Time to read: 5 min
Over the past few decades, there has been a steady increase in manufacturing demand, but simultaneously, there’s been a drop in the number of machinists entering the market. This shortage is hindering the growth of many businesses that have plenty of demand but simply cannot find the right people to drive growth on the manufacturing floor.
There are many strategies to help your company attract machinists, such as offering increased rates, better work-life balance, and other perks like relocation assistance. However, at this point, these benefits are commonly offered, so it’s time to consider new strategies.
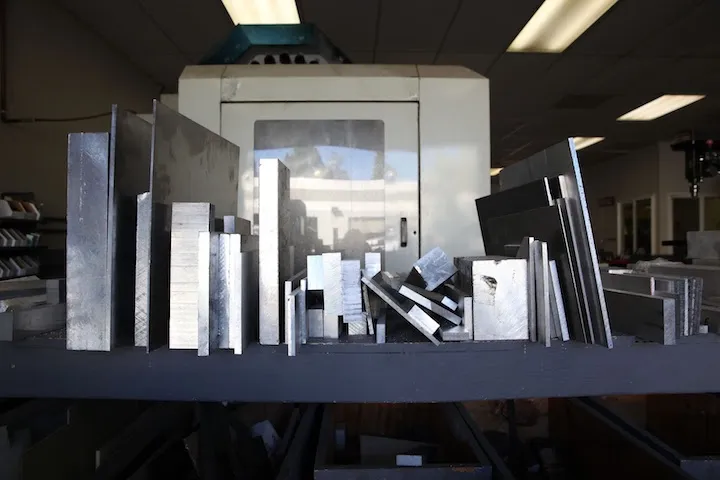
Combating the Machinist Shortage in 2023
With the demand for manufacturing only increasing, attracting new machinists and optimizing existing processes are critical to ensure your company stays competitive. Here are five methods to help your company overcome the machinist shortage in 2023:
Automation & Optimization
Automated systems are far from being capable of completely replacing machinists. Modern machinists still must program CNC machines, select the correct tools, spot potential challenges, and perform problem-solving tasks as they arise during normal machining activities. However, automated systems can be a force multiplier for existing machinists that significantly increases their productivity. Examples of physical automation can include ATCs (Automatic Tool Changers) and automated machine tending using robotic arms.
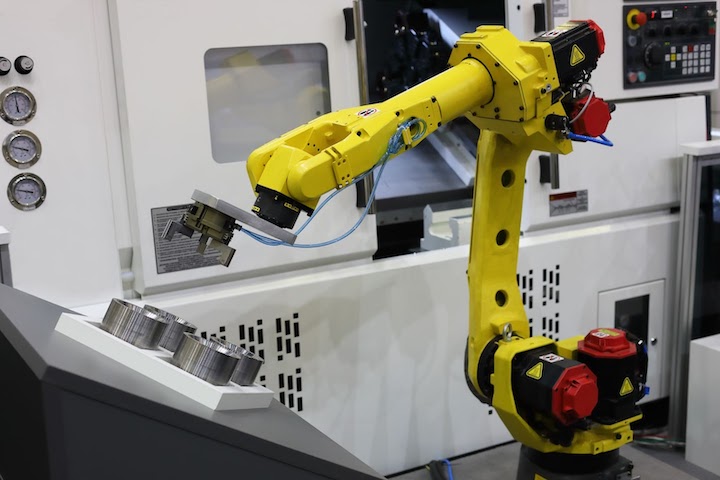
In terms of optimization, there are many potential interventions that can increase overall productivity. One example is the software used by machinists. Much of a machinist’s time is spent setting up programs for the machines to run. These programs are complex and require a thorough understanding of how to machine different materials, which tools to use, and how to set up a part to achieve the highest possible machining efficiency. However, newer software systems incorporate much of this knowledge into their systems, so machinists can spend less time setting up the program.
As far as attracting the top talent goes, showcasing your repertoire of technological advancements goes a long way in recruiting. Machinists geek out on new tech, and upgrading to newer systems will make your current machinists happy and more productive. Using automation to improve the productivity of existing machinists can give you time to find long-term solutions to increase your machining workforce.
Internships & Apprenticeships
Internships and apprenticeships are common methods of finding potential candidates and filling gaps within a manufacturing environment. While an apprentice or an intern won’t have the required skills to hit the ground running on their own, as long as they have a solid understanding of the fundamentals of machining, they just need general supervision by more experienced machinists. As such, they can assist your machinists with simpler and repetitive tasks while learning more complex tasks.
