Time to read: 6 min
Injection molding and blow molding can both produce plastic parts. These two manufacturing processes have some important differences, however.
- Injection molding heats plastic, injects it into a highly pressurized mold, and produces solid plastic parts. Depending on their design, injection molded parts can have complex shapes and intricate details. Examples include medical and aerospace components.
- Blow molding uses pressurized air to inflate a tube of heated plastic inside of a mold. Blow molded parts are hollow and lightweight, and they feature relatively simple designs. Examples include water bottles and milk jugs.
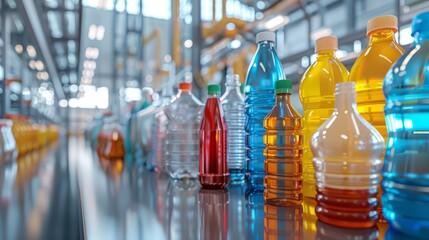
There are other differences between blow molding and injection molding, as the table below explains. Importantly, these differences cover everything from part design and material selection to tooling and production.
Table 1. Injection Molding vs. Blow Molding Comparison
Blow Molding | Injection Molding | |
Part Design | ||
Types of Parts | Hollow, simple parts | Solid, complex parts |
Wall Thickness | Thinner | Thicker |
Design Complexity | Less | More |
Design Flexibility | Less | More |
Strength | Less | More |
Part Sizes | Small to Medium | Small, Medium, and Large |
Precision | Less | More |
Materials | ||
Form Factor | Powder Pellets | Powder Pellets |
Thermoplastics | Fewer thermoplastics | More thermoplastics |
Tooling | ||
Cost | Less | More |
Life | Shorter | Longer |
Production | ||
Pressure | Lower | Higher |
Speed | Slower | Faster |
Part Volumes | Lower | Higher |
Requires Post-Processing | Yes | No |
This article from Fictiv explains what part designers need to know when comparing blow molding to injection molding. Keep reading to learn how each manufacturing process works and then compare these two plastic manufacturing methods in detail.
How Does Blow Molding Work?
