliness, making them ideal for general-purpose CNC machining. However, they require consistent monitoring of concentration levels to maintain optimal performance.
Straight Oils
Straight oils are non-water-miscible lubricants that provide excellent friction reduction and tool protection. They often contain additives like sulfur, chlorine, or phosphorus to enhance cutting performance. Straight oils are generally classified into two types: standard straight oils and highly compounded straight oils.
Standard straight oils are 100% petroleum-based and offer exceptional lubricity, creating a cushioning effect between the workpiece and the cutting tool. These oils are particularly effective in low-speed, high-precision machining operations that require superior surface finishes. Despite their higher cost, they are preferred for demanding applications like crush grinding and deep-hole drilling due to their superior lubrication properties.
Highly compounded straight oils are specially formulated to enhance lubrication and are commonly used for machining hard-to-cut metals such as titanium, stainless steel, and superalloys. While straight oils excel in lubrication, they have poor cooling properties and may produce smoke or fumes, which should be considered in machining environments.
Coolant Type | Composition | Most Common Applications | Common Industries |
Soluble (Water-Based) | Oil-in-water emulsions are a combination of a fluid that is either oil or water-based (mineral bases), surface-active additives such as rust inhibitors, antifoaming agents, pH stabilizers, and emulsifiers, lubricating agents, corrosion inhabitants, and detergents or dispersants. | Multi-functional and stable with excellent cooling and lubricity. Good for light to heavy-duty cutting and grinding of metals andprovide a good surface finish. | Multi-purpose, used for less precise applications like hardware parts and tighter tolerance applications such as bikes, automotive, construction, aerospace, etc. |
Synthetic (Water-Based) | Do not contain petroleum-based oils (which are organic); instead, they are a combination of rust inhibitors and synthetic lubricants, which are water-soluble. They typically come as concentrates and need to be mixed with water to create a usable coolant. | Since they are tailored specifically for the application, they offer superior cooling and lubricating properties compared to water-based coolants. Synthetic coolants are preferred for high-speed cutting, hard material CNC machining, or when trying to hit tight tolerances. | The demand for synthetic coolants is higher in applications like aerospace machining, where precision and surface finish are critical. |
Semi-Synthetic (Water-Based) | A combination of an engineered, synthetic-based fluid (polyglycol, polyalphaolefin), mineral oil, and surface-active additives such as rust inhibitors, antifoaming agents, pH stabilizers and emulsifiers, lubricating agents, and detergents or dispersants. | Provide a good balance between cost-effectiveness and performance; good for CNC milling, turning, and drilling; | Metal fabrication, automotive, aerospace, and medical device manufacturing. |
Straight (Straight Oils) or Neat Coolant | Provide the best lubricity, but the lowest cooling capacity; can contain organic lubricants like vegetable oil, fat, and ester; biodegradable; can be added to petroleum or mineral oils to increase lubricity; sometimes contain chlorine, phosphorus, and sulfur. | Heavy-duty machining, high-speed machining, hard metal machining, thread cutting, thread tapping, screw machining, and gear cutting. | Automotive, heavy machinery, metal fabrication, tool and die manufacturing, and precision engineering. |
How to Choose the Right Cutting Fluid for Your Application
Selecting the appropriate cutting fluid requires careful evaluation of these important factors to optimize machining efficiency while minimizing expenses and health risks:
- Cost & long-term value
- Material compatibility
- Fluid longevity & maintenance
- Environmental regulations
Cost & Long-Term Value
Straight oils generally have a higher up-front cost than water-miscible fluids due to their composition and high-quality base oils. However, their superior lubrication and extended tool life can result in lower overall expenses. A cost-benefit analysis (CBA) is essential to determine whether the higher initial investment translates into long-term savings through reduced wear, improved machining quality, and extended fluid life.
Material Compatibility
Different materials require specific fluid properties. High-speed machining benefits from synthetics due to their superior cooling, while tough materials like steel and titanium require straight oils for enhanced lubrication and protection.
