Time to read: 7 min
Rivets are a versatile and low-cost method for fastening two components together. They’re typically used to attach sheet and structural members, and in some cases only require access to one side of the joint to install. Rivets are low-cost and come in a range of different materials like aluminum, stainless steel, and copper. This article will explain how rivets are typically installed, what materials are used, and describe some commonly used rivets.
What is a Rivet and how Does it Work?
A rivet is a permanent mechanical fastener that is designed to join two or more parts together, and there are numerous types of rivets. Each rivet is composed of a head, a shank, and a tail. To install, a rivet is inserted into a slightly oversized hole, then undergoes a process that permanently deforms it via a compressive force. This permanent deformation is achieved using a range of tools that are dependent upon the type of rivet being used.
In general, rivets are installed via pneumatic or manual hammering, hydraulic pressing, and handheld rivet guns that are either manually or pneumatically operated. When selecting rivet sizes, it’s critical to consider the grip length and the size of the hole. Many different grip lengths are available for each hole size to accommodate different sheet thicknesses. Rivets are typically made from either aluminum or steel, though other materials like copper are also used. Industries that most commonly rely on the use and function of rivets include the automotive, aerospace, marine/naval, construction, aviation, and manufacturing industries.
Materials Used for Rivets
Rivets are made from a range of different materials suited to specific applications. These materials are listed below:
Materials Used for Rivets
Rivets are made from a range of different materials suited to specific applications. These materials are listed below:
- Aluminum: Aluminum rivets are the most common. They’re lightweight and have good corrosion and weathering resistance. These rivets can be easily deformed and, as such, blind rivets made from aluminum can be installed with a hand-operated rivet tool.
- Stainless Steel: Stainless steel rivets have excellent corrosion and weathering resistance. However, due to their hardness, they’re difficult to install with hand-operated rivet tools. Pneumatic rivet guns are recommended for installing blind stainless steel rivets.
- Copper: Copper has an excellent electrical and thermal conductivity in addition to being relatively easy to form.
- Steel: Carbon steel rivets are usually solid or hollow shank and must be installed using pneumatic or hydraulic equipment. Low-carbon steel is preferred as it is more ductile than rigid, high-carbon steel.
- Brass: Brass is an alloy of zinc and copper that has exceptional corrosion resistance and strength, and cannot spark. These properties make brass rivets ideal for applications in the oil and gas industry. They are also used for their aesthetic appeal.
It must be noted that some materials can be prone to creating a galvanic corrosion cell. As such, rivet materials must be chosen carefully to ensure compatibility with the material being fastened.
What are the Different Types of Rivets?
Listed below are the different types of rivets available. Each type of rivet is designed with a specific type of application in mind:
Blind Rivets
A blind rivet is the most recognizable type of rivet, and is also referred to as a pop rivet. These rivets are used when there is no access to the rear of the two parts being fastened. A blind rivet assembly consists of a shank and a stem. To install, the thicker shank is placed into a precisely drilled hole, and a handheld or pneumatic rivet gun is used to pull on the stem, which has a slightly larger diameter on the end of the shank. The pulling action causes the shank to plastically deform and clamp the two parts together.
The stem is designed to snap off at a specific clamping force and this snapping creates an audible popping sound, hence the name pop rivet. Blind rivets are supplied with an open-end, closed-end, large flange, grooved, and countersunk flanges. Blind rivets are often used on sheet metal constructions.
