Time to read: 10 min
Metal parts manufacturing is the process of shaping, cutting, and assembling metal materials into components used in countless industries. Its importance lies in its ability to produce durable, precise, and high-performance parts that meet the demanding requirements of modern technology and infrastructure.
This article reviews key metal parts manufacturing processes for everything from large-scale components down to small, intricate parts. We’ll cover CNC machining, casting, forging, metal injection molding, metal 3D printing, and sheet metal fabrication. It explains the advantages of each process, the materials used, and the factors to consider in choosing them.
CNC Machining for Precision Metal Parts
CNC (Computer Numerical Control) machining is a subtractive manufacturing process in which computer-controlled cutting tools remove material from a solid billet (block) to produce a finished part. This method is widely used in metal machining to create highly precise components with tight tolerances.
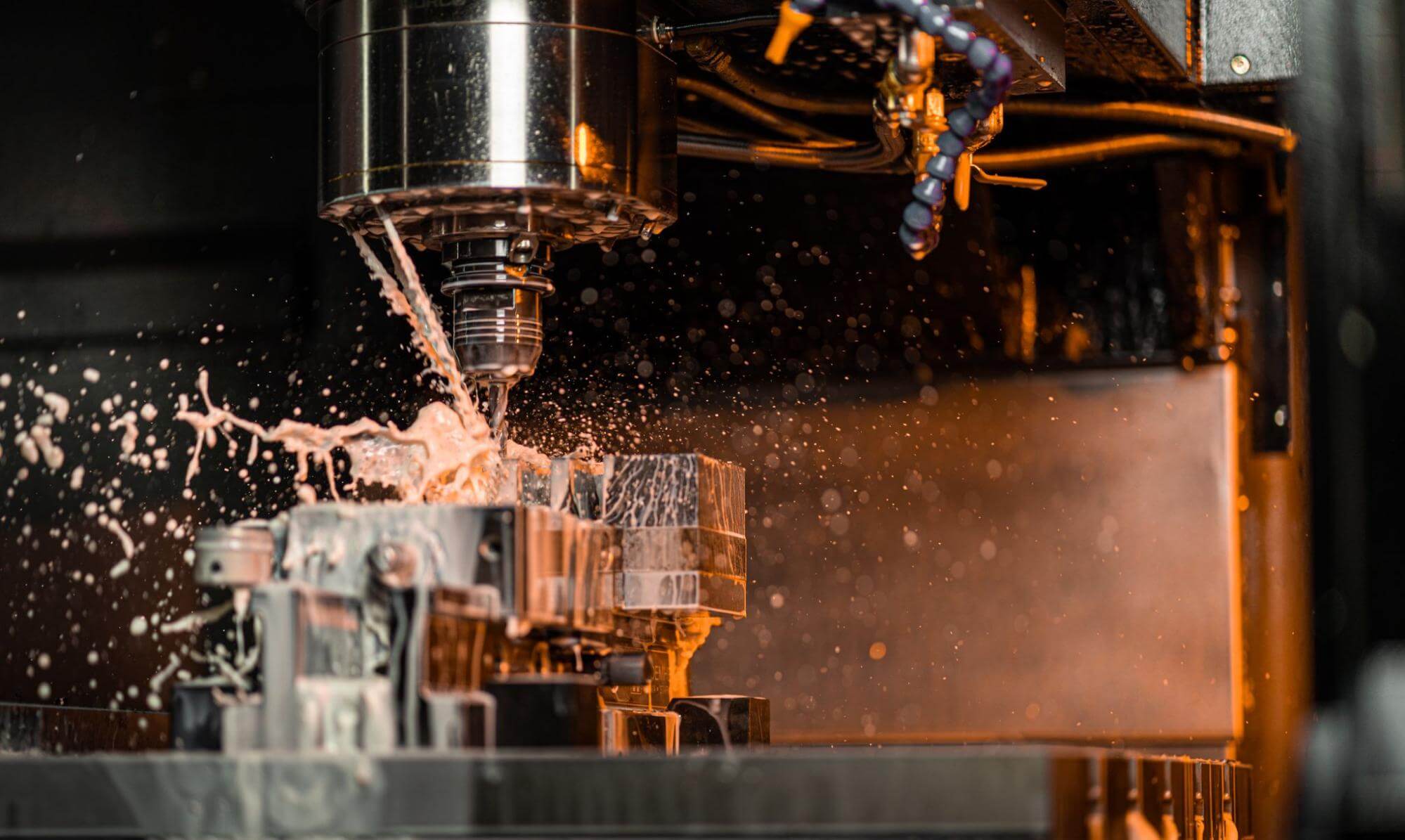
CNC machining supports a wide range of materials, including aluminum, steel, titanium, and brass—each selected for specific properties such as strength, durability, and corrosion resistance.
CNC machining is known for its high precision and versatility, and can be used with a variety of materials, including metals and plastics. It is suitable for both prototyping and low- to medium-volume production runs. This method offers excellent scalability and flexibility, making it ideal for a range of manufacturing needs.
A significant advantage is its ability to consistently produce parts with very tight tolerances and precise dimensions. This method can accommodate complex geometries, although with some limitations, making it adaptable to most engineering applications.
To dive deeper into creating CNC-machined parts, read our CNC machining design guide.
Sheet Metal Cutting and Stamping
Sheet metal cutting and stamping are used to shape thin metal sheets into highly functional components. Various techniques are employed to cut, bend, and form sheet metal with exceptional precision and repeatability, including:
- Laser Cutting: Uses a high-powered laser beam to create intricate and highly accurate designs.
- Waterjet Cutting: Uses a high-pressure stream of water mixed with abrasive particles, making it ideal for materials that are sensitive to heat.
- Punching and Stamping: Hardened tool-steel dies are used to produce holes, cutouts, or complex 3D features in metal sheets.
