Time to read: 5 min
Thermoplastic rubbers (TPR) and thermoplastic elastomers (TPE) are copolymers, or blends of polymers, that have the properties of both thermoplastic and elastomeric materials.
- Thermoplastics can be repeatedly softened or melted by heat and then reformed into different shapes without undergoing chemical degradation. Examples include acrylic and nylon.
- Elastomeric materials exhibit elasticity and are characterized by the ability to return to their original shape after being stretched or deformed. Examples include EPDM and silicone.
Thermoplastic rubber and thermoplastic elastomer are sometimes used interchangeably, but it’s important to understand that TPEs and TPRs are not one and the same. This article discusses the similarities and differences between these two categories of copolymers so you can make the right choice for your next project. But remember, it’s always good practice to speak with a manufacturing expert — like those at Fictiv — for help with material selection. We can also help you launch new products in record time.
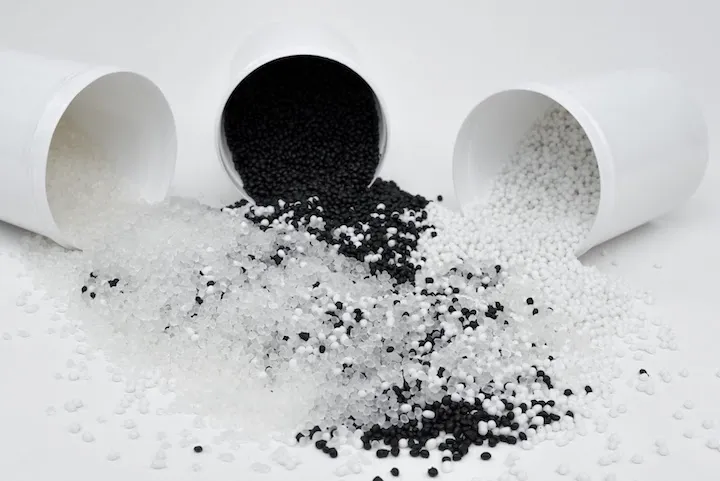
TPR and TPE materials are blends of two or more polymers.
How are TPE and TPR materials different?
Thermoplastic elastomers are a broader category of materials than thermoplastic rubbers. TPEs include TPRs, but they also include several other categories of materials. In other words, while all TPRs are TPEs, not all TPEs are TPRs. Also, thermoplastic elastomers and thermoplastic rubber differ in terms of their properties and end-use applications.
What are the similarities between TPR and TPE?
Thermoplastic rubber (TPR) and thermoplastic elastomer (TPE) materials both provide:
- High flexural fatigue resistance
- Resistance to tearing and abrasion
- Impact strength
- Good dielectric properties (electrical insulation)
- Weathering and chemical resistance
- Temperature resistance
Importantly, TPR and TPE materials are also recyclable. By contrast, thermoset rubbers (like those in automotive tires) and thermoset plastics (such those in electrical connectors) cannot be easily broken down or recycled.
What are the differences between TPR and TPE?
Typically, TPR materials are harder and more rigid. Consequently, thermoplastic rubbers are often used in applications that require greater durability and strength, such as industrial components and auto parts. Thermoplastic elastomers aren’t limited to less demanding applications, but TPEs are often used in food storage and medical and healthcare products. With their greater softness and flexibility, TPEs are also a good choice for seals, gaskets, and vibration control.
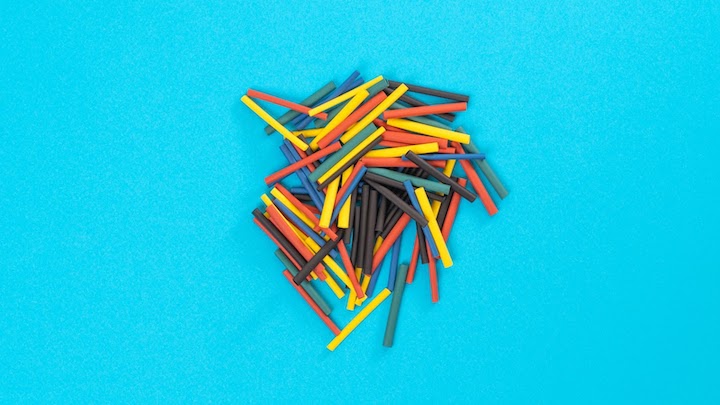
TPE and TPR materials are available in various colors.
What is TPR?
Thermoplastic rubber has a semi-crystalline structure and is synthesized from block copolymers like styrene butadiene styrene (SBS). Unlike vulcanized rubber, which is time-consuming and labor-intensive to produce, TPR rubber can be made less expensively and supports manufacturing processes like injection molding. Molten TPR can be injected into a mold to create complex parts, and it can be molded over a more rigid material (such as the handle of a tool) in a process known as overmolding.
What are the advantages of TPR materials?
