Time to read: 7 min
Does the part or product you’re designing fully consider your customer’s wants, needs, and expectations? That’s where Advanced Product Quality Planning (APQP) can help. APQP is a structured approach companies use to design, develop, and launch products that consistently meet customer requirements for quality.
APQP provides a framework to identify potential problems early in the product development process so the problems or risks can be mitigated, reducing the potential for quality issues or nonconformances during manufacturing. One goal of APQP is to ensure that customer requirements for quality and the design intent for each part are met.
Read on to learn more about APQP and how it can help provide better product quality and customer satisfaction.
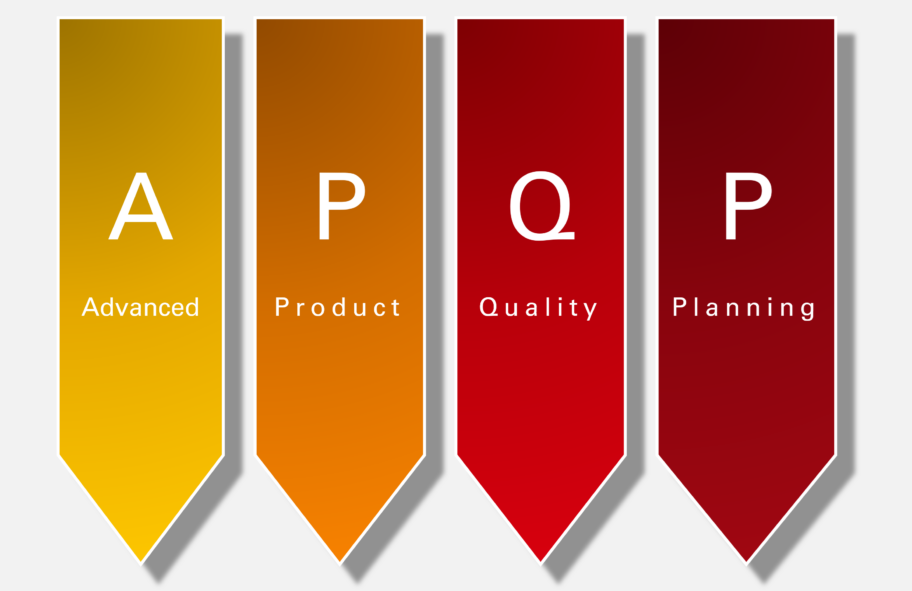
What is Quality?
The Q in APQP stands for quality, a term that’s frequently used but not so easy to define. According to the American Society for Quality (ASQ), quality is “the totality of features and characteristics of a product or service that bear on its ability to satisfy given needs.” In other words, quality is conformance to requirements. These are primarily customer requirements, but may also include regulatory or statutory requirements, such as for medical devices. Quality assurance is also about mitigating and containing issues as they arise in order to make the best product possible.
However, quality is about more than making a good product, as business management experts Hirotaka Takeuchi and John Quelch wrote in the Harvard Business Review nearly 40 years ago. Successful companies define quality in terms of meeting customer expectations, but the authors admit that “pinpointing what consumers really want is no simple task.”
That’s why successful companies take a deep dive into the customer experience. Haircare innovator m’Chel successfully worked with Fictiv to test for defects that would negatively affect the user’s experience and create a better product. It’s also important to note that many Quality Management System standards, such as those outlined in AS9100, have requirements for measuring and analyzing customer satisfaction, which can include surveys, feedback forms, and complaint analysis.
What is APQP?
APQP was originally developed for the automotive industry to give companies a way to meet the requirements of IATF 16949. IATF stands for the International Automotive Task Force, and the 16949 standard applies to companies that make automotive parts, assemblies, and components.
Advanced Product Quality Planning can help you improve quality because it amplifies the voice of the customer. In other words, APQP ensures that your customer values are clearly understood, translated into requirements, and present in technical specifications. That might sound simple enough, but there’s a risk that customer requirements will be overlooked because of other priorities.
