Time to read: 8 min
CNC machining outsourcing is a manufacturing strategy that involves contracting with another company for CNC machining services. Whether for prototyping or production, product designers who outsource their machined parts gain access to advanced technology, leverage custom machining solutions, and avoid expensive investments in equipment and training.
This guide provides an overview of computer numerical control (CNC) machining outsourcing and explains when third-party machining is a sound business decision. Outsourcing is used widely in the B2B sector, typically as a cost reduction tool, but its benefits go beyond the bottom line. With the right partner, companies that outsource machining work can get to market faster with reduced expenses, high-quality components, and a competitive edge.
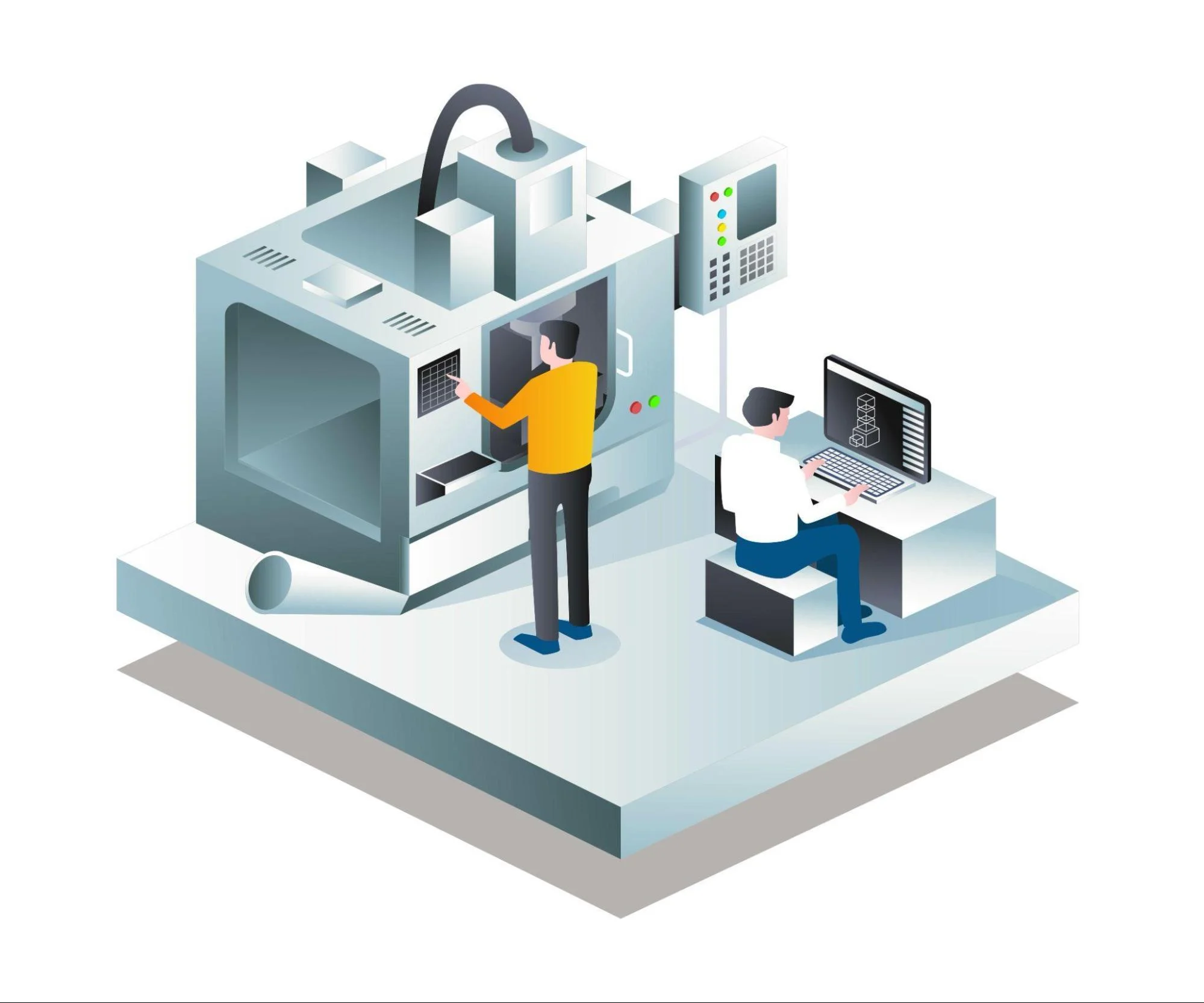
The Benefits of Outsourcing CNC Machining
There are many benefits to outsourcing CNC machining, such as:
