Time to read: 1 min
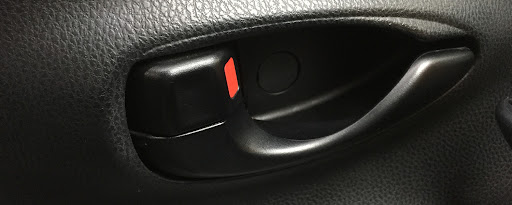
The Challenge: Shortening Innovation Lead Times
The automotive industry is highly innovative and competitive, which puts pressure on automakers to be both leading-edge and first to market. However, vehicle parts often go through dozens of iterations before the final part is deemed ready for mass production — requiring a speedy, efficient and cost-effective prototyping solution.
The Solution: Injection Molded Prototypes through Fictiv
In the early stages of part development, Fictiv will review part design plans and provide Design for Manufacturability (DFM) feedback. DFM allows you to remedy design issues earlier in the process to avoid costly roadblocks and pick up efficiencies along the way — which is key for ensuring speed to market.
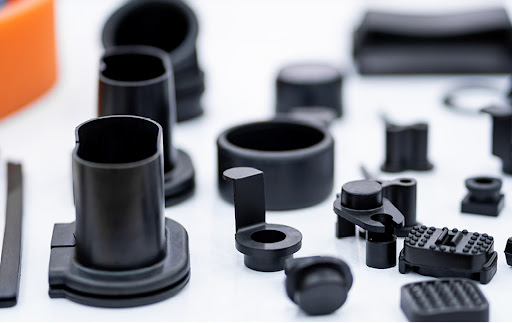
Fictiv’s injection molding services also offer the option to use low-cost, quick-cooling aluminum tooling for short runs of precision prototype parts. And once you’re past the prototyping stage and ready to scale up production, Fictiv offers steel molds for longer production runs and as a bridge tooling solution.

The Impact: Faster Prototype-to-Part Cycles
From exterior to interior to under the hood, Fictiv delivers high-performing automotive prototypes and parts with minimal lead time. Leveraging its technical design expertise and network of domestic and offshore injection molding manufacturing facilities, Fictiv has helped automakers produce functional prototypes in as little as three weeks. Precision end-use automotive parts can also be completed within 10 days — making “first to market” an achievable goal.