Time to read: 7 min
Are you ready to scale your design from prototyping to production quantities? If so, various bridge production methods can help you ramp up to higher volumes. You’ve likely heard of 3D printing for prototyping and injection molding for production, but you may not know about using the two together. 3D printing can provide on-demand tooling, particularly in mold production for low volumes.
Traditional mold-making methods, such as those used for injection molding and thermoforming, often come with higher upfront costs and extended lead times, making them less than ideal for small production runs or rapid prototyping. These methods are typically more expensive and require the creation of complex molds, which can take longer to fabricate.
By utilizing additive manufacturing for molds, 3D-printed tooling can be produced in a fraction of the time and cost it would take for traditional tooling. For low-volume production, this gives it a clear edge over traditional mold-making, which can be slower and more costly. As a result, manufacturers can now rapidly prototype, iterate designs, and bring products to market faster than ever–without the financial commitment of traditional tooling.
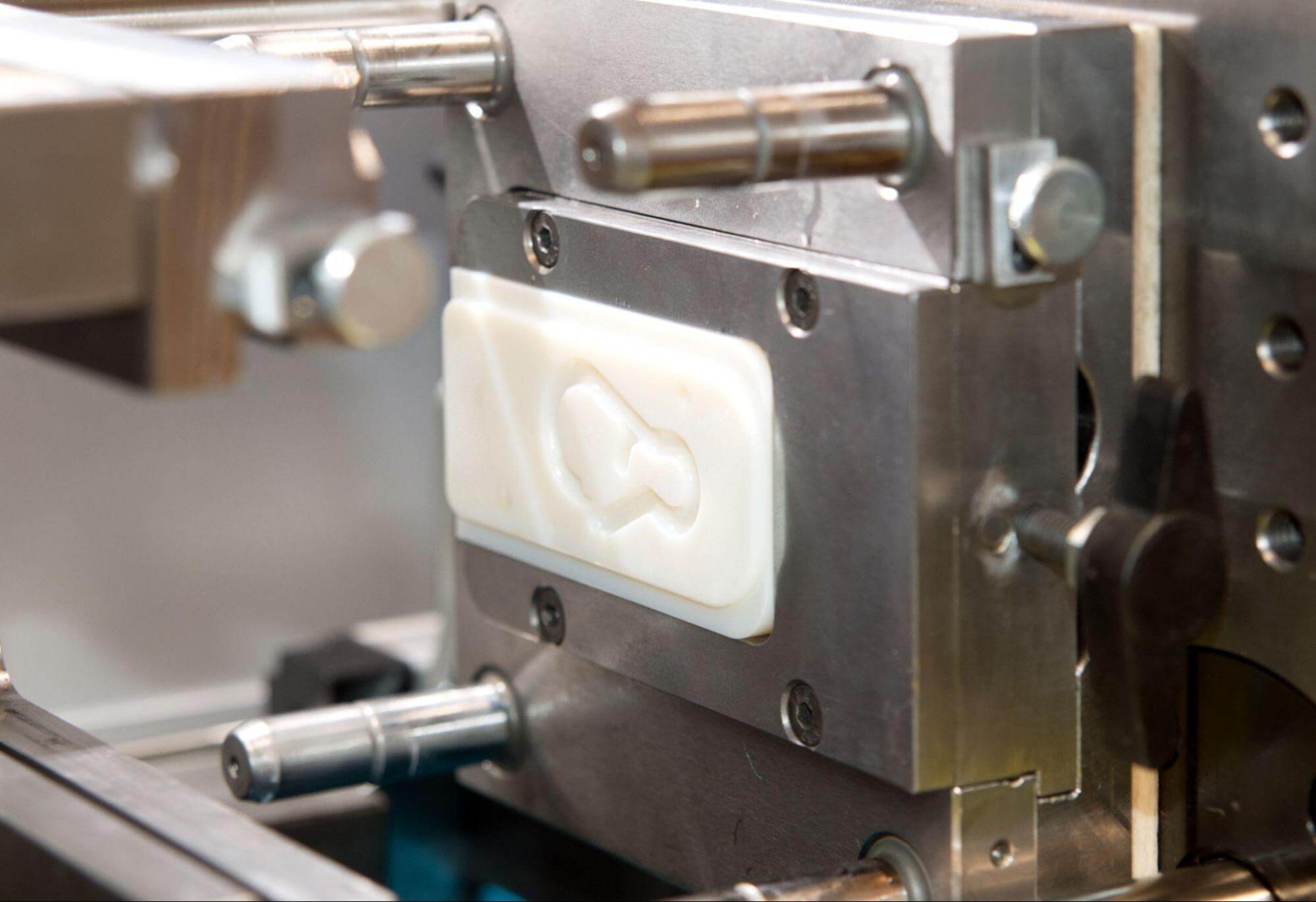
This article will highlight the advantages, limitations, best applications, and comparisons with traditional tooling while showcasing how digital manufacturing services like Fictiv can help companies implement 3D-printed mold solutions.
