Time to read: 6 min
Printing plays a critical role in modern manufacturing by enabling companies to add branding, safety information, traceability features, and functional markings to a wide range of products. Several different printing techniques exist, each suited to different materials, shapes, and production requirements. Among these, pad printing stands out as a highly versatile and precise method, particularly useful for transferring detailed designs onto curved, textured, or irregular surfaces.
Industries such as the medical, automotive, consumer electronics, and industrial manufacturing sectors rely on this printing method for high-quality, long-lasting markings. While alternative methods such as screen printing and UV printing offer advantages in specific applications, pad printing excels in detailed, small-area printing.
This article explores the pad printing process, its applications and advantages, and comparisons with other printing techniques.
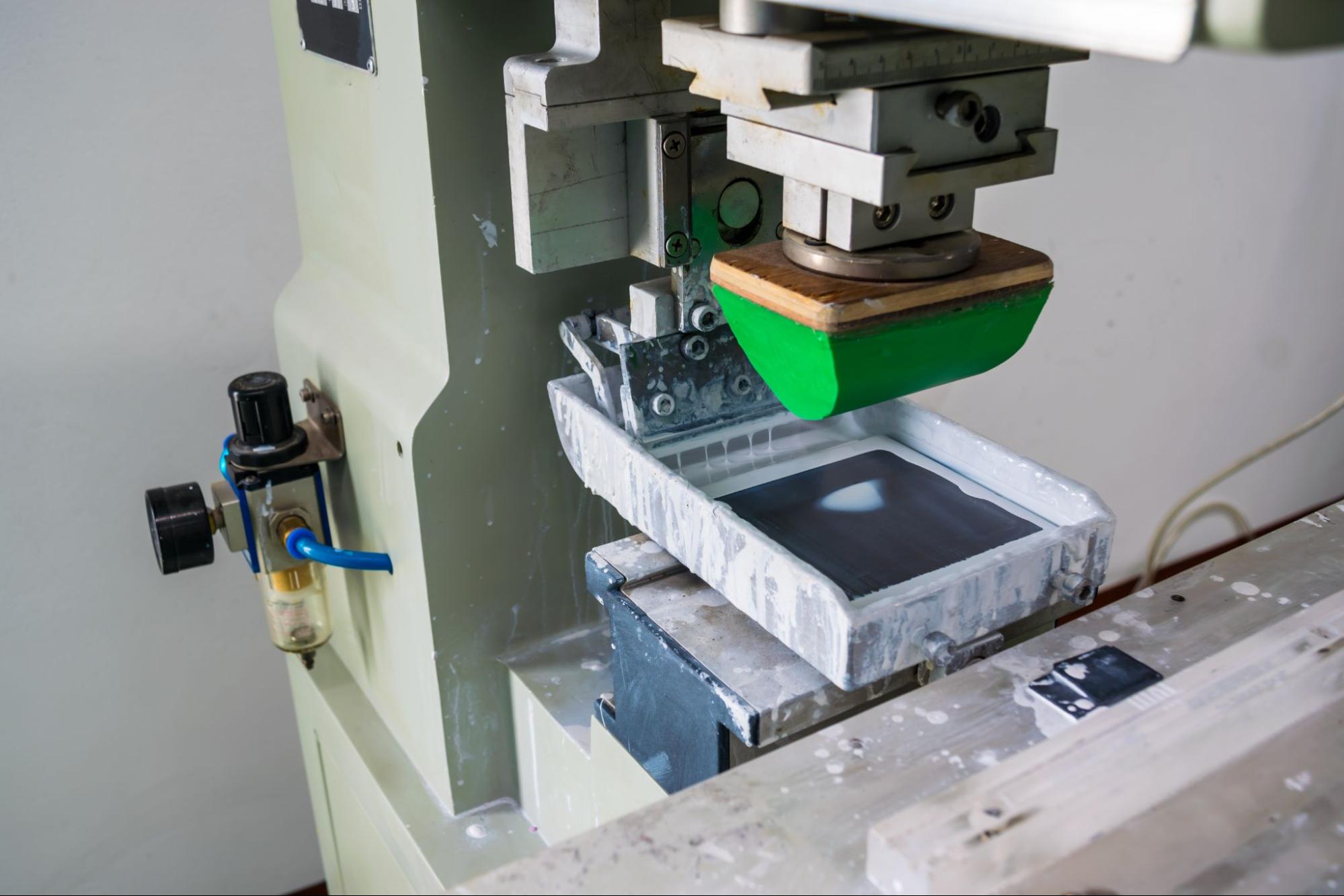
What Is Pad Printing?
