Time to read: 9 min
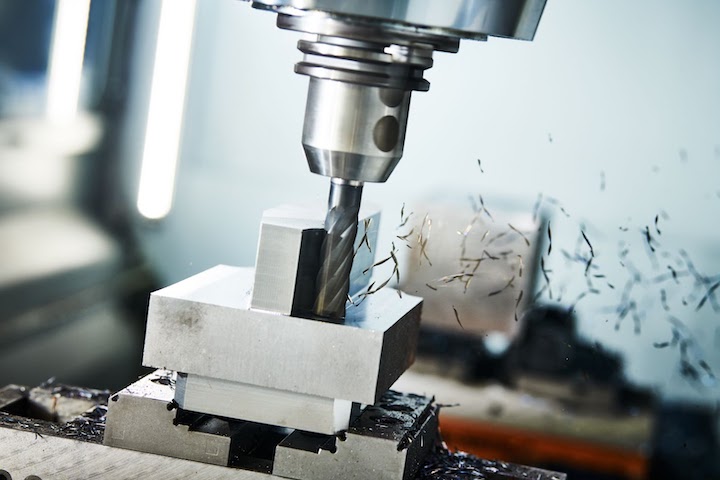
CNC milling is one of the most common machining processes used to manufacture complex parts. When milling a part, one of the first questions a machinist must ask is whether to use conventional or climb milling on that part. While climb and conventional milling are relatively similar, the key difference is in the rotation of the cutting tool in relation to the movement of the workpiece. While this may seem like a small change, it can have a big impact on the part being machined. Common wisdom is that CNC’ers are always Climb Milling and manual machinists are always Conventional Milling. It’s probably true that manual machinists should stick to Conventional Milling as their preferred way of milling because the backlash of their machines makes it dangerous to Climb Mill. However, with advancements in technology and the use of lead screws, Climb Milling has become a viable option for CNC milling machines as well. Read on to learn more about each type of CNC milling, as well as the use cases for each, including the production of a rough surface.
The Basics of Milling
CNC milling is a subtractive machining process whereby a rotating cutting tool is used to remove material from a workpiece. Milling allows for complex geometries with high repeatability and is a crucial process for making many parts. With 3, 4, 5, and even 6-axis CNC mills, part geometries can have many different features and components while still being highly repeatable. Complexity is no problem with today’s sophisticated CNC machinery.
To machine a component with a CNC mill, the workpiece must first be clamped down (aka fixtured) in the machine. Once fixtured, the cutting tool removes material from the workpiece with each pass. CNC milling machines either involve a moving tool impacting a stationary part or a stationary tool impacting a moving part. Regardless, the material removal is accomplished when the cutting tool rotates rapidly to remove chips of material and shape the workpiece into the desired part.
Variations in how the cutting tool moves over the workpiece results in different surface finishes, cutting styles, and machine requirements. Certain components benefit from specific CNC machines, for example Swiss machines are excellent at producing small parts with tight tolerances. Fictiv offers many different CNC options to produce even the most complex parts at ridiculous speeds.
Conventional Milling
Conventional CNC milling or conventional milling requires the cutting tool’s rotation to be opposite the direction of the feed, which is considered to be fighting the feed. This process is also called up milling because the cutting tool starts at the base of the cut and pulls up through the workpiece. Most often, manual CNC milling is accomplished via conventional milling.
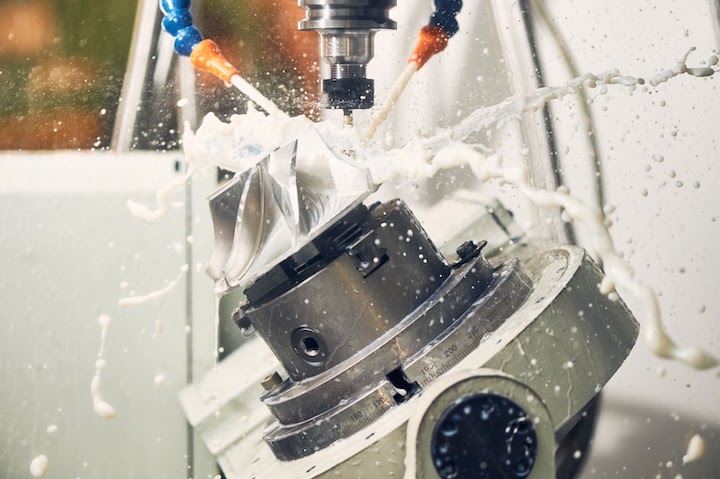
One of the reasons this type of machining is the traditional approach is because of its many advantages. Some of the advantages of conventional CNC milling are:
- More control of the cutting tool, higher accuracy
- The tool is less likely to pull into the workpiece
- Less powerful machines are needed
- Better for larger cuts
- Reduces chattering and tearing in some instances (at the micro surface level)
With less accurate and less powerful CNC machines, conventional milling still results in high-quality parts. Due to the direction of the rotation of the cutting edge, the tool is less likely to pull into the workpiece which keeps the accuracy high and prevents errors.