Sometimes, that risk is highest during a New Product Introduction (NPI). There’s a rush to take a product to market, and design and manufacturing decisions that seem like shortcuts ultimately result in production delays and customer dissatisfaction. Customer requirements can also be overlooked if a product or process change occurs after NPI is complete.
APQP and The Core Tools
APQP originated in the automotive industry during the 1980s to help Tier 1 companies improve product planning. It’s one of the Core Tools that the Automotive Industry Action Group (AAIG) developed to help automakers comply with IATF 16949, a standard that established the requirements for a quality management system (QMS) specifically for automotive manufacturers.
The other Core tools to be used for compliance with IATF 16949 are:
- FMEA (Failure Modes and Effects Analysis): Helps identify potential problems during product and process development
- PPAP (Production Part Approval Process): Ensures that a supplier’s manufacturing process can consistently produce parts that meet design and specification requirements
- MSA (Measurement Systems Analysis): Checks the quality of measurement systems such as coordinate measuring machines
- SPC (Statistical Process Control): Uses statistical methods, like control charts, to monitor and control the production process. This helps keep the process stable and ensures consistent product quality
Today, APQP isn’t limited to the automotive industry. Along with the other Core Tools, it’s used by companies in the aerospace, defense, medical device, electronics, and consumer products industries. APQP isn’t a substitute for compliance with ISO or other standards, but it does often lay the groundwork for an organization’s quality management system.
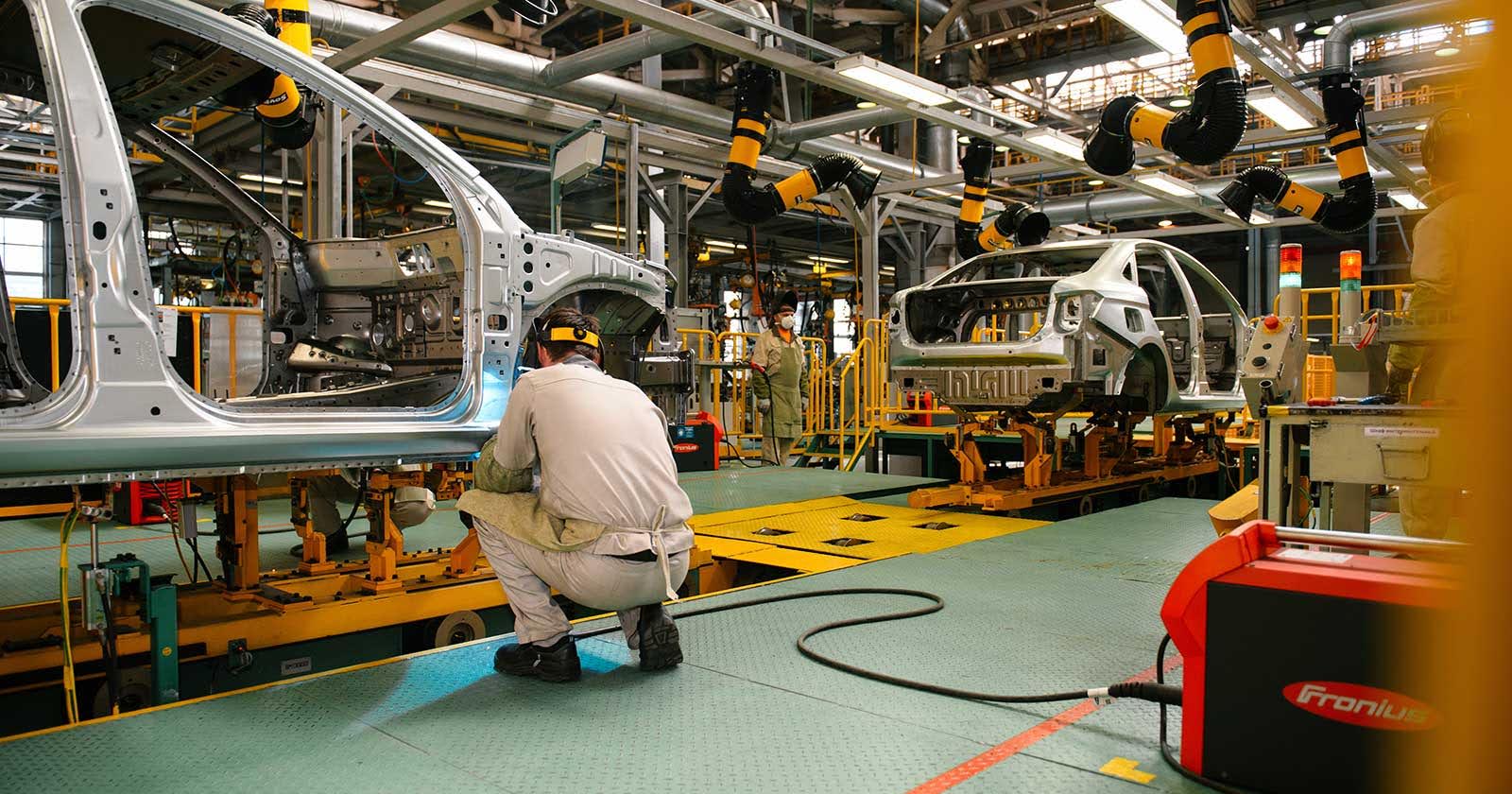
APQP and Product Quality Plans
APQP requires the establishment of a Product Quality Plan (PQP). This comprehensive document outlines the strategies, processes, and procedures needed to ensure that a product meets customer requirements for quality. In other words, it serves as a roadmap for the entire product development lifecycle, from initial concept through production and delivery.
These are the main components of a Product Quality Plan:
- Program Management and Planning: Defines the project scope and objectives along with the timeline and milestones
- Design and Development: Includes the product design requirements as well as the design review and verification steps
- Validation and Testing: Encompasses product and process validation plus control plans, which are documents that outline the processes needed to maintain quality throughout production
