Time to read: 6 min
How do you know if your manufacturing strategy is holding you back? Unexpected delays, rising costs, difficulty scaling up production, supply chain disruptions, and lack of innovation are red flags that your manufacturing strategy needs an overhaul. With the challenges and competition in product development and manufacturing today, staying ahead of the game is more important than ever.
By embracing digital manufacturing platforms like Fictiv, businesses can streamline production, cut costs, and stay agile in a volatile market.
Here are five common warning signs that it’s time to update your manufacturing strategy.
1. Production Lead Times Are Too Long
If your business is constantly dealing with production delays that cause missed deadlines and slow time-to-market, it’s a clear sign that your lead times are too long. This often happens when companies rely on rigid supply chains dependent on limited in-house capacity or overseas suppliers. Although, this is not the only reason for long lead times–every project phase can cause delays. Here are some common culprits:
- Inefficient RFQ (request for quote) processes: Response times are too slow and deadlines are missed.
- No clear lines of responsibility for who is managing a project.
- Lack of clear understanding of project requirements.
- The design process is too slow.
- Testing and verification are too slow.
- Too many design iterations are needed.
- Ineffective response to customer change requests.
- Problems with materials and MFG machine suppliers.
- Quality problems due to one of the previous elements.
On-demand digital manufacturing platforms like Fictiv help shorten your lead times from weeks to days. With AI-powered instant quoting and real-time design for manufacturability (DFM) feedback, businesses can speed up decision-making and get their products to market faster.
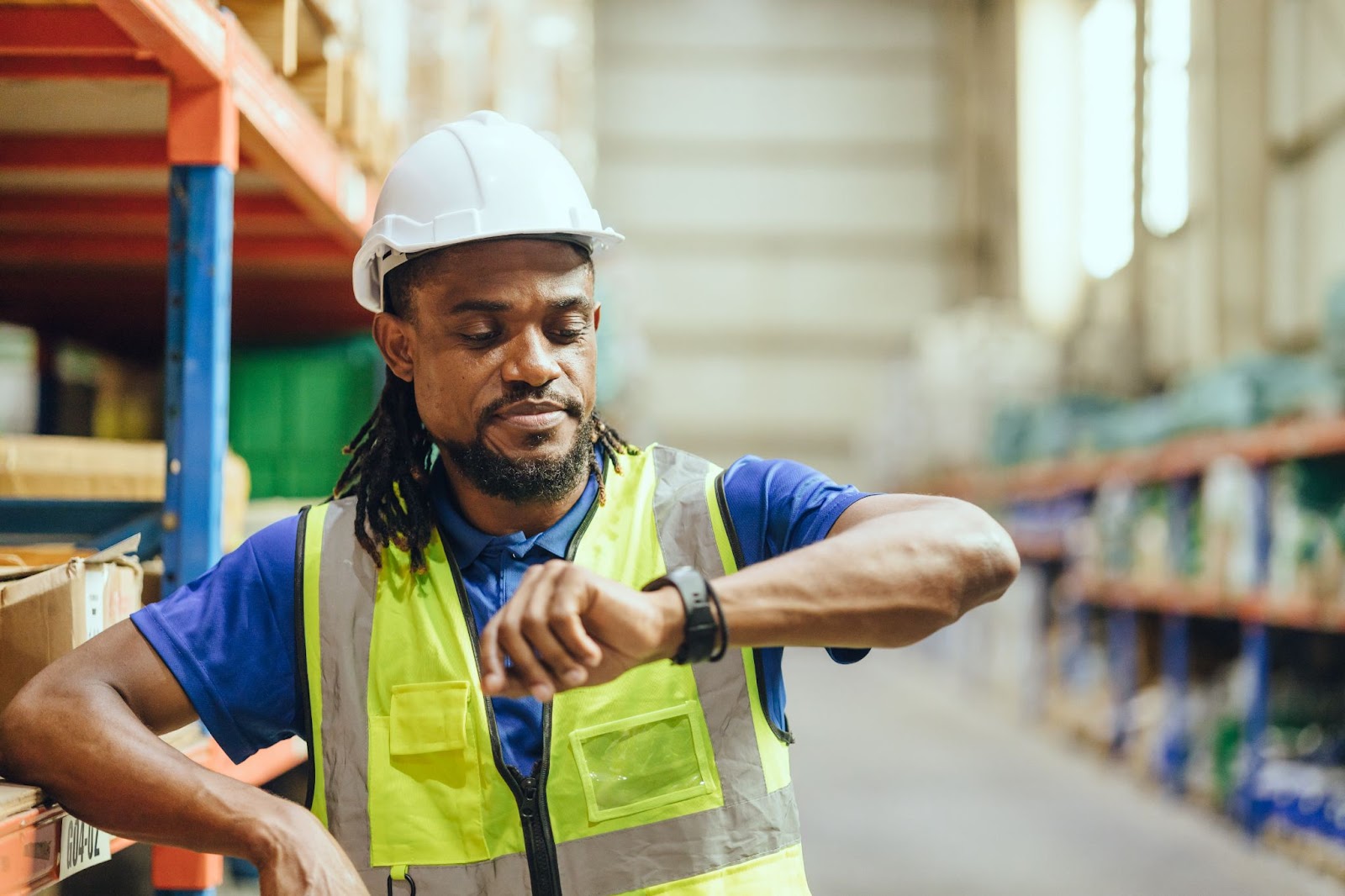
2. Manufacturing Costs Keep Rising
Another sign to look out for is rising material, labor, and operational costs cutting into your profit margins. This is a common problem for companies that use outdated production methods, often resulting in high waste and inefficiency.
Underutilized equipment and workers can also lead to unnecessary expenses and make it harder to maintain profitability. In many cases, it’s not that employees aren’t working hard, it’s because they’re working on the wrong things. This could be due to inefficient workflows, poor planning, and misaligned priorities. Machines also sit idle because production schedules aren’t optimized due to a lack of coordination between design, procurement, and manufacturing teams. At the same time, outdated methods often result in high material waste and rework, driving up costs even further.