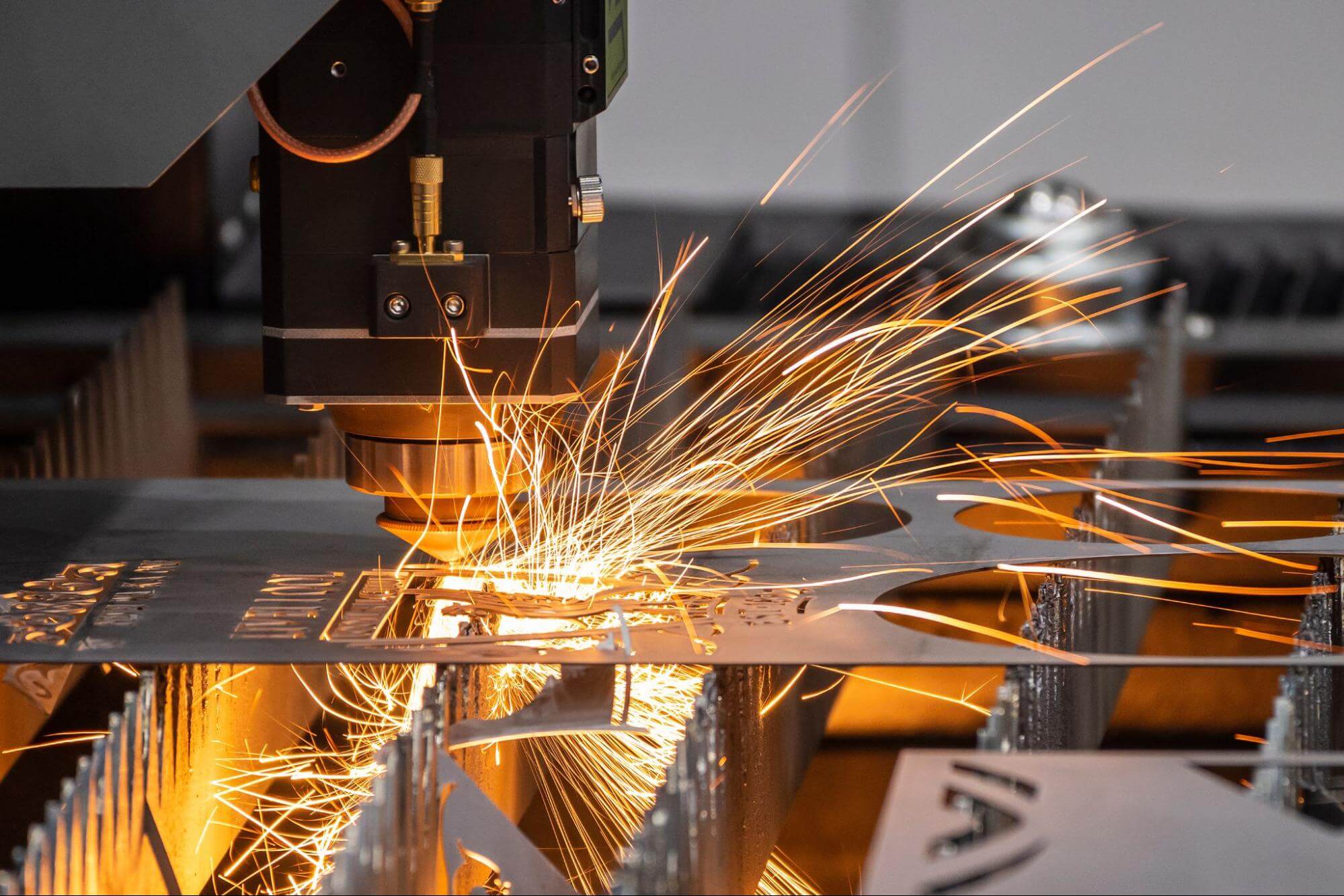
The commonly used materials include steel, stainless steel, aluminum, and copper—each chosen for its specific properties, applications, and cost-effectiveness. These techniques are widely applied in industries such as automotive (for body panels), electronics (for enclosures), and general manufacturing (for brackets and structural components).
Sheet metal cutting and stamping offer several advantages for producing metal parts. They offer high cost-efficiency in large-volume manufacturing due to their speed and consistency. Their design flexibility allows complex geometries with tight tolerances, while material efficiency minimizes waste in both mass production and custom designs.
These processes deliver a powerful combination of precision, scalability, and affordability, making them indispensable in modern metal fabrication. For more details on cutting and stamping, download our guide to sheet metal manufacturing.
Metal Forming
Metal forming methods are a versatile group of manufacturing processes that involve bending, rolling, and pressing metal sheets, bars, or plates to fabricate metal parts. Techniques such as press braking, roll forming, and stamping create a wide range of components, from those with simple bends to complex geometries. Common materials include aluminum and steel, valued for their strength and corrosion resistance.
