Time to read: 5 min
There’s a saying in the mechanical engineering world that really captures the gap between design and manufacturing: Anybody can design it; few people can make it.
As a design engineer, your job is to create a part or an assembly that will work properly. The manufacturer’s job is to make the part, make the assembly, and make sure they can make the same thing every time. They’re focused on the recipe: the ingredients and steps for baking, not just making a good muffin.
That means that a good design engineer has to understand those steps and document them. Give some thought to how you would do your job if you were the manufacturer, and write everything down.
Understand both your goal and your manufacturing partner’s perspective
As a design engineer, you need to understand the big picture–the whole muffin, if you will. Your role is to collaborate with stakeholders and make tradeoffs to incorporate your team’s needs into the design. You also need to account for whether you can make a part, whether you should make a part, and how to ensure you can make the part repeatedly.
“Winning” looks different to startups, compared to Fortune 500 companies. For example, some startups focus on just making a dozen parts to prove to investors it can be done. In contrast, companies like Johnson & Johnson, Proctor & Gamble, and Ford, who make hundreds of thousands of parts, need to be able to do that over and over.
Prototype and inspect your parts
Prototyping and assembling parts helps give you validation along the way of the steps required for a manufacturer to make that part at increasing fidelity, which helps bridge the gap between design and manufacturing.
Some mechanical engineers get what I call CADitis (I have been a victim): When you’re designing parts in CAD, you can zoom in and out, but as you’re working, you can lose your sense of how your design will work in reality. 3D printing is really useful because you can print a few designs and see what size they really are. Sometimes, you have to circle back to your engineering equations (bending stress, moments of inertia, etc.). I now have a pair of calipers at my desk to spot-check my reality (i.e., this belt looks more like a rubber band…I wonder if it can actually hold the load).
I also always inspect my parts, and it’s never backfired—data is always important (without data, you have what we in the science community call fake news). I’ll often ask for 10 parts and hold two back to get inspected, just to know where I am on my parts. If I see something questionable, I measure the rest of my parts to get more data. I take hand measurements (and record) before I assemble things, looking for data points along the way that challenge what I believe to be true, especially if there’s any risk that the assembly method could damage the part and mess up my ability to measure afterwards.
A lot of engineers overspec their parts and assume it’s correct without inspection, but I tend to assume it’s incorrect until I prove it’s correct. That’s because I’ve had parts that worked and then suddenly didn’t work, and I’ve had to look at the spec, compare what changed, figure out what measurements on the parts were different, and figure out what on the part has changed between my revs. That takes way more time than any time delay you might have asking for a systematic inspection to come with your original order.
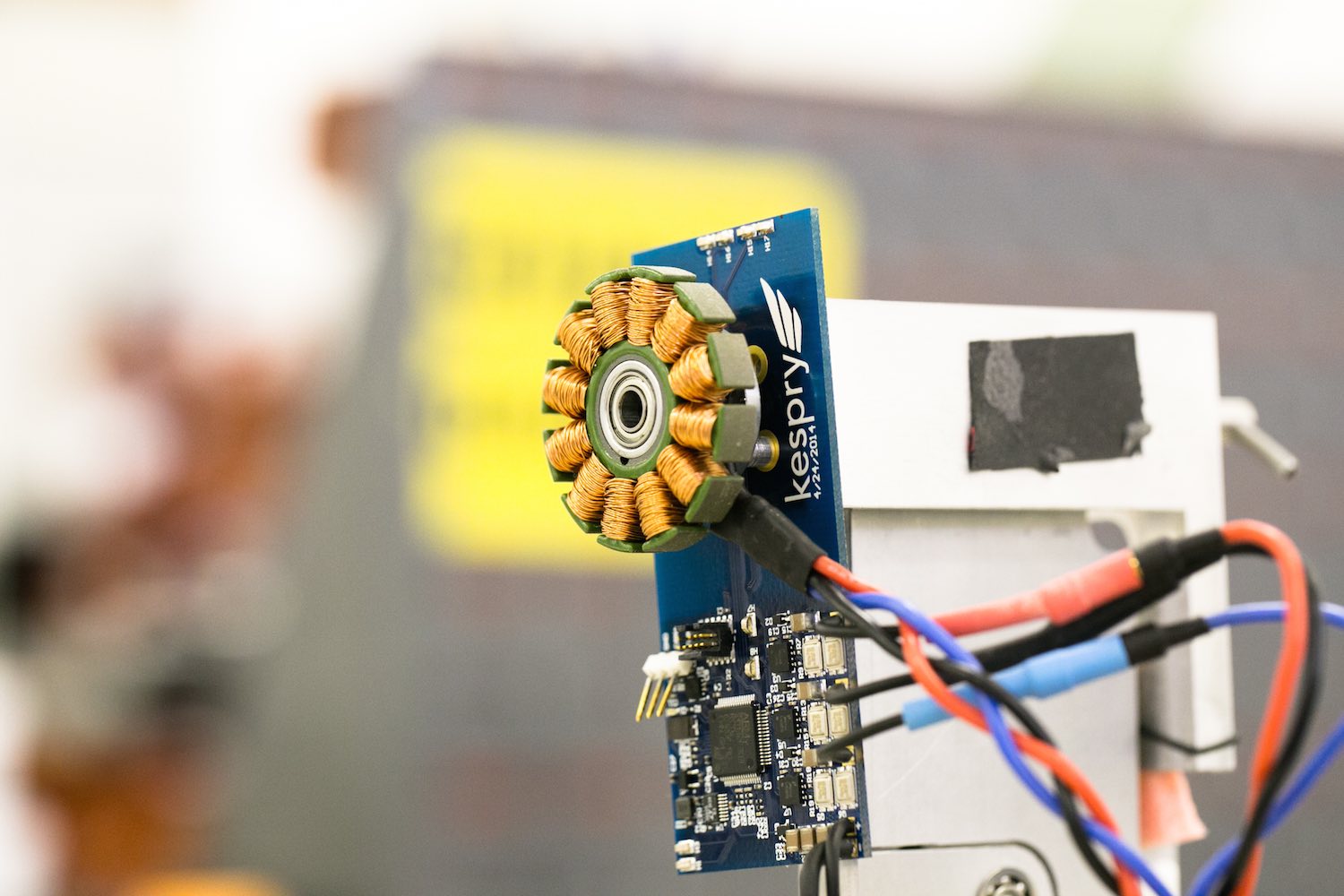
Document your process
It might seem like it’s much faster for one person to remember things in their head, rather than write things down in a format everyone can read and understand. However, in bigger companies, with procedures, S.O.P.s, and standards, you must write it down. That has nothing to do with the capability of the engineer and everything to do with longevity of the product and success of the company.