Pad printing, or tampography, is an indirect offset printing process that involves the transfer of ink from an etched plate to a substrate using a soft silicone pad. Silicone printing pads are often preferred due to the material’s low durometer (or hardness) and ability to conform to different shapes. The printing process enables precise and accurate printing on objects of various shapes, textures, and materials.
The following steps outline how pad printing works:
- Image Etching: A design is etched onto a metal or polymer plate (cliché), creating a recessed image that will hold ink. The depth and footprint of the etching influence the amount of ink retained, affecting the final print quality in terms of legibility and durability.
- Ink Application and Doctor Blade Removal: Ink is applied over the etched plate, and a doctor blade or ink cup blade removes the excess, ensuring that ink remains only in the recessed areas of the design. The type of ink used can vary based on the substrate, with solvent-based, UV-curable, and two-component inks being common choices.
- Transfer via Silicone Pad: A silicone pad makes contact with the etched plate, picking up the inked design and transferring it onto the part’s surface. The unique properties of silicone allow for minimal ink distortion and precise ink transfer, ensuring consistent results even on intricate or contoured surfaces. Additionally, the flexibility of the silicone pad allows it to conform to different surface textures and shapes, ensuring a uniform print.
- Drying and Curing Process: The ink dries or cures, depending on the type of ink and substrate. Some inks air dry quickly, while others require UV or heat curing to enhance adhesion and resistance. Choosing the appropriate method results in a highly durable print.
Applications of Pad Printing in Manufacturing
Pad printing is used in multiple industries for various purposes, such as branding, safety labeling, and instructional markings. Its versatility allows manufacturers to add crucial details to a wide range of products to achieve regulatory compliance, enhanced product aesthetics, and improved product functionality. Below are several ways pad printing is used in manufacturing:
- Medical Devices: Pad printing is crucial for marking instruments, syringes, and surgical tools with measurement indicators, dosage instructions, and traceability features. Since medical tools often have curved or small surfaces, this method ensures legible, durable markings on the tools’ surfaces. It can also withstand sterilization and repeated use.
- Automotive: Applications include symbols, traceability features like barcodes and labels, and text on dashboards, buttons, control knobs, and more. The ability to print fine details on textured or contoured surfaces ensures that critical safety information and functional markings remain readable and resistant to wear over time.
- Consumer Electronics: Pad-printed branding, logos, and functional symbols are featured on many consumer electronic devices, such as smartphones, laptops, GPS devices, and headphones. This method allows for precise application on plastic and metal components, enhancing aesthetic appeal while maintaining durability.
- Industrial Equipment: Heavy-duty machinery and industrial tools require legible serial numbers, safety warnings, and in-situ operating instructions. Pad printing ensures that these markings remain visible even in harsh environments, where they may come in contact with oil, grease, or other chemicals and can experience high temperatures or significant temperature fluctuations. It is an essential method for guaranteeing regulatory compliance, routine maintenance, and longevity for equipment through durable traceability markings.
- Injection-Molded & 3D-Printed Parts: As customization and rapid prototyping become more prevalent, manufacturers need reliable ways to mark 3D-printed and injection-molded parts. Pad printing enables branding, labeling, or instructional text to be applied efficiently, even on complex or non-uniform surfaces.
Do you need your parts pad-printed? Fictiv can do that for you.