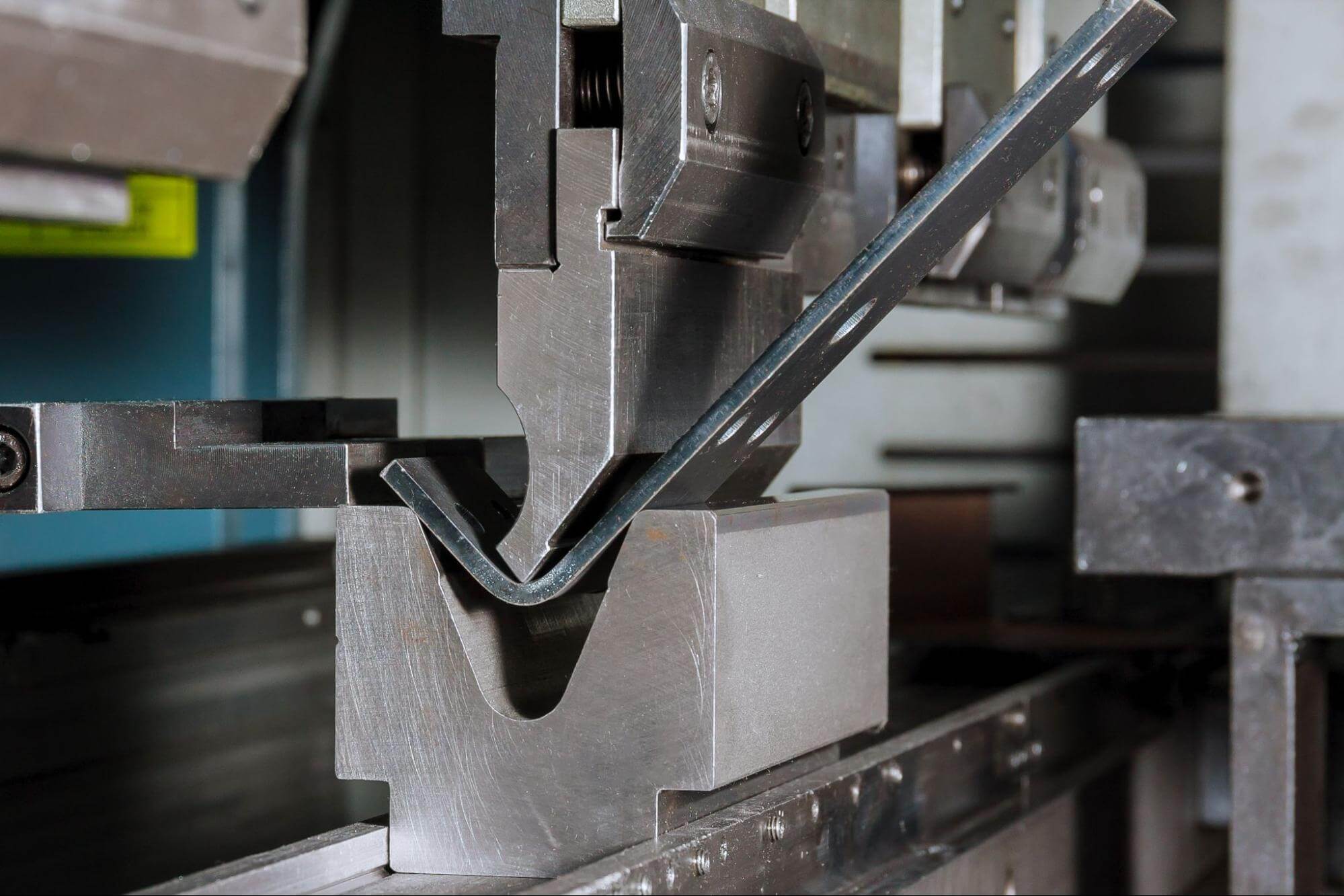
Metal forming is particularly effective for producing structural components and enclosures that require both durability and precision. This process is widely used in industries such as construction (pipes, beams), automotive (body panels, frames), and aerospace (fuselage parts, wing components).
The advantages of metal forming are numerous. It is highly cost-effective and allows for rapid production of parts with consistent quality, making it ideal for high-volume manufacturing. Additionally, metal forming can achieve complex net shapes with tight tolerances, ensuring parts meet exact design specifications.
To learn more about best sheet metal design practices, download our sheet metal design guide.
Metal Casting
Metal casting is one of the oldest and most fundamental manufacturing methods. In this process, molten metal is poured into a cavity to create complex shapes and components. Over time, it has evolved into various techniques:
- Die Casting: Uses high pressure to produce precise aluminum and zinc alloy parts, making it ideal for high-volume production and complex or thin features. Learn more from our die casting design guide.
- Investment Casting (also known as lost-wax casting): The process starts by shaping the component in wax, which is then encased in a refractory ceramic shell. Once the shell hardens, the wax is removed by heating, leaving behind a precise mold cavity. This method produces highly intricate, precise components with smooth surface finishes, making it ideal for aerospace and medical applications.
- Sand Casting: This is best suited for large parts, such as industrial machinery and automotive components, and is typically used in low- to medium-volume production.
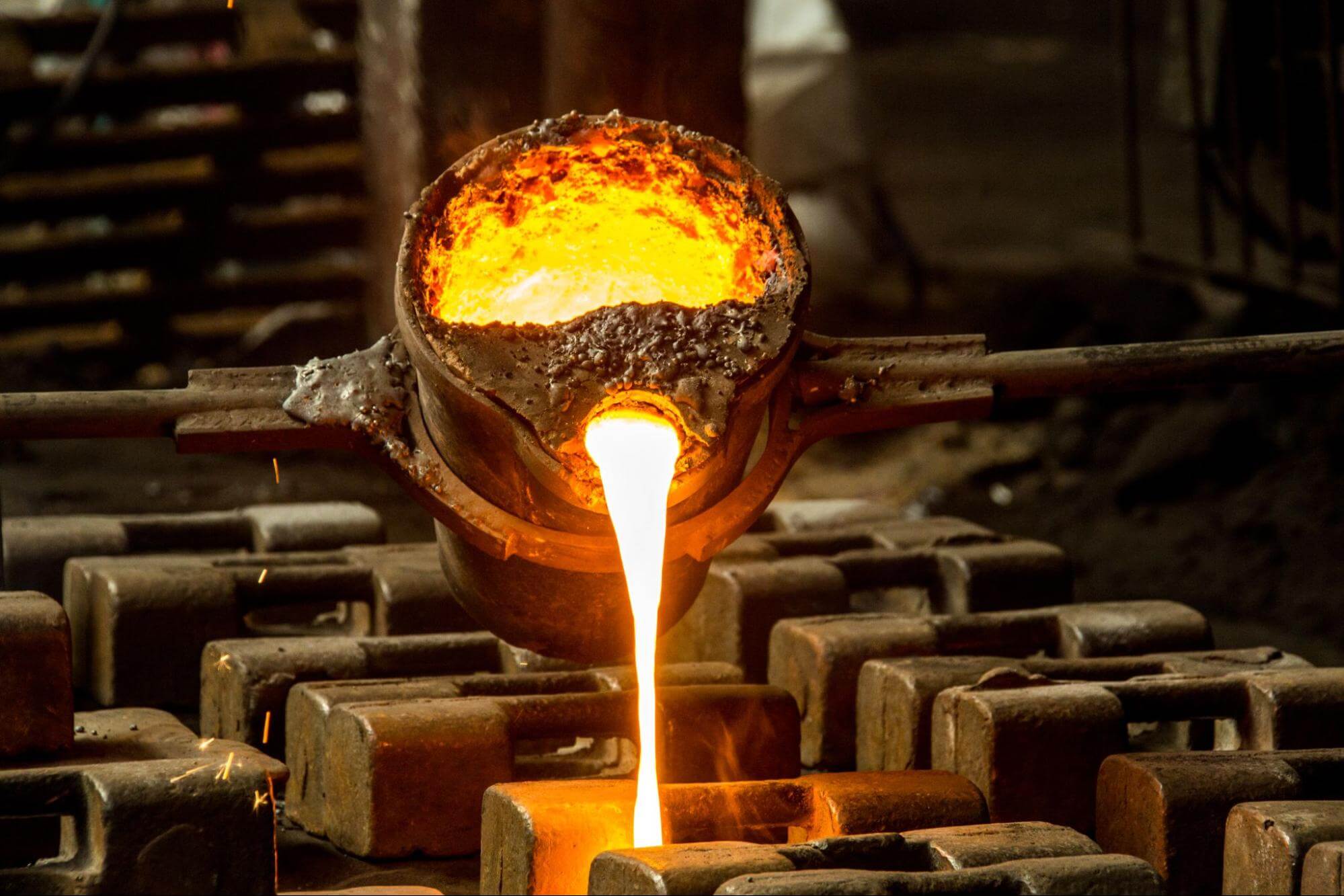
Metal casting is used in industries such as automotive (engine blocks, transmission cases), aerospace (turbine blades, structural parts), and industrial machinery (pumps, valves). Its ability to produce complex geometries with minimal post-processing makes it a preferred choice for parts requiring intricate designs.