What Are 3D Printed Molds?
A 3D printed mold is a mold produced using additive manufacturing techniques, such as SLA (stereolithography), FDM (fused deposition modeling), SLS (selective laser sintering), or even metal 3D printing processes like DMLS (direct metal laser sintering).
Unlike traditional tooling, which relies on CNC machining or casting methods, 3D printed molds are created by precisely laying down material layer by layer, giving designers more flexibility in mold design and production.
Types of 3D Printed Molds
Different types of molds are suited for specific applications, and 3D printing provides the ability to manufacture molds for various production processes. Common types include:
Injection Molding Tooling (for Plastics):
3D-printed inserts provide a lower-cost, faster alternative to traditional steel molds. Ideal for short runs, prototyping, and low-volume production, they enable the creation of complex geometries with reduced lead times.
Urethane Casting Molds (for Flexible & Rigid Materials):
Used for producing flexible and rigid parts, these molds allow liquid urethane to cure within them. They offer a cost-effective solution for low-volume production and prototyping, supporting a wide range of material hardness levels.
Thermoforming Molds (for Packaging & Consumer Products):
Designed for shaping thermoplastic sheets, they are widely used for small-batch production of packaging, medical trays, and consumer goods. With quick turnaround times and cost efficiency, they are ideal for prototyping and low-volume manufacturing.
Mantle3D (Metal Inserts):
Uses paste deposition technology to add layers of metal paste that are then machined and hardened in a high-temperature furnace. This creates 3D-printed inserts that surpass the performance and durability of traditional 3D printing.
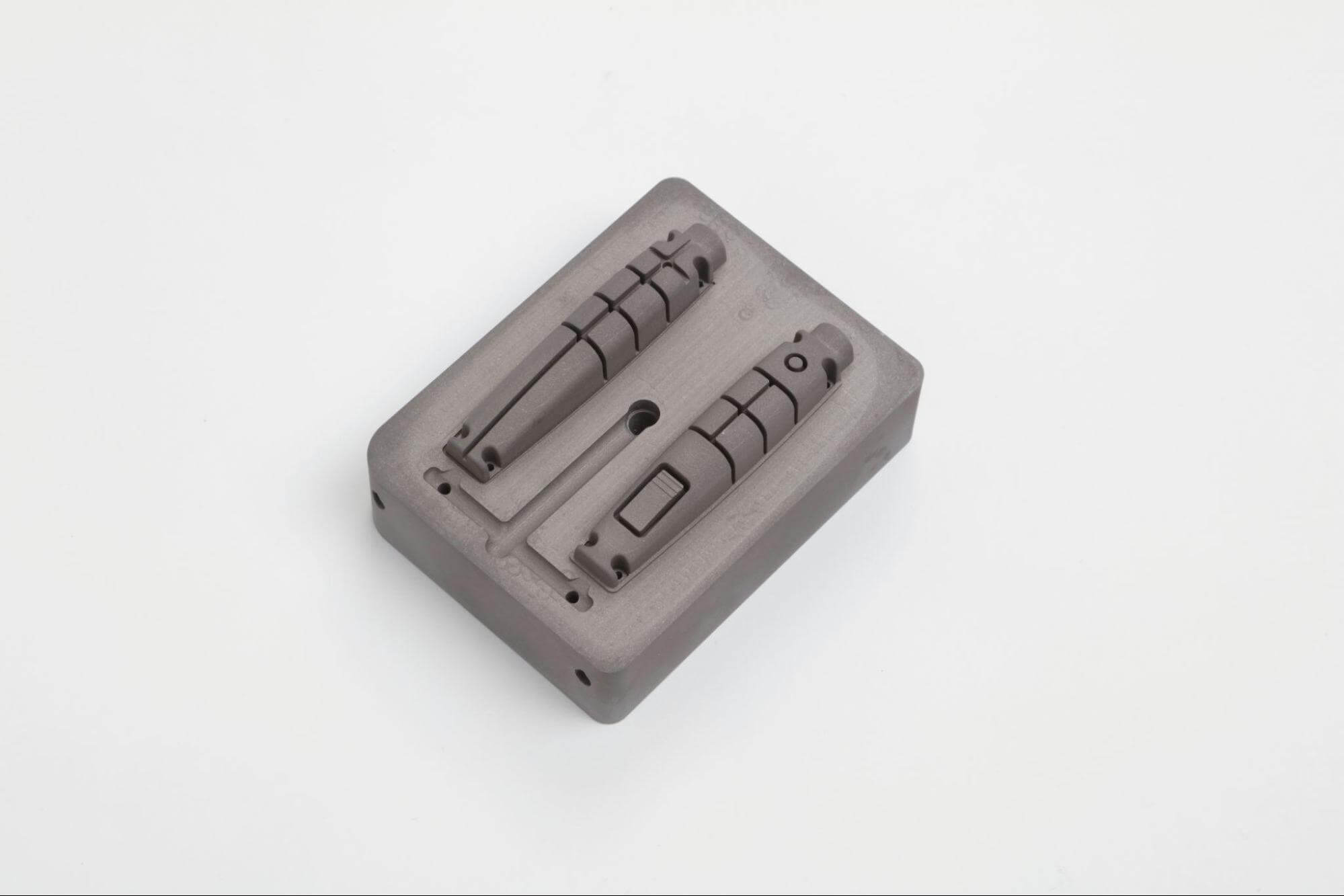
Materials Used in 3D Printed Molds
The materials used in 3D printing molds can vary greatly depending on the type of mold and the requirements of the production process. The most commonly used materials are:
Resin-Based Molds (SLA/DLP Printers):
Resin-based molds, made with SLA or DLP technologies, offer high detail, smooth finishes, and heat resistance. They are ideal for low-volume injection molding and urethane casting, where precision and durability are essential.