- Launch and Production: Begins with pilot production runs that are used to test the manufacturing process, then uses PPAP for ensuring consistent parts production
- Feedback, Assessment, and Continuous Improvement: Monitoring and feedback mechanisms and processes for corrective actions and ongoing improvements
- Documentation and Communication: Specifies the documentation to maintain throughout the project, such as design records and test results, and also outlines how information will be communicated among project stakeholders
APQP and Cross-Functional Teams
APQP uses cross-functional teams that grow and change as a project progresses. This collaboration leverages input from experts in departments such as design, sourcing, engineering, manufacturing, and quality assurance. The different viewpoints of a cross-functional team provide a holistic picture of the product and help identify possible weak points.
Initially, the cross-functional team gathers key details for product/process planning. Examples include project scope, key product requirements, past issues, team structure, and timing. As the project moves forward, experts from different areas join as needed. For example, purchasing personnel contribute to make/buy decisions about components, and packaging experts help with the selection of cardboard boxes or plastic containers.
What are the Benefits of APQP?
Advanced Product Quality Planning benefits the part or product designer, the manufacturer, and most importantly, the customer. Here is an overview of APQP’s main benefits.
- Better Product Quality: APQP’s risk assessments, control plans, and production trials aim to identify and address potential quality problems before mass production begins.
- Customer Satisfaction: When products meet or exceed expectations, customer satisfaction levels increase. Ultimately, this supports stronger relationships and opportunities for additional sales.
- Efficiency: With its early-stage emphasis on finding and resolving problems, APQP can minimize delays at subsequent and more complex stages of production.
- Cost Reductions: APQP helps to reduce costs associated with rework, product returns, redesigns, and warranty claims.
- Improved Supplier Relations: APQP’s emphasis on understanding and meeting customer requirements leverages the knowledge and expertise of suppliers.
- Better Risk Management: The risk assessment process within APQP helps companies take a proactive rather than reactive approach to problem-solving.
