Time to read: 5 min
Oftentimes engineers and product designers place much focus on selecting the appropriate grade of plastic when developing injection molding part designs. Equally important, though frequently an afterthought, are the metal materials used to manufacture the injection molding tool itself.
There are multiple commonly used grades of metals for tooling, and they’re typically used for the different stages of product development and validation. These different types of materials produce molds that provide assorted achievable tooling lead times and costs, different plastic part cycle times and associated unit costs, and varying levels of dimensional part precision and cosmetic quality of appearance.
Each type of mold material has its advantages and disadvantages, so it helps to create a “game plan” early in the design process for tooling and bringing your product to market. Here, we’ll discuss the prevalent mold materials, their advantages and disadvantages, and common use cases for each.
The three main categories of tooling materials are aluminum, soft and semi-hardened steel, and hardened steel.
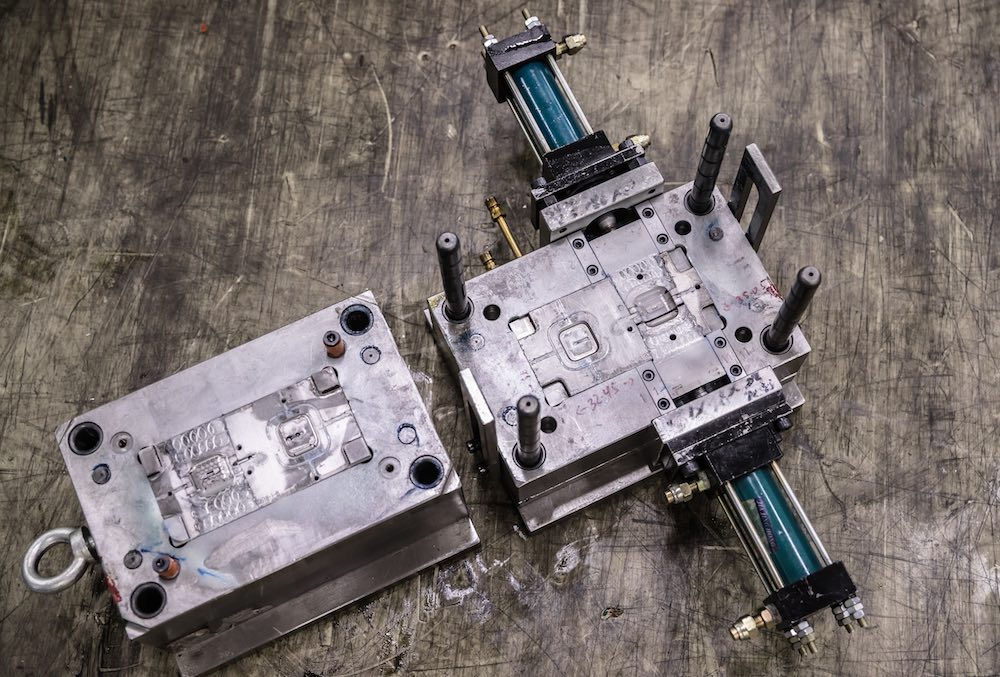
Aluminum
Aluminum is often used as an alternative to harder steel grades in situations that call for faster tool production time and prototype/low volume part production. Though aluminum is a common material in the industry, at present, it’s seldom used by Fictiv.
Advantages
- Aluminum can be machined more than twice as fast as steel, and It also doesn’t require post heat treatment. These two factors greatly shorten lead times and cost as compared to steel molds.
- Aluminum has excellent heat transfer properties, which enables heating and cooling of the tooling more easily. In some situations, the part cycle time can be faster than with steel tooling because of these properties.
Disadvantages
- Aluminum is softer than steel, so tooling typically wears out faster than harder grades of steel. Aluminum tooling delivers 10,000 shots or less depending on the part design and plastic grade of material.
- Since aluminum is softer, it also can’t handle high clamping pressures from larger injection molding presses. So, larger parts or parts with many side action features may not be suitable for aluminum tooling.
- Many prototype tooling factories neglect cooling lines design (or don’t include them at all), which can cause issues with dimensional precision and cosmetic part appearance.