Polymer-Based Molds (SLS/FDM Printers):
Polymer-based molds, created using SLS or FDM, are cost-effective and ideal for low- to medium-volume production. While less heat-resistant than resin or metal molds, they offer material versatility, such as nylon and PLA, making them suitable for thermoforming and urethane casting.
Metal 3D Printed Molds (Mantle3D, DMLS/SLM Printers):
Metal molds, made with Mantle3D, DMLS or SLM, are durable and heat-resistant, ideal for high-temperature, high-volume production. They offer superior strength, wear resistance, and longevity, making them suitable for extended production runs.
3D Printed Molds vs. Traditional Injection Molding Methods
Table 1 shows the difference between 3D-printed molds vs. traditional mold-making methods:
Factor | 3D Printed Molds | Traditional Metal Molds |
Setup Costs | Low | High (tooling required) |
Lead Time | Days to weeks | Weeks to months |
Per-Unit Cost | Higher at high volumes | Low at high volumes |
Design Iteration | Easy, fast changes | More expensive, slower changes |
Durability | Good for short runs (10-1,000 shots) | Excellent for higher-volume production |
Best For | Prototyping, low-to-mid volume production | Low- to high-volume production (250-10,000+ shots |
Table 1: 3D printed vs. traditional mold-making methods
Advantages of 3D Printed Molds
The usage of 3D-printed molds has the following advantages:
- Faster Iteration & Design Changes: 3D printing allows designers to quickly modify and produce new mold designs in days rather than weeks. This rapid turnaround is especially beneficial for R&D teams that need to test multiple iterations before full-scale production.
- Lower Costs for Low-Volume Production: By eliminating the need for expensive CNC machining and traditional mold-making processes, 3D-printed molds significantly reduce costs. Additionally, they minimize material waste compared to subtractive manufacturing methods.
- On-Demand Production & Localized Manufacturing: Digital mold files can be shared and printed anywhere, eliminating the need to stockpile costly metal molds. This reduces supply chain risks and enables localized production.