While conventional milling has many benefits, it has its share of downsides as well. Some of the cons to using conventional milling include:
- Rougher surface finish
- Higher likelihood of recuts due to chip ejection direction (which reduces surface quality and tool life)
- More heat is generated (which reduces tool life and distorts the workpiece)
- Higher forces are transferred to the workpiece
The rotation of the cutting tool relative to the workpiece causes chips to be ejected in the same direction as the tool is moving. Many of these chips will get recut as the tool passes over them again, which reduces the surface quality of the finished part and wears tools out faster.
Conventional, or up milling also requires higher clamping forces. The cutting tool naturally wants to pull the workpiece up and away from the machine table as chips are removed. For machines prone to backlash or for materials that commonly tear or chatter, the pros of conventional milling often outweigh the cons, including the need for an extra spring cut. Manual machines will almost always use conventional milling processes.
Climb Milling
What is climb milling, aka down milling? Climb milling is very similar to conventional milling with the only real difference being the rotation of the cutting edge relative to the workpiece. While the cutting tool rotates “up” in conventional milling, in climb milling the cutting edge rotates “down” resulting in the cutting tool climbing or pulling into the workpiece. Essentially, in climb milling, the direction of the cut and the direction of the cutting tool’s rotation are the same, and they work in conjunction to suck the mill up and over, away from the work piece, resulting in a better finish and requiring less energy. On some machines, like a gantry router, the spindle moves, so the labels would reverse. G-Wizard now reminds you with a little hint which one you should use.
No new equipment is needed to do climb milling. The machinist simply has to change the feed direction for the workpiece. Although the change may seem small, climb milling can have a big impact on the quality of the finished part.
Common benefits of climb milling include:
- Better surface finish since the chip reduces in width throughout the cut
- Reduced likelihood of recuts due to better chip ejection
- Lower cutting forces keep the workpiece in place, and reduce the clamping requirements
- Heat is pulled out away from the part due to the chip formation
- Less power required to cut
- Increased tool life because of reduced chip recutting