- Cost Savings
- Ability to Service Advanced Capability Requirements
- Improved Flexibility and Scalability
- More Time to Focus on Core Competencies
- Immediate Access to Industry Expertise
- Specialized Skills Access without Overhead
- Reduced Time to Market
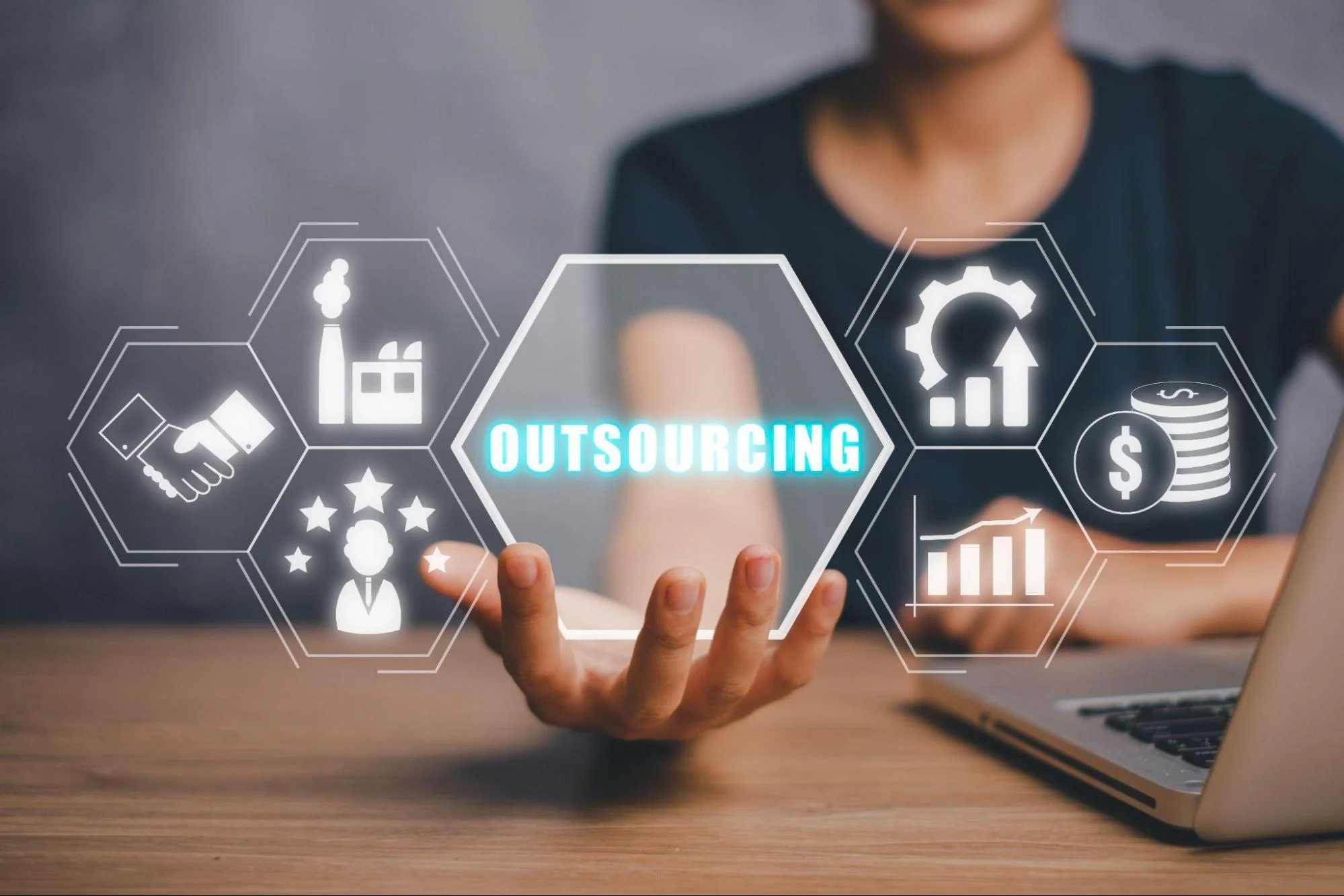
Cost Savings
Purchasing or leasing your own CNC machining equipment is a significant capital expenditure. In-house CNC machining requires substantial investments not just in machinery but also in ongoing maintenance and repair. Outsourcing CNC machining services allows you to avoid rental fees and capital expenditures, including maintenance and repair expenses. There are also cost savings on upfront and recurring overhead and labor. With CNC labor outsourcing, you won’t have to hire and train CNC machinists. You can also save money by reducing the overhead associated with storing raw materials or finished goods.