- Hybrid Manufacturing Potential: 3D-printed mold inserts can be combined with CNC-machined mold bases, allowing manufacturers to test designs before committing to full-scale metal tooling. This approach offers greater flexibility and cost savings during development.
Limitations & Challenges of 3D Printed Molds
While 3D printed molds offer numerous advantages, there are also some limitations and challenges to consider:
- Limited Lifespan for High-Volume Runs: Polymer-based 3D-printed molds wear out faster than traditional steel molds, making them best suited for production runs of 10 to 1000 parts. This is a significant drawback for higher-volume manufacturing.
- Material & Heat Constraints: Some 3D printing materials may not withstand the high injection pressures or temperatures required for specific molding processes. However, advancements in high-performance resins and metal 3D printing technologies are gradually mitigating these limitations.
- Post-Processing & Surface Finish: These molds often require additional finishing steps, such as sanding, coating, or polishing, to achieve a smooth surface. Fine details may not be as precise as those produced with CNC machining, adding time and cost to the mold-making process.
Best Applications for 3D Printed Molds
Some of the best applications for 3D-printed molds include:
- Prototyping & Rapid Iteration: Ideal for testing designs before full-scale production. They enable quick iterations and refinements, reducing development time and costs.
- Short-Run & Custom Manufacturing: Perfect for small batches of niche or custom products, allowing manufacturers to respond swiftly to market demands and offer personalized products without high tooling costs.
- Low-Volume Injection Molding: Provides a cost-effective alternative to traditional metal molds, reducing both expenses and lead times for runs of 10–1,000 plastic parts.
- Medical, Aerospace, & Automotive Components: Enables quick design testing and refinement while minimizing material waste and costs in industries where rapid iteration and lightweighting are essential.
- Urethane Casting & Thermoforming: Widely used in urethane casting, where silicone molding is employed for flexible parts. They are also effective as vacuum-forming molds for creating packaging and consumer goods.
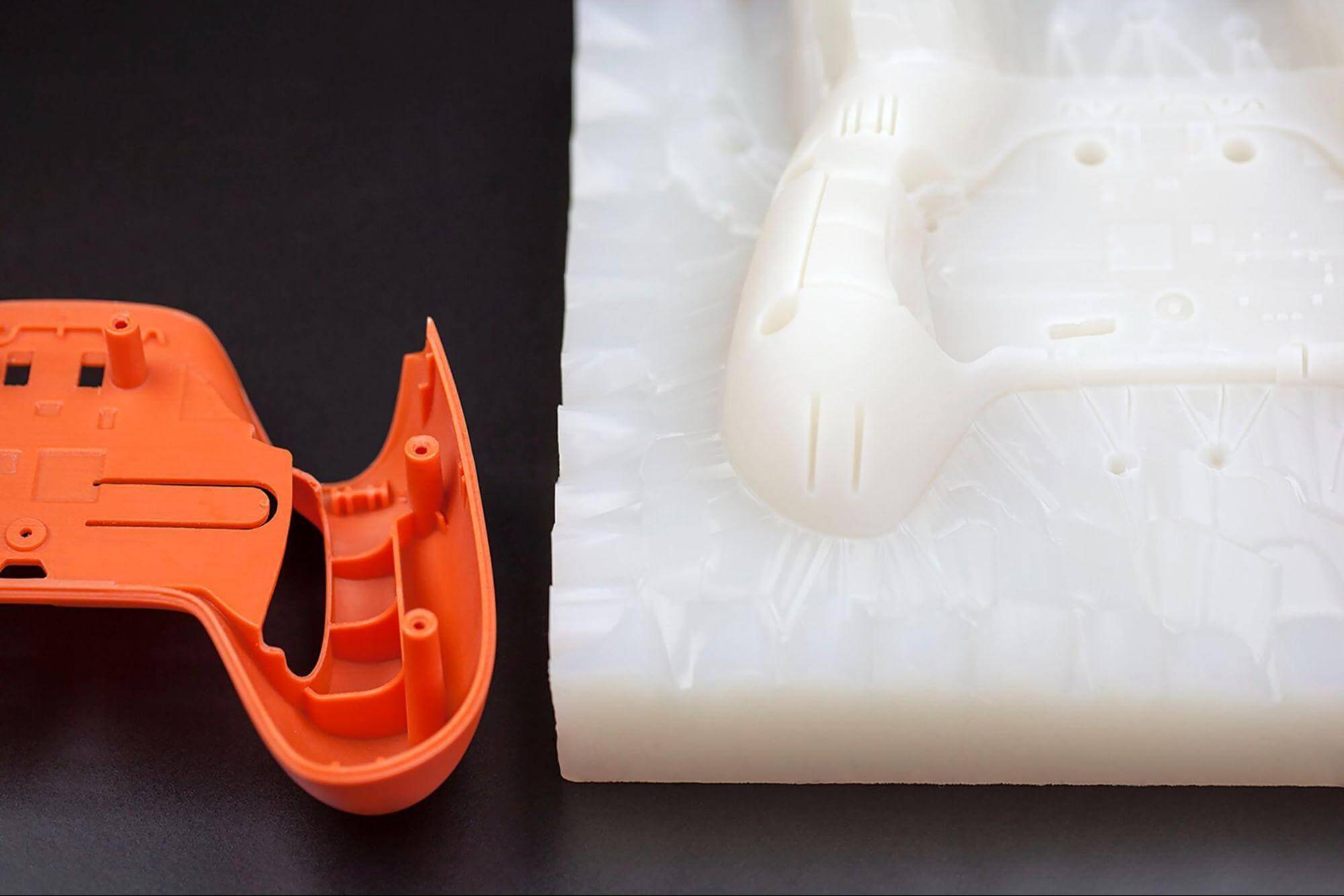
The Future of 3D Printed Molds & Digital Manufacturing