The advantages of metal casting are significant. It supports high-volume production, making it economical for large-scale manufacturing. The process also accommodates a wide range of metals, offering flexibility in material selection. Additionally, casting enables the creation of near-net-shape parts, reducing material waste and machining requirements. With its blend of versatility, precision, and scalability, metal casting remains a cornerstone of modern manufacturing.
Forging
Forging is a manufacturing process that shapes metal using compressive forces. This force is typically applied through hammering and pressing, often in conjunction with precise dies.
This method aligns the metal’s grain structure with the shape of the finished part, enhancing its strength, durability, and resistance to impact and fatigue. Common materials used in forging include most steels, titanium, and brass, chosen for their ability to withstand high stress and environmental conditions.
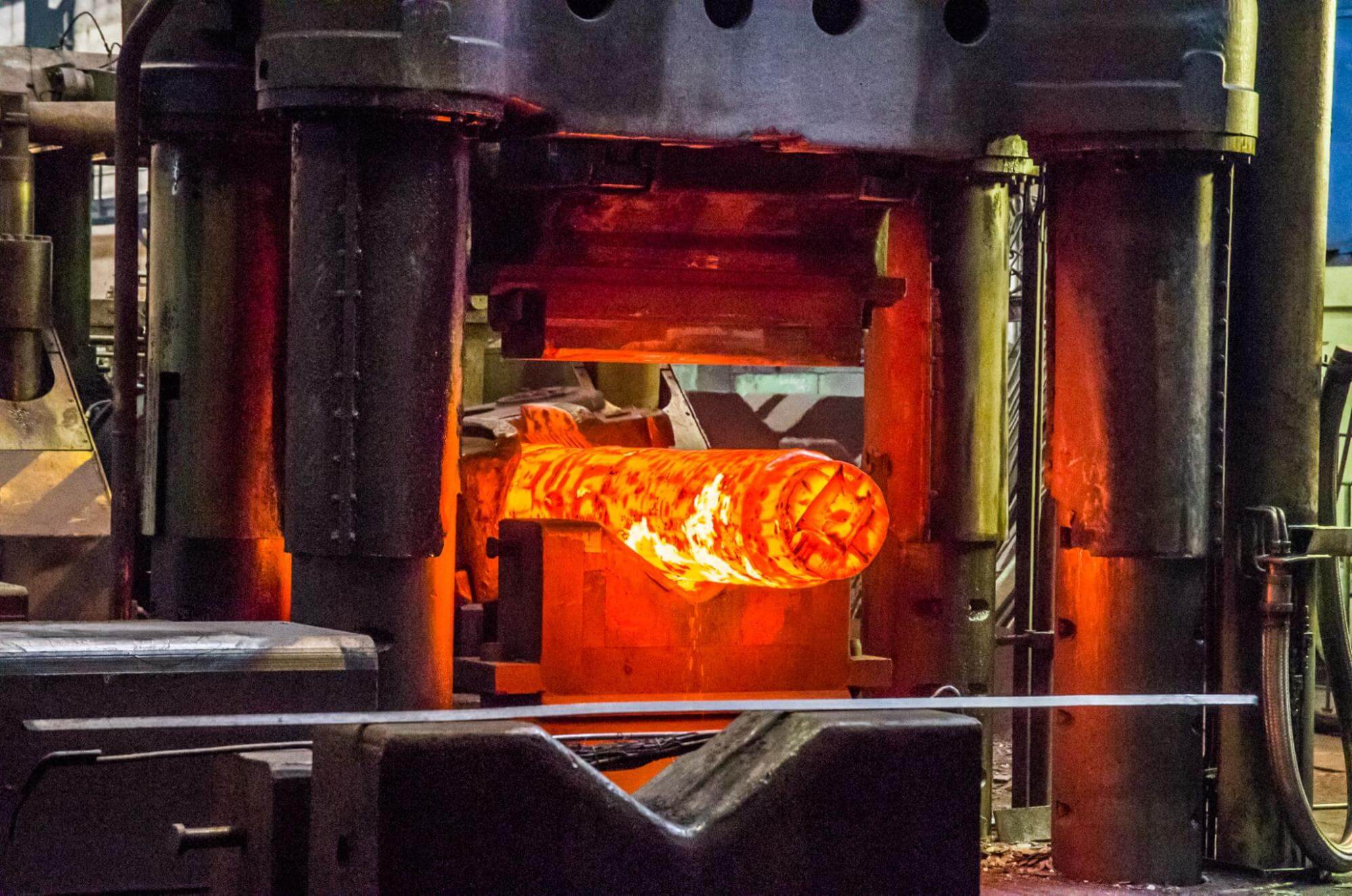
Forged components are critical in demanding industries that require parts that can endure high loads, fatigue, and harsh environments, such as aerospace (landing gear, engine parts), oil and gas (valves, drill bits), and heavy machinery (crankshafts and gears).
