Time to read: 7 min
We’re no longer in the Bronze Age, but some manufacturing techniques stand the test of time. Casting, a process where molten metal is poured into a mold, has been around for over 6,000 years and is still widely used and prominent in manufacturing to this day Advances in casting technology enable the casting of high-quality parts with tight tolerances, not unlike CNC machining, a newer manufacturing method that’s also commonly used.
But have you ever considered CNC machining a part that you usually cast? Or are you considering which method is best to manufacture your design? Let’s look at the two manufacturing processes, including their advantages and disadvantages.
What is Casting?
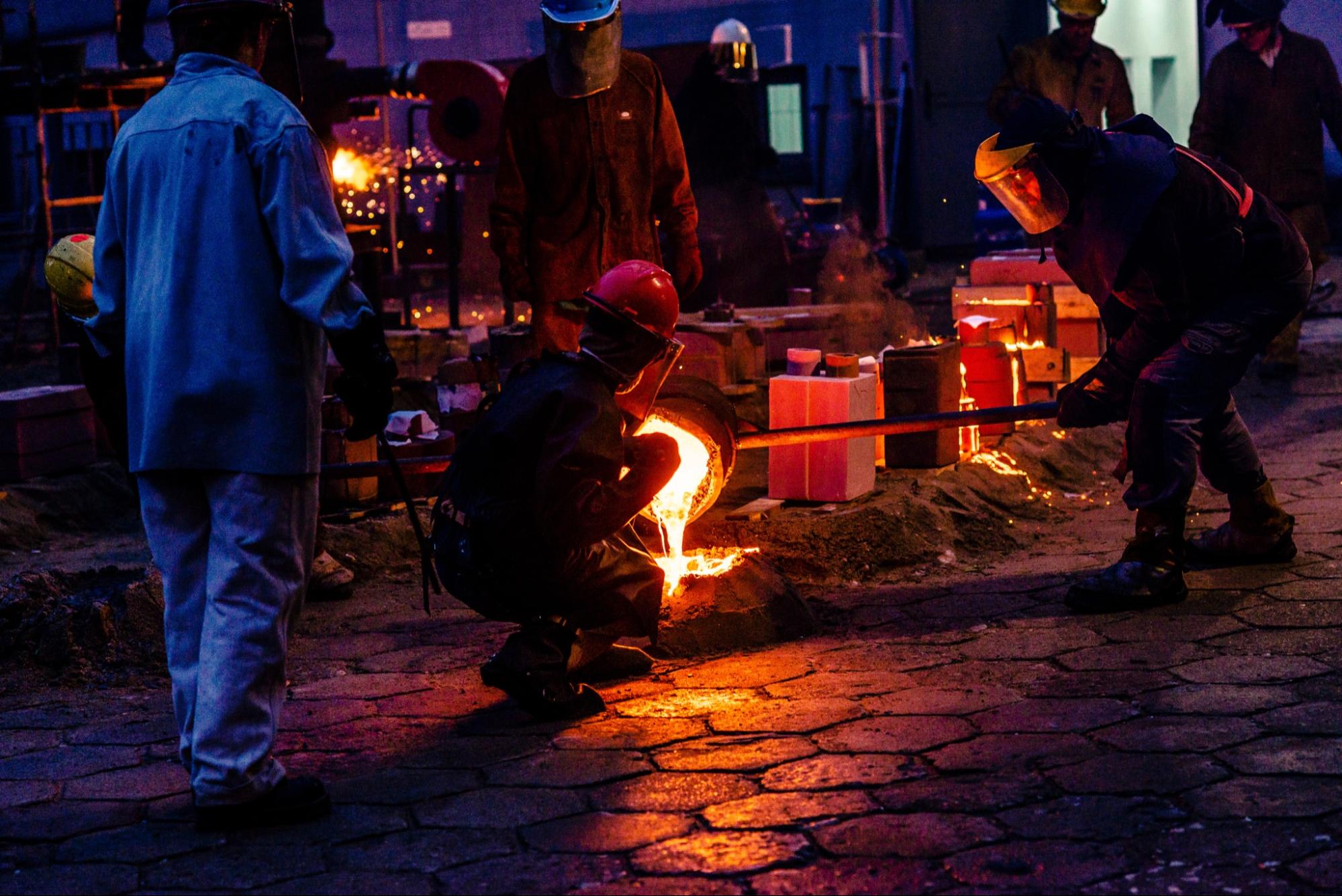
Casting is considered a formative manufacturing process that uses molds to make parts. Various casting methods and materials can be used in the process. This article focuses on metal casting, which includes techniques such as high- and low-pressure die casting, sand casting, gravity die casting, permanent mold casting, investment casting, and centrifugal casting. It will not cover the casting of other time-setting multi-component materials, such as epoxy.
Die Casting
In metal casting, molten metal is poured or injected into a pre-made mold, which may include cores or inserts if complex internal geometries and cavities are required. Die casting is a specific type of casting that uses pressure to force the molten metal into the mold. The pressures used in high-pressure die casting are significantly higher than those in low-pressure die casting.