A great solution that can significantly reduce overhead costs is to move towards a digital manufacturing platform, a hub that connects you to a global network of vetted manufacturers. The platform acts as a command center, managing everything from design and quoting to production and delivery. It matches your specific requirements—whether CNC machining, injection molding, or 3D printing—with the best-suited manufacturer results. It also allows you to scale production up or down as needed, without the burden of maintaining underutilized equipment or overstaffed teams.
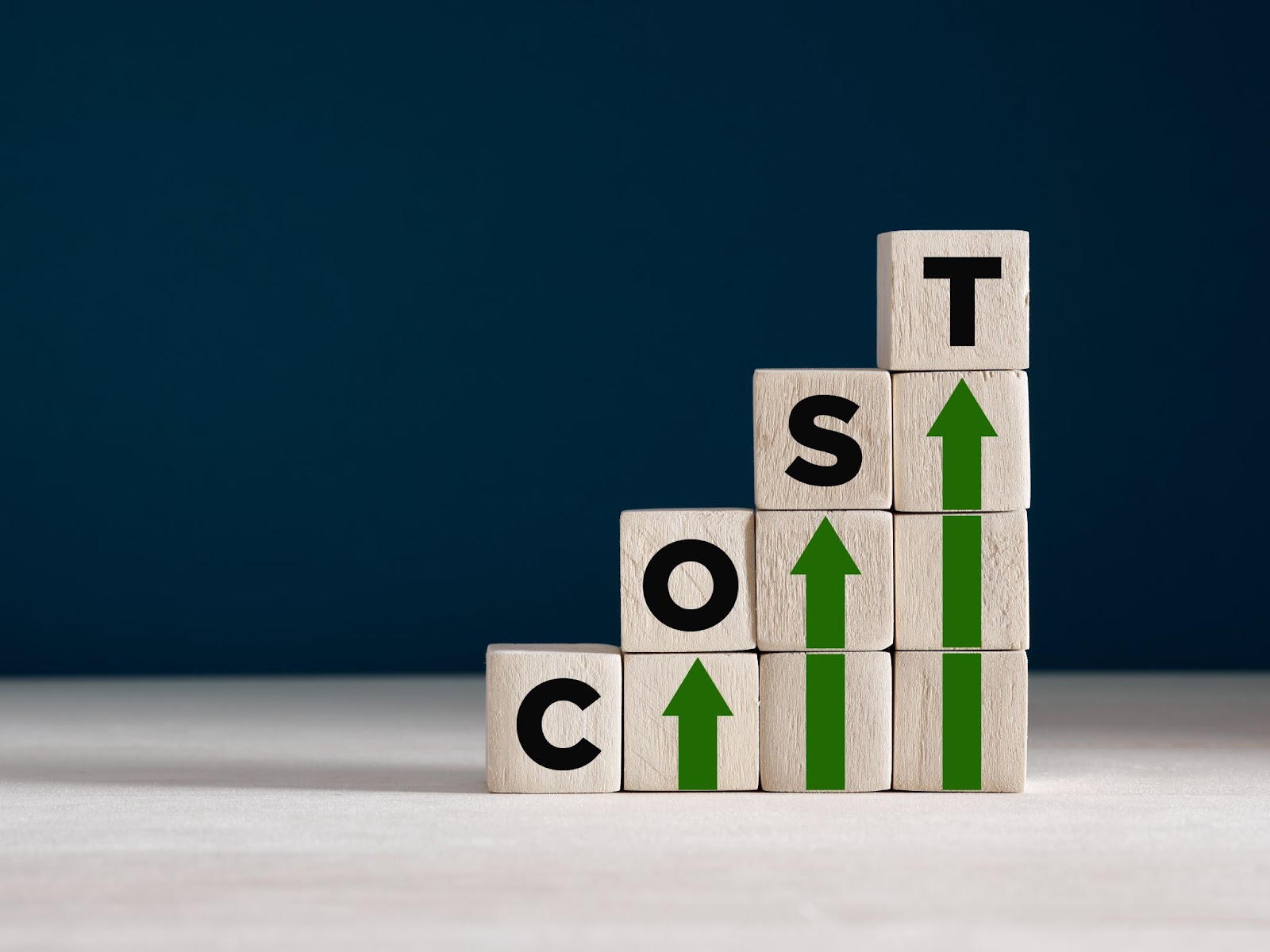
3. Scaling Up Production Is Nearly Impossible
Problems scaling up to production can be caused by everything from limited machine capacity to workforce shortages to an inadequate supplier network. For example, if your in-house facilities or primary suppliers are maxed out, you may struggle to ramp up production quickly.
Other scaling issues could also arise, such as situations where you need to increase output from Production Volume A to Production Volume B. If your current setup can’t handle the surge, you risk losing customers to competitors who can meet their needs faster.
Fictiv connects you with a global network of vetted, build-to-print manufacturers who can step in to meet sudden spikes in demand or scale your prototype into full production. Whether you need CNC machining, injection molding, or 3D printing, Fictiv’s on-demand model ensures you have the flexibility to scale up—or down—as needed, without overextending your resources. Log in to your account to get started on a quote today!
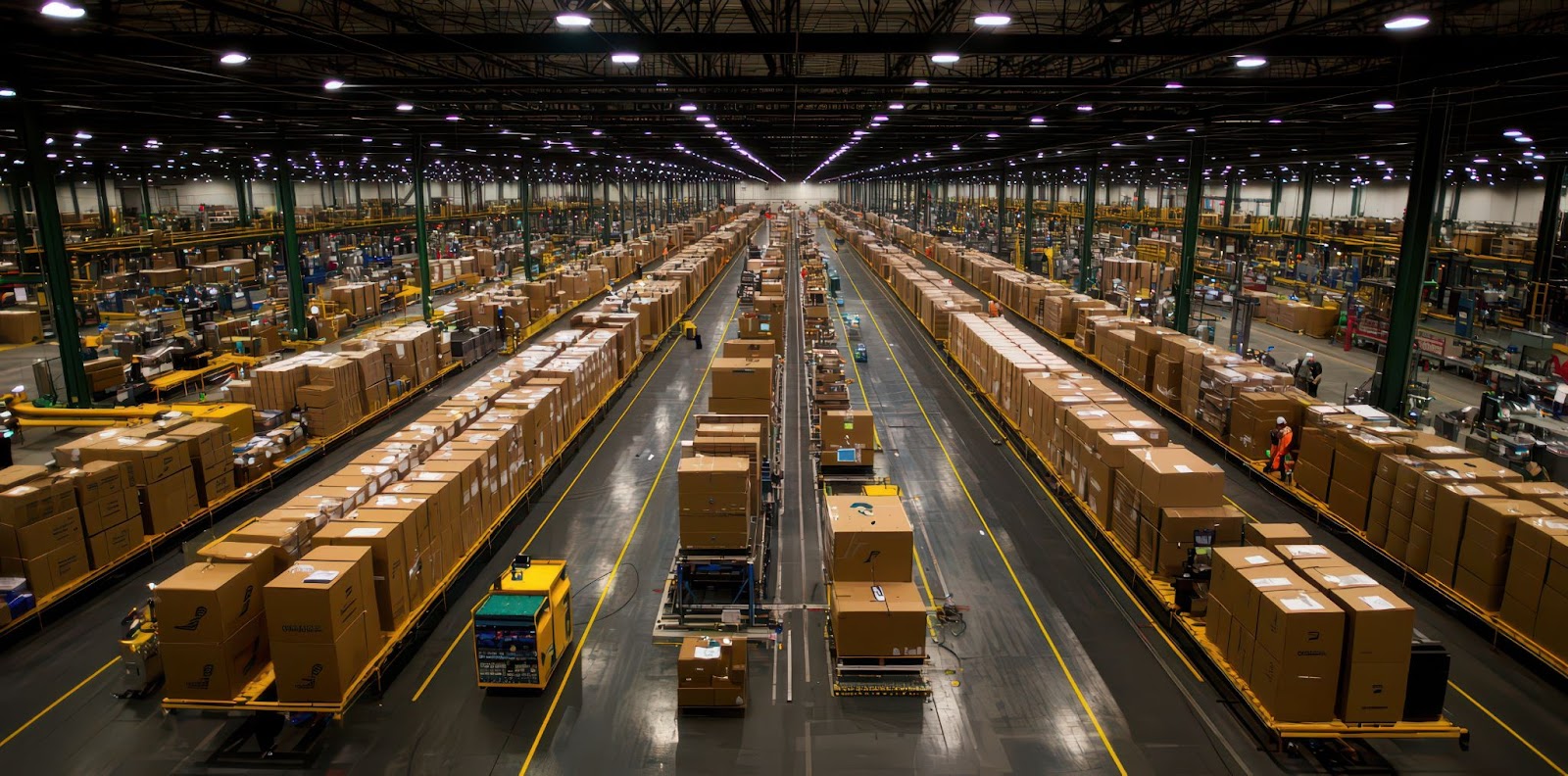
4. Supply Chain Disruptions
If supplier delays, raw materials shortages, or logistics issues are disrupting your production schedule, it’s time to address your supply chain. Supply chain disruptions are usually unpredictable and can be caused by anything from adverse weather conditions to geopolitical conflicts. Without real-time visibility into your supply chain, it’s nearly impossible to anticipate and mitigate these risks.
So how can companies reduce supply chain risks? Since supply chain issues usually arise due to a single-source or overseas supplier, they can be addressed by implementing a distributed supply network. This means having backup options and regionalized production capabilities, so you’re never left stranded when problems arise.
Fictiv addresses possible supply chain disruptions through a distributed manufacturing network that provides redundancy and regional production options. If one supplier faces delays— due to weather, geopolitical issues, or other disruptions—you can quickly shift production to another partner in the network. This ensures your production stays on track, even when unexpected challenges arise.
Additionally, Fictiv’s digital tracking and logistics management tools give you real-time visibility into your supply chain. You can monitor production progress, track shipments, and anticipate potential risks—all from a single platform. This transparency allows you to make informed decisions and respond quickly to disruptions, minimizing downtime and keeping your customers happy.
