Time to read: 11 min
Aluminum Anodizing Overview
The anodizing process (sometimes known as anodization) converts the surface of aluminum into a thicker, more uniform oxide layer through an electrolytic process.
Electrochemically anodizing aluminum produces an aluminum oxide surface that has:
- Corrosion resistance
- A pleasing appearance
- Wear resistance
- Improved paint or adhesive bonding
- Improved lubricity
- Improved plating adhesion
This article will focus on anodizing aluminum. But, other metals can be anodized, including magnesium, titanium, and aluminum alloy. There are several types of anodized aluminum finishes, including clear anodized aluminum, black anodized aluminum, and hard anodized aluminum. There are also a few commonly referenced anodizing types: Type I, Type II, and Type II.
Many industries typically use military specification MIL-PRF-8625 (which supersedes MIL-A-8625) to define the anodizing process such as anodizing line design and anodizing patterns. We will refer to it several times in this article. But, it’s always a good idea to check your anodizing requirements before specifying your design.
Benefits of the Anodizing Process
The natural aluminum oxide layer is replaced through the anodizing process with a new aluminum oxide layer to improve part durability, paint adhesion, component appearance, and corrosion resistance. It also produces a chemically resistant coating against harsh cleaning agents. The image below shows a few parts that have been anodized and then dyed in different colors.
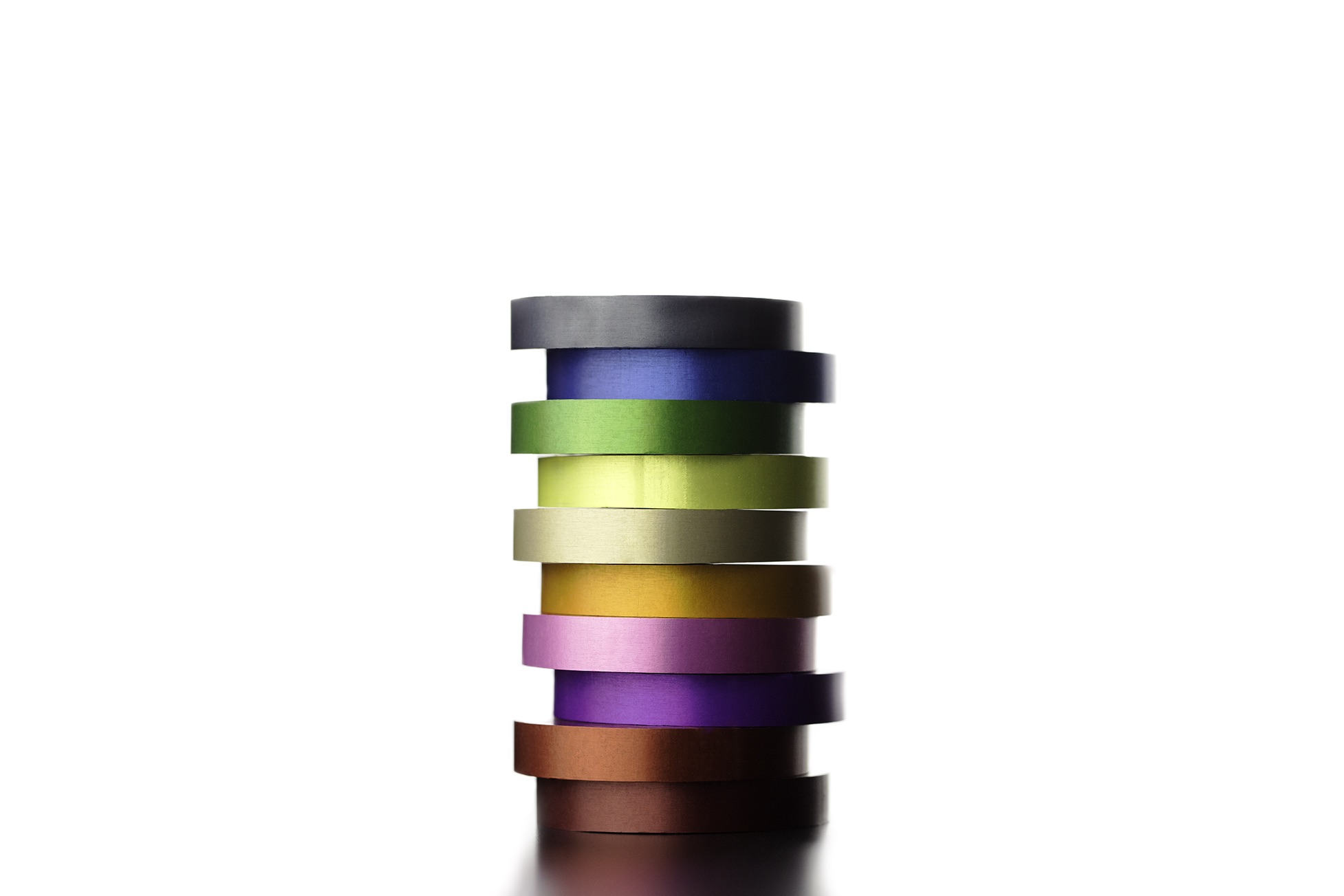
The anodizing process uses an acid bath and an electrical current to create this anodic layer on the base metal. In simple terms, we’re creating a controlled and durable aluminum oxide layer on our component instead of relying on the thin oxide layer that naturally occurs on any bare aluminum surface. It’s similar to bluing, Parkerizing, passivating, and other conversion coating surface treatments used for corrosion resistance and surface hardening.
Typical Applications for Anodized Aluminum Parts
Anodic oxide coatings have a broad range of applications, but one of the most common is for aesthetics because it enables dyeing components in various colors.
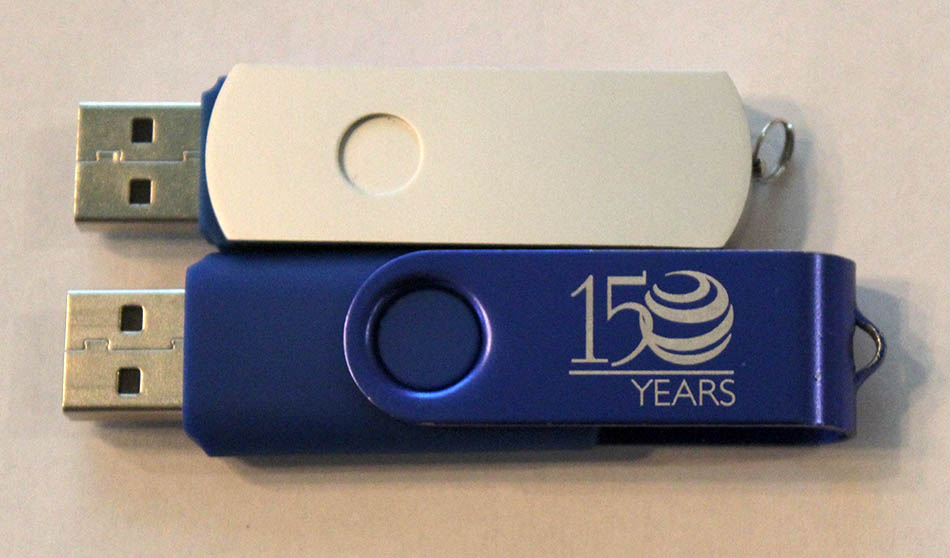
The top thumb drive is class 1 (undyed), so the anodic coating appears clean, and the color is almost that of the base alloy. The bottom thumb drive has been dyed a vibrant blue color. Another example is the thread adapter below that has been anodized and dyed black.