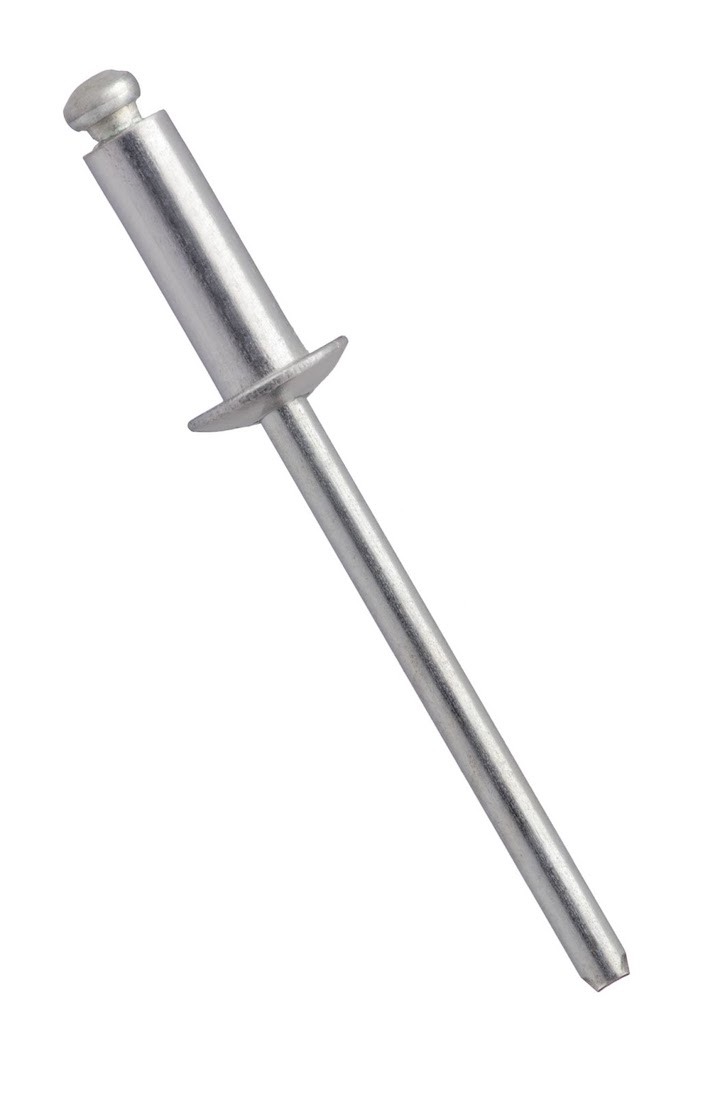
A Blind Rivet
Solid Rivets
Solid rivets are the oldest form of rivets, and have been used on ships and large steel structures like bridges. A solid rivet consists of a shank and a head. The head can be rounded, conical, countersunk, flat, or oval. To install, solid rivets are placed into a pre-drilled hole, then a hammer or a rivet gun is used to permanently deform the straight end into the required head shape.
In some cases, the rivet is softened by heating it until it’s red hot, which aids the deformation process. During deformation, the shank expands to fill any clearance in the drilled hole, then forms a second head to clamp the two materials firmly together. This type of rivet is robust and is used in critical applications such as vehicle bodies or structural members.
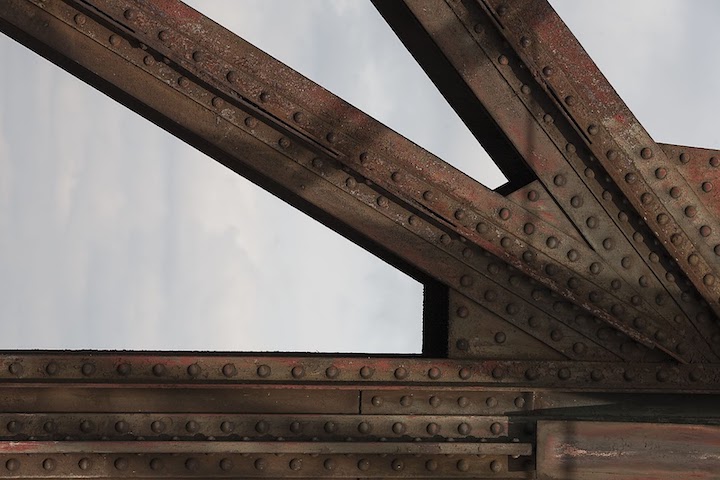
Solid Rivets
Pro-Tip: Check out our Press Fit Calculator to determine how tight your rivets should be in your assembly (not all rivets should be press fits, some should be tight fits depending on your application).
Tubular Rivets
Tubular rivets are similar in form to solid rivets; however, on the straight side of the rivet, there is a hole that travels a short distance into the shaft. Tubular rivets are designed to be easier to install when compared to solid rivets because less force is required to deform them. This is because only the thin walls of the hole must be flared outwards to secure the joint. Tubular rivets are used in applications such as HVAC ducting and other low-risk applications due to their thinner walls.