Forging enhances a part’s mechanical properties by aligning the metal’s grain structure through controlled compression. This directional grain flow improves tensile strength, fatigue resistance, and overall structural integrity—ideal for high-performance applications.
Forged components also exhibit high durability and reliability, reducing the risk of failure in critical applications. Additionally, forging allows for precise, near-net-shaping with minimal material waste, making it both efficient and cost-effective for high-performance parts.
Metal Injection Molding (MIM)
Metal Injection Molding (MIM) is an advanced manufacturing process ideally suited for creating small, complex metal components. It combines the versatility of plastic injection molding with the durability of metal.
The process begins by mixing fine metal powder with a polymer binder to create a moldable feedstock. This mixture is injected into a mold to form the desired shape. The molded part undergoes debinding and sintering at high temperatures to achieve its final density and strength. During this process, the binder is burned out—causing the oversized, as-molded part to shrink to its intended size as the metal particles fuse, resulting in 100% density.
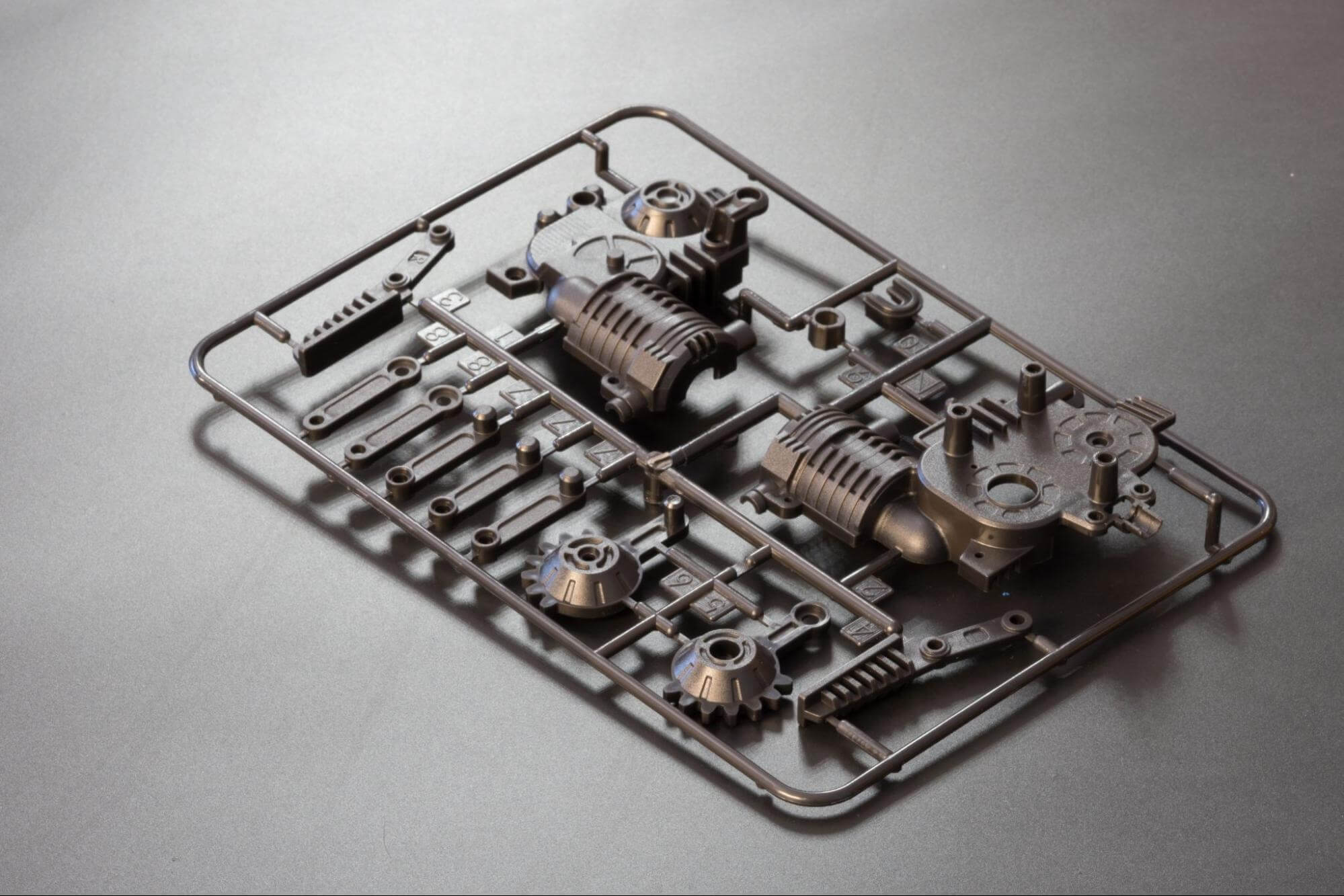
Common materials used in MIM include stainless steel and nickel alloys, known for their corrosion resistance and durability. This process is ideal for small, complex parts requiring tight tolerances. Industries such as electrical goods, automotive, and consumer electronics use MIM to produce complex, high-precision components.
MIM excels at creating highly detailed, true-net-shape components that would be difficult or costly to produce using traditional methods. This also includes high-quality surface finishes, reducing post-processing to a minimum. The process is also highly scalable, making it cost-effective for mass production. Additionally, MIM offers excellent material utilization, minimizing waste and reducing overall costs.
Metal 3D Printing
Metal 3D printing, also known as metal additive manufacturing, is a cutting-edge process that builds parts layer by layer from metal powder using high-energy sources such as lasers or electron beams. This technique enables the creation of highly complex and lightweight geometries that would be difficult or impossible to achieve with traditional manufacturing methods.