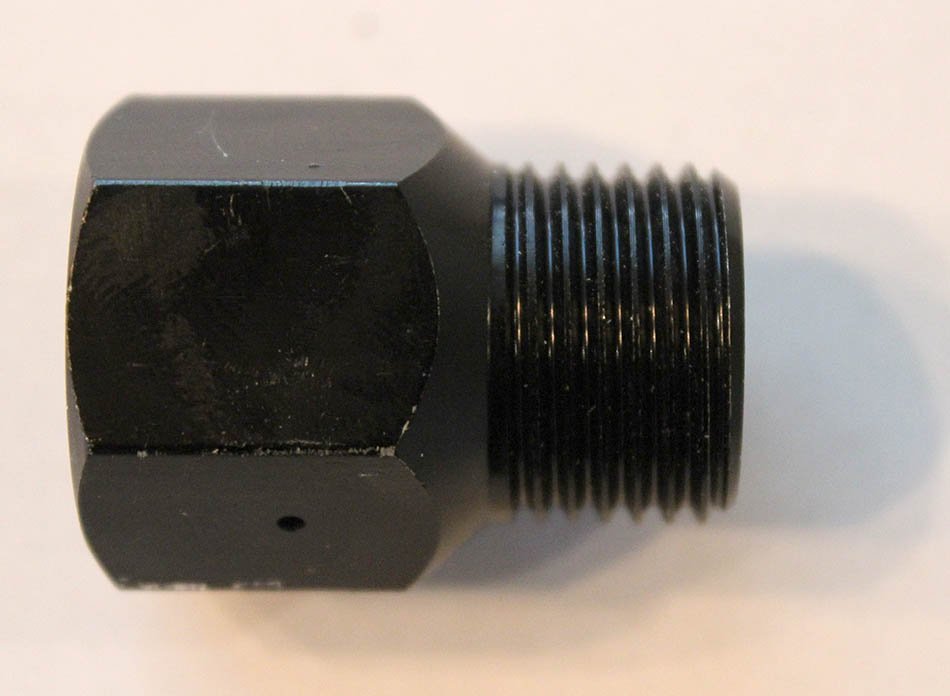
The thread adapter coating does not appear to be wear-resistant, indicating that it was coated with a thinner Type II anodize or was produced with poor process controls.
As a fourth example, we have some anodized heat sinks seen below.
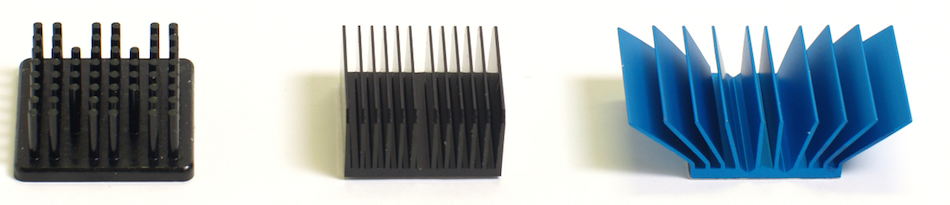
Anodic coatings can improve the effectiveness of heat sinks by increasing the surface emissivity by an order of magnitude over bare aluminum, which improves the radiation heat transfer.
Below, we can see a matte black valve that has a relatively high-quality anodic layer. Also, note the attractive laser-etched logo that contrasts with the rest of the component. It’s common to etch through the anodic layer instead of printing on a part’s surface — both to increase the logo’s durability and to save cost and process steps.
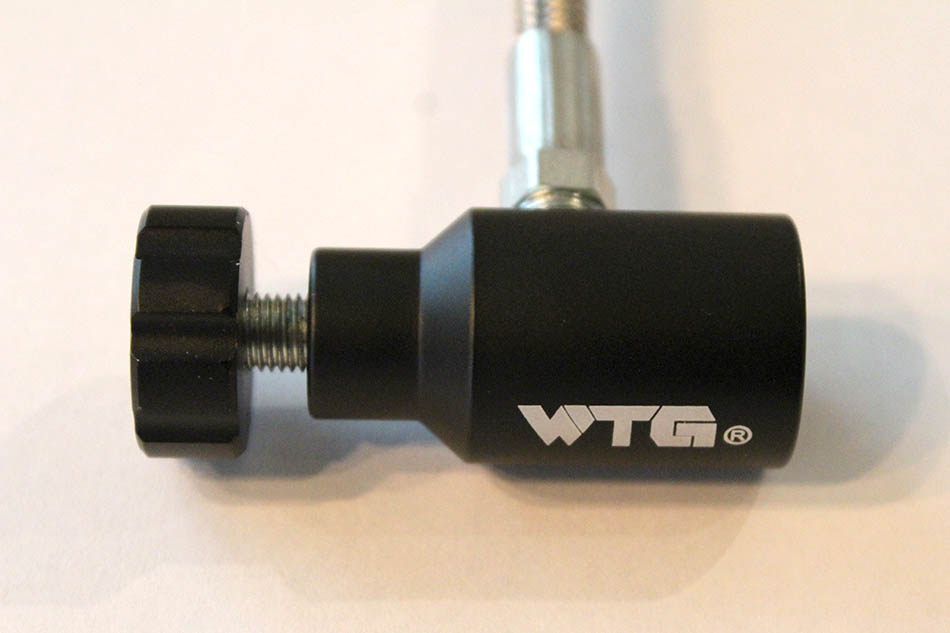
An anodized aluminum sheet is excellent for outdoor signage because it’s lightweight, corrosion-resistant, and more durable than paint. The anodized surface can be readily screen printed or covered with reflective materials like the outdoor signage example below:
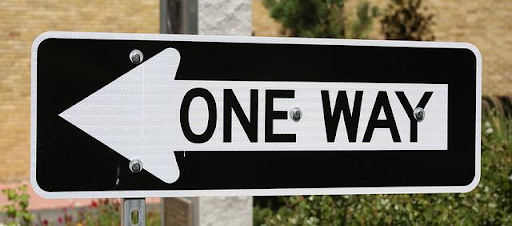
While we’ve discussed a broad range of applications, we’ve barely scratched the surface of all the potential applications for anodized aluminum. If you’re looking for more information and examples, we recommend you check out the Aluminum Anodizers Council’s website.
Types of Anodizing Aluminum Processes Available
Military specification MIL-PRF-8625 Type II acid sulfur anodizing and Type III hard coat anodizing are the most commonly used. Type II is widely called regular anodizing, while Type III is called tough or hard anodizing. What about Type I? We’ll get to that in a moment.
The three types of anodizing per MIL-PRF-8625 are as follows:
Type I
- Type I and IB – Chromic Acid Anodizing
- Type IC – Non-Chromic Acid Anodizing as a replacement for Type I and IB
Type II
- Type II – Conventional coating from a sulfuric acid bath
- Type IIB – Non-chromate alternative for Type I and IB coatings
Type III
- Type III – Hard Anodize
Each type of anodization creates different functional and aesthetic characteristics:
- Types I, IB, and II are used for corrosion, abrasion resistance, and paint preparation. For applications that are fatigue critical, Types I and IB are used because they are a thinner, more flexible coating — for example, these types are often applied to highly fatigued structural components on aircraft.
- Types IC and IIB are used when a non-chromate alternative is desired, often due to environmental regulations or requirements. When developing systems in the defense industry, new contracts require environmentally friendly options (Types IC and IIB) because of the hexavalent chromium in Types I and IB.
- Type III is used primarily to increase abrasion and wear resistance. It’s a much thicker coating that outperforms the other types for abrasion and wear. This coating may reduce fatigue life, however. Type III anodize is frequently used on firearm components, gears, valves, and other parts that slide relative to each other.
All anodizing helps the adhesion of paints and some other bonding agents as compared to bare aluminum. In addition to the anodizing process, some parts may be dyed, sealed, or treated with other materials, such as dry film lubricant. If a part is dyed, it’s considered Class II, whereas an undyed part is Class I per the MIL-PRF-8625 specification.
Elements to Consider When Planning for Aluminum Anodizing
Here’s what you need to consider when designing aluminum parts that will be anodized:
1. Dimensions
First, consider the dimensional change associated with anodizing aluminum components. On a drawing, an engineer or designer may specify that the dimensions apply after processing to compensate for this change. Still, drawings are rare when making rapid prototypes, especially when using a quick-turn service that relies on solid models.
When a part is anodized, surfaces tend to “grow” (i.e., the outer diameters will get larger, and holes will get smaller). This is because the anodic layer accretes on the part surface as it builds up the aluminum oxide.
The dimensional growth can be estimated to be approximately 50% of the total thickness of the anodic layer. The table below details the thickness ranges of the different types of coatings per the MIL-PRF-8625 spec.