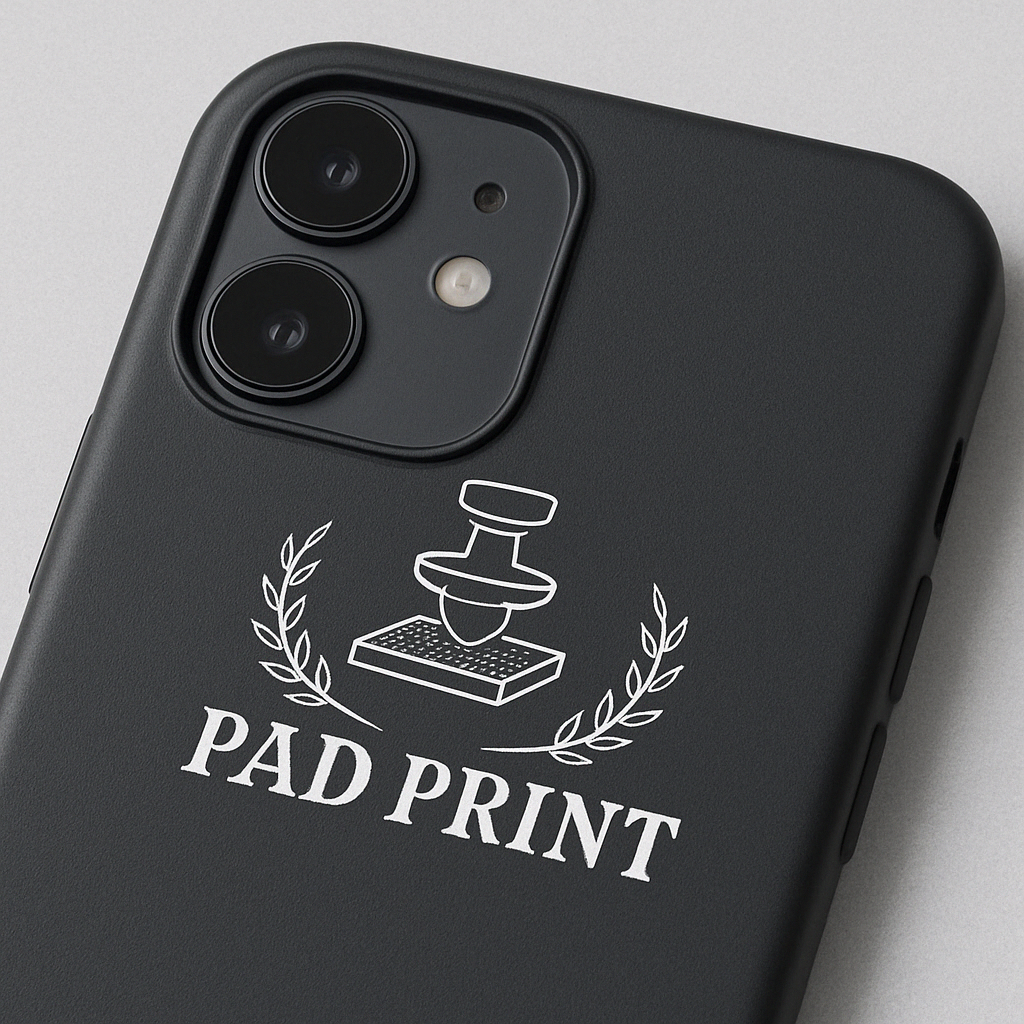
Advantages of Pad Printing
Pad printing offers several key benefits that make it a preferred choice for marking products in manufacturing. Its ability to imprint complex, textured, and contoured surfaces and maintain high accuracy makes it indispensable for industries that require detailed, long-lasting markings. Below are some of its advantages:
- Works on Irregular, Curved, and Textured Surfaces: It can produce designs on concave, convex, and textured areas, making it ideal for applications where traditional printing methods fail.
- High Accuracy and Fine Detail Capability: It allows for the reproduction of intricate designs, small fonts, and detailed logos. The ability to achieve high-resolution prints makes it an excellent choice for applications requiring small writing and narrow line widths, such as medical devices and electronic components.
- Compatible with Multiple Substrates: One of the biggest advantages of the pad printing method is its versatility. It can be used to print on various materials, such as plastics, metals, glass, ceramics, rubber, and even wood. This makes it a highly flexible solution across different industries that utilize a variety of materials.
- Strong Ink Adhesion with Optional Post-Curing for Enhanced Durability: Pad-printing inks can be formulated to resist chemicals, heat, and abrasion, depending on the application. Curing techniques, such as UV or heat, further enhance ink adhesion to ensure that markings remain intact even under extreme conditions.
- Cost-Effective for Medium- to High-Volume Production Runs: Pad printing is an efficient and economical choice for medium- to high-volume production runs, balancing quality and cost. Unlike screen printing—which requires costly setup and is better suited for large-scale production of flat-surfaced products—pad printing provides a more affordable solution. It’s ideal for manufacturers needing detailed, high-quality prints on irregular surfaces in moderate quantities.
- Multicolor Printing Capability: It enables the application of multiple, accurately located color layers, making it ideal for both decorative branding and functional labeling. Specialized pad printing systems can accommodate multicolor processes efficiently and ensure vibrant and durable results without compromising production speed.
Comparing Pad Printing to Other Printing Methods
While pad printing is highly versatile, other methods have their strengths and may be preferred in certain scenarios. Below are some comparisons of pad printing vs. screen printing and UV printing.