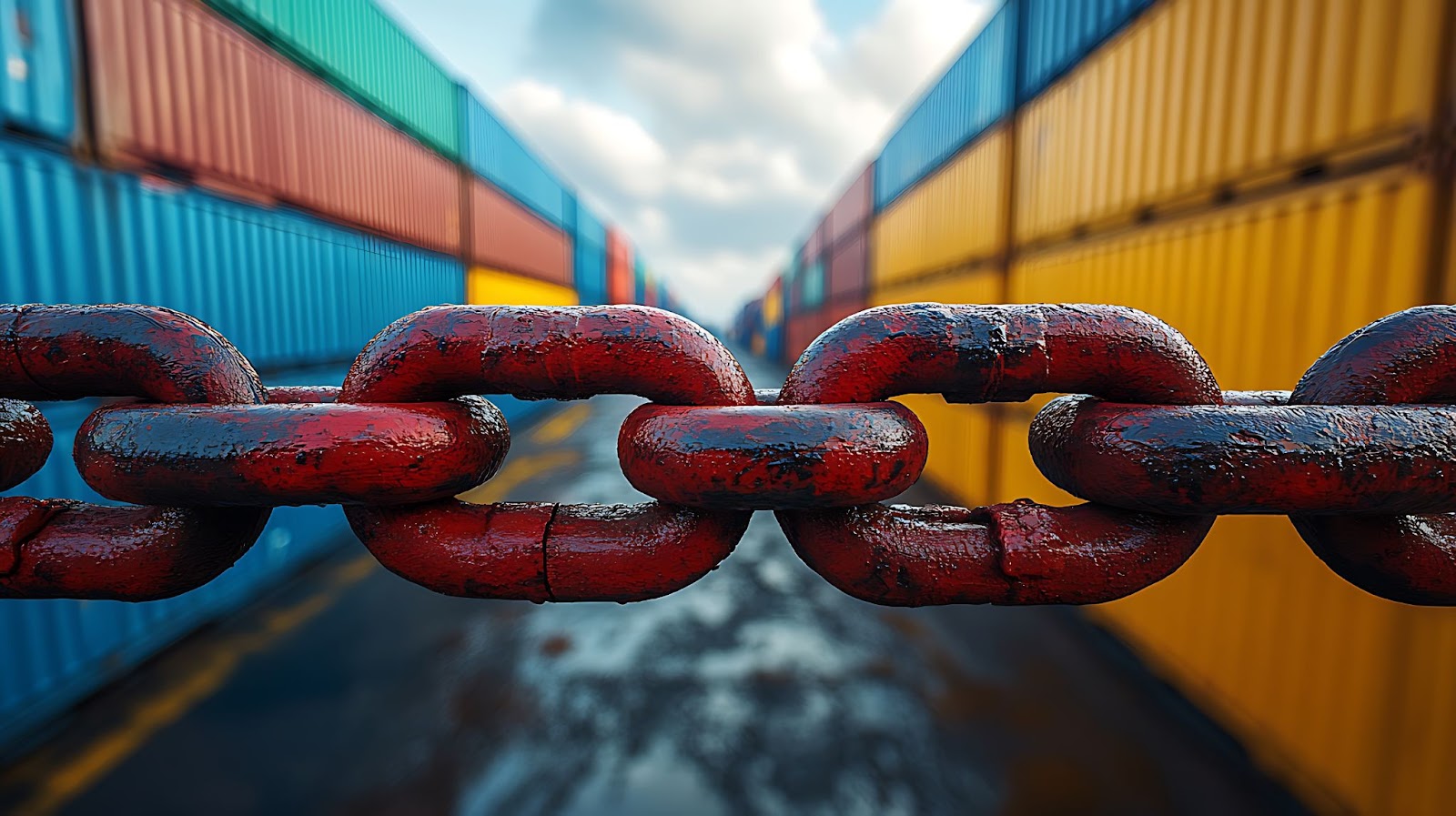
5. Your Product Innovation Cycles Are Slowing Down
Many companies struggle with sluggish innovation cycles, as delays in prototyping and design iteration slow down the entire product development timeline. This can be a big issue in industries where speed-to-market can make or break your competitive edge, such as in the consumer electronic industry.
This happens because traditional manufacturing workflows are often slow and rigid. Sometimes, it’s difficult to implement innovative design changes because certain manufacturing processes, such as injection molding, rely on expensive tooling that is time-consuming to change. For example, creating a new mold for a redesigned product component can take weeks and cost thousands of dollars.
This discourages frequent design changes and can force a design team to stick with suboptimal designs rather than introducing improvements, even as the need for them becomes clear. Even a prototype of a new design can sometimes take weeks, or even months, depending on supplier availability and shipping times. Depending on the industry and product, market demands may even have shifted by the time you receive a prototype.
To address this, Fictiv offers rapid prototyping services, including 3D printing, CNC machining, and urethane casting. These technologies allow you to turn your ideas into prototypes in days instead of weeks.
3D printing allows limitless design iteration by simply updating the underlying CAD model and printing the new design. It’s a quick, cost-effective way to test and refine product ideas.
CNC machining can be used to provide high-precision parts that closely mimic final production components, to give companies an idea of how their product will perform in the real world.