After the part cools and solidifies, it’s cleaned and processed to achieve the desired surface finish. Secondary operations may include CNC machining to produce even tighter tolerances or removing other undesirable features from the die casting process, such as flash. Other methods of deflashing include grinding, cryogenic freezing, and tumbling.
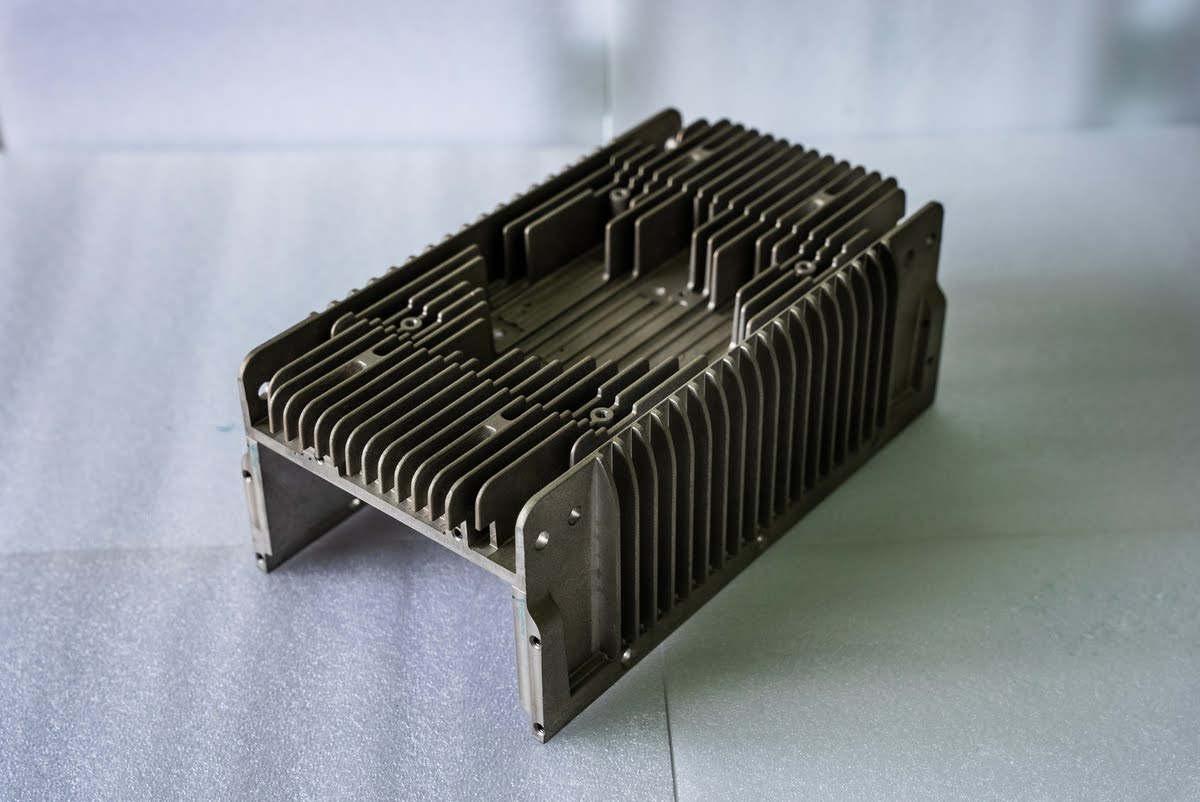
Train wheels, bus pedals, turbine blades, and engine blocks are common examples of die-cast parts. Cast parts are used in almost every industry, including automotive, aerospace, consumer products, and medical devices.
To learn more about part design for the die casting process, download our die casting design guide.