Thermoplastic rubber materials provide the following advantages:
- Flexibility and durability for applications that involve twisting, bending or compression
- Ease of processing for high-volume manufacturing, including injection molding
- Chemical resistance for use in harsh environments with substances like oils and solvents
- Lower costs than natural or synthetic rubber, and some types of specialty plastics
- Versatility in terms of properties and applications, with TPR uses that range from medical devices to footwear
What are the disadvantages of TPR materials?
Although TPR materials offer many advantages, they also come with some disadvantages:
- Brittleness or loss of flexibility outside of their service temperature range
- Less resilience, or the ability to snap back, than natural or synthetic rubber
- The potential for creep, or deformation over time under a constant load, that can result in dimensional changes
- Limited resistance to ultraviolet (UV) light, a potential problem in outdoor applications
- Limited bonding capability to other materials, which can complicate overmolding or the use of adhesives for product assembly
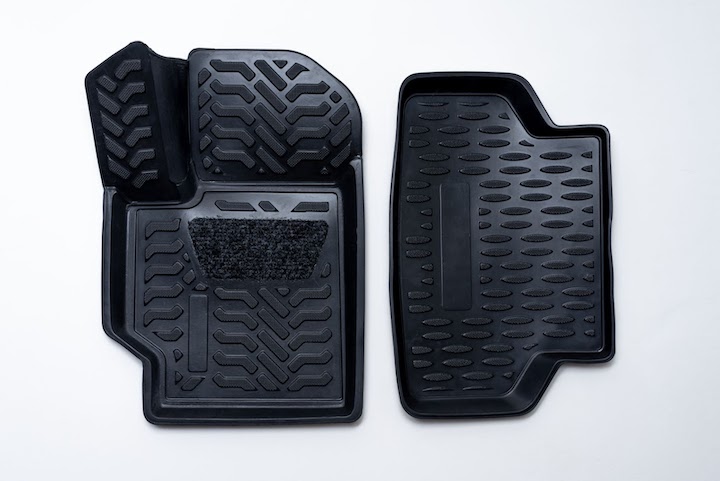
Thermoplastic elastomers are durable, which makes them a good choice for high wear applications
What is TPE?
Thermoplastic elastomers are processed like plastics, but share the performance characteristics of rubber. They include block polymers and blends of polymers with crystalline and amorphous structures.
- The hard blocks impart the properties of plastics, including temperature resistance
- The soft blocks impart elastomeric properties and are also responsible for hardness, flexibility, and the amount of permanent deformation
TPE Category | Abbreviation | Applications |
Syrenic Block Copolymers | TPE-S | Footwear |
Thermoplastic Polyolefins | TPE-O or TPO | Automotive bumpers Dashboards Airbag covers Mudguards |
Thermoplastic Vulcanisates | TPE-V or TPV | Automotive Seals Bellows Hoses Pipe Seals |
Thermoplastic Polyurethanes | TPE-U or TPU | Caster Wheels Power Tool Grips Hoses and Tubes Drive Belts |
Thermoplastic Copolyesters | TPE-E, COPE, or TEEE | Vehicle Air Ducts Ventilator Bags Dust Boots Conveyor Belts |
Melt Processable Rubber | MPR | Automotive Weather Strips Inflatable Boats Seals Goggles |
Thermoplastic Polyether Block Amides | TPE-A | Aerospace parts Cable Jacketing |
What are the advantages of TPE materials?
Thermoplastic elastomers provide the following advantages:
- Good flexibility for applications that require stretching and compression without breaking
- Ease of processing using traditional thermoplastic processes like injection molding
- Durability for use in demanding applications and harsh environments
- Cost-effectiveness, especially for high-volume production runs
- TPEs are easy to sterilize, which makes them a good choice for medical tubing
- These materials do not require reinforcing agents, stabilizers, or cure resins
Also, because TPEs are a broad class of materials, they can be formulated with a wide range of properties such as softness vs. hardness and rigidity vs. flexibility.
What are the disadvantages of TPE materials?
Although TPE materials offer many advantages, they also come with some disadvantages:
- Lower melting point limits use in high-temperature applications
- Limited chemical resistance, especially with highly aggressive chemicals or solvents
- Some types of TPEs degrade or discolor when exposed to UV light, which limits their use in outdoor applications
- Some TPEs are difficult to recycle because they contain specific types of additives
- More expensive than rubber materials such as EPDM
Fictiv Can Help With TPR vs. TPE Material Selection
Do you need help with material selection for your next prototyping or production project? Whether you need TPR, TPE, or another type of material, the injection molding experts at Fictiv can help you pick the right material for your application.
TPR and TPE are commonly used injection molding plastics, but a good plan and skilled production partner are critical to avoid the added costs and risks that come with inadequate drying or improper processing methods. Fictiv has the global manufacturing network and production experts you need to get quality injection parts, fast, no matter how complex your design. We have the skills and know-how to support you from part design through prototyping and production.
Create your free Fictiv account and request an injection molding quote today — we mold complex parts at ridiculous speeds!