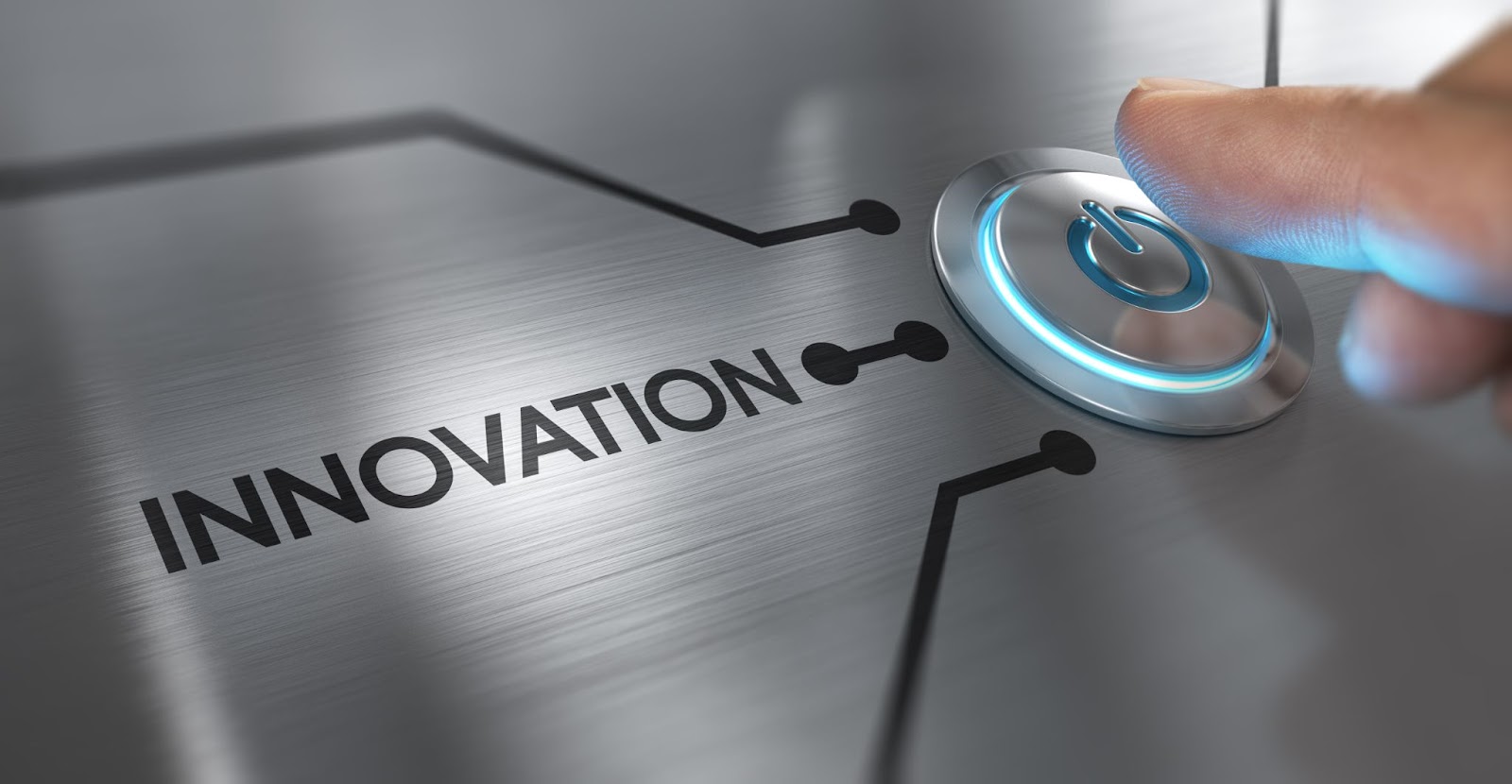
Fictiv is a digital manufacturing platform designed to modernize and streamline production processes. Here’s how Fictiv can help you upgrade your manufacturing strategy:
- Instant Quoting & DFM Feedback: Get real-time quotes and DFM feedback to optimize designs and reduce errors before production begins.
- Flexible, On-Demand Manufacturing: It’s easy to scale production up or down effortlessly with access to technologies like CNC machining, injection molding, and 3D printing—all through a single platform.
- Global Network of Vetted Suppliers: We make use of a rigorously vetted network of manufacturers with regional options to minimize lead times.