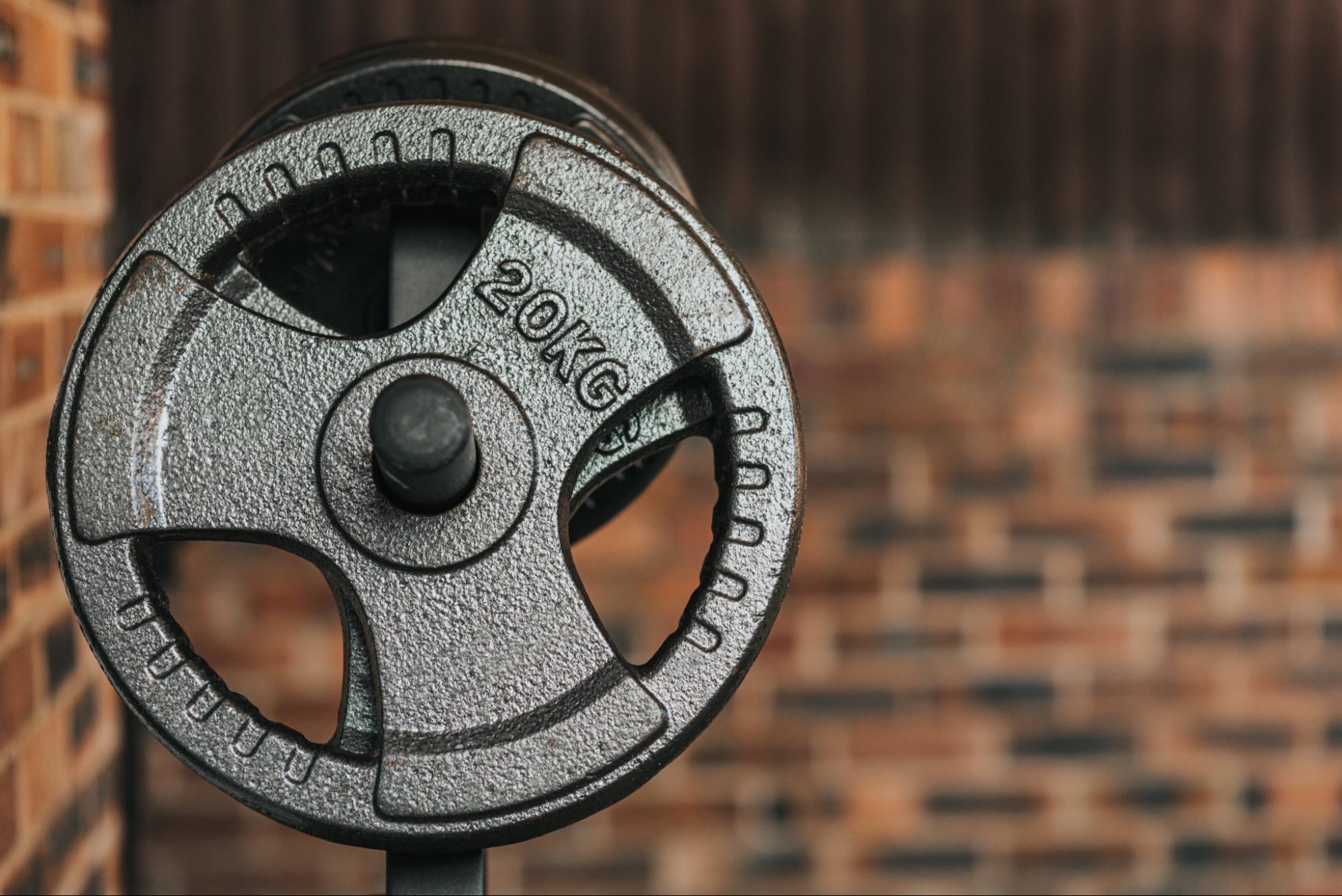
What is CNC machining?
CNC machining is a subtractive manufacturing method that utilizes a cutting tool to remove material to achieve the desired geometry. A computer program using G-code tells the machine where to move and how to cut.
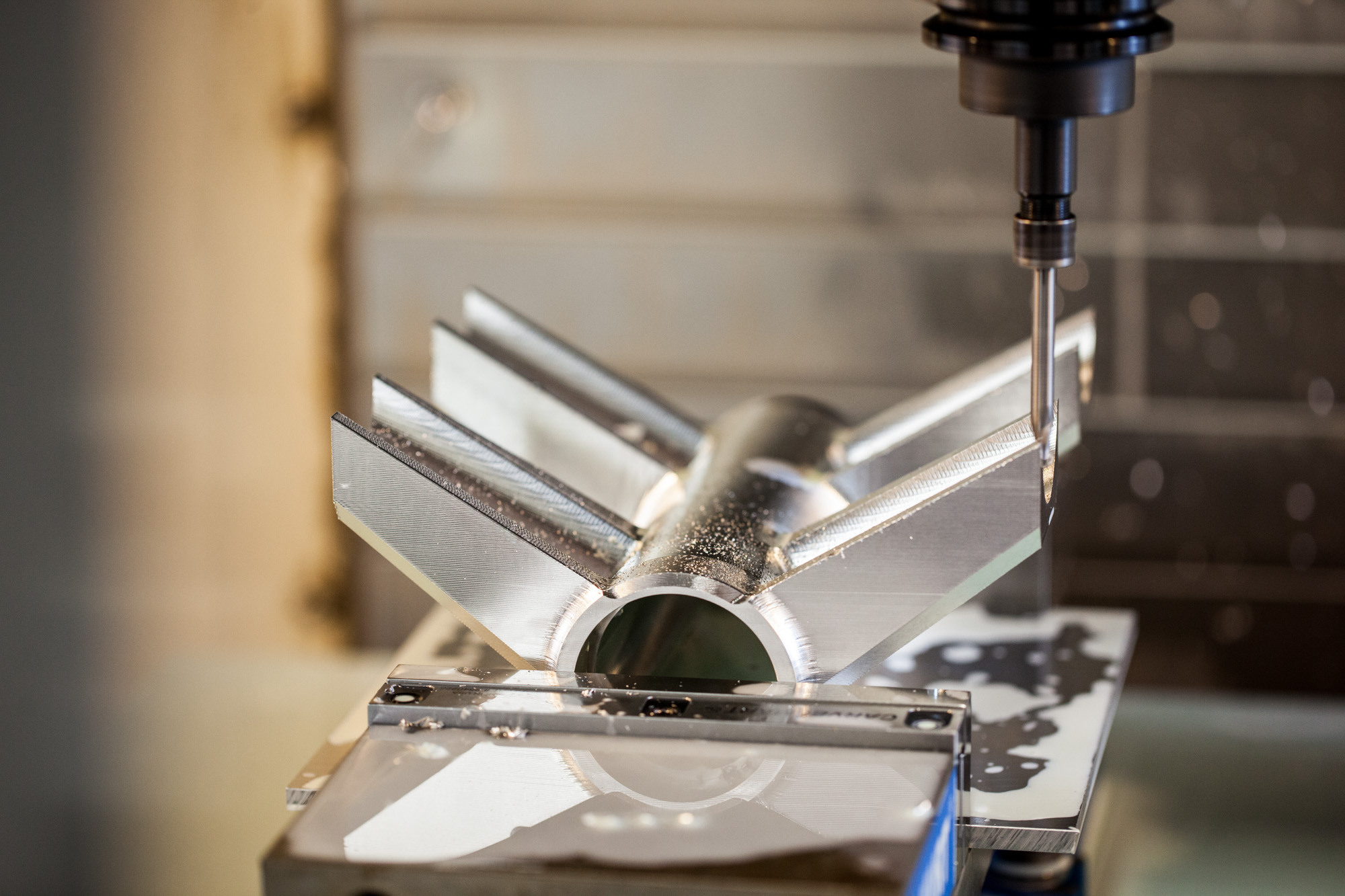
CNC-machined parts are everywhere. Metal laptop enclosures, small components inside cell phones, aerospace, and automotive parts, fixtures and jigs—even casting molds are manufactured using CNC machining.
Choosing Your Manufacturing Method
When designing a part, there are two common approaches to determine a manufacturing method to make the part (CNC vs casting):
- Design engineers often start with a manufacturing method in mind so that the design can be realistic, manufacturable, and have features that are well-suited to that process.