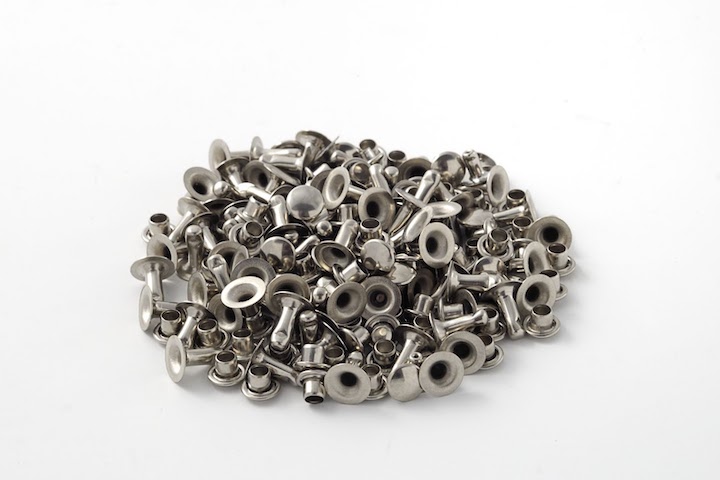
Tubular Rivets
Drive Rivets
A drive rivet is a type of blind rivet that consists of a short shank and a protrusion on the head of the rivet. Once the rivet is placed into a pre-drilled hole, the protrusion is driven with a hammer. This action causes deforms the shank outwards, clamping the joint. Installation of a drive rivet does not need a special riveting tool like a standard blind rivet. Drive rivets are typically used in commercial sheet metal fabrication.
Split Rivets
A split rivet is a light-duty rivet whose shaft is split into two separate legs. The rivet is installed into a pre-drilled hole, then the two legs are separated and flattened with a hammer against the rear component. Split rivets are often used on plastics, textiles, and thin metal sheets — they are is not as robust as blind rivets.
Self-Piercing Rivets
Self-piercing rivets are unique for two reasons: first, they need no pre-drilled holes, and second, the rivet does not pass completely through the second plate. To install a self-piercing rivet, two plates are placed into a press in which the rivet is held in a blank holder and pressed into the top sheet. The rivet then pierces into the second sheet without passing all the way through — a die on the rear side helps prevent the rivet from passing through — and an embossed section is produced on the rear plate.
This is a high-speed process that creates a robust connection, however, access to both sides is required. Self-piercing rivets can provide a watertight connection and are sometimes used in the aerospace industry.
Advantages of Using Rivets
Rivets are a widely used fastener due to a range of advantages:
- Simple Installation: Most rivets are quick and easy to install. For example, a blind rivet can be installed in a few seconds if a pneumatic tool is used.
- Accessibility: Access to one side of the joint is enough for rivet installation. Most other types of joining methods require access to the faying surfaces, or access to both sides of the joint.
- Low Cost: Rivets are a low-cost alternative to bolted connections, especially if the joint must be permanently fastened.
- High Strength: Solid rivets provide one of the most robust connections available and can last many years without significantly loosening due to their resistance to vibration.
Disadvantages of Using Rivets
Despite their advantages, rivets are not always the best option. Below are some common disadvantages:
- Permanence: Rivets are designed to be permanent fasteners, which isn’t ideal if an assembly ever needs to be disassembled. As such, rivets are typically used for permanent installations like bridges or aircraft body panels.
- Inferior to welding: If a permanent joint is required, welding offers a more robust connection while also being cheaper and more lightweight. Welds do not typically reduce the strength of the base parts the way rivets do — rivets require placing holes in the base material, which reduces the cross-sectional area that must bear the stress for the application.
- Not Leak Proof: Most rivets – apart from hot rivets or self-piercing rivets – do not provide a watertight connection. As such, additional costs and effort are required to create a watertight seal for riveted joints.
Fictiv – Complex Parts at Ridiculous Speeds
Whatever kind of components you need to join via rivets (or other methods), Fictiv is here to help you manufacture them, whether with CNC machining, injection molding, 3D printing, or urethane casting. We deliver 95.4% of orders on-time and to-spec, thanks to our network of highly-vetted partners, on-site quality engineers, and robust quality management system. Our AI-Powered DFM feedback and instant pricing (even for 2D drawings) makes it simple to get complex parts delivered fast. So, create an account and get started with Fictiv today!