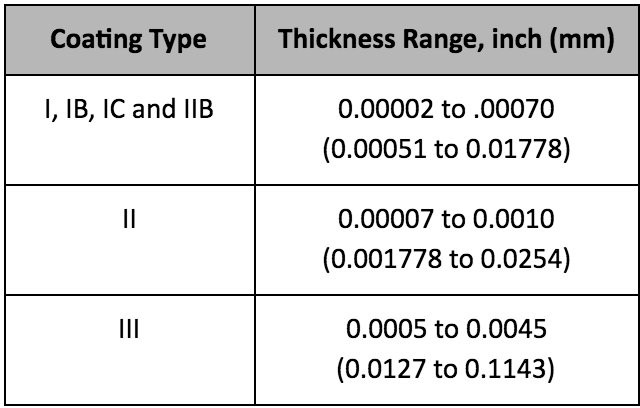
Of course, these thicknesses will vary depending on the specific alloy used and the process controls. If a designer is concerned about controlling the growth of a high-precision feature, it may need to be masked. In some cases, such as thick Type III coatings, the parts can be lapped or honed to the final dimension, but only for an added cost.
Another dimensional consideration is the radii of outside edges and inside corners because anodic coatings don’t form well on sharp corners. This is especially true for Type III coatings, where MIL-PRF-8625 recommends the following minimum corner radii for a given Type III thickness:
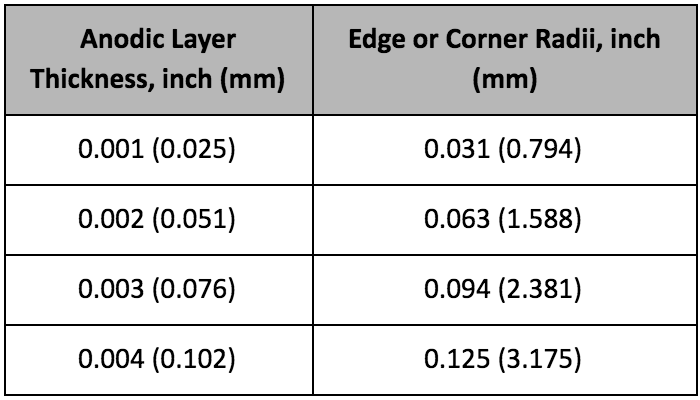
With thinner coatings, an edge break in the range of 0.010-0.020 inch may be sufficient, but it’s best to consult with your anodizing shop to verify their requirements.
2. Wear resistance
Given the increased hardness of the anodic layer, it follows that the surface hardness of the part being anodized increases as well. It is not typical to specify the hardness of the coating because of the interaction between the softer base metal and a hard anodic layer. MIL-PRF-8625 specifies a test for abrasion resistance to accommodate these challenges.
As a frame of reference, non-finished 2024 aluminum has a hardness in the range of 60-70 Rockwell B, whereas Type III anodize has a hardness of 60-70 Rockwell C. The image below is a CNC hold-down clamp that has been anodized and dyed red.
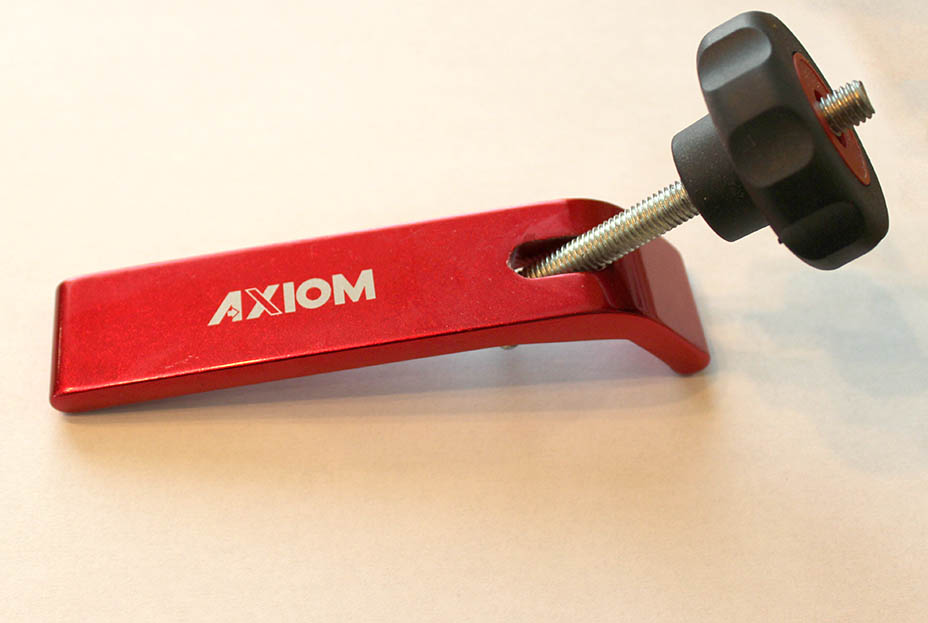
As you can see, the surfaces show almost no wear, despite being used to secure hardwoods, engineered plastics, and non-ferritic metals in a high vibration environment.