Blow molding uses heat, compressed air, and metal tooling to produce plastic parts. There are three different versions of the blow molding process, depending on whether the plastic is extruded, injected, or stretched. There are other differences as well, as the following sections explain.
Extrusion Blow Molding
Extrusion blow molding (EBM) heats plastic powder or pellets and extrudes this molten material into a hollow tube called a parison or preform. The mold then closes around the parison and holds the plastic tube in place. Compressed air is blown in so that the parison inflates and plastic fills the entire mold. The part is cooled, removed from the tool, and trimmed.
Typically, EBM is used to mold parts and products like jugs and bottles.
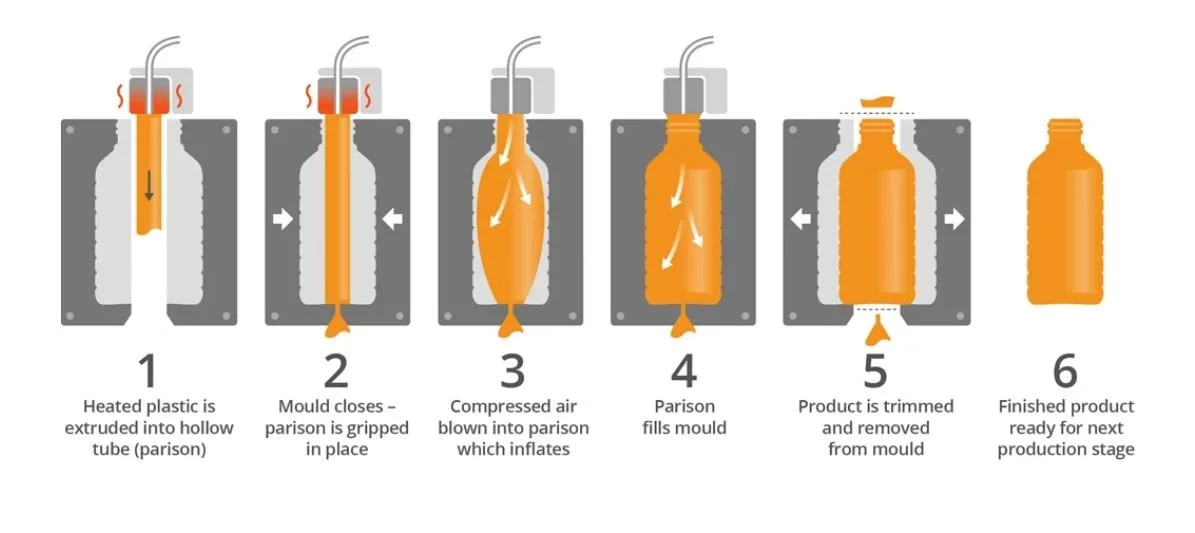
The extrusion blow molding process. Image Credit: Robinson
Injection Blow Molding (IBM)
Injection blow molding (IBM) heats plastic powder or pellets and injects this molten material into a special preform mold. The solid preform is then heated to a stretchable temperature and transferred to a blow mold, where the tool closes and air is blown in. The pliable plastic expands to the shape of the blow mold and then cools and solidifies. The mold opens, the finished part is ejected, and post-processing, such as trimming, occurs.
IBM is used for producing small, precise parts like medical syringes and small bottes.
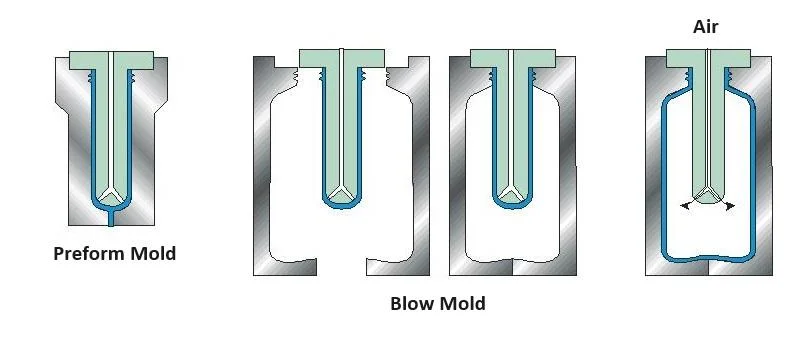
The injection blow molding process. Image Credit: Plastic Production
Stretch Blow Molding (SBM)
Stretch blow molding (SBM) stretches the preform or parison to improve the strength and clarity of the end product. This can be a one- or two-stage process.
- One-Stage: The preform is molded and stretched in one machine.
- Two-Stage: Preforms are molded, then reheated, and blown into shape.
SBM is ideal for making strong, clear containers like plastic water bottles.
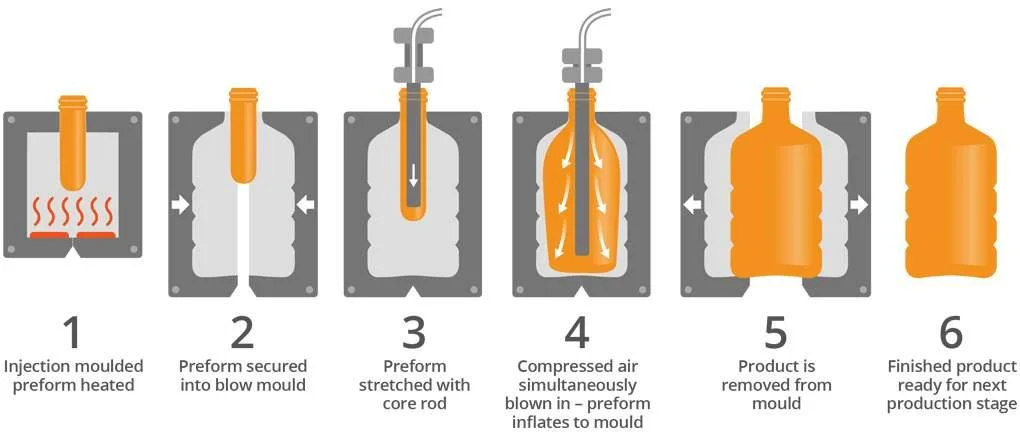
The stretch blow molding process. Image Credit: Unity Manufacture
How Does Injection Molding Work?