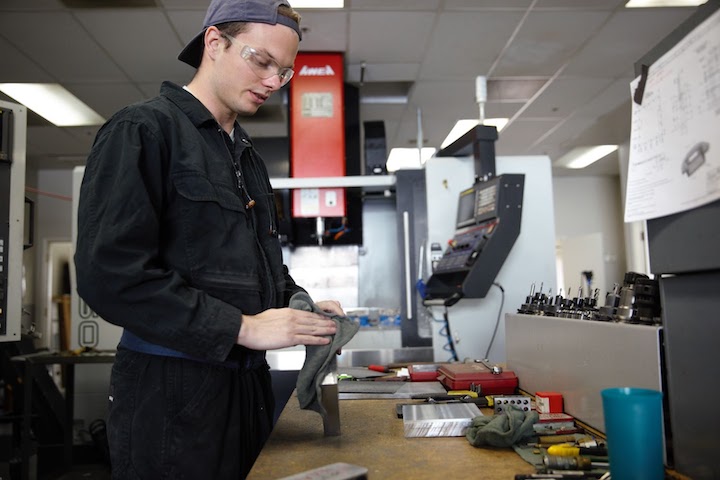
Engaging with local trade schools is a good way to find potential interns or apprentices that are looking for work and have basic machining knowledge. So, attend job fairs, post on trade school job boards, or even go speak to a class — get creative! Interns aren’t a permanent solution, but when they have completed their studies you can offer them employment in an environment they already know. And internships provide valuable experience for up-and-coming machinists while giving them an inside look into your company before committing to a full-time position.
Reskilling Existing Employees
Another option for increasing your machinist workforce is to re-skill existing employees. Some employees may want to move from other departments into production, and training them up can help plug gaps. Plus existing employees already know how the company’s policies and procedures work and are a known culture fit.
Ideally, the employees that move are from a position that is easier to fill than a machinist or machinist assistant. However, training a machinist from scratch is a lengthy process and requires a deep understanding of a broad range of topics. Also, the person may need some formal training, which will not only cost money but also remove that person from the floor for a while. However, a reskilling program increases employee retention and provides a long term solution to the machinist shortage.
Build an Online Presence
One of the most creative methods for recruiting machinists is to build a strong online presence. There are many groups of machinists who have created a strong following online — one of my favorites is Titans of CNC. Many of these influencers are from fully-fledged manufacturing companies that have social-media departments. The key is to find clever ways to show your company’s daily work without giving away any potential IP (intellectual property), and you can also create unique projects to market.
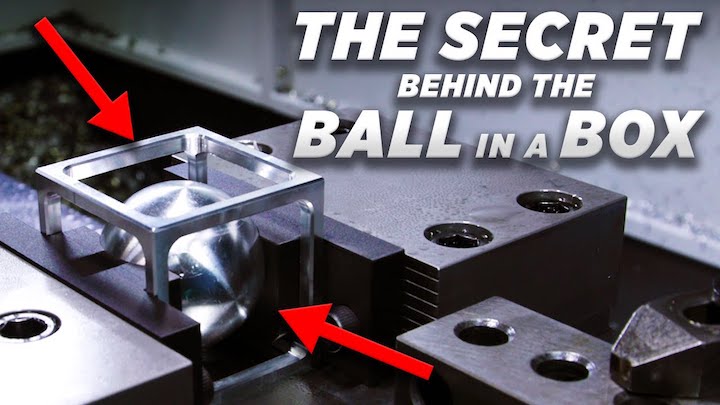
Many companies find an audience on YouTube or Instagram, but in order to optimize your online presence, you’ll need a dedicated, social media expert — not only to make content that looks professional, but also to tweak and promote the content so it reaches your target market.
When done well, social media improves your brand awareness and attracts potential machinists by showcasing the quality work your company is doing on a day-to-day basis. Make good enough content and you might even have skilled machinists reach out to you for a job!
Incorporate Cutting-Edge Technology
Machinists like to work on cutting-edge equipment, so it’s a good idea to incorporate cutting-edge machining equipment into your workflows. While this tech and the training required are expensive, not only will it attract experienced machinists who want to grow their skills, but it will also improve machining speed, productivity, and overall part quality — which can offset the initial capital investment over time.
Will Machinists Be Replaced by Robots?
You may think that, in a few years, machinists will no longer be needed because of the progress being made within the automation sphere. However, most of the easily automated machinist tasks have already been automated by CNC tending robots — and there is still a machinist shortage. This is because machining is a complex task that requires a breadth of knowledge that cannot be programmed into a simple robot arm. For the foreseeable future, machinists will simply integrate more robots into their workflow to increase productivity and keep pace with ever-increasing manufacturing demand.
How Important Is a Machinist?
Machinists are required to program tool paths, set up equipment, and operate CNC mills, turning centers, and lathes. Without a machinist, it would be impossible for a layperson to operate these expensive machines, so machinists are absolutely critical – they’re the only people who can turn a CAD model into a finished part.
The machinist shortage in 2023 doesn’t show any signs of improvement in the short term and, while the strategies in this article can work, they require time and investment that you may not have. That’s why Fictiv is here to plug your gaps in production and help you stay competitive in the market.
Fictiv is your operating system for custom CNC machined mechanical parts. Our expert engineers and machinists ensure you get quality components no matter how complex your designs. So, create an account and upload your design today to see what our instant, CNC machining quote process, DFM feedback, and intelligent platform can do for you — we deliver complex parts at ridiculous speeds!