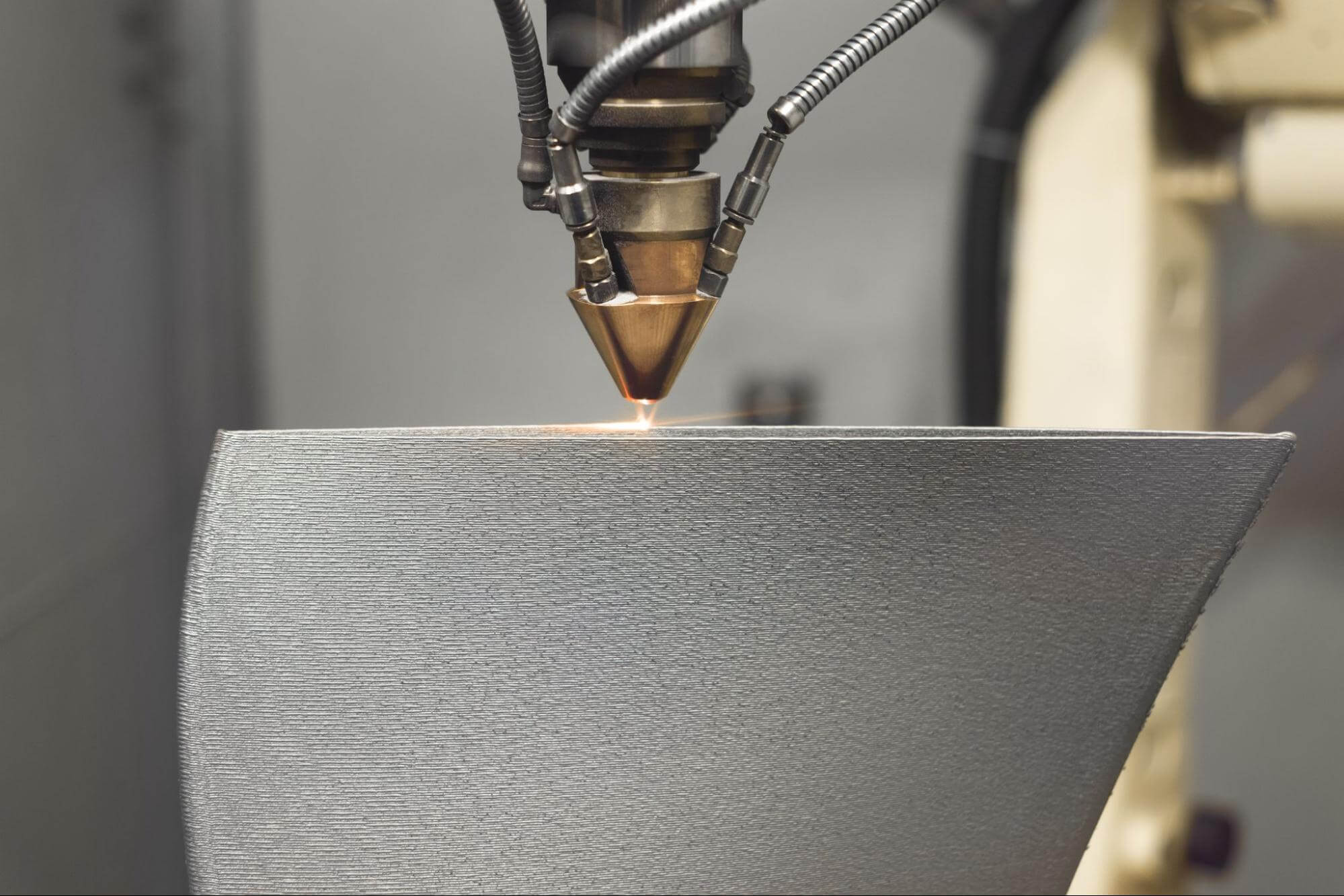
Common methods include:
- Selective Laser Melting (SLM) and Direct Metal Laser Sintering (DMLS): These use a laser to fully or partially melt metal powders and fuse them together.
- Electron Beam Melting (EBM): Similar to SLM but uses an electron beam in a vacuum, suitable for high-temperature materials like titanium.
- Binder Jetting: Involves depositing a binding agent onto a powder bed, followed by sintering—ideal for high-volume, lower-cost production of metal parts.
Materials commonly used in metal 3D printing include stainless steel, titanium, aluminum, cobalt-chrome, and Inconel. These metals are chosen for their mechanical strength, corrosion resistance, and temperature tolerance.
Metal 3D printing is widely used in industries such as aerospace (lightweight structural parts), medical (custom implants and surgical tools), and automotive (prototyping and motorsport components). Its ability to consolidate multi-part assemblies into a single piece reduces assembly steps and enhances performance.
The key advantages of metal 3D printing include exceptional design freedom, low material waste, and rapid prototyping of high-performance parts. The process also supports true near-net-shape manufacturing, reducing or even eliminating the need for secondary machining. Additionally, metal additive manufacturing excels in producing custom or low-volume parts quickly, making it ideal for innovation-driven applications and high-mix, low-volume production environments.
To learn more about additive manufacturing design best practices and material selection, explore our 3D printing design guide.
Metal Extrusion
Metal extrusion is a manufacturing process where heated metal is forced through a die to create parts with a uniform cross-section. This method is particularly effective for producing long, continuous shapes such as rods, bars, and tubes. Common metals used in extrusion include aluminum, copper, and magnesium, chosen for their lightweight properties, strength, and conductivity.