Although outsourcing may reduce direct labor costs, it can also introduce expenses related to managing the outsourced relationship, such as quality control, logistics, and communication. While these costs are typically significantly less than the cost of performing CNC machining in-house, they should be carefully considered and included in any cost-benefit analysis to ensure that outsourcing delivers a financial advantage.
Ability to Service Advanced Capability Requirements
CNC production outsourcing also lets you gain access to advanced technologies such as automation and robotics, smart manufacturing systems, six-axis machining, high-end cutting tools, and rapid prototyping capabilities without any additional financial investment. With improvements in CNC software and the faster processing power of advanced CNC controllers, you can get greater precision during machining for tighter tolerances and, consequently, fewer issues with tolerance stack-ups. This allows you to take on more business without being limited by the technologies you have access to.
Improved Flexibility and Scalability
Outsourcing also lets you scale production up or down based on demand without major investments in labor and equipment. Flexible machining resources make it possible to move from small batches to high-volume production (or vice versa) in response to product development efforts or market changes. The ideal partner can grow with you and offer cost-saving advice that reflects your production forecasts.
In addition, the outsourcing method for CNC machining can allow you to realize inventory management strategies such as just-in-time (JIT), which helps to reduce the cost of holding inventory by streamlining materials and production.
Fictiv offers streamlined sourcing by providing CNC machined parts in as little as one day. Get an instant quote now.
More Time to Focus on Core Competencies
Opportunity cost is a potential loss of profit from not having more time to pursue what you consider to be a core competency. If you’re a product designer or engineer, there’s an opportunity cost to spending part of your workday running a CNC milling machine instead of creating or refining innovative designs. Outsourcing work to a machining service provider lets you focus on your core competencies for greater profitability. While you focus on what you do best, they focus on the prototyping or production process.
However, opportunity cost goes beyond the potential loss of profit; it also includes the potential reduction in efficiency and innovation. By diverting focus from your core competencies, you risk compromising the development of new products or improvements to existing ones. Outsourcing can help you maximize efficiency, foster innovation, and ensure that your resources are allocated to activities that drive the most value for your business.
See how Catalyst Engineering kept their core competencies in-house and let Fictiv handle the rest. This enabled them to produce twice as fast as competitors and reduced overhead costs by 20-30%.
Immediate Access to Industry Expertise
The manufacturing industry is becoming increasingly complex, but you can get the expertise you need through precision outsourcing. For example, if you’re designing custom parts with high-volume manufacturing, you may need a CNC machining provider that offers outsourced production management services such as scheduling and inventory control. You can find industry expertise in areas such as aerospace machining and medical device machining.
Fictiv provides instant access to a Fortune 500 supply chain, along with guided expertise for NPI, DFM, and more. We provide the industry knowledge you need to make smart sourcing decisions.
Access to Specialized Skills
Now, more than ever, skilled CNC machinists can be difficult to find and retain. Because demand for their services is high, wages are at a premium. Outsourcing provides you with access to talented workers but without the challenges associated with workforce recruitment and retention. You can also choose a CNC machining provider who offers CNC programming services that support the prototyping or production of high-quality components.
Key Considerations for Outsourcing CNC Machining
If you’re ready to outsource your CNC machining work, start by evaluating your CNC machining needs. Here are some key considerations.