Writing it down isn’t something you do for yourself: You do it because if you leave, the next person needs to know how you got there. That’s the thing, when you bridge the gap between design and manufacturing: A paper trail is important because it’s the Reeses pieces trail that helps get ET home.
Your job as a design engineer is to make the design that helps meet business metrics and document it. I’ve been on projects before where the plan was only to make 500 parts, and then all of a sudden, the market was super receptive, and the product forecast did so well that we needed to make 50,000. That’s only doable if the steps are written down, parts are measured, etc., and even then, this is a different requirement. Different inputs drive different outputs.
Documentation is also essential for safety in certain industries. In the aerospace and medical industries, in which I’ve spent much of my career, writing down your work for teammate review is nonnegotiable, and your parts have to be perfect for safety.
I personally believe a real engineer puts work out for their team members to critique. It’s not a closed-book test; leverage your team’s expertise.
You can document your process in an engineering journal or in CAD (computer aided drafting). You can do rolling revisions in CAD and see the progression of your design according to your notes in CAD. Note what you changed and why. It doesn’t have to be super exhaustive, but do it frequently to track updates to your design, so anyone reading it can follow your train of thought.
While that’s a must-do for medical and aerospace projects, it’s useful for everything. On a recent air conditioning unit project, writing down our decisions helped us troubleshoot issues.
Bridging the gap between design and manufacturing involves GDP (good documentation practice), and if you skip it, your manufacturing team will be upset–and let’s be real, you’ll be upset with yourself, when the inevitable, “Whoopsie!” happens. Good documentation pulls enough from the GDP rulebook (which is exhaustive) to make it clear how to move forward. Don’t get sucked into, “You’re saying it wrong. It’s LeviOSA, not LevioSAR!”—nobody’s got time for that.
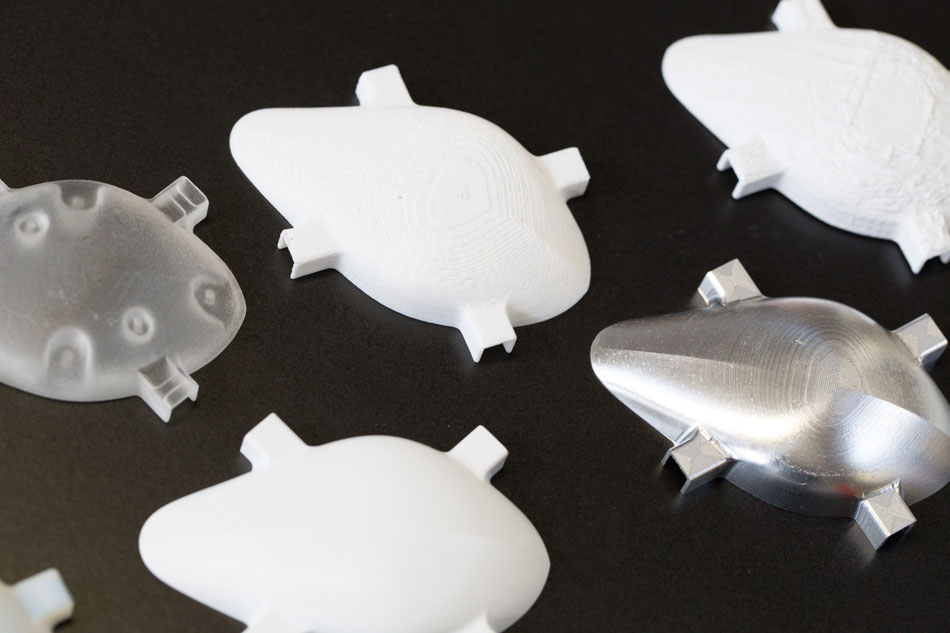
Use Fictiv to help bridge the gap from design to manufacturing
I talked about some of the ways you can use 3D printing to prototype and do initial reviews, but you can also use Fictiv for CNC DFM to understand part limitations. You might learn that something can be done if you add certain processes that might be more expensive. You might learn that it can’t be made or that it must be made with a 5-axis. You might get insight into random features you’re unsure about.
Fictiv can help with design experimentation. If you’re unsure about something, make three versions of the part and test them. Fictiv can also help provide parts for testing, when you’re evaluating materials selection, surface finish options—everything that contributes to your design and prototype performance.
Our engineers and sales team can answer your questions before you place an order, too. Let us know what questions you have now, or learn more about our 3D printing and CNC capabilities.