- On the other hand, a part’s function may require a specific size, shape, or geometry, which dictates the manufacturing process. CNC machining and die-casting are each best suited to particular geometries.
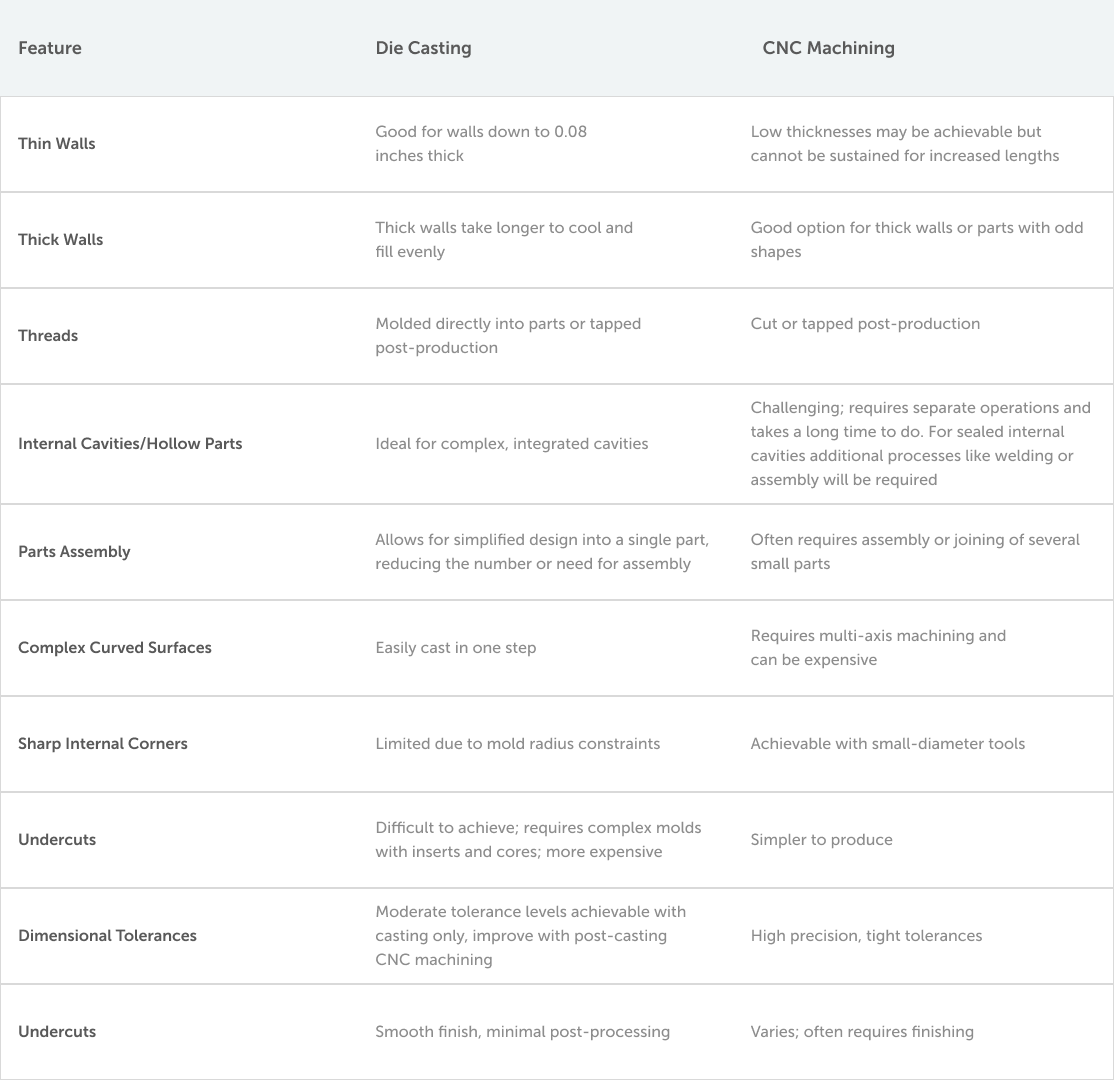
Casting or CNC Machining: Choosing Based On Part Geometry
Choosing the correct manufacturing technique starts with considering the part’s geometry. Certain designs require a large amount of material removal, which can be time-consuming and create excessive waste. Such designs are often good candidates for casting, such as hollow parts with thin walls and large cavities. Complex geometries, which take a long time to machine, are also good candidates for casting.