The future of 3D printed molds and digital manufacturing looks promising, with several key developments on the horizon:
- Advancements in High-Performance Materials: The development of heat-resistant SLA resins will enable these molds to withstand higher temperatures and pressures, increasing their durability and lifespan. Additionally, metal 3D-printed molds may be able to replace traditional steel molds for mid-volume production, offering improved performance and cost-effectiveness.
- Automated 3D Printing for On-Demand Tooling: AI-driven automated mold design and production will streamline the mold-making process, reducing lead times and costs. To further enhance supply chain flexibility, cloud-based digital tooling storage will enable remote manufacturing, allowing companies to produce molds anywhere in the world using a 3D printer.
- Hybrid Manufacturing with 3D Printed Inserts: Combining CNC-machined mold bases with 3D printed inserts will offer manufacturers greater flexibility in their production processes. This hybrid approach allows for rapid design changes and cost-effective low-volume production while maintaining the durability and precision of traditional metal molds.
Is 3D Printed Tooling Right for Your Business?
3D-printed tooling is well-suited for rapid iteration, prototyping, and low-to-mid-volume production. It allows companies to quickly test and refine designs, significantly reducing development time and costs compared to traditional metal molds.
While not a complete replacement for traditional metal tooling in all cases, this technology offers a fast and cost-effective alternative for specific applications. Businesses can efficiently produce small batches of parts without the high upfront investment typically required for conventional molds.
For those seeking flexible, on-demand manufacturing solutions, exploring additive manufacturing for mold production is a recommended option. It enables companies to adapt quickly to changing market demands and create customized products with shorter lead times.
Ultimately, the decision to adopt 3D-printed molds depends on factors such as production volume, design complexity, and material requirements. By carefully evaluating these aspects and consulting with experienced digital manufacturing providers like Fictiv, businesses can determine if this approach is the right fit for their needs.