- Enhanced Process Control: Using SPC in conjunction with APQP enables manufacturers to closely monitor and control the production process.
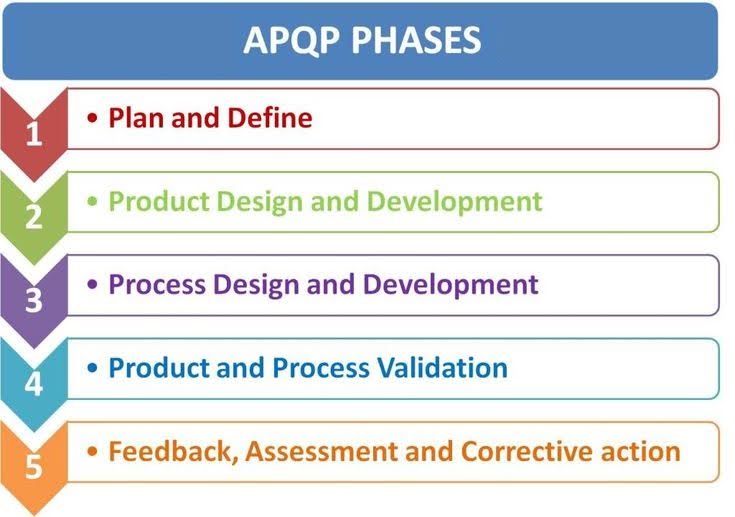
The 5 Phases of the APQP Process and How to Implement Them
The APQP process consists of one pre-planning phase and five concurrent phases, or stages.
Phase 0: Pre-Planning
APQP begins with gathering data, questioning assumptions, and applying lessons learned. The pre-planning stage involves collecting existing information, such as customer questionnaires, and identifying areas where significant changes may occur. This establishes the basis for a smooth transition to the planning phase.
Phase 1: Plan and Define
The goal is to ensure that a product will meet a customer’s standard for quality right from the start. Planning involves understanding the customer’s needs and translating them into product requirements. This stage covers product design, reliability objectives, quality targets, the bill of material (BOM), preliminary process flow, special attributes or features, product assurance planning, and securing management support.
Phase 2: Product Design and Development
During product design and development, engineers review geometry, features, and tolerances and create prototypes to test the design. Tools like Design Failure Mode and Effects Analysis (DFMEA) can help identify potential issues. The outputs include detailed engineering drawings, material specifications, and a prototype control plan.
Phase 3: Process Design and Development
This phase ensures the manufacturing process is well-defined, efficient, capable of meeting production demands, and manufacturable (i.e., DFM). Deliverables include Process Failure Mode and Effects Analysis (PFMEA), a risk management tool that helps organizations identify and evaluate potential failures in a process.
Phase 4: Product and Process Validation
Validating both the product and the process ensures that a manufacturer can meet all quality standards while handling the required production volume. MSA and SPC, two of the other five Core Tools, are used. PPAP is also completed during this stage.
Phase 5: Feedback and Corrective Action
The final phase, the full-scale production launch, focuses on evaluating and improving processes. The company collects feedback from manufacturing, assesses any issues, and implements corrective actions. The goal is to reduce variation and use lessons learned to ensure ongoing quality and customer satisfaction.
Choose Fictiv for High-Quality Parts
Fictiv works closely with a carefully vetted network of manufacturing partners who provide streamlined CNC machining, injection molding, 3D printing, and more—all backed by AI-powered instant quoting and expert design for manufacturability (DFM) feedback. Our team of manufacturing and quality engineers ensures your parts meet the highest standards, helping you optimize designs, select the right materials, and mitigate production risks.
Whether you’re prototyping, scaling to low-volume production, or preparing for high-volume manufacturing, Fictiv simplifies the sourcing process to deliver precision parts at industry-leading speeds. Get started by creating a Fictiv account and uploading your part file. You’ll receive DFM insights along with your quote within 24 hours.