- Not all grades of plastic are suited for aluminum tooling. Plastic materials that require high mold temperatures, such as PEI, PEEK or PSU, don’t process well, since it’s a challenge to maintain high heat in aluminum. Corrosive grades of plastic — such as PVC or POM — quickly eat away aluminum, and other grades with glass fiber additives can cause aluminum to wear away quickly.
- Aluminum does not take polishing as well as steel and is also more easily scratched, which causes issues for parts intended to be glossy or optically clear
Soft and Semi-Hardened Steels
P20
P20 is a commonly used, general purpose tool material. It strikes a strong balance between cost, available tooling lead time, part quality and dimensional part stability. Fictiv often uses another grade of steel, 718H, which is a bit harder than P20, but has the same general advantages and disadvantages.
Advantages
- P20 material is harder than aluminum and the tooling life is 5-10x higher — 50,000-100,000 shots — depending on the plastic material and part design.
- Heat treatment isn’t required, and P20 can be machined more quickly than other harder grades of steel.
- P20 is easily welded, giving more flexibility to non steel-safe engineering changes (ECO’s) and repairs.
Disadvantages
- The tooling available lead time may be 1-2 weeks, when an aluminum equivalent can be completed in days.
NAK80
NAK80 is semi-hardened tool steel, which Fictiv most often uses for highly polished clear or glossy plastic parts. It’s also used when the tooling life needs to be longer than P20 steel or when a part has several side actions.
It has similar advantages and disadvantages as P20, plus:
Advantages
- NAK80 takes polishing well, and produces optically clear and high glossy parts.
Disadvantages
- It costs more than P20 and typically takes 20-25% longer to produce the tooling than a P20 steel tool.
Hardened Steels
Hardened steels are most often used for high production quantity tooling. They’re typically multiple cavities with hot runner systems. The tool lives are longer but the manufacturing time and tooling costs are the highest of any material. High production quantity tooling is used to minimize part unit costs, which offsets the higher up front NRE (non-recurring engineering) costs.
H13
This grade of steel is the most commonly used for high production quantity tooling, and is good for thermal fatigue, and longer tooling life. It can better resist wear from some plastic materials, such as those with glass-filled additives, than the metal materials previously listed.
Advantages
- The available tooling life is 500,000 to 1 million shots.
- The dimensional tolerances can be held tighter than in aluminum or softer grades of steel.
Disadvantages
- Typically, H13 tools are heat treated after rough CNC machining, so the remaining manufacturing steps take longer to complete.
- The tooling is more costly than aluminum or softer grades of steel.
S136
S136 is a grade of stainless steel and used for more speciality cases in high production tooling.
Advantages
- The tooling life is typically 1 million or more shots.
- This grade of stainless steel can be polished to the highest level, and is best suited for applications when the highest optical clarity is required.
- S136 is able to resist the corrosive chemicals for PVC and POM material.
Disadvantages
- The tooling cost and lead times are the highest and longest of all mold materials.
The Typical Tooling Game Plan
Usually, Fictiv customers start with single cavity, P20 or NAK80 steel tools for their engineering validation testing (EVT) and design validation testing (DVT). These tools are finished and produce the first samples (T1) in 10-25 days.