Internal cavities are often ideal for casting, as forming them with CNC machining can be incredibly complex. This is especially true for sealed internal cavities that require assembly or metal joining processes in addition to CNC machining. In contrast, casting lets you simplify the design of a part or assembly. Instead of machining many small parts and assembling them, you can cast the entire part and eliminate assembly steps.
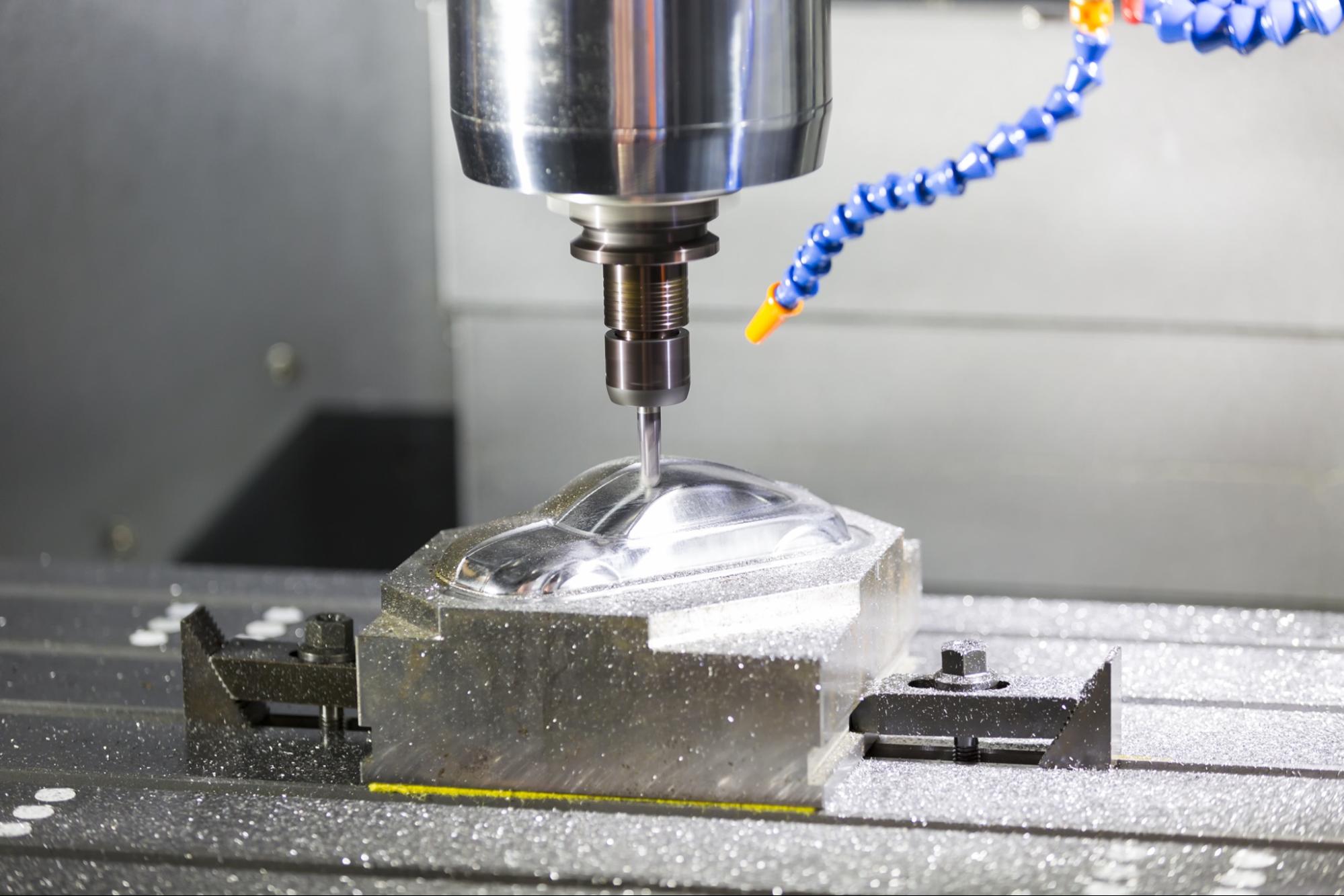
However, certain features are more difficult to achieve with casting. Undercuts or internal features are more complicated and require complex molds with cores and inserts. Sharp edges or corners are not ideal for casting, either, and cast parts require a draft angle on all features. Large or oddly shaped parts with thick walls are also better suited to CNC machining because those geometries are difficult to fill and cool evenly during casting.