- Selecting the Right Partner
- Evaluating Cost and Savings
- Ensuring Clear Communication
- Managing Intellectual Property
- Quality Control and Assurance
- Supplier Location and Logistics
- Compliance and Certifications
- Data Security and Confidentiality
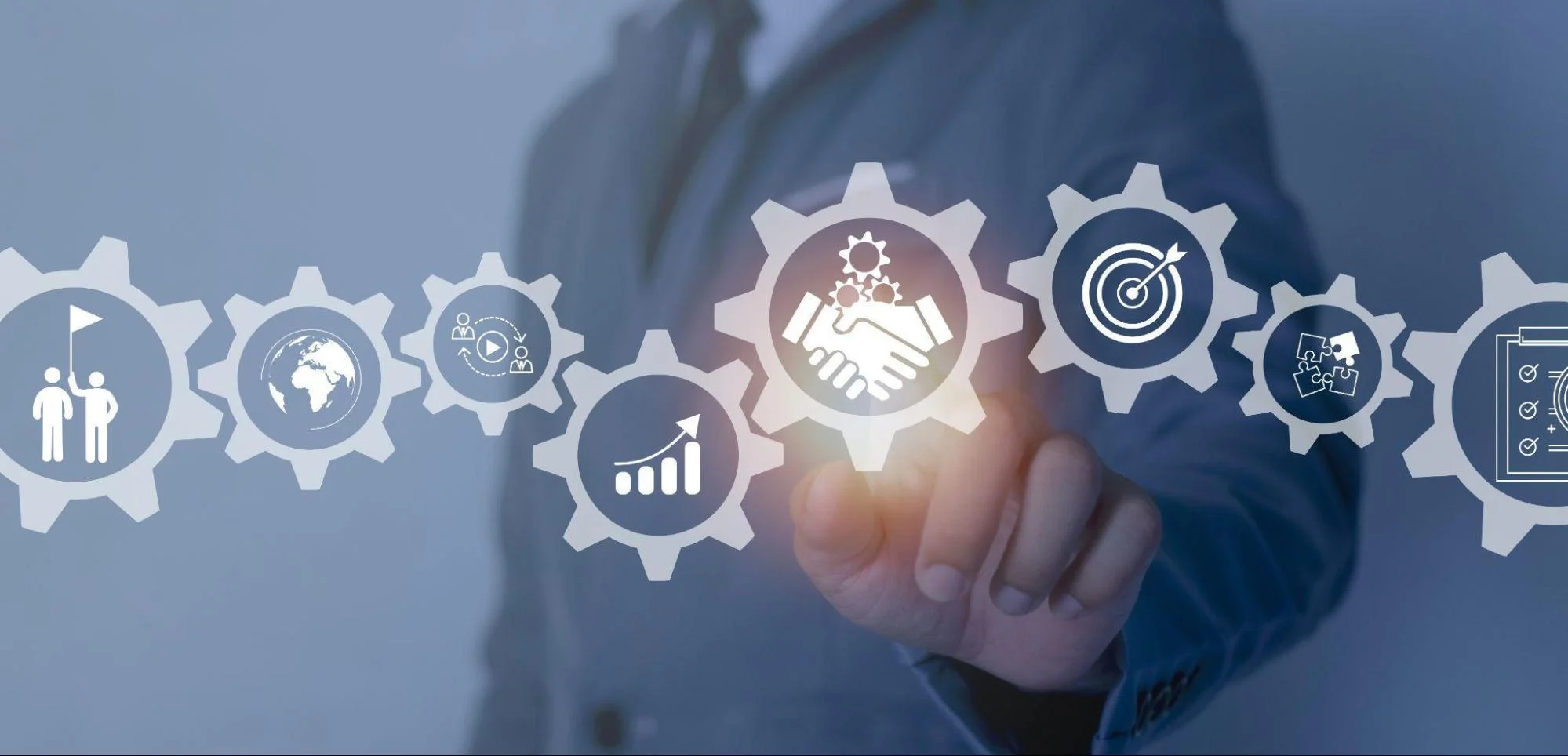
Selecting the Right Partner
Determine your criteria for selecting an outsourced CNC machining services partner who can best meet your manufacturing needs. Experience, certifications, and machining capabilities are important, but you may need more than a CNC job shop that can inspect with hand metrology. Today, lasers and coordinate measurement machines are often used in NABL-certified labs. A partner who understands CNC workflow optimization and can make sound production process decisions also adds value.
Evaluating Costs and Savings
Perform a cost-benefit analysis to determine whether it’s better to outsource your CNC machining, pursue a CNC machine rental, or perform operations in-house. Identify all the costs and benefits, assign a monetary value to each one, and evaluate this data carefully as part of your outsourcing decision. To achieve a true CNC machining cost reduction, you’ll need a complete picture that includes the opportunity cost of your own contributions.