Fluid Longevity & Maintenance
Beyond the purchase price, consider the fluid’s lifespan and upkeep. Premium fluids may have a higher initial cost but often last longer, reducing the need for frequent replacements. While straight oils require less maintenance than water-miscible fluids, they still need filtering and antioxidants to prevent oxidation and contamination, which adds to operational costs.
Environmental Regulations
Proper disposal of cutting fluids is crucial, as some may be classified as hazardous waste. Compliance with local disposal regulations impacts both environmental responsibility and operational costs.
By considering all these factors, manufacturers can improve their machining processes while keeping costs and health risks as low as possible. Factors appropriate to metal cutting fluid are shown in Table 1:
Main Goal | Recommended Cutting Fluid |
High-speed machining | Synthetic or semi-synthetic |
Heavy-duty cutting (steel, titanium) | Straight oils or emulsions |
Precision machining | Water-soluble fluids |
Chip evacuation | High-pressure synthetic fluids |
Environmental concerns | Vegetable-based oils |
Recommended Metal Cutting Fluid
Always check the tool manufacturer’s recommendations for the best cutting fluid to use.
Cutting Fluid Maintenance and Disposal
Proper cutting fluid maintenance extends tool life, prevents contamination, and reduces costs by ensuring optimal performance. Responsible disposal is equally important for environmental compliance, making it essential to follow best practices for fluid management and waste reduction.
Monitoring and Maintenance
Key practices for proper cutting fluid maintenance include:
- Monitoring concentration levels using refractometers or chemical titration for greater accuracy.
- Maintaining pH between 8.5 and 9.5 to prevent bacterial growth and maintain fluid stability.
- Removing tramp oil regularly to preserve fluid performance and reduce disposal costs.
- Installing filtration systems to help eliminate metal fines and contaminants, extending the fluid lifespan.
- Proper training to ensure operators can identify fluid degradation and perform routine maintenance effectively.