Casting or CNC Machining: Choosing Based On Materials
Casting results in less wasted material than CNC machining. The casting process only uses the material needed for the final part, aside from a small amount of metal that flows through the gate, runner, and sprue. This excess material can be easily removed, remelted, and reused in another part.
However, casting offers far fewer material choices than CNC machining. Virtually all alloys can be CNC machined, while the list of alloys that can be cast is much shorter.
Casting or CNC Machining: Choosing Based On Production Speed
The casting process is pretty fast once the mold is ready, which is why it’s a good option for producing high volumes of parts. However, mold design and machining require some lead time, typically a few weeks. In addition, the mold must go through quality checks and maintenance, though some types of casting use expendable molds. A permanent mold is used with die casting, so the time and cost per part decrease as the volume of parts increases.
CNC machining provides a faster production speed, resulting in a quicker turnaround for a low volume of parts. There’s no need to wait for the mold to be manufactured since all you need is the CAD model, CAM program, and a CNC machine to start making parts.
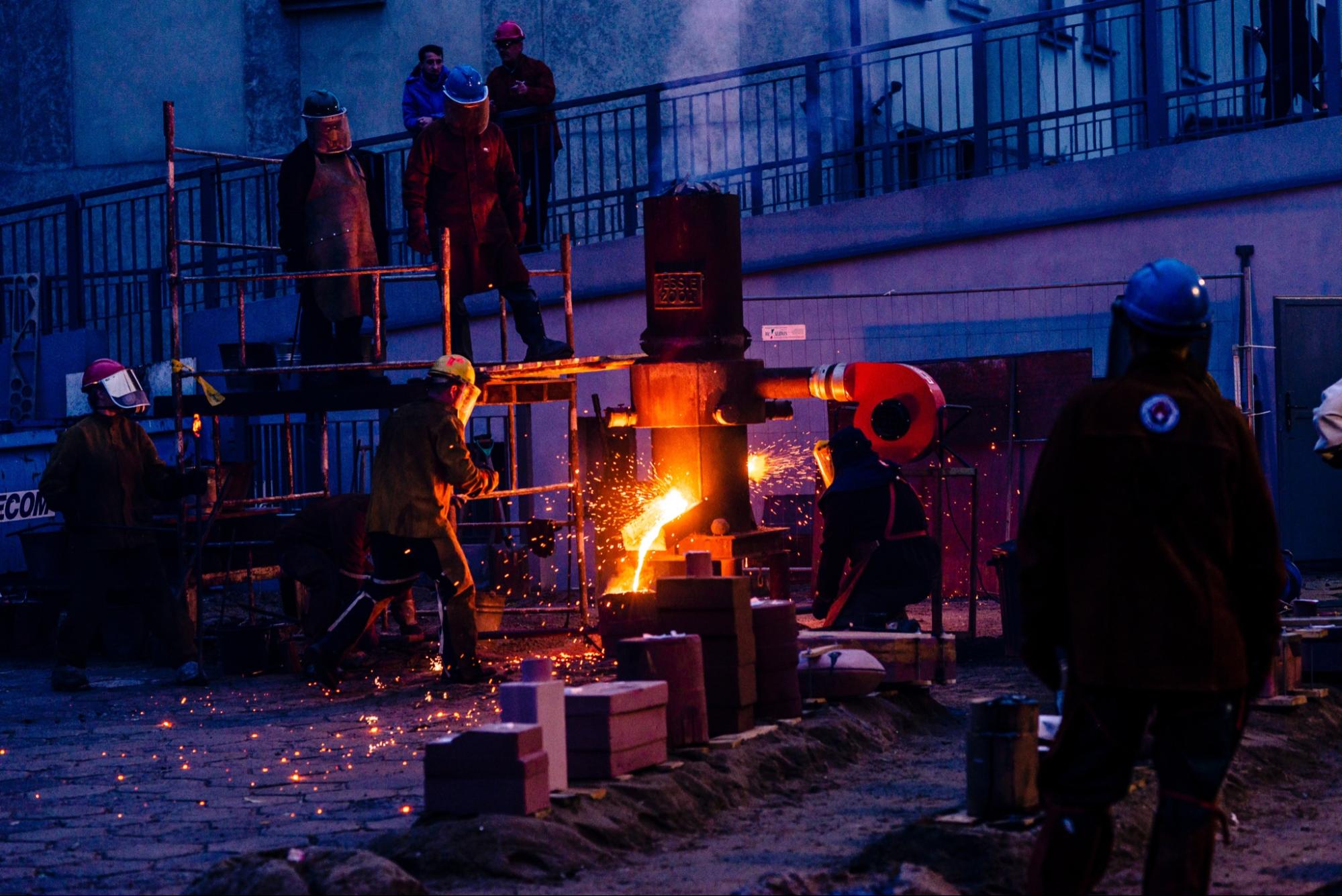
Casting or CNC Machining: Choosing Based On Repeatability and Precision
Repeatability is essential in manufacturing, and the casting process produces highly repeatable parts. Once the mold and process are dialed in, every part can be made precisely the same. With precision die casting, tolerances can be held to +/- 0.1 mm per 25 mm.