- Cloud-Based Order Management: We offer our clients full visibility and control over workflows with a centralized platform for tracking production, managing logistics, and ensuring transparency.
- Rapid Prototyping: Our fast-turnaround prototyping service enables quicker design iterations and faster time-to-market.
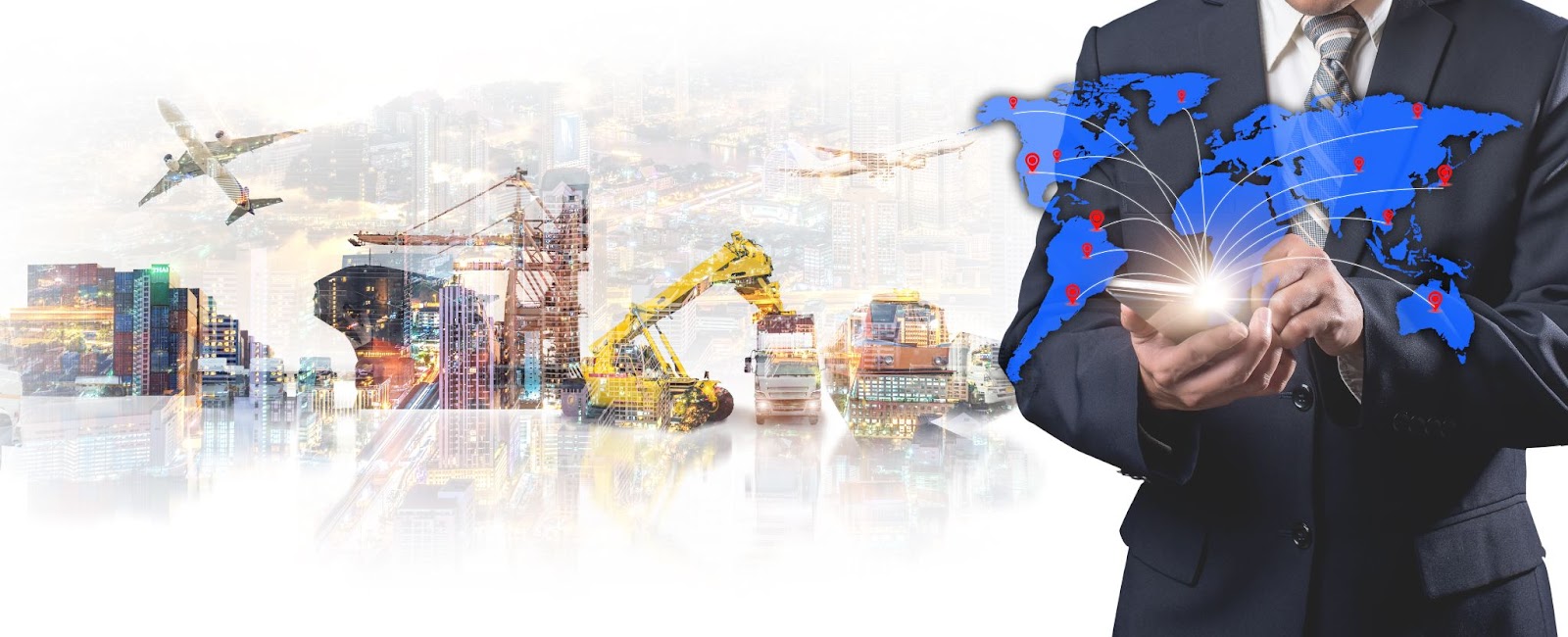
Is It Time To Upgrade Your Manufacturing Strategy?
If your company is experiencing any of these five warning signs–long lead times, high costs, sluggish innovation cycles, problems scaling to production, or supply chain disruptions–it’s a clear sign that your manufacturing strategy needs an upgrade. Outdated processes and rigid systems can hold you back, leading to vulnerability and missed opportunities.
Digital manufacturing platforms like Fictiv use AI in manufacturing to offer an effective modern solution, and provide the flexibility, speed, and cost savings needed to stay competitive in today’s fast-paced market. It’s possible to overcome manufacturing bottlenecks with our on-demand platform, real-time feedback, and global network of suppliers.
Don’t let outdated methods slow you down. Get a quote today and transform your manufacturing strategy with Fictiv.