Proper Disposal
To minimize environmental impact and avoid legal penalties, consider these practices to stay in compliance with environmental regulations:
- Setting up recycling programs extends fluid life by filtering and reprocessing coolants, reducing waste and costs.
- Following hazardous waste guidelines requires testing before disposal to properly handle harmful chemicals.
- Using coolant management systems helps maintain fluid quality and minimize waste.
- Using biodegradable cutting fluids reduces environmental impact, and companies must follow disposal regulations to prevent fines and remediation costs.
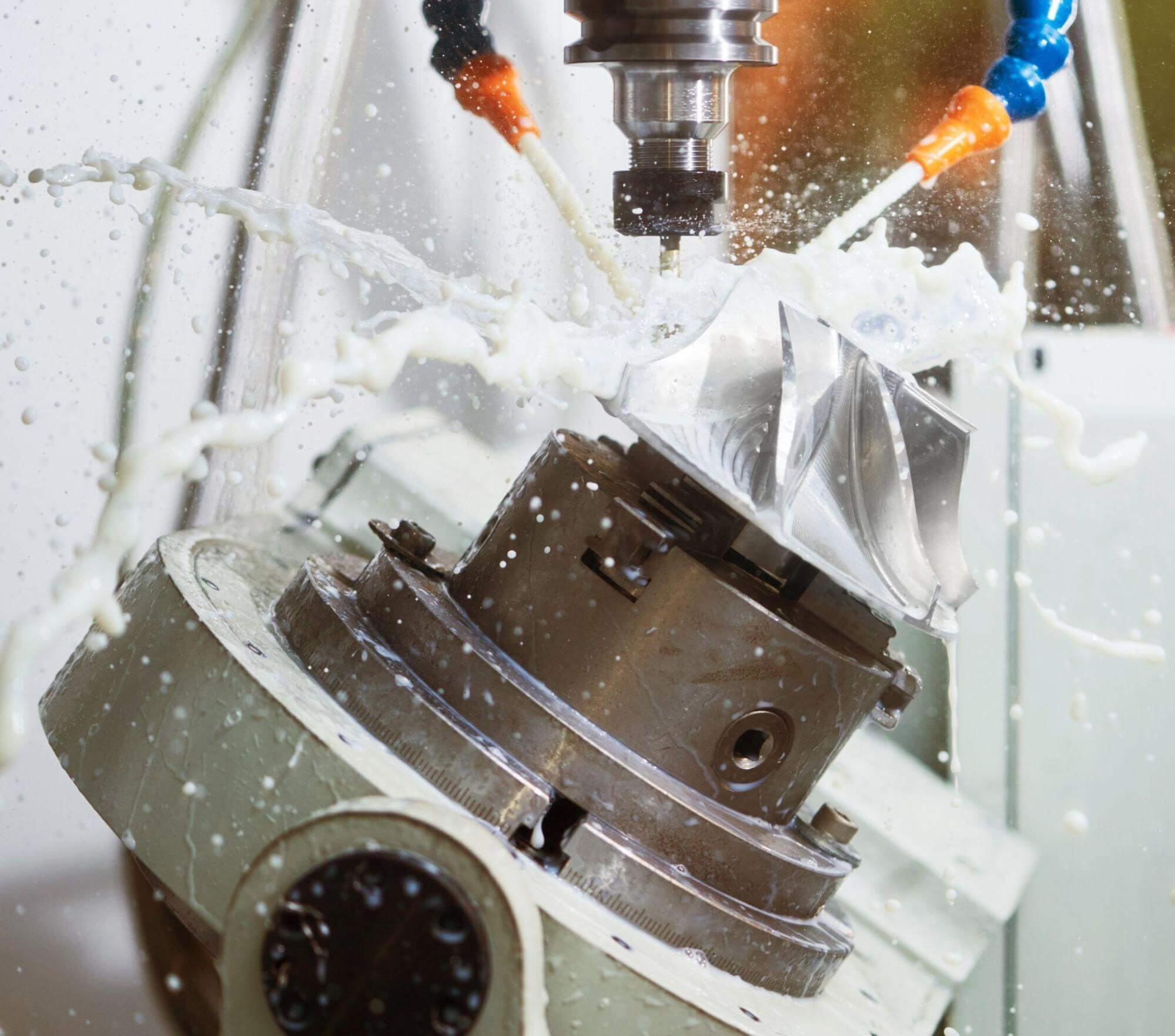
Future Trends in Cutting Fluids
As CNC machining continues to advance, there are innovations in metal cutting fluids that aim to boost efficiency and help reduce environmental impact:
- Eco-Friendly Fluids: Plant-based oils and biodegradable coolants are becoming more popular. Vegetable oils, especially coconut oil, actually work better than conventional options in terms of tool life and chip thickness when used with Minimum Quantity Lubrication (MQL).
- AI-Driven Fluid Monitoring: Sensors that can detect contamination in real time use artificial intelligence to analyze and track fluid conditions. This optimizes performance, catches anomalies, and improves efficiency.
- Nano-Enhanced Lubricants: Cutting-edge fluids with superior cooling and wear resistance use nanoparticles to boost thermal conductivity and lubrication properties.
- Reduction of Cutting Fluid Usage: There’s a growing trend toward minimizing or eliminating the use of cutting fluids in machining processes. Strategies like MQL and dry machining are being explored to reduce fluid consumption while still maintaining performance.
- Innovative Fluid Types: The development of new fluid formulations is expected to continue, with a focus on biodegradable and environmentally friendly options. Synthetic fluids that offer superior cooling and lubrication properties are getting more attention, as they can reduce waste and health risks associated with traditional cutting fluids.