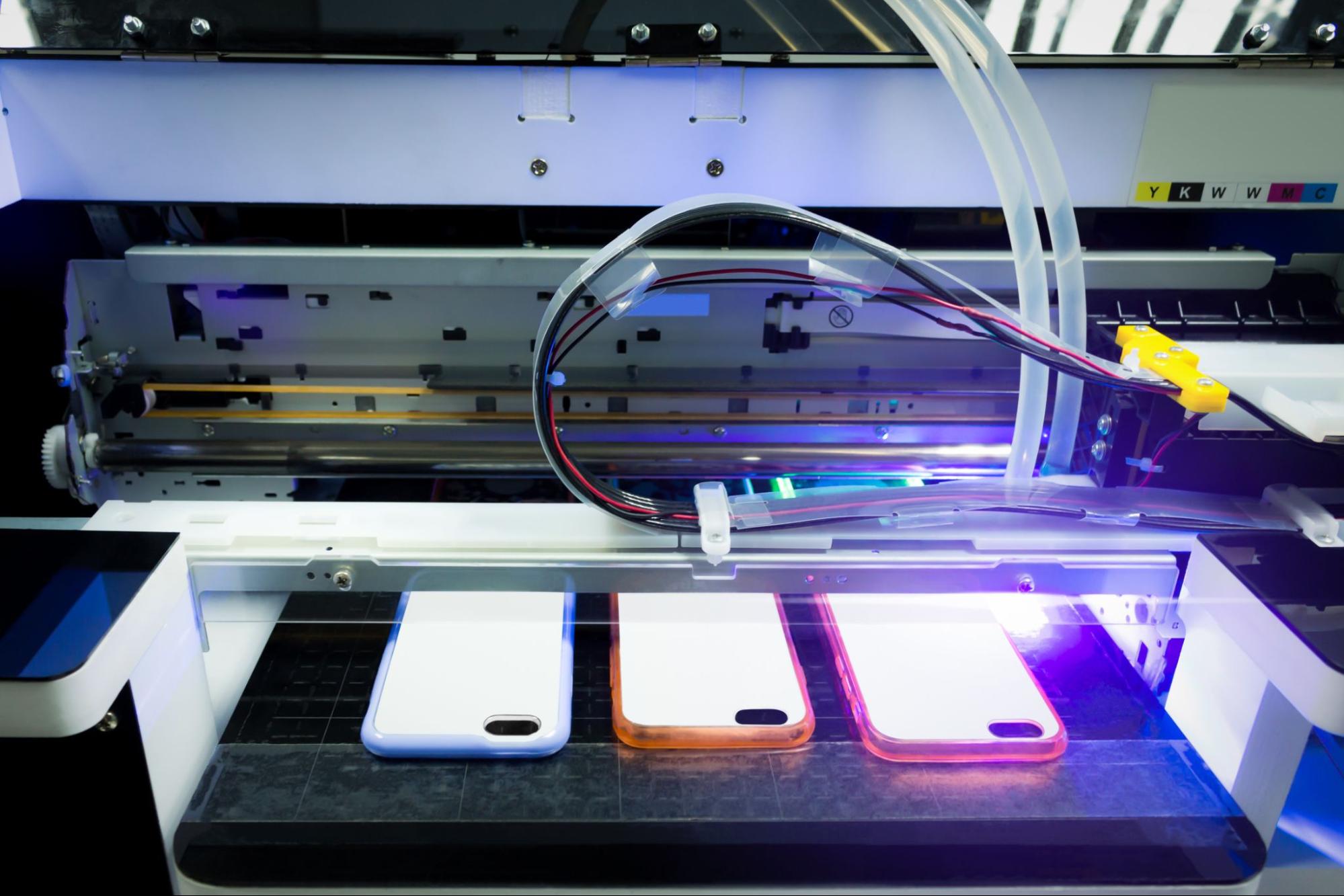
Screen Printing vs. Pad Printing
In screen printing, ink is discharged through a stencil onto a fabric, paper, or plastic surface. It’s commonly used for making T-shirts, posters, signs, and artwork. Screen printing is better suited for large, flat surfaces than pad printing. It can also provide thicker ink deposits, which increases durability and resistance to wear.
Pad printing excels in printing on small, intricate, or contoured shapes by offering high detail and accuracy where screen printing may struggle. It is also more effective for multicolor applications or irregular surfaces.
UV Printing vs. Pad Printing
UV printing is a digital printing technique that utilizes ultraviolet (UV) light to instantly cure the ink once printed onto a surface. UV printing enables full-color, high-resolution graphics, making it ideal for branding and decorative applications.
Pad printing is more suited for functional markings on uneven surfaces where durability and precision are crucial, such as serial numbers or safety warnings. Unlike UV printing, which works best on flat surfaces, pad printing can handle a variety of shapes and textures without compromising print quality.
Pad Printing on Metal and Other Materials
Pad printing on metal surfaces requires specialized inks and substrate treatments to ensure long-lasting results. Proper surface preparation, ink selection, and post-curing processes ensure strong adhesion on stainless steel, aluminum, and coated metals. Techniques such as plasma treatment or chemical primers can enhance ink bonding.