3. Adding color with dyes
Anodized coatings are dyed for various reasons, including aesthetics, stray light reduction in optical systems, and part contrast/identification in assemblies.
When it comes to dyeing anodize, it’s also essential to discuss expectations with the shop that will anodize the parts. Some key points to discuss with your suppliers are:
Coloring methods
- Electrolytic coloring
- The anodized aluminum is immersed in a bath containing metallic salts and the metal deposits fill the anodic pores utilizing electrolytic current. You can get different UV-resistant colors depending on the type of metal and the length of time the aluminum soaks in the bath.
- Dip coloring
- The anodized aluminum is placed in a heated dye bath so that the dye fills the anodic pores. De-ionized water is then used to end the process. You can get various non-UV-resistant colors with this process.
- Integral Coloring
- This process “integrates” the anodizing process with the dyeing process to form the oxide layer while also coloring the material in shades of bronze and black. This process produces a part that’s more abrasion resistant than conventional anodizing.
- Interference Coloring
- Sulfuric acid enlarges the pores of the anodized aluminum, then metal is deposited in the pores to produce a range of light-fast colors including shades of blue, green, yellow, and red. These colors result from optical-interference effects rather than the light scattering effects of the other coloring processes.
Color matching
It can be challenging to get a true color match with anodized parts, especially if they’re not all treated in the same batch. If an assembly is composed of multiple anodized pieces that are supposed to be the same color, you’ll need to dye them together or utilize unique controls to get the desired consistency.
Fading
Anodized coatings exposed to UV and heat may fade. Organic dyes are more affected than inorganic dyes, but many colors require organic dyes. Choose your hues accordingly.
Dye responsiveness
Not all anodize types and coatings will take dye well. Type I black anodized aluminum has trouble reaching true black because the coating is thin. Often the part will appear gray despite the black dye; a colored dye may not be efficient without special processing. Type III hard anodized aluminum may also appear dark grey or black on some alloys when the coating is thicker, therefore color choices will be limited due to the grey beneath. Some thinner Type III coatings may accept multiple colors, but if aesthetics are your primary concern, Type II is the best choice to get the widest range of color options.
4. Conductivity
Anodic layers are good insulators, despite the base metal’s conductivity. For this reason, it may be necessary to apply a clear chemical conversion coating and mask certain areas if there is a need to ground to a chassis or component.
(Protip: a common way to determine if an aluminum part is anodized is to test the conductivity of the surface with a digital multimeter. If the part is not anodized, it will likely be conductive and have very low resistance.)
5. Combined coatings
Anodizing is often performed prior to other surface finishing or coating processes due to its ability to improve adhesion and bonding for plated deposits and coatings alike. Here are some of the common coatings and surface finishes applied to anodized aluminum:
Paint
Anodic coatings may be painted to increase corrosion resistance and to achieve specific colors not obtainable through dyeing.
Teflon impregnation
Teflon can impregnate Type III hard coats to reduce their friction coefficient and is often used in mold cavities and sliding/contacting components.
Electroplating
Chrome plating is performed by electroplating nickel and then chromium on an anodized aluminum part. Decorative chrome plating gives an aesthetically pleasing shiny appearance with improved corrosion resistance. While hard chrome plating is not as shiny, it offers exceptional corrosion and wear resistance.
Other processes can be applied to change the properties of anodic coatings, but they’re rare and usually require working with a specialized vendor. If you have a particular need, it’s best to reach out to a coating specialist.