The tool enters the workpiece much more aggressively since it comes in from the top with climb cutting milling. As the cutting tool rotates, it takes a large chunk of material with it. The chip width decreases as the tool rotates until the cutting tool exits at a gentle angle. This gentle exit angle results in superior surface quality over conventional milling techniques.
The change in rotation has other benefits, too. Since chips are ejected away from the cutting tool’s path of motion, the chance of recutting is greatly reduced. The cutting angle also helps push the workpiece into the table, which reduces the clamping requirements.
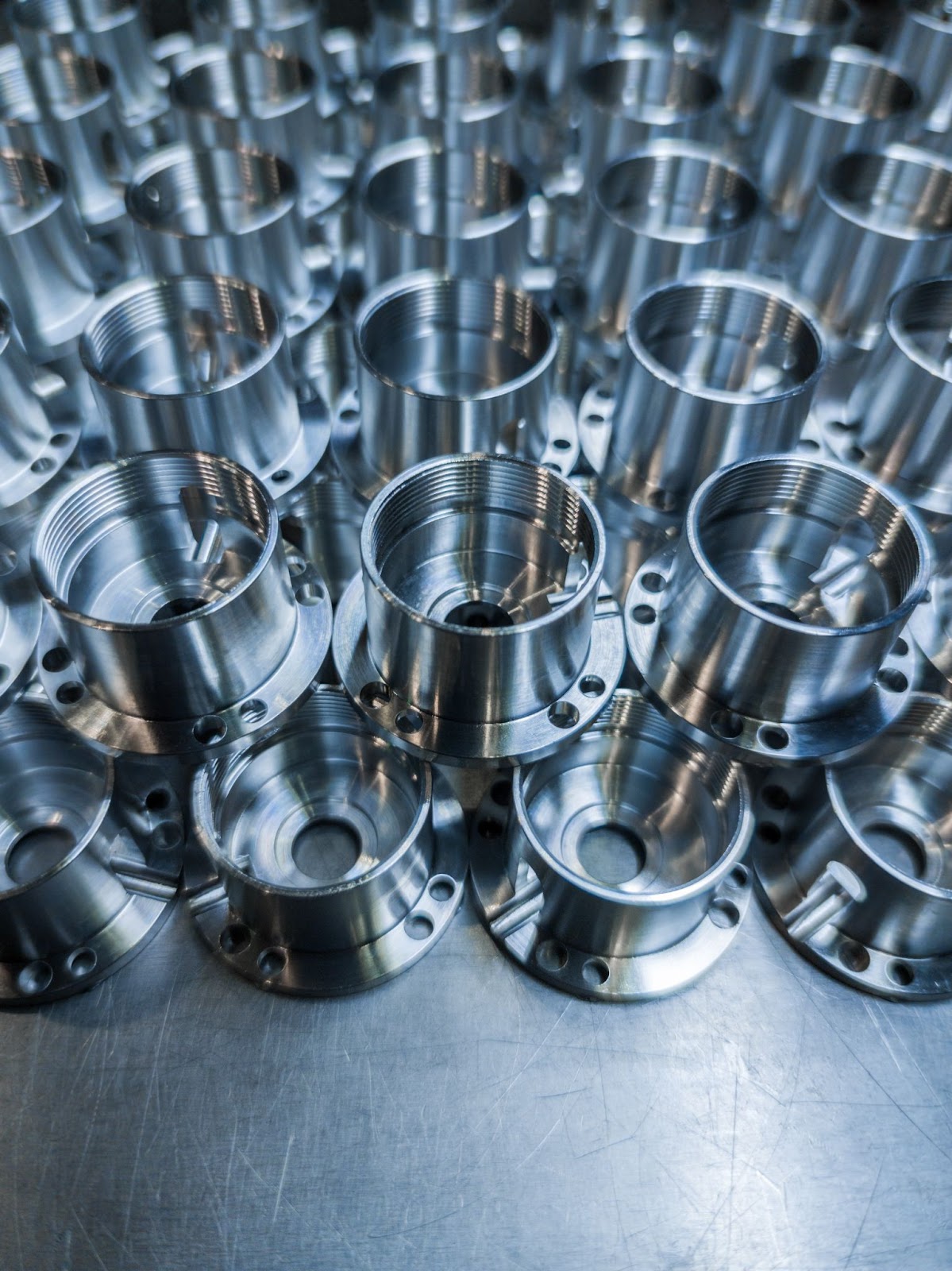
Climb milling is not without its downsides, which include:
- Machines with minimal backlash are required for climb milling
- Backlash and high forces lead to vibration and chatter, which degrades the surface finish
- The cutter can suck the workpeice into the cut and break the cutter or cause chatter
- Less control of the cutting process since the cutting edge and workpiece are moving in the same direction
- The tool can be pulled into the workpiece
- Some materials are not suitable for climb milling
Pro-Tip: To reduce the likelihood of backlash, reduce the cutting force by reducing tooling size, cut depth, feed height, and spindle speed.
The aggressive entry angle of the cutting tool is great for material removal rates, but can also result in a great deal of backlash, or chatter. Conventional milling was often used to reduce the likelihood of backlash and chatter, but with many modern machines using backlash eliminators, backlash in climb milling less of a concern, but it can still greatly affect surface quality if not taken into account.
The same forces that help to reduce clamping requirements can have a negative impact as well. Because the tool is climbing, or pulling into the workpiece, it can be much easier for the tool to pull too far and remove too much material. Because the tool and the workpiece are moving in the same direction, the process is also harder to control, though with modern machine tools and CNC controls, many of these problematic aspects are compensated for.
Download our DFM for CNC machining checklist for tips that’ll help ensure your part is well-designed for machining the first time:
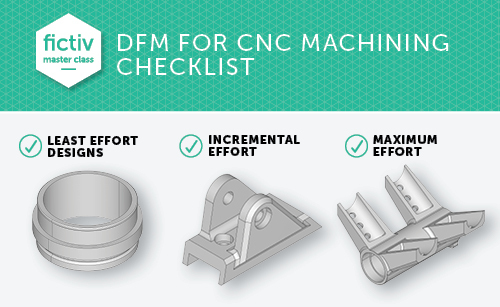
How accurate are milling machines?
Milling machines are highly accurate, capable of achieving precision within a few thousandths of an inch. However, the accuracy of a milling machine depends on various factors such as machine quality, operator skill, and tooling. Regular maintenance and calibration can also help ensure optimal accuracy.
Climb milling vs Conventional milling
Climb milling and conventional milling are two different techniques used in milling operations.