Injection molding uses heat, pressure, and metal tooling to produce plastic parts. The process begins when plastic powder or pellets are fed into a hopper. These granules enter a barrel and are heated to a molten state. A screw inside the barrel pushes the molten plastic through gates and runners into a mold cavity. The plastic part is then cooled and ejected from the mold. Sometimes, post-processing is necessary.
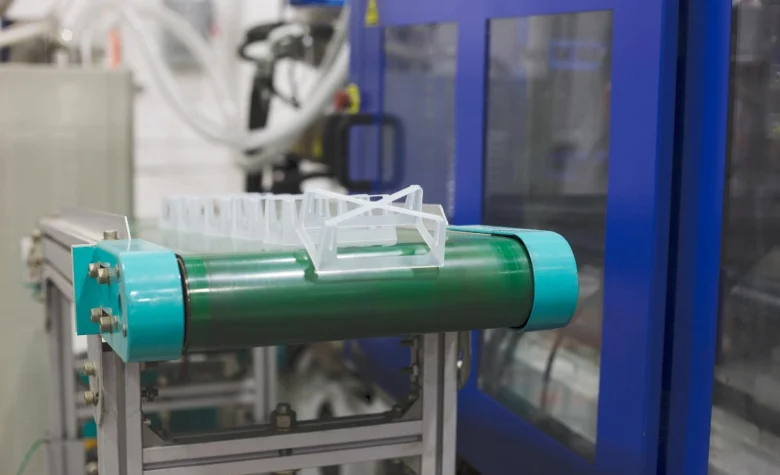
Injected molded parts moving on a conveyor after leaving a press
Now that you know the basics of how blow molding and injection molding work, it’s time to consider how they compare in terms of part design, materials, tooling, production, and applications.
Part Design
Injection molding supports the design of solid plastic parts with an excellent surface finish. Compared to blow molding, injection molding also supports greater design complexity and parts with thicker walls and features such as ribs for added strength. In addition, injection molded parts are characterized by higher precision, tighter tolerances, and greater part-to-part uniformity. In terms of size, injection molding supports small, medium, and large parts.
Blow molding supports the design of hollow, lightweight plastic parts with thinner walls. Compared to injection molding, this process also supports simpler designs that require less precision. Blow molded parts are weaker than injection molded parts, and defects such as air leaks, streaking, and wall thinning can occur. Blow molding doesn’t support large parts, but is suitable for small or medium-sized components.
Materials
Blow molding and injection molding both support the use of thermoplastics, polymers that can be recycled and reused. Typically, blow molding uses soft, flexible thermoplastics such as acrylonitrile butadiene styrene (ABS), high-density and low-density polyethylene (HDPE and LDPE, respectively), and polypropylene (PP). These materials are ideal for creating hollow, thin-walled products like bottles and containers.
Injection molding can use these materials, as well as rigid plastics such as polycarbonate (PC). Additionally, injection molding can be used with reinforced materials such as glass-filled nylon. Blow molding can also use these materials, but the applications are less common since blow molded products aren’t as strong as injection molded parts.
Other thermoplastics used with both processes include:
- Acrylic
- Acetal (POM)
- Polyetheretherketone (PEEK)
- Polyvinyl Chloride (PVC)
- Polyester
- Urethane
Because blow molding creates hollow, thin-walled parts, it uses less material than injection molding. This reduces material costs, but blow molding has other advantages as well. For example, because blow molded parts are lighter-weight, they cost less to transport. However, thin-walled parts are also more susceptible to damage.