Considerations for Aluminum Anodizing
Anodizing aluminum provides many benefits, but the process has its limitations. Here are some to keep in mind:
- Thick anodic coatings may reduce the fatigue life of components, especially if they incorporate Type III processes.
- Geometric changes need to be considered for any parts that will be anodized. This is critical for Type II and III processes, but may not be required for some Type I.
- Color matching can be complex when dealing with multiple batches and very difficult when working with different vendors.
- For complete corrosion protection, it may be necessary to seal the pores of the anodic layer.
- The abrasion resistance of Type III hard coats will likely drop as the thickness approaches and surpasses 0.003″.
- Different alloys may respond in different ways to the anodizing process. For example, alloys with 2% copper content or greater are typically less wear-resistant than other alloys when subject to MIL Spec testing of Type III coatings. Which is to say that Type III hard coat on 2000 series aluminum and some 7000 series will not be as wear-resistant as 6061 with a hard coat. We recommend you consult your vendor if you have concerns with the alloy you are using.
FAQs
How does the aluminum anodizing process work?
The anodizing process converts the surface of aluminum into a thicker, more durable, and more uniform oxide layer through an electrochemical process. The porous structure of the resultant surface allows for improved paint and adhesive bonding, plating adhesion, enhanced heat emissivity, and permits secondary infusions of lubricants and colorants.
What colors can you anodize aluminum?
You can achieve most colors by using dyes during the anodizing process or by painting afterward (e.g., to achieve a pure white color).
Various methods are used for anodizing coloring, including electrolytic coloring, dip coloring, integral coloring, and interference coloring (see the Coloring methods section ). Possible anodizing colors include Black, Blue, Blue-Gray, Brown, Gold, Gray, Green, Olive Drab, Pink, Red, Violet, and Yellow. Some processes produce UV-resistant colors. Some processes produce colors caused by optical-interference effects, others by light scattering.
The anodized aluminum surface is also ideal for accepting paint, screen printing, or applied reflectives (i.e., reflective road sign materials) to achieve the desired color.
What does clear anodized aluminum look like?
Clear anodized aluminum has a uniform, transparent film with increased corrosion and wear resistance. The film varies in color from very light to dark gray as the coating thickness increases.
Which type of anodizing should I choose?
Most machined parts are anodized per Type II (or “regular”) sulfuric anodizing and Type III Hardcoat or “hard” sulfuric anodizing per Military specification MIL-PRF-8625. Type I anodizing uses an environmentally-unfriendly chromic acid that is specified rarely (e.g., military or aerospace applications requiring significant requalification efforts). Please see the “What elements should I consider…” section for additional details.
How much does anodizing aluminum cost?
The cost depends on coating thickness, anodizing type, secondary finishing services, part geometry, and batch size.
Does anodizing wear off?
Anodize is long-lasting because it is part of the base aluminum material. However, it can wear away with abrasion and the color may fade with extended outdoor exposure. Type III hard anodize retains its color and wear resistance longer than Type II.
Conclusions
Anodizing aluminum is an excellent surface treatment option to improve corrosion and wear resistance, but the applications extend far beyond that. Anodizing also improves paint adhesion, provides a good surface for impregnation, and improves other surface qualities and the aesthetics of coated parts.
Aluminum anodizing is complex, as discussed in this article. Utilize our design tips and account for our concerns and you’ll be well on your way to a successful batch of anodized aluminum parts.
Sourcing Simplified
It’s also complex to solidify the supply chain for anodized aluminum parts from material procurement to CNC machining to anodizing. But you don’t have to source your parts alone. If you’re tasked with sourcing and supplying CNC machined, anodized parts, Fictiv is your operating system for custom manufacturing that makes it faster, easier, and more efficient.
In other words, Fictiv lets engineers, like you, engineer. We offer a range of manufacturing capabilities to produce both simple and incredibly complex geometries — create a free account and upload your designs today!
Meta title: Aluminum anodizing: all you need to know
Meta description: learn all about aluminum anodizing with our simple guide which describes the different anodizing types and design for anodizing
We can see that the top thumb drive is class 1 (undyed), so the anodic coating appears clean, and the color is almost that of the base alloy, while the bottom has been dyed blue. In another example, we can see a thread adapter that has been anodized and dyed black.