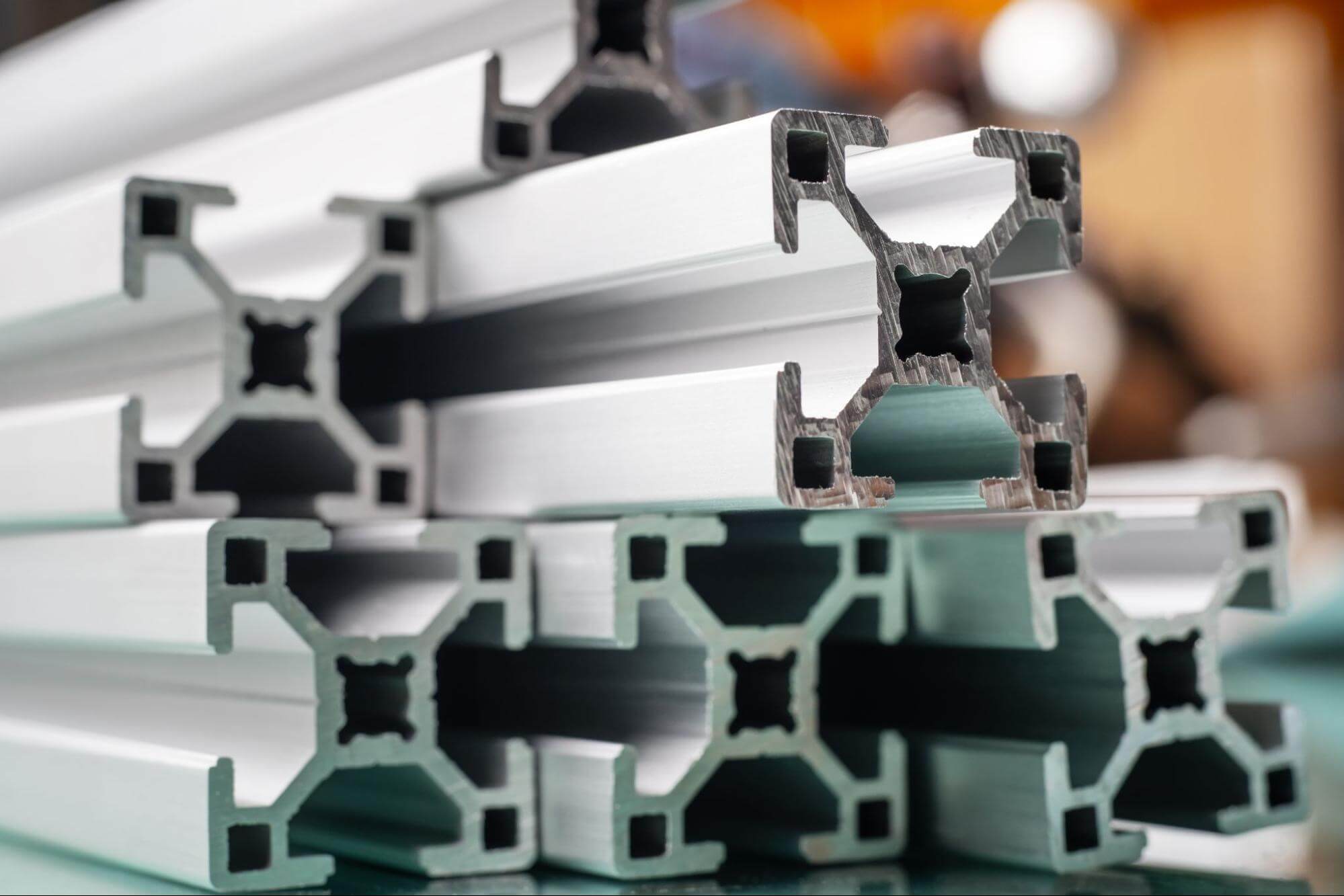
The process is widely used in industries such as electronics (heat sinks, connectors), construction (structural frames, window profiles), and automotive (tubing, chassis components). Extruded parts are valued for their consistency, precision, and ability to meet complex design requirements.
Metal extrusion is ideal for creating lightweight, high-strength parts, making it a preferred choice for applications where weight reduction is critical. The process also offers excellent material utilization, as it minimizes waste and allows for the recycling of scrap material. Additionally, extrusion supports the production of complex cross-sections with tight tolerances, ensuring high-quality results.
Did you know Fictiv offers metal extrusion for high volumes? Contact Us to get your quote for high-quality metal extrusions.
Welding in Metal Manufacturing
Welding is one of the most critical metal parts fabrication processes, involving the joining of metal components using high heat, often with the addition of a compatible filler material. This creates a permanent coupling, ensuring structural integrity and resilience/strength. Common welding techniques include:
- MIG (Metal Inert Gas): Also known as Gas Metal Arc Welding (GMAW), this method uses a consumable wire electrode and a shielding gas delivered through the welding gun. It’s fast, relatively easy to learn, and produces strong, clean welds—making it ideal for steel, aluminum, and high-throughput fabrication.
- TIG (Tungsten Inert Gas): Also called Gas Tungsten Arc Welding (GTAW), TIG uses a non-consumable tungsten electrode and a separate filler rod (if needed), along with an inert shielding gas like argon. Known for its precision and clean finish, TIG is commonly used for critical welds in aerospace, marine, and precision fabrication.
- Spot Welding: A type of resistance welding that joins overlapping metal sheets by applying pressure and passing a high electric current through the contact point. Unlike arc welding, it doesn’t use a wire electrode or shielding gas. It’s ideal for joining sheet metal in high-volume applications such as automotive body panels and electronics enclosures.