In climb milling, the cutter rotates against the direction of feed, which results in the tool “climbing” into the workpiece. This technique offers advantages such as reduced tool wear, smoother surface finish, and less chance of workpiece lifting. However, it requires careful consideration of factors like backlash and control.
Conventional milling, on the other hand, involves rotating the cutter in the same direction as the feed. This technique is more commonly used when working with older machines or materials that are prone to chipping
When to Use Conventional or Climb Milling
Conventional and climb milling are both great options for machining, but how do you know which process to use for your project? The material being machined and the desired surface quality are key factors for determining the optimal process.
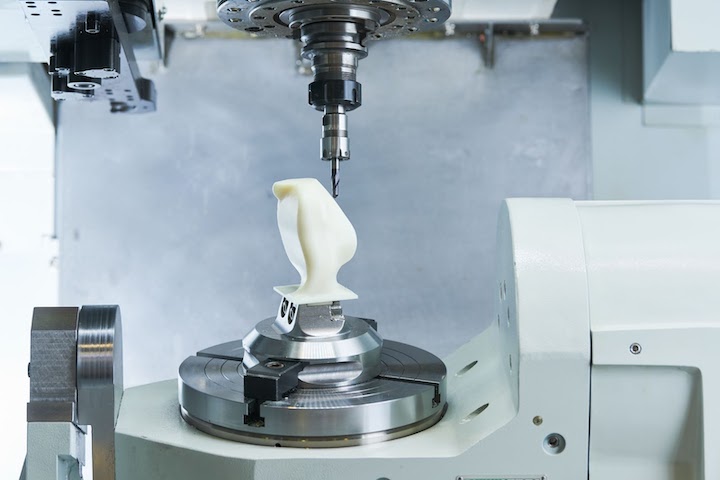
Soft materials like aluminum work well with climb milling. While most materials work well with conventional milling, here are some that do well with climb milling:
Hard materials like cast iron and hot rolled steel are typically better machined using conventional milling processes, while some softer variations of steel respond better to climb milling. Conventional milling should be used with materials that are prone to chatter or tearing. Climb milling is great for workpieces that have a tendency to lift since the forces push the workpiece into the table.
Pro-Tip: Climb milling is the better choice when cutting less than half the cutter tool’s diameter. For cutting more than 75% of the cutter tool’s diameter, use conventional milling due to the potential for negative rake.
Because climb milling can improve the surface finish of many parts, it is often used as a final pass. Conventional milling does the bulk of material removal with climb milling used at the end to get the final dimension with a superior surface quality. Aerospace parts, even for harder materials like titanium, often have a final climb milling process pass, which can be counterintuitive for a lot of machinists who were trained for most of their careers. The consensus over at Practical Machinist supports this approach as well, especially in thin wall work where the walls are weak and the tool diameter and stickout result in small enough deflection for your finish pass.
Conventional and Climb Milling: Two Tools in the Toolbox
Milling is one of the most common machining operations for a reason. The ability to shape workpieces into the desired form with high tolerances and great repeatability makes it an ideal process for many applications.
Knowing the differences between these two main types of milling, conventional cutting and climb milling, help you make the best selection when deciding how a part should be milled. The workpiece’s material properties and the desired surface finish of the part have a big impact on how well each process will work, but both are useful tools for machining many different kinds of parts. Tool deflection affecting cutting accuracy is a major difference between these two milling methods, as the conventional mill finish pass would make the workpiece more accurate with little tendency for deflection. The following illustration contains small arrows (often called vectors) showing the direction of tool deflection as the cutter moves along the toolpath:. The arrows show where the cutting force is attempting to deflect the cutter in a climb cut, so it is important to avoid too much depth of cut when climb milling to create less kind of deflection.
Sourcing Simplified – Start Your Next Project With Fictiv
For all your CNC machining (conventional, climb, or otherwise) and finishing needs, Fictiv has you covered. We’re experts at producing custom CNC machined tight tolerance parts, in a variety of materials, and we simplify custom part sourcing with intelligent, streamlined, automated workflows. Fictiv is your operating system for custom manufacturing that makes part procurement faster, easier, and more efficient.
Create an account and upload your part to get an online CNC quote, design for manufacturability feedback, and see what our intelligent platform can do for you.
Nick Ysidron Nick is a mechanical engineer working in the HVAC and IoT space. When he isn’t designing new tech to make our lives more connected and improving the air we breathe, he enjoys spending time with his wife Bridget and son James. He holds Bachelor’s degrees in Mechanical Engineering and Spanish from Louisiana State University. His hobbies include anything outdoors, 3D printing, playing with his son, and reading as often as he can.