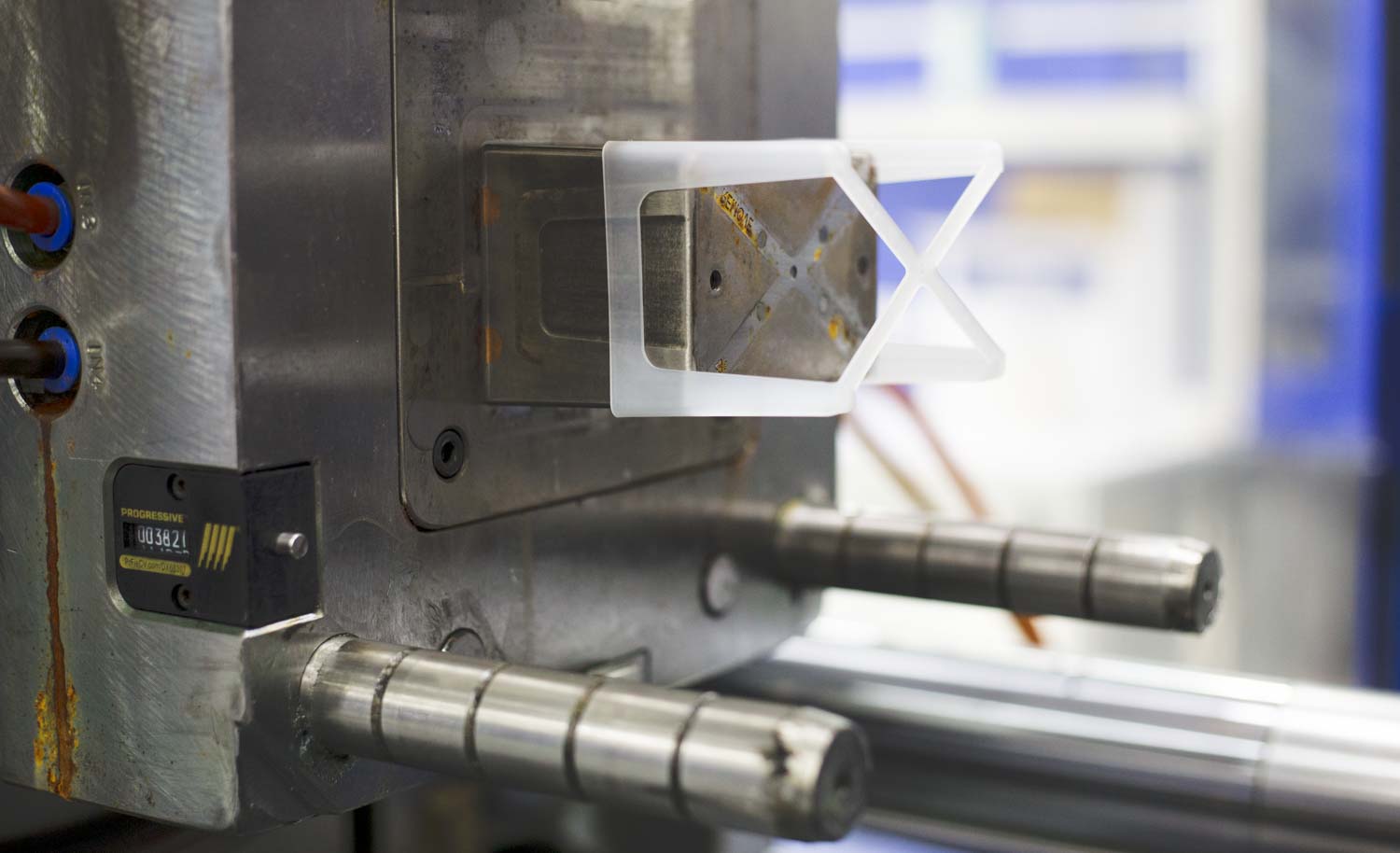
Such molds enable our customers to save on NRE costs at the beginning stages of a new product, and help bring an initial product to market faster. This can unlock investments and produce a bridge production quantity of parts to tide them over until production tooling comes online.
During these validation phases, more than one third of Fictiv customers’ tools require design changes through an ECO, which usually takes 3-5 days to modify the tooling. Single cavity, P20 or NAK80 tooling for ECO’s provides more freedom to make non steel-safe changes than aluminum at a lower cost than a hardened steel, multi-cavity production tool.
A word of advice: we find that if customers 3d print a prototype set prior to releasing tooling, the need for ECO’s is drastically reduced.
If the product demand is high and the designs are finalized and locked, customers typically move to hardened steel, production multi-cavity tooling. The NRE tooling costs are higher, but the minimized unit pricing and cycle times combined with maximized production capacity make it a logical next step in tooling.
Though the sequence described above is typical for Fictiv customers, there are factors which may prompt engineers and product designers to do it differently. Fictiv has a wealth of knowledge and expertise for injection molding, both in the US and overseas, and we’re happy to review and provide DFM feedback on your next tooling project.
Create an account today, and when you upload your CAD data and provide RFQ details, we’ll find the solutions that meet your needs.