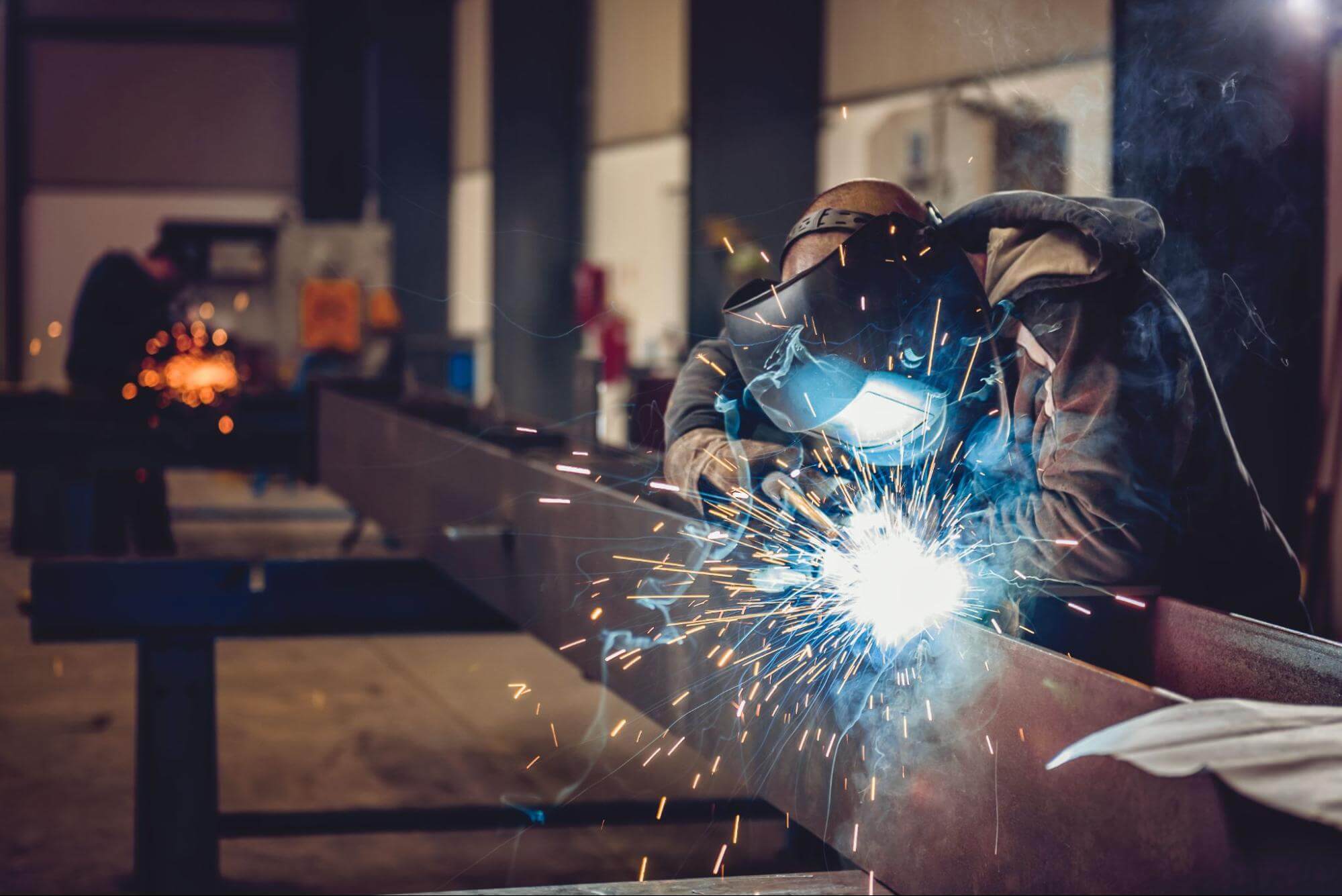
Welding is widely used in industries such as automotive (chassis, body frames), shipbuilding (hulls, structural components), and heavy machinery (frames, attachments). Its ability to create durable, high-strength joints makes it indispensable for constructing large and complex structures.
The advantages of welding are numerous and difficult to substitute in custom metal part fabrication. It provides permanent and native material connections, ensuring long-lasting and reliable coupling without the need for fasteners.
The process also enhances structural strength by improving stress dissipation, as well as resistance to vibration and fatigue, making it suitable for load-bearing applications. Additionally, welding is versatile, accommodating a wide range of metals and thicknesses, and can be adapted for both manual and automated production.
To maintain consistency and precision in welded assemblies, weld fixtures — specialized tools that hold components in place during welding — are often used to ensure accurate alignment and preserve critical specifications throughout production. Fictiv offers welding for prototype and production requirements.
Choosing the Right Metal Parts Manufacturing Process
Selecting the appropriate manufacturing process for metal parts is a critical decision that impacts quality, cost, and production timelines. Table 1 is a comparison chart of the key differences of various metal parts manufacturing methods:
Process | Materials | Production volume | Typical tolerance (mm) | Surface quality | Cost | Example Applications |
Casting | Aluminum, Iron, Bronze, Zinc | Low-high | 0.5–2.0 | Medium- rough | Low- medium | Engine blocks, tool structures, pipes, sculptures |
Forging | Steel, Aluminum, Titanium | Medium-high | 0.3–1.0 | Medium | Medium- high | Crankshafts, gears, aerospace parts |
Machining | All metals | Low-high | 0.025–0.1 | Very smooth | High | Precision parts, tools, prototypes |
Sheet Metal Forming | Steel, Aluminum, Copper | Medium-high | 0.1–0.5 | Smooth | Low- medium | Car panels, enclosures, appliances |
Metal 3D Printing | Steel, Aluminum, Titanium | Low-medium | 0.1–0.5 | Medium- rough | High | Aerospace, medical implants, lightweight structures |
Extrusion | Aluminum, Copper, soft alloys | High | 0.1–0.5 | Smooth | Low- medium | Window frames, rods, tubing |
Metal Injection Molding | Steel, Titanium, Tungsten | High | 0.1–0.3 | Medium | Medium | Gears, bearings, filters |
Welding | Most metals | Variable with skill and equipment | 0.5–3.0 | Rough | Variable | Pipelines, shipbuilding, machinery |
Comparison of Different Metal Manufacturing Methods
By carefully evaluating these factors, manufacturers can choose the most efficient and effective process, ensuring high-quality parts that meet design requirements while optimizing time and cost.
Optimizing Metal Processing: Choosing the Right Method for Superior Results
Metal processing offers a variety of manufacturing methods with unique advantages and applications. From casting and forging to machining and welding, selecting the proper technique depends on factors like material properties, precision requirements, production volume, and cost efficiency. For example, casting is ideal for complex shapes, while forging provides superior strength. Machining ensures high precision, and welding enables robust joins.
As technology evolves, staying informed about these processes helps optimize production quality and efficiency. Manufacturers and engineers are encouraged to evaluate their project needs carefully—considering the material, design complexity, and budget—to choose the most suitable method. By doing so, businesses can enhance performance, reduce waste, and achieve better results in their metalworking endeavors.
Need precision-manufactured metal parts? Fictiv offers a range of metal manufacturing services, including CNC machining, sheet metal fabrication, casting, and more.
Request an instant quote today with a process tailored to your needs, and bring your custom metal components to life through high-quality, on-demand production.