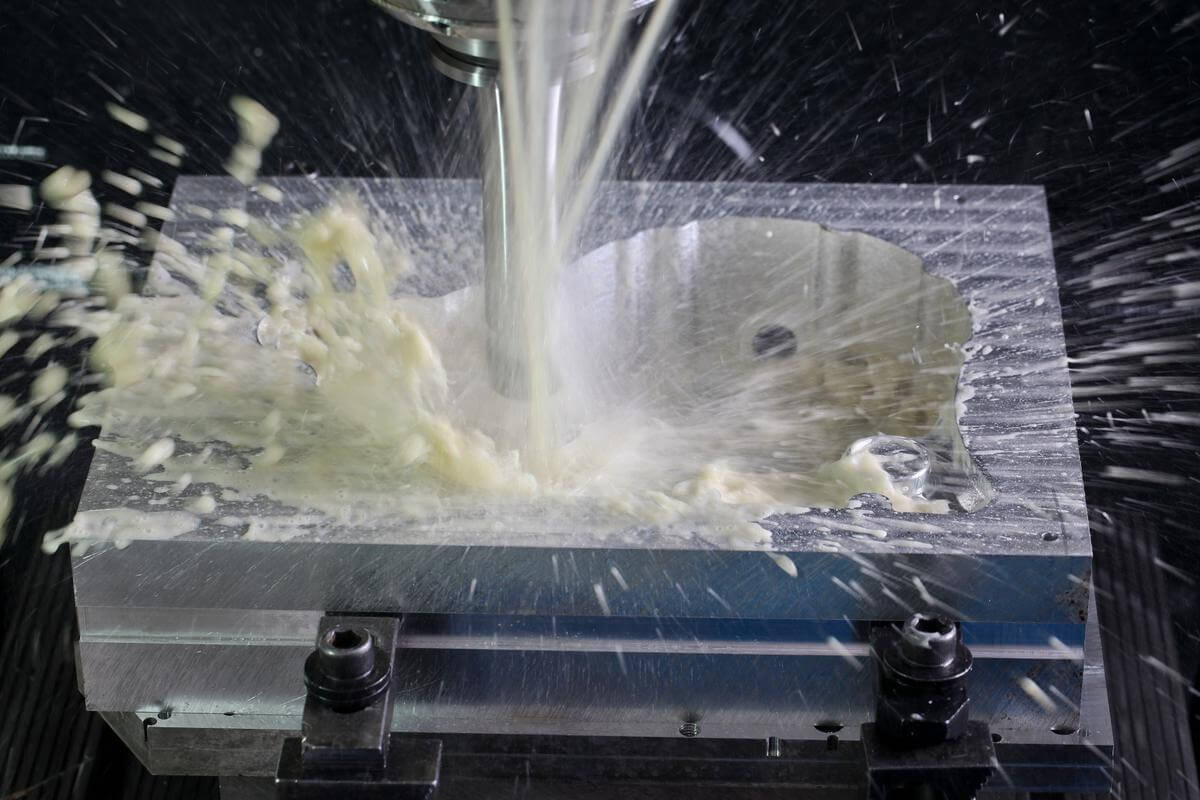
Choosing and Managing CNC Cutting Fluids for Optimal Performance
CNC cutting fluids are essential in machining, playing a key role in heat dissipation, lubrication, chip evacuation, and workpiece quality enhancement. They also extend tool life, improve productivity, and help manage environmental considerations. Understanding the different types of cutting fluids, along with best practices for maintenance and disposal, enables manufacturers to optimize machining performance while minimizing costs and health risks.
As the industry advances, innovations such as eco-friendly formulations, AI-driven fluid monitoring, and nano-enhanced lubricants are emerging, further improving efficiency and sustainability. These developments are shaping a more environmentally responsible future for CNC machining.
Properly selecting and managing the right cutting fluid is crucial for achieving optimal machining results. Whether you’re an industry veteran or new to the field, staying informed about the latest technologies and best practices ensures efficient, cost-effective, and sustainable operations.
Fictiv – Your Expert CNC Machining Partner
If you’re looking for a CNC machining partner that can provide the support, quality, and speed you need, then CNC machining with Fictiv is the right choice. We have some of the most skilled CNC machinists in the world who are well-versed in choosing the proper coolant and machining setup for any application. They can leverage their expertise and start your project quickly with precision parts delivered in as little as 2 days!
Create an account and upload your design today for high-precision CNC parts!