Those tolerances may vary depending on the material and your supplier. Aluminum has a higher melting point than zinc, for example, so it requires a higher injection pressure and a more aggressive process overall. That results in looser tolerances with casting versus machined aluminum. Tighter tolerances can be held when casting zinc.
CNC machining metal is also an extremely repeatable, accurate process that produces much tighter tolerances than casting. For standard metal machining, 0.025mm (0.001”) is a reasonable expectation. Fictiv precision machining can produce parts with tolerances as tight as +/- 0.0002”.
Casting or CNC Machining: Choosing for Prototyping
Although casting has its advantages, it is not ideal during the prototyping phase of the design process.You’ll have to pay for expensive molds to be re-created or adjusted every time you change your design, which increases lead times and cost. A prototype die cast can cost thousands, if not hundreds of thousands of dollars. And, while sand casting is typically cheaper, there isn’t much benefit to choosing die casting vs sand casting for prototype manufacturing.
CNC machining is the better choice for prototyping, due to the relative agility of changing a CNC machining process. When the design is still in flux, all you need to do is change the model and redo the CAM program, rather than remaking a mold or trying to modify an existing mold.
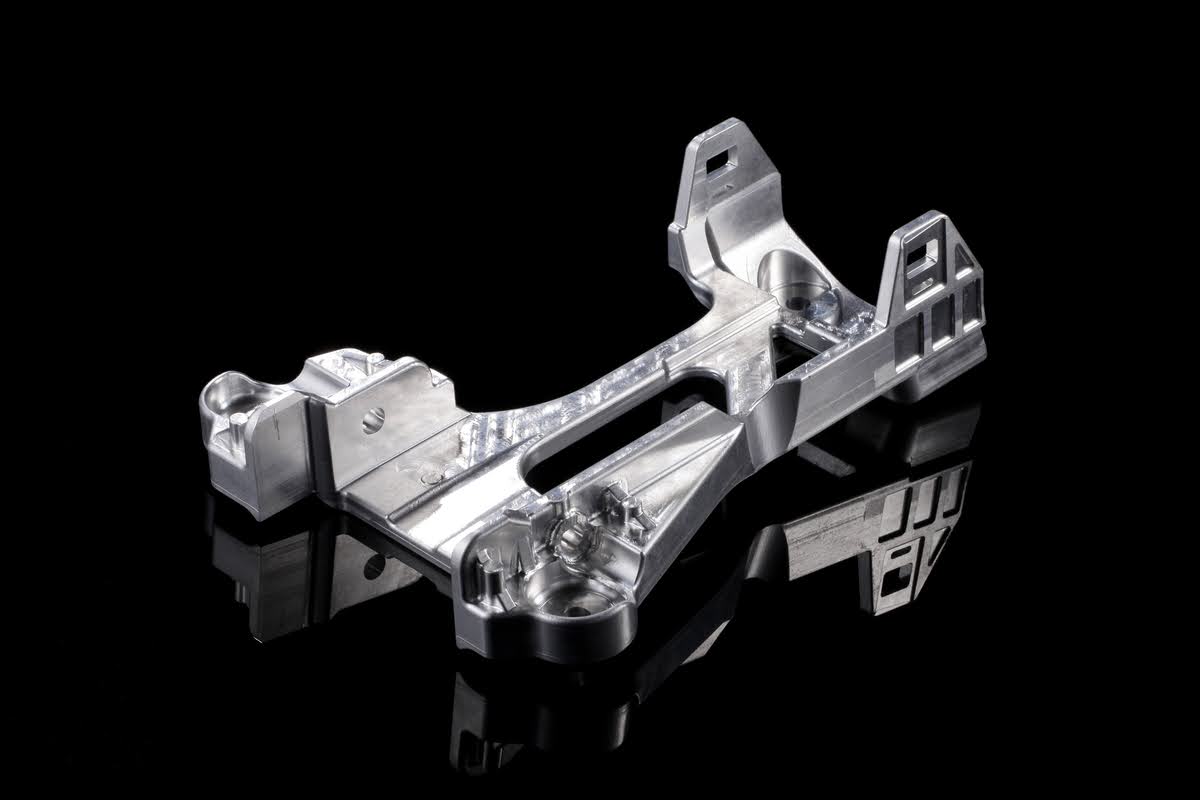
Casting or Machining: Choosing Based On Quantity and Demand
The quantity of parts you need will also figure into your choice. Earlier in the prototyping process you may not need many parts, so CNC machining makes more sense. The variability of your demand is another consideration: How often do you actually need to produce more parts? If demand fluctuates, CNC machining might be a better choice.