Ensuring Clear Communication
Clear communication is critical to the success of your project. At a minimum, you need the ability to convey design changes without confusion – and in a timely manner. Setting expectations and addressing concerns can also help you avoid unnecessary project expenses and delays. If communicating with a service provider is difficult and time-consuming, that just adds to the total cost of ownership for your CNC machined parts.
Learn how Fictiv helped EBI Robotics reduce costs and lead times for precision CNC parts by improving supplier communication and simplifying sourcing. Fictiv can help you do the same.
Managing Intellectual Property
Your part or product design is a form of intellectual property (IP) that needs legal protection. Perform due diligence, sign a non-disclosure agreement (NDA), and complete a master service agreement that protects your IP by clearly defining ownership and usage rights. Also, consider how much information you need to share. Even if you hold a patent on a product, there’s a risk of IP theft or loss by sharing complete product information.
Quality Control and Assurance
Quality assurance (QA) and Advanced Product Quality Planning (APQP) ensure that product quality requirements are met. Quality control (QC) is an aspect of QA that focuses on part inspection. Because manufacturers may use sampling to inspect only a portion of a production run, investigate how a potential outsourcing partner will meet your exact specifications. Depending on your industry, you may need a quality-driven CNC machining service with ISO 13485, AS 9100, or IATF 16949 certifications to ensure the production of precise components that meet stringent standards.
Supplier Location and Logistics
Consider the geographic location of potential partners and how this could affect shipping times, CNC project management costs, and logistics management. For example, if you need machined parts quickly but want to avoid air freight, a domestic supplier might be a better choice than an offshore CNC machining service. Remember, however, that you can choose a partner with global CNC services.
Compliance and Certifications
Certifications demonstrate that a manufacturer’s quality management system (QMS) meets a published standard such as ISO 13485, AS 9100, or IATF 16949. Compliance ensures that your product is made accordingly. If you need a CNC outsourcing partner that’s certified to a quality standard, determine how they will ensure your product is machined to comply with that standard.
Having a certification doesn’t automatically guarantee consistent quality. Compliance with industry standards involves ongoing audits and quality checks. Therefore it’s best to work with an outsourcing partner who not only holds the necessary certifications but also demonstrates a commitment to continuous adherence to these standards through regular inspections and quality controls.
Data Security and Confidentiality
Protecting design and production data is becoming increasingly challenging because of the use of Internet-enabled CNC machinery and the growth of cybersecurity threats. If you decide to outsource CNC programming, ensure that adequate data security is in place. For example, if you’re a defense contractor, you may need remote CNC programming services from a NIST 800-171 certified provider.
Best Practices for Successful CNC Machining Outsourcing
Choosing the right outsourcing partner is important but so are following these best practices during your vendor selection process.
- Detailed Project Planning: Develop a comprehensive project plan and align requirements, timelines, and quality standards to meet your manufacturing needs.
- Leveraging Advanced Capabilities: Find out if a potential partner uses high-speed cutting tools and precision machining, especially for custom parts with complex geometries and tight tolerances.
- Continuous Improvement: Periodically review and optimize your company’s outsourcing processes. Solicit feedback both internally and externally, and then make any necessary adjustments.
- Building Long-Term Partnerships: When possible, establish long-term relationships with outsourcing partners for stronger collaboration and improved performance. Choosing a manufacturing partner you can grow with can eliminate the need for another vendor search.
- Detailed Contract Agreements: Clearly define terms, responsibilities, and deliverables. Insist upon clear and detailed contracts that specify roles and responsibilities.
- Performance Monitoring and Feedback: Monitor performance metrics and provide feedback that your outsourced CNC machined service partner can use for continuous improvement.
- Risk Management: Continue to identify any potential risks in outsourcing and develop strategies for mitigating and managing them. For example, if there’s a risk of material shortages, work with your vendor to avoid stock-outs.