Alternative marking methods such as laser engraving, chemical etching, or anodized printing may provide superior durability and longevity for metal parts subject to extreme wear or exposure to harsh environments.
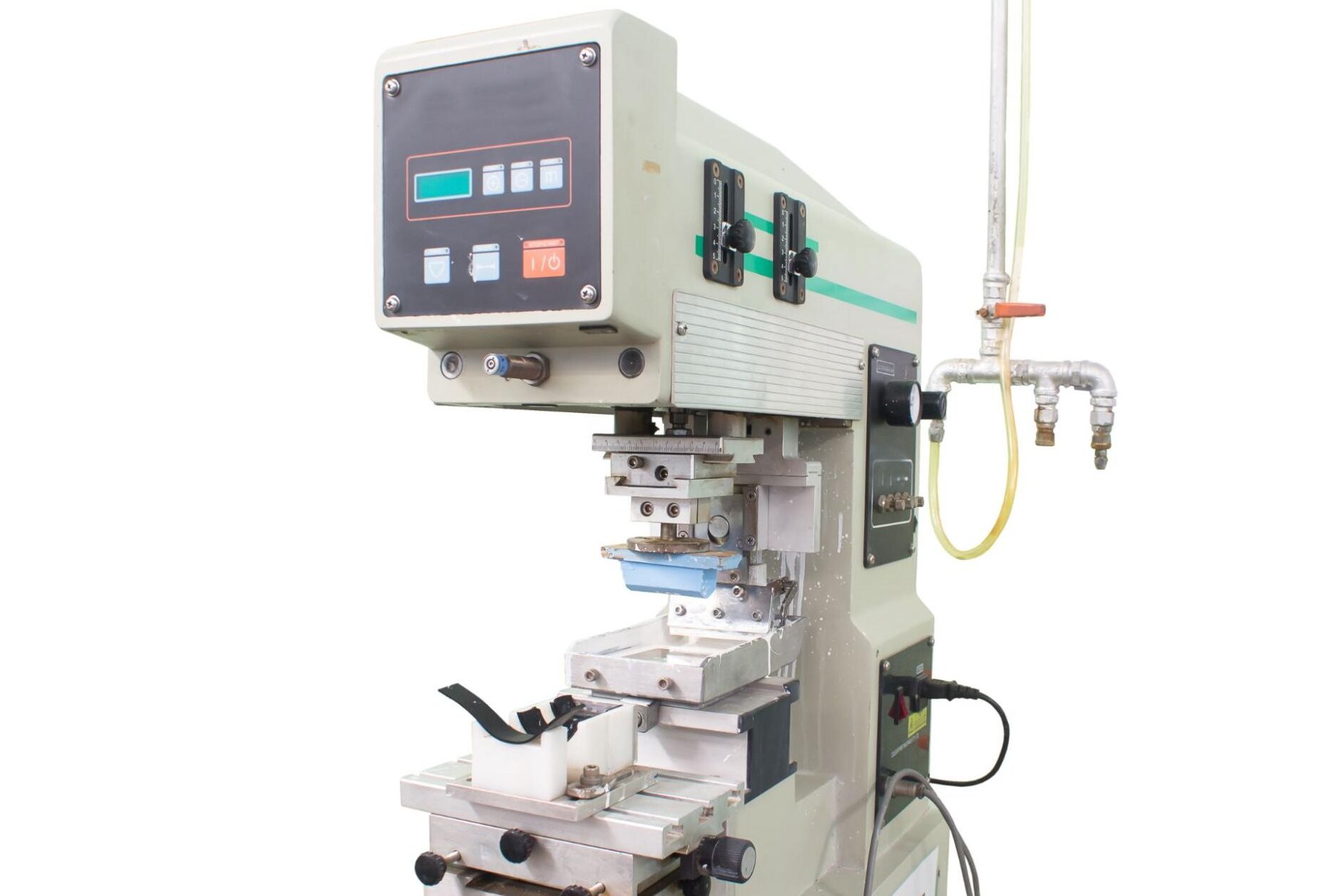
Choosing the Right Printing Solution for Precision Manufacturing
Pad printing remains a critical tool in manufacturing due to its adaptability and precision. Whether marking medical devices, automotive parts, or consumer electronics, this method provides a reliable and efficient method for detailed and durable prints.
When selecting a printing method, manufacturers must consider material, surface shape, ink durability, cost, and other factors. For businesses seeking high-quality printing solutions, exploring processes such as pad printing, screen printing, and UV printing can help optimize production needs.
Looking for high-quality, precision printing on manufactured parts? Get an instant quote today to explore the best printing solution for your project.