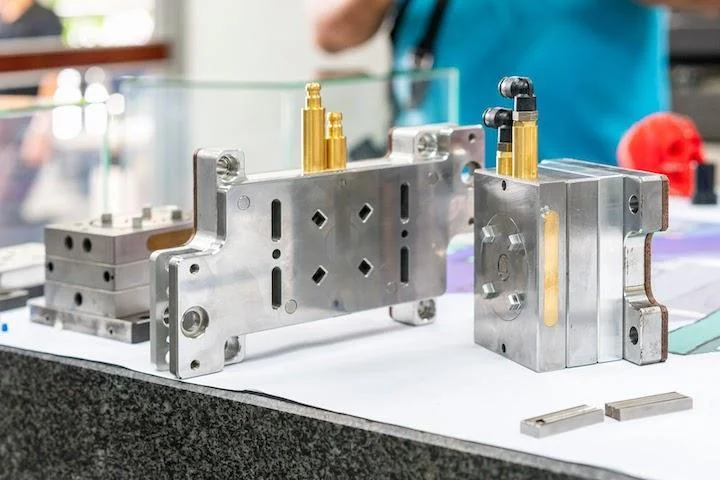
Injection molds cost more than blow molds but last longer.
Tooling
The tooling for blow molding costs less. Because its molding pressures are lower, blow molds use tools made from less durable and less expensive materials, typically aluminum, stainless steel, or beryllium-copper alloys. Blow molds won’t last for as many cycles as injection molds, but blow molding is a low to medium-volume process. The tooling for blow molding also costs less because the part designs are less complex and require less machining.
Injection molds are more expensive because they’re made from materials that withstand high clamping pressures. Otherwise, the mold halves could separate during the injection process. Although injection molds can be made of aluminum, various grades of steel are used to produce parts that require greater precision and higher production volumes. The larger part sizes and greater complexity that injection molding supports also increase mold costs. Across higher part volumes, however, the per-part cost of an injection mold decreases.
Production
When it comes to parts production, blow molding and injection molding differ in terms of pressure, speed, part volumes, and whether post-processing is required. Injection molding pressures are higher, but this plastics manufacturing process is faster and can produce parts in as little as 60 seconds. This makes injection molding ideal for high-volume production runs, despite its higher initial tooling costs.
Blow molding is slower and has longer cycle times. Still, that might not be an issue for low-to-medium part volumes, especially when accounting for blow molding’s lower initial tooling costs. Because it’s less precise, however, blow molded parts require trimming. That adds costs and extends project timelines. Extrusion blow molding is faster than injection blow molding, and stretch blow molding can be either faster or slower depending on whether a one-stage or two-stage process is used.
Applications
Finally, blow molding and injection molding differ in terms of applications.
Blow molded parts are used for these types of applications:
- Packaging: Plastic bottles, containers, and jugs for products like food and beverages
- Automotive: Fuel tanks, ducts, and reservoirs
- Household Products: Laundry baskets, water containers, and toys
- Medical: Vials and pharmaceutical packaging
- Industrial: Tanks for storing chemicals
- Furniture and Home Goods: Waste bins and patio chairs
Injection molded parts are used for these types of applications:
- Packaging: Caps, lids, and thicker-walled containers
- Automotive: Bumpers, dashboards, door panels, and internal components
- Consumer Goods: Toys, household items, and electronic housings
- Medical: Syringes, diagnostic devices, and single-use healthcare products
- Electronics: Housings and components for electronic devices
- Construction: Flooring panels, roofing vents, insulators, and deck fasteners
Is Blow Molding or Injection Molding the Right Choice?
What kind of plastic part does your project require? Solid or hollow? Thin-walled or thick-walled? Simple or complex? Blow molding is fine for parts like water tanks, containers, beakers, and bottles; however, if your part design has complex features and requires fine details, injection molding is the better choice.
Fictiv provides plastic injection molding services and provides expert design for manufacturing (DFM) feedback along with your request for a quote. As your go-to platform for mechanical parts from prototyping to production, Fictiv can injection-mold complex parts at amazing speeds.
Are you ready to get started? Create a free Fictiv account and upload your design today!