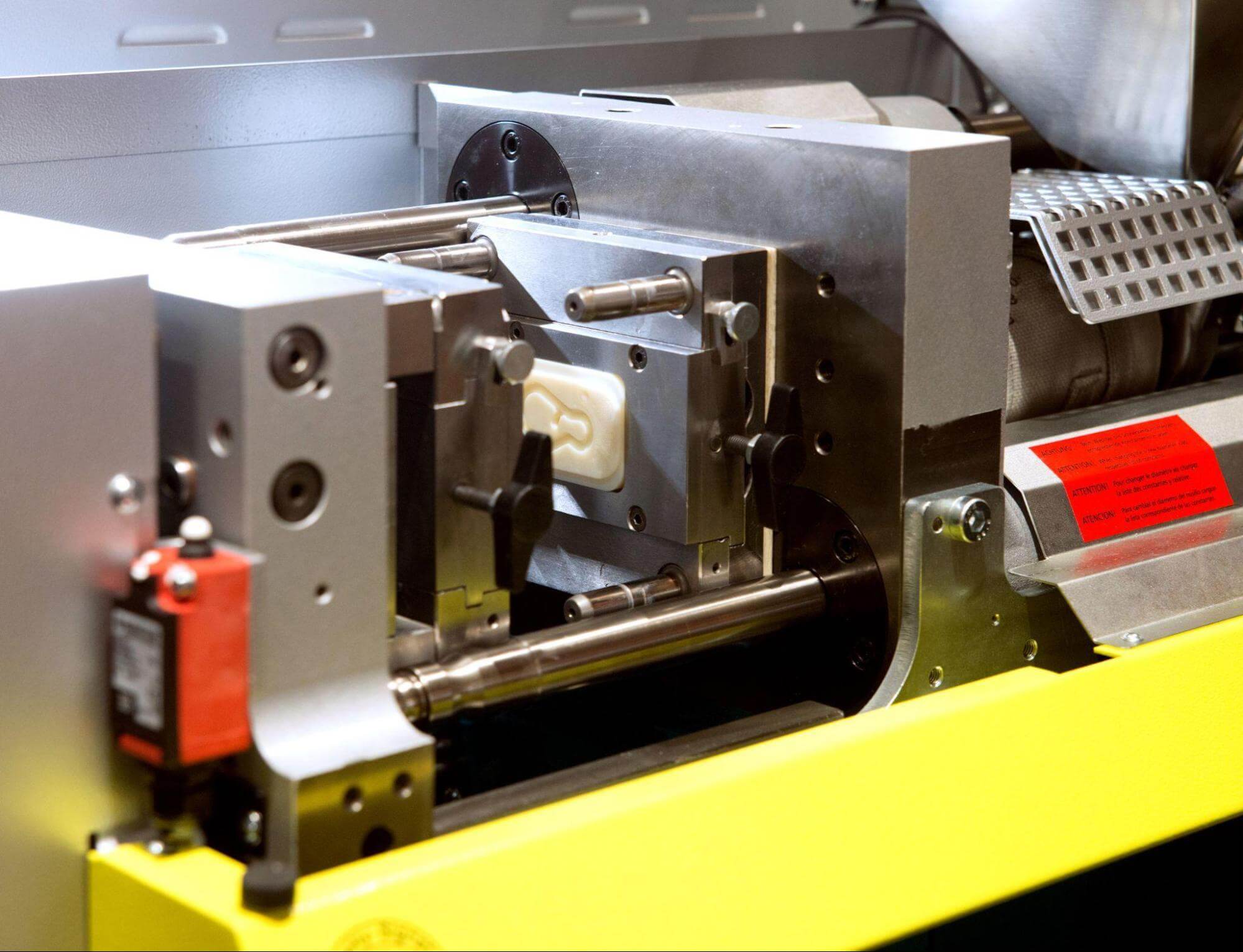
How Fictiv Helps With 3D Printed Molds & Low-Volume Manufacturing
Fictiv is a digital manufacturing platform that helps companies with 3D-printed molds and low-volume manufacturing in several ways:
- Access to Multiple Manufacturing Technologies: Fictiv provides access to various manufacturing technologies, including CNC machining, injection molding, urethane casting, and 3D printing. This allows companies to choose the most suitable method for their specific needs and requirements.
- Cost-Effective Production: By leveraging 3D-printed molds and other digital manufacturing techniques, Fictiv helps companies eliminate high upfront tooling costs associated with traditional manufacturing methods. This makes low-volume production more accessible and cost-effective.
- Fast Turnaround & Iteration: Fictiv enables companies to move quickly from prototype to production in a matter of days. This rapid turnaround allows for faster iteration and refinement of designs, reducing development time and costs.
- Global Network of Vetted Manufacturers: Fictiv’s platform connects companies with a global network of vetted manufacturers, enabling them to scale production as needed. This flexibility ensures that companies can meet demand without overinvesting in tooling or inventory.
Get an instant quote today and discover how Fictiv can help streamline your production process with bridge production solutions and support from our experts and global network of manufacturing partners.