You can get CNC machined parts much faster and on demand, especially with digital transformation in the manufacturing industry. So, CNC machining is more economical since you can order parts as needed instead of trying to predict demand and ending up with excess parts in inventory.
However, if you’re moving into production with the expectation of high demand, casting is a good choice because it’s better suited to producing thousands of parts or more quickly.
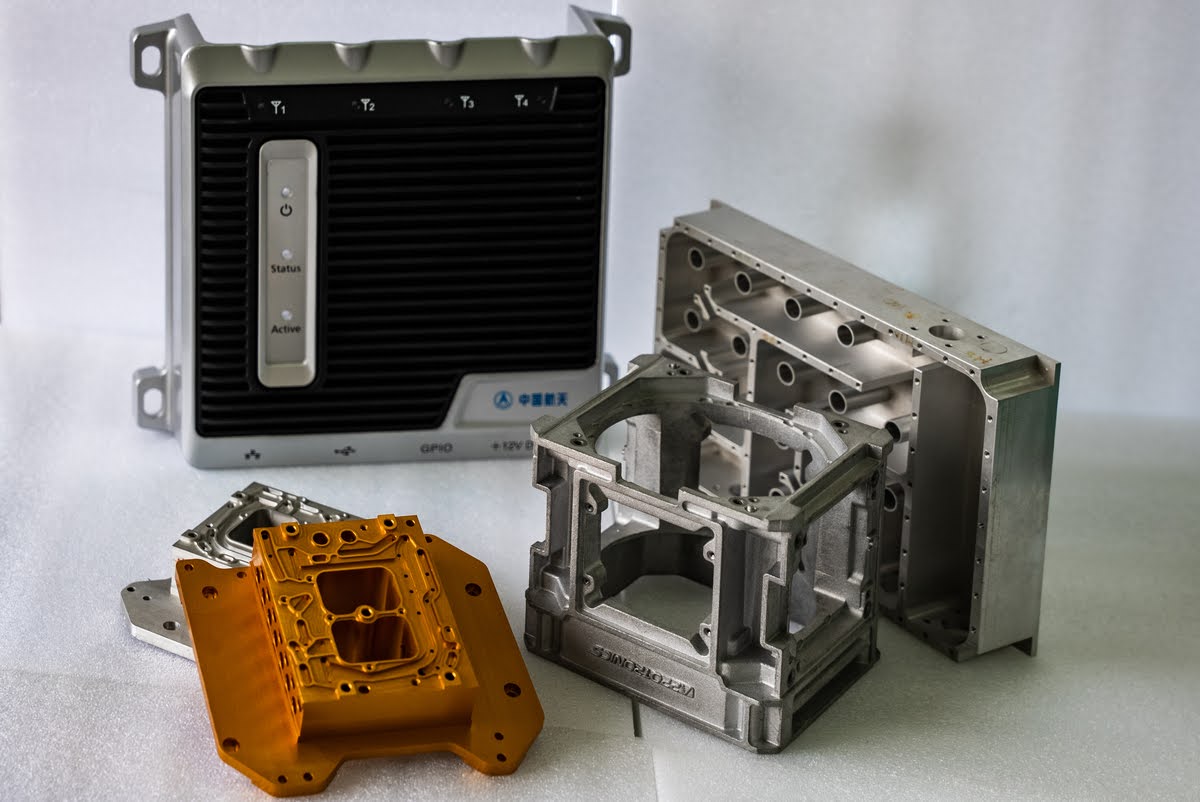
Casting or Machining: How Do You Choose?
When deciding between casting and machining, consider the following factors: your stage in the development process, the quantity of parts required, demand variability, and the geometry of the parts. It’s also important to note that you can use both methods; for instance, you can post-machine a die-cast part if necessary.
The proper manufacturing process will always come down to your specific opportunity. You may find yourself with a unique combination of requirements that forces you to be creative and find an innovative solution.
Although CNC machining has soared in popularity, there’s still a valuable place for casting! As we set forth in this article, each manufacturing method has its own advantages and disadvantages. With the knowledge you’ve gained, you can make the right choice for your project based on the part geometry, quantity, quality needs, and your timeline. Your project may even require a mixture of casting, CNC machining, and finishing!
Simplify Your Sourcing Decisions With Fictiv
Now that you know the differences between casting and CNC machining and have our tips for choosing the right method, you may need to source a supplier to produce your metal parts. Check out Fictiv’s CNC machining and die casting capabilities, then create an account and upload your part to find out how our instant quote process, design for manufacturability feedback, and intelligent platform can help you.
Fictiv is your operating system for custom manufacturing that makes part procurement faster, easier, and more efficient. In other words, Fictiv lets engineers, like you, engineer.