Why Choose Fictiv for CNC Machining Outsourcing
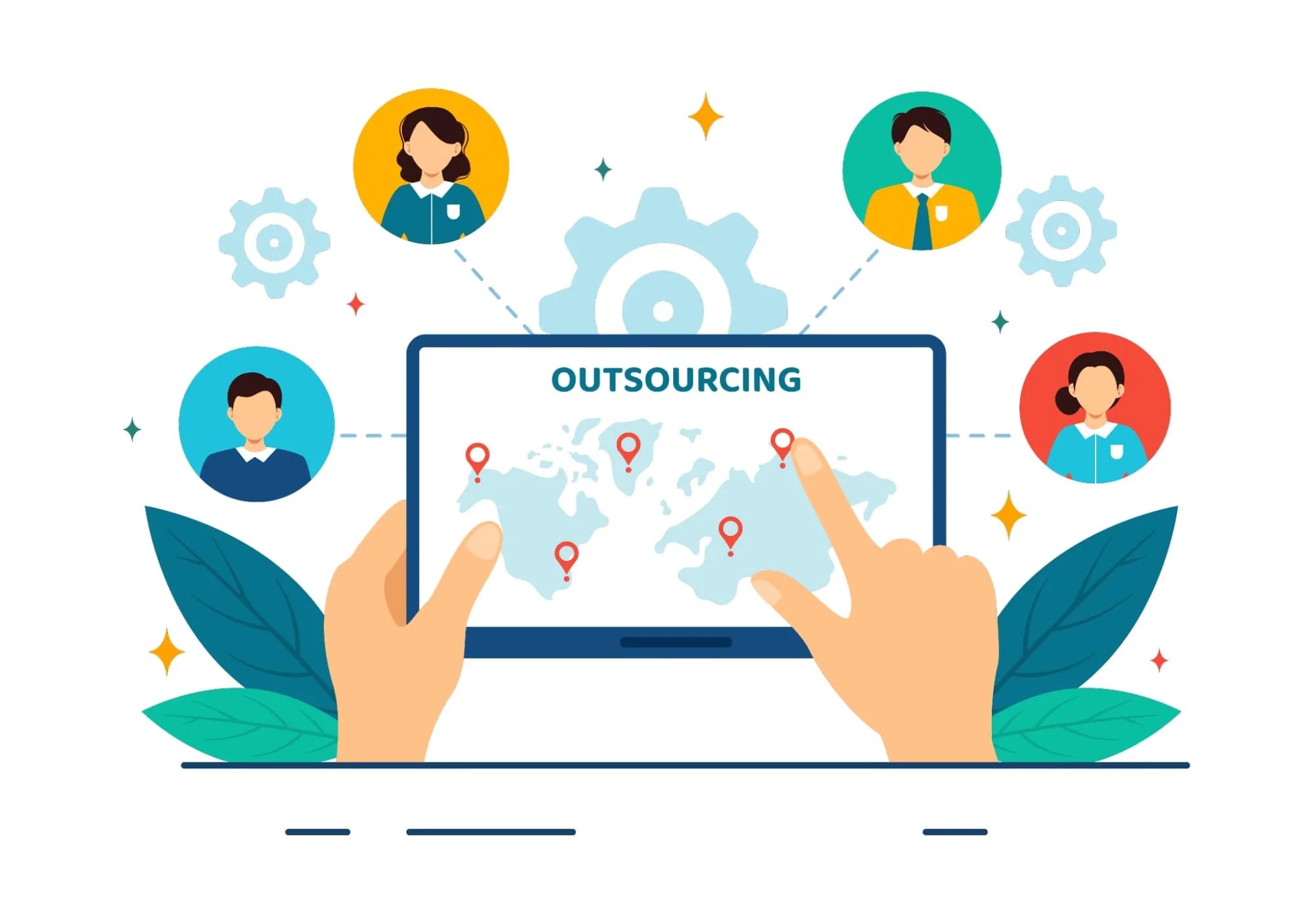
The decision to outsource CNC machining can provide business and technical benefits, but CNC subcontracting is not without risks. Product designers want to save time and money, but companies must receive high-quality components to ensure customer satisfaction. Fortunately, there’s a way to pursue CNC machining outsourcing that strengthens your supply chain.
Fictiv works with a global network of highly-vetted machining partners who use the latest technology to offer comprehensive CNC machining services. From rapid prototyping through high-volume production, you’ll get a commitment to quality and a customer-centric approach. Plus, Fictiv offers instant design for manufacturing feedback (DFM) along with your request for a quote.
Create a free Fictiv account and upload your part design to get started.